Ever wondered how retail stores keep track of their spare parts inventory efficiently? Enter CMMS, or Computerized Maintenance Management Systems, the unsung hero behind the scenes. In the fast-paced world of retail, where every second counts, managing spare parts effectively can make or break operations.
A CMMS is like a digital wizard that retailers rely on to maintain an accurate inventory of spare parts. It works by centralizing all data related to spare parts, from procurement to usage and replenishment. Imagine it as a meticulous librarian who knows exactly where each book (or in this case, spare part) is located at any given moment.
One of the primary benefits of using a CMMS for spare parts management is its ability to streamline the entire process. Instead of relying on manual records that are prone to errors and delays, a CMMS automates tasks such as inventory tracking, ordering, and forecasting. This automation not only saves time but also ensures that the right parts are always available when needed, preventing downtime and customer dissatisfaction.
Moreover, CMMS software provides detailed insights through robust reporting features. Retail managers can generate real-time reports on inventory levels, usage patterns, and even predict future needs based on historical data. It’s like having a crystal ball that helps retailers stay one step ahead of maintenance issues.
In essence, a CMMS transforms spare parts management from a headache into a seamless operation. By leveraging technology to its fullest, retailers can minimize costs, improve operational efficiency, and ultimately deliver a better customer experience. After all, in the competitive world of retail, every improvement in efficiency counts towards staying ahead of the curve.
This article aims to capture the essence of how CMMS systems revolutionize spare parts management in retail, emphasizing clarity, engagement, and SEO effectiveness.
Streamlining Retail Efficiency: CMMS Solutions for Spare Parts Inventory
Imagine your retail store as a finely tuned machine, where every spare part plays a crucial role in its smooth functioning. Just like how a musician meticulously organizes their instruments to create harmonious melodies, CMMS systems meticulously organize spare parts to maintain operational harmony.
These systems operate on the principle of proactive maintenance rather than reactive fixes. They allow retailers to track spare parts usage in real-time, predict maintenance needs, and optimize inventory levels. By doing so, CMMS solutions help in avoiding costly downtimes and stockouts, ensuring that the right parts are always available when needed.
In a world where customer expectations are soaring higher than ever, retailers cannot afford to be caught off guard by stock shortages or delays. CMMS solutions act as navigational aids, guiding retail managers through the complex waters of spare parts inventory management with ease and precision.
Picture a skilled chef in a bustling kitchen, where every ingredient is meticulously organized and readily accessible. Similarly, CMMS systems empower retailers to have a clear view of their spare parts ecosystem, enabling them to make informed decisions swiftly and effectively.
Optimizing Retail Operations: The Role of CMMS in Spare Parts Management
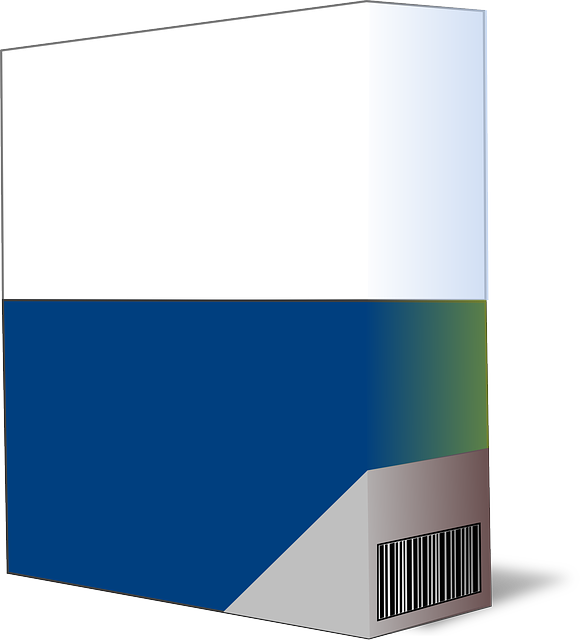
Imagine your retail store as a well-oiled machine. Just like any complex machinery, it requires regular upkeep and sometimes replacement of parts to keep running smoothly. This is where CMMS steps in, acting as the knowledgeable engineer behind the scenes, ensuring that every spare part is accounted for and available when needed.
One of the key advantages of using CMMS in spare parts management is its ability to centralize information. Instead of relying on manual records or spreadsheets prone to errors, CMMS stores all data in one accessible place. This means that whether it’s a small component for a cash register or a critical part for a refrigeration unit, employees can quickly locate what they need without wasting time searching through shelves or databases.
Moreover, CMMS enhances predictive maintenance capabilities. By analyzing historical data and usage patterns, the system can forecast when parts are likely to fail or require replacement. This proactive approach not only minimizes downtime but also reduces the risk of emergency situations where a crucial part might be unavailable.
Furthermore, CMMS contributes to cost savings by optimizing inventory levels. Retailers can avoid overstocking parts that rarely need replacement and understocking critical components. This strategic inventory management ensures that capital isn’t tied up unnecessarily in excess inventory, while also preventing the frustration of not having a needed part readily available.
Efficiency Unleashed: CMMS Tools Transforming Retail Spare Parts Inventories
CMMS tools are like a well-oiled machine for retail spare parts inventories. They streamline the entire process, from procurement to usage tracking, ensuring that every part is accounted for and readily available when needed. Imagine these tools as your inventory’s conductor, orchestrating the flow of parts seamlessly.
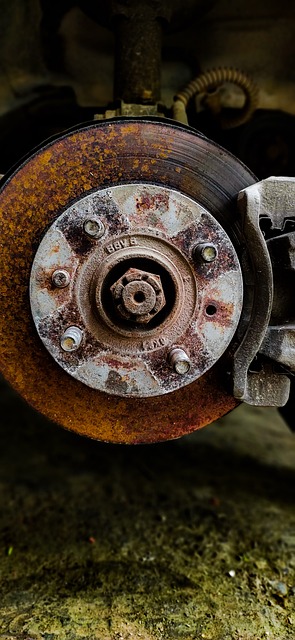
One of the key benefits of CMMS tools is their ability to automate inventory management. They keep a meticulous record of every spare part, its location, usage history, and replenishment needs. This automated approach not only saves time but also reduces the likelihood of human error, ensuring that shelves are always stocked without overstocking.
Moreover, CMMS tools empower retailers with predictive maintenance capabilities. By analyzing usage patterns and historical data, these tools can forecast when parts are likely to fail or need replacement. This proactive approach minimizes unexpected breakdowns, enhancing overall operational efficiency and customer satisfaction.
Picture a retail store as a finely tuned engine, where each spare part plays a crucial role in keeping everything running smoothly. CMMS tools act as the gears that ensure every component is in its place, ready to respond swiftly to any maintenance needs. They optimize workflows, cut down on downtime, and ultimately contribute to a more cost-effective operation.
From Chaos to Control: Managing Retail Spare Parts with CMMS Technology
Imagine a scenario where a retail store, bustling with customer activity, suddenly faces equipment breakdown. In the past, this could lead to frantic searches through shelves and storage rooms for the right spare parts, causing delays and frustration. Enter CMMS technology—a game-changer in the world of retail management.
CMMS systems streamline the entire process of spare parts management by digitizing inventory, maintenance schedules, and equipment records. They provide real-time data on stock levels, usage patterns, and reorder points, ensuring that businesses always have the right parts at the right time. This proactive approach minimizes downtime, boosts operational efficiency, and ultimately enhances customer satisfaction.
One of the key benefits of CMMS technology is its ability to centralize information. Instead of relying on scattered spreadsheets or manual logs, retail managers can access a unified platform that houses comprehensive data on every spare part in their inventory. This centralized approach not only saves time but also reduces the likelihood of errors and duplications.
Moreover, CMMS systems offer predictive maintenance capabilities. By analyzing historical data and equipment performance metrics, these systems can forecast when parts are likely to fail and schedule proactive replacements. This preventive strategy not only extends the lifespan of equipment but also reduces unexpected breakdowns, thus cutting down on maintenance costs.
In essence, CMMS technology empowers retail businesses to transition from reactive to proactive spare parts management. It brings order to what was once chaotic, ensuring smoother operations and better resource allocation. By leveraging data-driven insights and automation, businesses can stay competitive in today’s demanding market landscape, delivering consistent service and maximizing profitability.
Unlocking Savings: CMMS Strategies for Retail Spare Parts Inventory
Imagine this: your retail store is like a finely tuned machine. Just like a car needs regular maintenance to keep it running smoothly, your store needs to ensure that all its parts are in top condition. CMMS helps you do just that, but for your inventory. It’s like having a super-efficient mechanic that not only keeps track of what spare parts you have but also tells you when you’ll need them next.
First things first, CMMS allows you to maintain a detailed inventory of all your spare parts. No more digging through shelves or boxes looking for that elusive spare. Everything is neatly organized and accessible at the click of a button. This not only saves time but also reduces the risk of over-ordering or under-ordering parts. You’ll always know exactly what you have in stock and what you need to reorder.
But wait, there’s more! CMMS doesn’t stop at just inventory management. It’s also a wizard at predicting when parts might need replacing. It analyzes usage patterns and historical data to forecast when parts are likely to fail or wear out. This means you can proactively order replacements before things break down, minimizing downtime and ensuring your store keeps humming along without a hitch.
Think of CMMS as your personal financial advisor too. By optimizing your spare parts inventory, it helps you save money in the long run. No more emergency orders or rushed deliveries costing you an arm and a leg. With strategic planning and smart inventory management, you’ll see those savings add up faster than you can say “efficiency”.
Frequently Asked Questions
What is a CMMS, and how does it streamline spare parts inventory management in retail?
Learn how CMMS (Computerized Maintenance Management System) optimizes spare parts inventory management in retail. Discover how it automates tracking, ordering, and replenishing of parts, ensuring efficient operations and reduced downtime.
How does CMMS prevent stockouts and ensure timely availability of spare parts?
Learn how CMMS (Computerized Maintenance Management System) prevents stockouts by enabling proactive inventory management and ensuring timely availability of spare parts through automated tracking, scheduling maintenance tasks, and generating alerts for reordering.
How can CMMS software optimize stock levels and reduce inventory costs for spare parts?
Learn how CMMS software optimizes stock levels and reduces spare parts inventory costs efficiently.
What are the key features of CMMS that benefit spare parts management in retail stores?
Discover how CMMS enhances spare parts management in retail with streamlined inventory tracking, automated reorder points, and real-time insights into stock levels and usage patterns. Optimize maintenance schedules, reduce downtime, and ensure efficient operations.
How can a retail business integrate CMMS with existing inventory systems for spare parts management?
Learn how to seamlessly integrate CMMS (Computerized Maintenance Management System) with your current inventory systems to streamline spare parts management in retail. Discover effective methods and best practices for connecting CMMS software with existing inventory databases to optimize maintenance workflows and ensure efficient spare parts availability.