In the fast-paced world of retail, minimizing equipment downtime is crucial for maintaining seamless operations. That’s where a Computerized Maintenance Management System (CMMS) steps in as a game-changer. Imagine having a tool that not only tracks maintenance schedules but also predicts potential issues before they disrupt your business.
A CMMS works like a digital assistant for your maintenance team, keeping all equipment data organized and accessible at your fingertips. It streamlines workflows by automating maintenance schedules, sending alerts for preventive maintenance tasks, and logging repair histories in real-time. This proactive approach ensures that minor glitches are fixed before they escalate into costly breakdowns.
Picture this: A busy retail store with multiple refrigeration units suddenly faces a breakdown during peak hours. Without a CMMS, this could mean scrambling to find a technician, losing valuable inventory, and frustrating customers. However, with a well-implemented CMMS, such scenarios are minimized. The system alerts maintenance staff about potential issues early on, allowing them to schedule maintenance during off-peak times or even before signs of trouble arise.
Moreover, a CMMS helps in optimizing spare parts inventory. By tracking usage patterns and maintenance history, it ensures that you always have the right parts available when needed, reducing downtime caused by waiting for replacements.
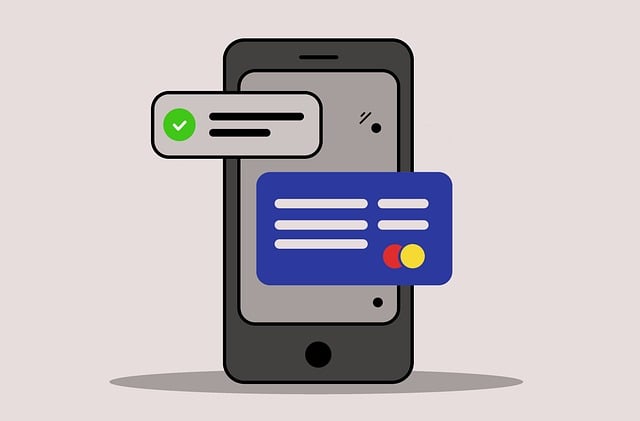
In essence, integrating a CMMS into retail operations isn’t just about fixing things when they break. It’s about staying ahead of the curve, maximizing equipment uptime, and ultimately, delivering a superior customer experience. After all, in the retail world, every minute counts.
Boosting Retail Efficiency: The Role of CMMS in Minimizing Equipment Downtime
In the fast-paced world of retail, efficiency is the heartbeat that keeps operations running smoothly. Imagine a bustling store where every second counts, from checkouts to stocking shelves. Here’s where CMMS (Computerized Maintenance Management Systems) steps in as the unsung hero, quietly ensuring that equipment downtime doesn’t throw a wrench into the gears of productivity.
CMMS is like a vigilant sentinel, monitoring the health of every piece of equipment in a retail environment. From cash registers to HVAC systems, it keeps a watchful eye on performance metrics, schedules maintenance checks, and even predicts potential issues before they escalate into costly disruptions. It’s the behind-the-scenes wizard that turns chaos into seamless operation.
Picture this: a busy Saturday afternoon in a department store. Shoppers weave through aisles, and staff hustle to restock shelves and assist customers. Suddenly, a malfunctioning checkout terminal brings everything to a screeching halt. This is where CMMS shines brightest. By alerting maintenance teams in real-time, it ensures that repairs are swift and minimal, minimizing customer wait times and maximizing satisfaction.
But CMMS isn’t just about reacting—it’s about proactive magic. It’s the foresight to schedule routine maintenance during off-peak hours, preventing breakdowns before they even have a chance to disrupt the shopping experience. It’s akin to a well-timed pit stop in a Formula 1 race, ensuring that the retail engine runs at peak performance without skipping a beat.
Moreover, CMMS isn’t exclusive to large chains. Even smaller retail operations benefit immensely. Imagine a boutique with limited staff and resources. With CMMS, they can manage their equipment efficiently, ensuring that every piece—from lighting fixtures to inventory scanners—operates reliably. It’s about empowering every retailer, big or small, to deliver consistent service and uphold their reputation.
Cutting Costs and Enhancing Performance: CMMS Solutions for Retail Equipment
In the fast-paced world of retail, efficiency is the name of the game. Imagine a scenario where every piece of equipment in your store operates at peak performance, without unnecessary downtime or unexpected breakdowns. That’s where CMMS (Computerized Maintenance Management System) solutions step in, revolutionizing how retail businesses manage their equipment.
CMMS software isn’t just about scheduling maintenance tasks; it’s a strategic tool that helps cut costs and boost performance simultaneously. Picture it as your store’s backstage manager, keeping everything running smoothly behind the scenes. From HVAC systems to refrigeration units and even point-of-sale terminals, CMMS ensures each asset operates efficiently and reliably.
One of the standout features of CMMS is predictive maintenance. Instead of waiting for equipment to fail, CMMS analyzes data to predict when maintenance is needed. It’s like having a crystal ball for your retail equipment, foreseeing issues before they disrupt your operations. This proactive approach not only saves money by preventing costly repairs but also enhances overall performance by minimizing downtime.
Moreover, CMMS solutions provide real-time insights into equipment usage and performance metrics. It’s akin to having a fitness tracker for your store’s machinery, monitoring metrics like energy consumption, usage patterns, and operational efficiency. Armed with this data, retail managers can make informed decisions to optimize workflows and allocate resources effectively.
In essence, adopting CMMS solutions isn’t just a technological upgrade; it’s a strategic investment in the future of your retail operations. By cutting costs through efficient maintenance practices and enhancing performance with data-driven insights, CMMS empowers retailers to stay competitive in a dynamic market landscape.
This article aims to capture the essence of how CMMS solutions benefit retail operations by focusing on efficiency, cost savings, and performance enhancement, all while maintaining a conversational and engaging tone.
Keeping Retail Operations Smooth: CMMS Strategies to Reduce Equipment Downtime
Imagine this: your cash registers are humming, customers are browsing happily, and suddenly, a key piece of equipment malfunctions. It’s a nightmare for any retail manager. But with a well-implemented CMMS strategy, these nightmares can become rare occurrences.
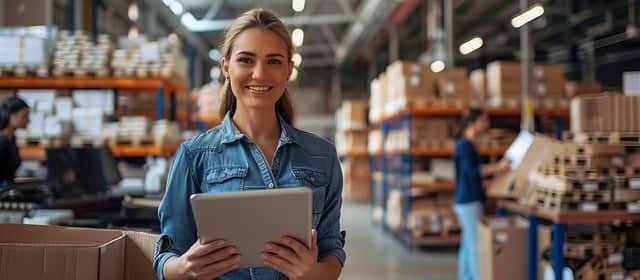
CMMS software acts as a digital guardian angel for your equipment. It keeps track of maintenance schedules, alerts you when preventive maintenance is due, and helps your team stay proactive rather than reactive. By scheduling regular inspections and servicing, you can catch potential issues before they escalate into costly breakdowns.
Think of it like a regular check-up at the doctor’s office. Just as you’d go in for a health check to prevent major health issues, CMMS ensures your retail equipment gets the attention it needs to stay in top shape. This proactive approach not only saves you money on repairs but also keeps your operations running smoothly without unexpected disruptions.
Moreover, CMMS doesn’t just stop at preventive maintenance. It also optimizes your maintenance workflows. It streamlines work orders, tracks spare parts inventory, and provides valuable data insights into equipment performance. With this data at your fingertips, you can make informed decisions about when to repair or replace equipment, ensuring you’re always operating at peak efficiency.
In today’s fast-paced retail environment, every minute counts. Customers expect seamless experiences, and any hiccup in your operations can impact their satisfaction and your bottom line. By embracing CMMS strategies, you’re not just keeping the lights on — you’re ensuring that every aspect of your retail operation runs like a well-oiled machine.
Efficiency Unleashed: How CMMS Technology Can Transform Retail Equipment Management
CMMS technology acts as the ultimate tool for retail managers, offering a centralized platform to oversee maintenance schedules, track repairs, and manage inventory seamlessly. By digitizing maintenance workflows, CMMS systems ensure that equipment downtime is minimized, allowing stores to operate at peak efficiency without disruptions.
One of the key benefits of CMMS is its proactive maintenance capabilities. Instead of waiting for equipment to break down, which can lead to costly repairs and lost productivity, CMMS allows retailers to schedule preventive maintenance tasks based on usage patterns and manufacturer recommendations. This proactive approach not only extends the lifespan of equipment but also reduces the likelihood of unexpected failures during busy periods.
Moreover, CMMS technology provides detailed insights into equipment performance through comprehensive analytics. Managers can analyze data on equipment uptime, maintenance costs, and repair histories to make informed decisions about replacements or upgrades. This data-driven approach not only optimizes operational efficiency but also helps in budget planning and resource allocation.
In essence, CMMS technology transforms retail equipment management from reactive to proactive, ensuring that every asset operates at its best. By streamlining maintenance processes and harnessing data analytics, retailers can focus more on delivering exceptional customer experiences rather than worrying about equipment malfunctions.
Maximizing Uptime: Implementing CMMS to Prevent Downtime in Retail Settings
Implementing a Computerized Maintenance Management System (CMMS) is a game-changer in this scenario. CMMS software empowers retail businesses to proactively manage maintenance schedules, equipment repairs, and asset lifecycles. By digitizing maintenance processes, CMMS ensures that critical systems and equipment remain in optimal condition, minimizing unexpected breakdowns and costly downtime.
Picture this: a retail store equipped with CMMS can schedule preventive maintenance tasks like HVAC system checks or conveyor belt inspections during off-peak hours. This proactive approach prevents equipment failures before they happen, avoiding disruptions during busy periods when customers are shopping.
Moreover, CMMS software provides real-time insights into equipment performance and maintenance histories. Managers can track maintenance activities, identify recurring issues, and analyze data trends to make informed decisions. It’s like having a crystal ball that predicts when equipment might need attention, allowing for timely interventions to keep operations humming smoothly.
In essence, implementing CMMS in retail settings is not just about fixing things when they break; it’s about optimizing efficiency and ensuring reliability. By embracing technology to streamline maintenance processes, retail businesses can focus more on delivering exceptional customer experiences and less on firefighting unexpected downtime.
So, whether it’s a supermarket, a fashion boutique, or a hardware store, maximizing uptime through CMMS transforms how retail operates. It’s the proactive approach that keeps the wheels turning and the doors open, day in and day out.
From Reactive to Proactive: Using CMMS to Mitigate Equipment Downtime in Retail
Enter CMMS, short for Computerized Maintenance Management System. It’s not just a tool but a strategic asset that transforms how retail businesses handle equipment maintenance. Unlike traditional reactive approaches where maintenance is performed only after a breakdown, CMMS empowers businesses to be proactive. It’s like having a vigilant guard that detects potential issues before they escalate into costly downtime episodes.
How does CMMS achieve this? By leveraging data and analytics, CMMS monitors equipment performance in real-time. It tracks metrics like usage patterns, energy consumption, and wear and tear indicators. This proactive monitoring allows maintenance teams to anticipate maintenance needs and schedule repairs during off-peak hours, minimizing disruption to daily operations.
Think of CMMS as a fitness tracker for your retail equipment. Just like how a fitness tracker monitors your heart rate and steps, CMMS monitors the “vital signs” of your machinery. It notifies maintenance teams when equipment shows signs of inefficiency or potential failure, prompting timely interventions to keep everything running smoothly.
Moreover, CMMS centralizes maintenance operations. It stores equipment manuals, service histories, and maintenance schedules in one accessible platform. This centralized approach ensures that all stakeholders—from store managers to maintenance technicians—have instant access to critical information, fostering collaboration and efficiency across the board.
Strategic Advantage: Reducing Equipment Downtime Through CMMS Integration
Imagine running a race with hurdles. Each hurdle represents potential downtime for your equipment – a delay that could cost you time, money, and precious resources. In today’s fast-paced industrial landscape, minimizing these hurdles is not just advantageous but essential for staying ahead. This is where CMMS integration steps in as your strategic advantage.
CMMS, or Computerized Maintenance Management System, is more than just a tool; it’s a game-changer. By integrating CMMS into your operations, you’re essentially putting on a pair of glasses that lets you see hurdles before you reach them. It empowers you to schedule maintenance proactively rather than reactively, ensuring that your equipment stays in peak condition and minimizing unexpected breakdowns.
Think of CMMS integration as having a personal assistant who knows your equipment inside out – from its maintenance history to predictive analytics that foresee potential issues. It’s like having a crystal ball that helps you foresee and prevent downtime, keeping your operations running smoothly.
One of the key benefits of CMMS integration is its ability to streamline workflows. By automating maintenance schedules and processes, it reduces the administrative burden on your team, allowing them to focus on more strategic tasks. This not only boosts efficiency but also enhances overall productivity.
Moreover, CMMS integration fosters a culture of accountability and transparency. Every maintenance task is logged and tracked, providing you with real-time data and insights. You can easily monitor performance metrics, identify recurring issues, and make data-driven decisions to optimize your maintenance strategies.
In essence, CMMS integration isn’t just about reducing downtime – it’s about gaining a competitive edge. It empowers you to stay agile in a dynamic market, anticipate challenges, and maintain operational excellence. So, if you’re looking to outpace your competitors and leap over hurdles with ease, CMMS integration might just be your secret weapon.
Frequently Asked Questions
What are the key features of a CMMS that help minimize downtime in retail stores?
Learn about the essential features of a CMMS that reduce downtime in retail stores. Discover how preventive maintenance scheduling, real-time asset monitoring, and automated work order management contribute to maximizing operational uptime.
How can implementing a CMMS improve equipment reliability in retail settings?
Learn how implementing a Computerized Maintenance Management System (CMMS) in retail settings can enhance equipment reliability by enabling proactive maintenance scheduling, reducing downtime, and ensuring timely repairs and inspections.
What is a CMMS and how does it prevent equipment downtime in retail?
Learn how a CMMS (Computerized Maintenance Management System) reduces equipment downtime in retail by scheduling preventive maintenance tasks, tracking equipment performance, and alerting maintenance teams to potential issues before they cause disruptions. This proactive approach helps retail businesses maintain operational efficiency and minimize costly downtime.
What are the cost savings associated with using a CMMS to manage equipment downtime in retail?
Learn about the cost savings achievable through using a CMMS (Computerized Maintenance Management System) to manage equipment downtime in retail. Discover how proactive maintenance scheduling and faster issue resolution can minimize downtime, reduce repair costs, and optimize operational efficiency.
How does predictive maintenance through a CMMS reduce unplanned equipment failures?
Predictive maintenance through a CMMS (Computerized Maintenance Management System) helps reduce unplanned equipment failures by utilizing data analytics and condition monitoring. By analyzing equipment performance trends and detecting early signs of potential issues, maintenance tasks can be scheduled proactively. This proactive approach minimizes downtime, extends equipment lifespan, and optimizes maintenance costs.