Have you ever wondered how businesses manage to keep their equipment running smoothly without frequent breakdowns? The answer lies in an effective CMMS (Computerized Maintenance Management System). CMMS software plays a crucial role in reducing equipment failure rates by streamlining maintenance processes and ensuring timely inspections and repairs.
One of the key features of CMMS is its ability to schedule preventive maintenance tasks. Instead of waiting for equipment to break down, which can lead to costly repairs and downtime, CMMS allows businesses to proactively maintain their machinery. By setting up regular inspections and servicing based on equipment usage and manufacturer recommendations, potential issues can be identified and resolved before they escalate into failures.
Moreover, CMMS helps in managing work orders efficiently. When maintenance issues arise, employees can quickly create work orders detailing the problem and assign them to maintenance staff. This streamlined process ensures that problems are addressed promptly, minimizing the risk of equipment failures disrupting operations.
Another advantage of CMMS is its ability to track maintenance history. By recording all maintenance activities and repairs performed on each piece of equipment, CMMS provides valuable insights into asset performance and reliability. Managers can analyze this data to identify recurring issues, optimize maintenance schedules, and even make informed decisions about equipment upgrades or replacements.
Furthermore, CMMS software facilitates inventory management by keeping track of spare parts and supplies needed for maintenance tasks. This ensures that maintenance technicians have the necessary resources on hand, reducing delays in repairs and further minimizing equipment downtime.
Implementing a CMMS system can significantly reduce equipment failure rates by enabling proactive maintenance, efficient work order management, comprehensive maintenance tracking, and optimized inventory control. Businesses that leverage CMMS effectively not only extend the lifespan of their equipment but also enhance overall operational efficiency and reliability.
Mastering Maintenance: Using CMMS to Slash Equipment Failure Rates
Imagine a world where equipment breakdowns are rare occurrences rather than headaches that disrupt productivity. This is where CMMS, or Computerized Maintenance Management Systems, step in as the unsung heroes of efficient maintenance strategies. In essence, CMMS software isn’t just a tool; it’s the proactive shield that businesses wield against the costly specter of equipment failures.
At its core, CMMS empowers maintenance teams with a comprehensive digital toolkit. It tracks maintenance schedules, logs repair histories, and even forecasts potential issues before they escalate. By centralizing maintenance data in one accessible platform, CMMS doesn’t just react to breakdowns; it anticipates and prevents them altogether.
Picture this: just like a vigilant guardian, CMMS sends alerts when maintenance is due, ensuring equipment stays in peak condition. It’s like having a personal trainer for your machines, guiding them through regular exercises (maintenance tasks) to keep them fit and running smoothly.
Moreover, CMMS isn’t limited to just reactive fixes. It fosters a proactive maintenance culture by analyzing historical data to identify trends and weak spots in equipment performance. This predictive prowess transforms maintenance from a firefighting operation into a well-oiled preventive machine.
In practical terms, businesses that embrace CMMS see tangible benefits beyond reducing downtime and repair costs. They foster a culture of reliability and efficiency, where every piece of equipment operates at its optimal level for longer periods. It’s not just about slashing failure rates; it’s about maximizing uptime and operational excellence.
So, whether you’re managing a fleet of manufacturing machines or a network of HVAC systems, CMMS is the strategic ally that ensures your equipment works smarter, not harder. It’s the secret sauce that turns maintenance from a reactive chore into a proactive advantage, ensuring your business stays ahead of the curve in a competitive landscape.
This article is crafted to engage the reader with a conversational tone, employing analogies (like the personal trainer for machines) and rhetorical questions to maintain interest and clarity.
Unlocking Efficiency: Strategies for Lowering Equipment Failure with CMMS
Imagine your equipment as a well-oiled machine, humming along perfectly day after day. That’s the ideal scenario every facility manager dreams of, right? Well, with CMMS, it’s not just a dream—it’s a tangible goal. Here’s how it works: CMMS software helps you schedule maintenance tasks like clockwork. Whether it’s routine inspections, oil changes, or part replacements, CMMS keeps track of it all so you don’t have to. It’s like having a personal assistant for your equipment, reminding you of what needs attention and when.
But wait, there’s more. CMMS doesn’t just keep you organized; it’s also your crystal ball into the future of your machinery. By analyzing historical data on equipment performance, CMMS can predict when components might fail. It’s like foreseeing an upcoming storm and battening down the hatches before it hits. This predictive maintenance approach is a game-changer, saving you from costly emergency repairs and unplanned downtime.
Now, let’s talk about efficiency. With CMMS, every maintenance task is streamlined. Technicians receive work orders directly on their mobile devices, complete with all the details they need. No more back-and-forth, no more time wasted searching for manuals or tracking down parts. It’s all there at their fingertips, ready to go. This streamlined process not only saves time but also boosts productivity across the board.
Think of CMMS as the conductor of an orchestra, harmonizing all the moving parts of your maintenance operations into a symphony of efficiency. It’s not just about fixing things when they break—it’s about preventing breakdowns altogether. By staying ahead of the curve with proactive maintenance, you’re not just saving money; you’re safeguarding your operations against disruptions that could impact your bottom line.
Proactive Maintenance: Harnessing CMMS to Prevent Equipment Breakdowns
Imagine your production floor operating smoothly, each machine humming with efficiency. Now, picture the chaos if one critical piece of equipment suddenly breaks down. Downtime, delays, and the headache of emergency repairs—all of these can significantly impact your bottom line. This is where proactive maintenance steps in, and with the aid of Computerized Maintenance Management Systems (CMMS), businesses can revolutionize their approach to equipment upkeep.
CMMS isn’t just another piece of software; it’s your secret weapon against unexpected breakdowns. By integrating CMMS into your maintenance strategy, you’re not just fixing problems as they arise; you’re preventing them from occurring in the first place. How does it work? Think of CMMS as your digital maintenance planner, keeping track of every asset, scheduling inspections, and even predicting when maintenance is due based on historical data and real-time analytics.
Gone are the days of reactive repairs eating into your productivity. With CMMS, maintenance becomes proactive. It shifts your focus from firefighting to strategic planning, ensuring that every piece of equipment receives timely attention before it becomes a costly problem. By identifying potential issues early, you not only save on repair costs but also extend the lifespan of your equipment, maximizing your return on investment.
But CMMS isn’t just about data and schedules; it’s about empowerment. It empowers your maintenance team to work smarter, not harder. By streamlining workflows and automating routine tasks, CMMS frees up valuable time for your technicians to focus on more complex challenges and continuous improvement initiatives.
In today’s fast-paced business environment, staying ahead means more than just keeping up—it means anticipating and preventing disruptions before they occur. With CMMS as your ally, proactive maintenance isn’t just a strategy; it’s a mindset that drives efficiency, reduces costs, and ensures that your operations run like a well-oiled machine. So, are you ready to transform your maintenance approach and safeguard your business against downtime? CMMS is your answer.
Cutting Costs and Downtime: Optimizing Equipment Maintenance with CMMS
Imagine running a factory where every machine hums in perfect rhythm, productivity soaring without a hitch. Now, imagine the same factory plagued by frequent breakdowns, downtime stretching like a long shadow over your profits. The difference lies in how well you manage equipment maintenance, and that’s where CMMS (Computerized Maintenance Management System) steps in as your knight in shining armor.
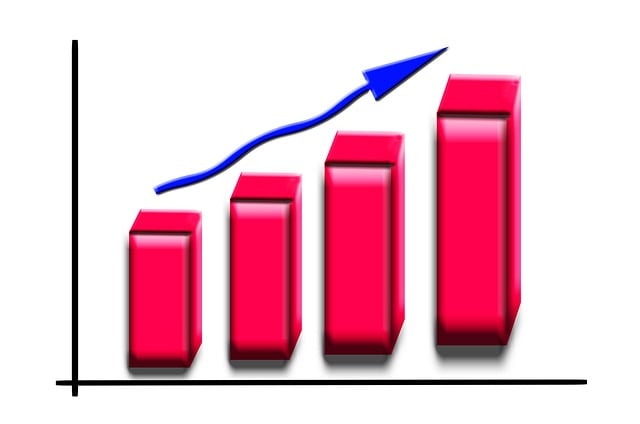
CMMS isn’t just another tech tool; it’s the conductor orchestrating a flawless symphony of maintenance operations. By centralizing maintenance data and scheduling, CMMS empowers your team to nip potential issues in the bud before they blossom into costly repairs. Think of it as a proactive shield rather than a reactive band-aid.
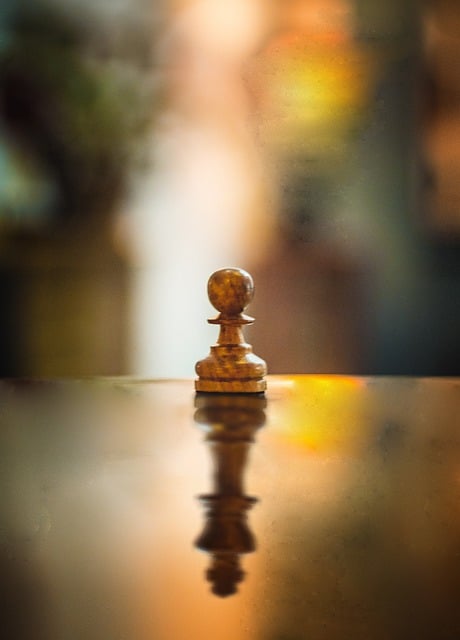
One of the biggest headaches in any industry is unexpected downtime. It’s like a surprise guest at a party—you didn’t invite it, and now it’s ruining the fun. CMMS ensures those surprise guests are few and far between by scheduling preventive maintenance like clockwork. It’s like giving your machines regular check-ups to catch issues early, ensuring they stay in top shape.
Cost-cutting isn’t just about pinching pennies; it’s about investing in smart solutions that pay dividends. CMMS does exactly that by optimizing maintenance schedules, reducing the need for emergency repairs, and extending the lifespan of your equipment. It’s like switching from buying cheap shoes that wear out quickly to investing in a sturdy pair that lasts for years—a smart move that saves money in the long run.
In today’s fast-paced world, downtime is the arch-nemesis of productivity. Every minute a machine sits idle, money trickles away like sand through fingers. CMMS keeps your operations humming smoothly by minimizing downtime through predictive maintenance. It’s like having a crystal ball that predicts when and how your machines might falter, allowing you to intervene before they do.
In essence, CMMS isn’t just a tool; it’s a strategic partner in your quest for operational excellence. By optimizing equipment maintenance, it cuts costs, slashes downtime, and ensures your business runs like a well-oiled machine—efficient, reliable, and ready to conquer new heights. So, if you’re still wrestling with maintenance chaos, maybe it’s time to let CMMS be your guiding light toward smoother operations and greater profitability.
Frequently Asked Questions
What is CMMS and how can it reduce equipment failure rates
Learn what CMMS is and how it can effectively lower equipment failure rates. CMMS, or Computerized Maintenance Management System, is a software tool that helps organizations streamline maintenance activities. By automating scheduling, tracking maintenance tasks, and optimizing equipment performance, CMMS enhances preventive maintenance, minimizing unexpected breakdowns and extending equipment lifespan.
What are the best practices for integrating CMMS with existing maintenance workflows
Learn how to effectively integrate CMMS (Computerized Maintenance Management System) into your current maintenance processes with these best practices. Ensure seamless data migration, establish clear workflows, provide comprehensive training, and regularly review and optimize your integration.
How does CMMS data analysis help in predicting and preventing equipment failures
Learn how CMMS data analysis anticipates and prevents equipment failures efficiently by identifying patterns and anomalies in equipment performance, enabling proactive maintenance strategies.
What are the key features to look for in a CMMS for reducing equipment downtime
Discover the essential features to minimize equipment downtime with a CMMS. Learn how to optimize maintenance schedules, track asset performance, and streamline work orders efficiently.
How to implement CMMS to optimize preventive maintenance schedules
Learn how to implement a Computerized Maintenance Management System (CMMS) effectively to optimize preventive maintenance schedules, ensuring equipment reliability and minimizing downtime.