Imagine a factory bustling with activity, where machines hum rhythmically, ensuring products roll out seamlessly. Behind this smooth operation lies a crucial element: maintenance. In manufacturing, every minute of downtime can translate into significant losses. This is where CMMS (Computerized Maintenance Management System) steps in as a game-changer.
CMMS isn’t just another software; it’s the backbone of efficient maintenance tracking in manufacturing. By digitizing maintenance operations, CMMS streamlines everything from scheduling preventive maintenance to managing work orders and tracking equipment performance. It acts as a virtual assistant for maintenance teams, ensuring no machine is overlooked and no task is delayed.
One of CMMS’s standout features is its ability to create detailed maintenance histories. Imagine having instant access to records detailing when each machine was last serviced, what issues were addressed, and what parts were replaced. This historical data isn’t just for documentation; it’s a goldmine for predictive maintenance. By analyzing trends and patterns, manufacturers can preemptively address potential failures before they escalate, thus minimizing unplanned downtime.
Moreover, CMMS enhances communication and collaboration among teams. Whether it’s notifying technicians of urgent repairs or alerting managers of impending maintenance tasks, CMMS ensures everyone stays in the loop. This real-time visibility fosters proactive decision-making and reduces the risk of costly breakdowns.
In essence, CMMS transforms maintenance tracking from reactive to proactive. It empowers manufacturers to operate with precision and efficiency, maximizing uptime and optimizing resources. As technology continues to evolve, CMMS remains at the forefront, driving innovation in manufacturing maintenance strategies.
This article highlights the transformative impact of CMMS in manufacturing, focusing on efficiency, proactive maintenance, and enhanced communication facilitated by this essential tool.
Streamlining Efficiency: How CMMS Transforms Maintenance Tracking in Manufacturing
Imagine a bustling manufacturing plant, where every machine hums with precision and every process contributes to the final product. Behind this seamless operation lies a crucial element: maintenance. In the realm of manufacturing, where downtime can mean lost productivity and revenue, efficient maintenance management is paramount. This is where Computerized Maintenance Management Systems (CMMS) step in to revolutionize the landscape.
CMMS software serves as the backbone of proactive maintenance strategies in modern manufacturing facilities. It replaces traditional pen-and-paper methods with digital solutions that offer real-time insights and predictive capabilities. By centralizing maintenance data and workflows, CMMS enables managers to monitor equipment health, schedule preventive maintenance tasks, and track work orders effortlessly.
One of the standout features of CMMS is its ability to streamline maintenance operations. Through automated alerts and notifications, it ensures that maintenance tasks are carried out promptly before equipment failure occurs. This proactive approach not only minimizes unplanned downtime but also extends the lifespan of critical assets, optimizing overall operational efficiency.
Moreover, CMMS empowers decision-makers with comprehensive analytics and reporting functionalities. By analyzing historical maintenance data, managers can identify trends, pinpoint recurring issues, and make data-driven decisions to improve asset reliability and performance. This proactive approach not only reduces maintenance costs but also enhances production output, driving profitability in the long run.
In essence, CMMS transforms maintenance tracking in manufacturing by fostering a culture of efficiency and reliability. It empowers maintenance teams to work smarter, not harder, by automating routine tasks and providing actionable insights. As manufacturing landscapes evolve, embracing CMMS becomes not just a choice but a strategic imperative to stay competitive in today’s dynamic market.
Unveiling the Future of Maintenance: CMMS Solutions in Modern Manufacturing
Imagine a factory floor where machines operate seamlessly, downtime is minimized, and maintenance tasks are scheduled with precision. This is the promise of CMMS solutions. By integrating cutting-edge technology with robust maintenance practices, these systems empower manufacturing facilities to achieve unprecedented efficiency and reliability.
At its core, CMMS serves as a digital nerve center, orchestrating maintenance activities from routine inspections to predictive maintenance based on real-time data analysis. This proactive approach not only prevents unexpected equipment failures but also optimizes the lifespan of critical assets.
Think of CMMS as a conductor guiding a symphony of operations. It captures and analyzes data on equipment performance, usage patterns, and historical maintenance records. This wealth of information enables manufacturing managers to make informed decisions swiftly, ensuring equipment is operational when needed most.
Moreover, CMMS solutions foster a culture of continuous improvement by providing actionable insights into maintenance processes. By identifying trends and areas for enhancement, manufacturers can refine their strategies, reduce operational costs, and elevate overall productivity.
In the competitive landscape of modern manufacturing, staying ahead requires more than just efficiency—it demands agility and foresight. CMMS solutions not only meet these demands but pave the way for future innovations in maintenance practices. As technology evolves, so too will CMMS, integrating AI and IoT capabilities to further enhance predictive maintenance and adaptability.
The future of maintenance in manufacturing is unfolding before our eyes, driven by the evolution of CMMS solutions. Embracing these advancements isn’t just about keeping up; it’s about leading the charge towards a more efficient, resilient, and sustainable future for industrial operations.
From Chaos to Control: CMMS and the Evolution of Maintenance Tracking
Imagine your facility’s maintenance operations as a well-orchestrated symphony. Each component, from machines to manpower, plays a crucial role in the harmony of productivity. However, without a conductor, this symphony could descend into chaos. Here’s where CMMS steps in as the conductor, bringing order and efficiency to the maintenance process.
CMMS software serves as a centralized hub where all maintenance-related activities are orchestrated and tracked. It allows maintenance managers to schedule tasks, track work orders, manage inventory, and analyze historical data to predict maintenance needs. This proactive approach helps organizations shift from reactive firefighting to proactive maintenance strategies.
Picture this: instead of scrambling to fix a breakdown, imagine foreseeing it before it happens. CMMS empowers maintenance teams with predictive maintenance capabilities, utilizing data analytics to detect patterns and potential failures early on. This not only minimizes downtime but also optimizes resources, saving costs in the long run.
Moreover, CMMS facilitates compliance with regulatory standards and audits by maintaining detailed records of maintenance activities and asset histories. It ensures that organizations adhere to safety protocols and operational standards effortlessly.
In essence, CMMS transforms the way maintenance is managed, offering a streamlined approach that enhances operational efficiency and prolongs asset lifespan. It’s the conductor that turns chaos into control, enabling organizations to thrive in a competitive landscape by maximizing uptime and minimizing disruptions. As industries evolve, CMMS remains at the forefront, driving the future of maintenance management towards greater reliability and sustainability.
Data-Driven Maintenance: Harnessing CMMS for Manufacturing Excellence
Imagine a factory where every machine operates at peak performance, seamlessly maintaining production schedules without unexpected downtime. This vision is not far-fetched with CMMS, which acts as a digital nerve center for maintenance activities. It collects vast amounts of operational data, from equipment performance metrics to maintenance history, organizing them into actionable insights.
Using CMMS, manufacturing managers can schedule preventive maintenance based on actual equipment usage rather than generic timetables. This proactive approach not only minimizes breakdowns but also extends the lifespan of critical machinery, reducing overall maintenance costs. By predicting potential failures before they occur, CMMS transforms reactive maintenance into a proactive, cost-saving strategy.
Furthermore, CMMS enhances workforce productivity by automating routine tasks like work order generation and inventory management. This automation frees up maintenance teams to focus on strategic initiatives and complex problem-solving, fostering a culture of continuous improvement within the organization.
Analogous to a conductor orchestrating a symphony, CMMS harmonizes the various components of manufacturing operations. It synchronizes maintenance schedules with production demands, ensuring that equipment downtime does not disrupt workflow rhythm. This synergy translates into higher output consistency and customer satisfaction, as orders are fulfilled promptly and with precision.

In essence, data-driven maintenance through CMMS represents a paradigm shift in manufacturing management. It empowers businesses to leverage data as a strategic asset, driving operational efficiency and sustainable growth. As industries embrace digital transformation, CMMS stands at the forefront, reshaping how manufacturers achieve and sustain excellence in their operations.
Innovative Solutions: CMMS Redefining Maintenance Strategies in Manufacturing
Imagine a factory floor buzzing with activity, machines humming in rhythm, each part crucial to the seamless operation of the production line. In such a dynamic environment, maintenance is not just a routine task but a strategic imperative. This is where Computerized Maintenance Management Systems (CMMS) step in, revolutionizing how manufacturers approach equipment upkeep.
CMMS software acts as the digital backbone of modern maintenance operations, streamlining processes from scheduling routine checks to predicting equipment failures before they occur. It’s like having a proactive maintenance assistant that never sleeps, ensuring every machine operates at peak efficiency.
One of the standout features of CMMS is its ability to automate maintenance workflows. By digitizing work orders and maintenance schedules, CMMS eliminates the inefficiencies of paper-based systems, reducing downtime and increasing overall productivity. Imagine a scenario where a technician receives instant notifications on their mobile device about pending maintenance tasks, complete with detailed instructions and historical data on the equipment’s performance. This level of real-time visibility empowers teams to make informed decisions swiftly, keeping operations running smoothly.
Moreover, CMMS software doesn’t just stop at scheduling repairs. It’s a treasure trove of data analytics, capturing valuable insights into equipment performance trends over time. This data-driven approach enables manufacturers to adopt predictive maintenance strategies, preemptively addressing potential issues based on historical data and predictive algorithms. It’s akin to having a crystal ball that foresees equipment failures before they manifest, saving costs and preventing unplanned downtime.
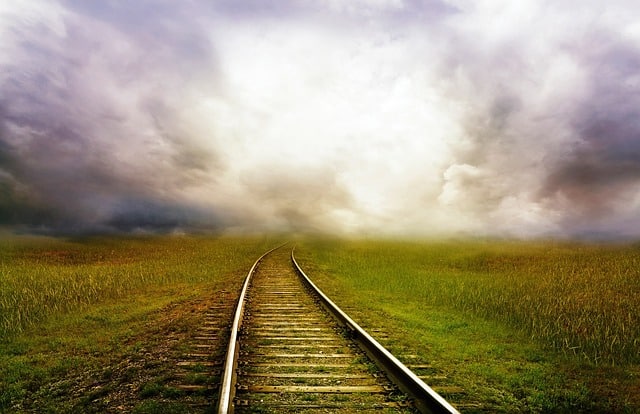
In essence, CMMS is not just a tool but a transformational force in modern manufacturing. By integrating technology with maintenance practices, it empowers businesses to optimize resources, extend the lifespan of critical assets, and ultimately enhance their competitive edge in the market. As industries evolve, CMMS continues to evolve alongside, driving innovation and efficiency across the manufacturing landscape.
The Power of Predictive Maintenance: CMMS Leading the Way in Manufacturing
In essence, predictive maintenance anticipates machinery issues before they occur, leveraging data analytics and IoT sensors to monitor equipment health in real-time. This proactive strategy contrasts sharply with traditional reactive maintenance, where repairs are made only after equipment failure disrupts operations. By predicting when maintenance is needed based on data-driven insights, CMMS enables manufacturers to schedule repairs during planned downtime, optimizing efficiency and reducing costs.
The beauty of CMMS lies in its ability to turn raw data into actionable intelligence. Through continuous monitoring and analysis, CMMS identifies patterns and anomalies that signify potential problems. It’s akin to a skilled doctor diagnosing symptoms before they escalate into serious illnesses. This foresight not only prevents breakdowns but also extends the lifespan of equipment, saving companies significant capital expenditure in replacement costs.
Furthermore, CMMS doesn’t just stop at predictive insights. It streamlines maintenance workflows by automating routine tasks, such as work order generation and inventory management. This automation frees up maintenance teams to focus on strategic initiatives rather than firefighting daily operational issues.
In today’s competitive manufacturing landscape, where downtime can translate into substantial financial losses, CMMS-powered predictive maintenance offers a crucial competitive advantage. It ensures operational continuity, enhances product quality, and boosts customer satisfaction by delivering goods on time and as promised.
Frequently Asked Questions
How can CMMS help reduce maintenance costs in manufacturing
Learn how CMMS (Computerized Maintenance Management Systems) streamline maintenance tasks, optimize scheduling, and track equipment performance, resulting in reduced downtime and operational costs in manufacturing.
How does CMMS improve equipment uptime and reliability
Learn how CMMS (Computerized Maintenance Management System) enhances equipment uptime and reliability by scheduling preventive maintenance, swiftly responding to breakdowns, and optimizing asset performance through data-driven insights.
What features should I look for in a CMMS for manufacturing facilities
This FAQ answers what features to consider when selecting a CMMS for manufacturing facilities. It provides a concise, clear guide to help users understand essential functionalities that ensure effective maintenance management in industrial settings.
What is CMMS and how does it enhance maintenance tracking in manufacturing
CMMS (Computerized Maintenance Management System) is a software solution that enhances maintenance tracking in manufacturing by centralizing maintenance operations. It allows manufacturers to schedule and track maintenance tasks efficiently, manage work orders, and monitor equipment performance. CMMS improves overall equipment effectiveness (OEE) by reducing downtime, optimizing resource allocation, and ensuring timely maintenance, ultimately enhancing productivity and prolonging equipment lifespan.
What are the key benefits of implementing CMMS in manufacturing maintenance
Learn about the essential benefits of implementing CMMS (Computerized Maintenance Management System) in manufacturing maintenance, enhancing efficiency, reducing downtime, optimizing asset management, and improving overall operational reliability.