Imagine a world where machines predict their own maintenance needs, where downtime is minimized, and operations run seamlessly. That’s the promise of CMMS. By integrating data analytics, IoT sensors, and predictive algorithms, CMMS platforms empower engineers to preemptively address equipment issues before they escalate. This proactive approach not only saves time and resources but also enhances overall productivity.
CMMS isn’t just about fixing what’s broken; it’s about optimizing performance. Think of it as a digital assistant for maintenance teams, organizing schedules, tracking work orders, and ensuring compliance with regulatory standards. This streamlined management not only reduces human error but also improves safety protocols and extends the lifespan of critical assets.
In the field of engineering, adaptability is key. CMMS doesn’t just adapt; it evolves. As technology advances, so too does its capability to integrate with other systems, from ERP software to AI-driven analytics. This interconnectedness creates a comprehensive ecosystem where data flows seamlessly, insights are actionable, and decisions are informed by real-time information.
Moreover, CMMS isn’t limited to large-scale enterprises. Its scalability makes it accessible to businesses of all sizes, democratizing advanced maintenance practices across industries. Whether in manufacturing, healthcare, or facilities management, the principles remain the same: efficiency, reliability, and cost-effectiveness.
Digital Revolution in Engineering: CMMS Paving the Way for Future Maintenance Practices
Imagine CMMS as the conductor of a complex orchestra, where each instrument symbolizes a crucial aspect of maintenance: from scheduling preventive tasks to managing work orders seamlessly. Just like a skilled conductor ensures harmony among musicians, CMMS integrates data, operations, and resources to orchestrate efficient maintenance workflows.
Unlike traditional methods reliant on paper records and manual processes, CMMS leverages digital prowess to streamline every facet of maintenance. It empowers maintenance teams to predict equipment failures before they occur, optimizing downtime and extending asset lifespan. This predictive capability is akin to a weather forecaster, preempting storms before they disrupt plans.
Moreover, CMMS acts as a storyteller of equipment health, narrating trends and patterns hidden within data streams. Much like a historian interpreting ancient scripts, it deciphers the language of machinery, translating it into actionable insights for decision-makers.
In essence, CMMS isn’t just about upgrading to digital; it’s about embracing a new era of maintenance intelligence. It transforms reactive firefighting into proactive strategy, ensuring operations hum along smoothly like a well-oiled machine. By fostering a culture of foresight and efficiency, CMMS paves the way for a future where downtime is minimized, costs are optimized, and productivity reaches new heights.
This digital revolution in engineering, driven by CMMS, heralds a future where maintenance isn’t a chore but a strategic advantage. It’s a journey from the manual to the digital, from uncertainty to foresight, marking a significant leap towards smarter, more sustainable industrial practices.
Streamlining Efficiency: The Role of CMMS in Modernizing Engineering Maintenance
In today’s fast-paced engineering landscape, efficiency is not just a goal but a necessity. As industries evolve, so do the demands on maintenance teams to keep operations running smoothly. This is where Computerized Maintenance Management Systems (CMMS) step in as crucial tools for modernizing engineering maintenance practices.
CMMS software empowers maintenance teams by centralizing essential information about equipment, assets, and work orders into one accessible platform. Imagine having a digital command center that tracks the health of every machine, schedules preventive maintenance tasks, and alerts technicians about potential issues before they escalate. This proactive approach not only minimizes downtime but also extends the lifespan of critical equipment.
One of the standout features of CMMS is its ability to streamline workflows. By automating routine tasks such as work order generation and inventory management, CMMS frees up valuable time for maintenance professionals to focus on more strategic initiatives. This efficiency not only reduces operational costs but also enhances overall productivity across the organization.
Moreover, CMMS provides valuable insights through detailed analytics and reporting capabilities. Maintenance managers can analyze historical data to identify trends, forecast maintenance needs, and optimize resource allocation. This data-driven decision-making not only improves efficiency but also supports continuous improvement efforts within the organization.
In essence, CMMS is not just a software tool but a catalyst for transformation in engineering maintenance. By embracing CMMS, organizations can achieve higher operational efficiency, reduce costs, and deliver superior service reliability to customers. As industries continue to evolve, the role of CMMS in modernizing engineering maintenance will only become more indispensable, driving sustainable growth and competitive advantage.
Predictive Power: How CMMS is Forecasting Maintenance Needs of Tomorrow
Imagine a world where machines predict their own maintenance needs before they break down. That’s the promise of Computerized Maintenance Management Systems (CMMS) today. CMMS isn’t just about fixing things when they break; it’s about foreseeing issues and preventing downtime altogether.
CMMS utilizes a blend of historical data, real-time analytics, and predictive algorithms to anticipate when equipment might fail. It’s like having a crystal ball for maintenance, but instead of magic, it’s powered by data. By analyzing past maintenance records and current operational data, CMMS can identify patterns and anomalies that might indicate a future problem.
Take a manufacturing plant, for example. With CMMS, instead of waiting for a critical machine to fail unexpectedly, maintenance teams receive alerts based on predictive analytics. These alerts allow them to schedule proactive maintenance during off-peak hours, minimizing disruptions to production. It’s akin to scheduling a doctor’s appointment before you feel ill, ensuring the health of your equipment and operations.
Moreover, CMMS doesn’t just stop at predicting breakdowns. It also optimizes maintenance schedules and inventory management, ensuring that the right parts are always available when needed. This proactive approach not only saves costs associated with emergency repairs but also enhances overall operational efficiency.
In essence, CMMS transforms maintenance from a reactive to a proactive strategy, leveraging data-driven insights to keep operations running smoothly. It’s the difference between fixing problems as they arise and anticipating needs before they become issues. As industries embrace digital transformation, CMMS emerges as a cornerstone technology, empowering businesses to stay ahead of maintenance challenges and embrace a future where downtime is minimized and productivity soars.
From Reactive to Proactive: CMMS and the Evolution of Maintenance Strategies
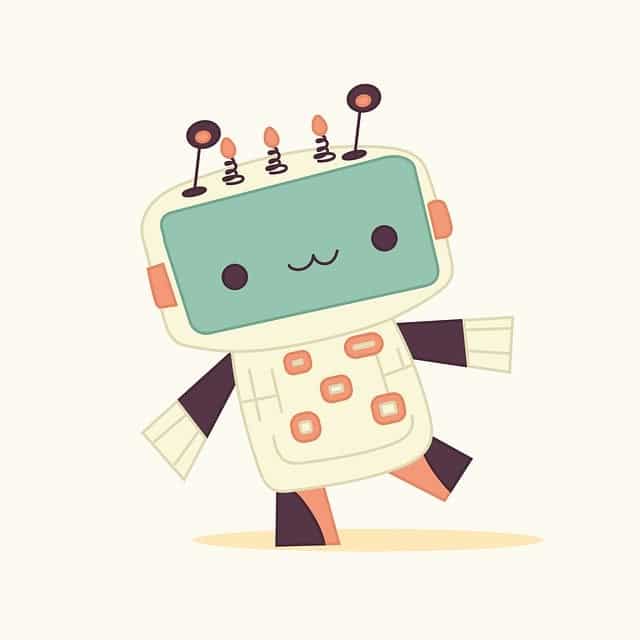
Imagine a factory where machines hum with precision, each part working in sync like a well-choreographed dance. Now, picture this efficiency maintained not by hurried repairs after breakdowns but by preemptive measures that nip potential issues in the bud. This is the promise of proactive maintenance, and at its heart lies CMMS.
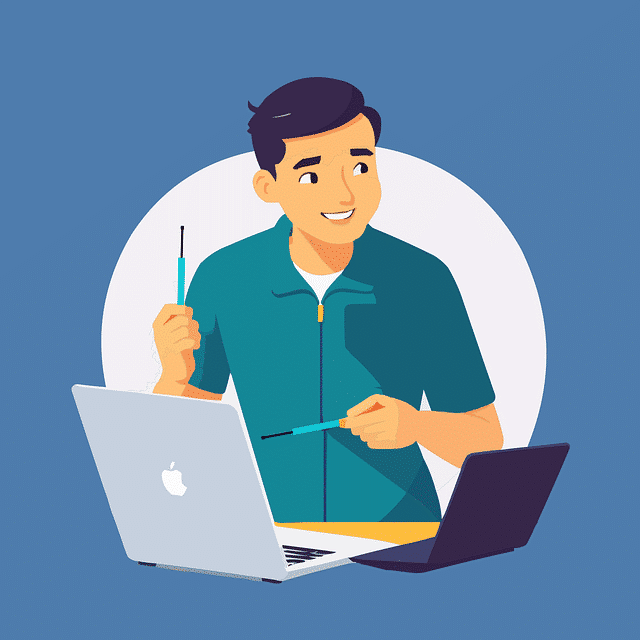
CMMS isn’t just a tool; it’s the brain behind the transformation. Traditionally, maintenance was reactive – fix it when it breaks. This approach led to costly downtime, emergency repairs, and frustrated production teams. Enter CMMS, equipped with predictive analytics and real-time data insights. It monitors equipment health, predicts failures before they occur, and schedules maintenance during downtimes that least impact operations.
Think of CMMS as a vigilant sentinel, constantly gathering data from machines, analyzing patterns, and issuing alerts when anomalies arise. It enables maintenance teams to shift from firefighting mode to strategic planning, allocating resources efficiently and maximizing equipment lifespan.
Analogous to a skilled doctor who prescribes preventive care to keep patients healthy, CMMS empowers industries to diagnose equipment issues early and prescribe preventive maintenance schedules. This proactive approach not only saves costs but also enhances reliability and safety, fostering a culture of continuous improvement.
As industries embrace digital transformation, CMMS stands as a beacon of innovation in maintenance strategies. It’s not just about fixing what’s broken; it’s about foreseeing challenges and preemptively addressing them. In the competitive realm of modern manufacturing and facilities management, proactive maintenance with CMMS isn’t just an option – it’s a necessity for staying ahead.
By adopting CMMS-driven proactive maintenance, industries can elevate their operational efficiency, reduce unplanned downtime, and ultimately, ensure smoother, more reliable production cycles. As technology continues to evolve, CMMS remains at the forefront, reshaping how maintenance is perceived – from reactive necessity to proactive advantage.
Harnessing Data for Success: CMMS Transforms Engineering Maintenance
Imagine a world where every piece of equipment in your facility communicates its health and performance in real-time. This isn’t science fiction—it’s the reality made possible by Computerized Maintenance Management Systems (CMMS). In today’s fast-paced industrial landscape, optimizing engineering maintenance isn’t just about fixing things when they break; it’s about proactive management and strategic decision-making fueled by data.
CMMS software serves as the backbone of modern maintenance operations, revolutionizing how engineers and maintenance teams approach their work. By centralizing data on equipment maintenance schedules, repair histories, and performance metrics, CMMS empowers organizations to predict failures before they occur. This proactive approach not only minimizes downtime but also extends the lifespan of critical assets, reducing overall operational costs.
One of the most compelling advantages of CMMS is its ability to transform raw data into actionable insights. Imagine each piece of machinery as a storyteller, constantly relaying information about its condition and usage patterns. Engineers can leverage this data to schedule maintenance tasks based on actual need rather than arbitrary schedules. This predictive maintenance strategy ensures that resources are allocated efficiently, maximizing uptime and productivity.
Furthermore, CMMS enhances regulatory compliance by maintaining accurate records of maintenance activities and inspections. This capability is crucial for industries with stringent safety and environmental regulations, ensuring that every operation meets or exceeds compliance standards.
In essence, CMMS isn’t just a tool—it’s a strategic asset that drives operational excellence. By harnessing the power of data, organizations can transition from reactive to proactive maintenance practices, paving the way for sustainable growth and competitive advantage in the market.
This article captures the transformative impact of CMMS on engineering maintenance while maintaining a conversational tone and emphasizing the power of data-driven decision-making. Let me know if there are any adjustments you’d like to make!
Efficiency Unleashed: CMMS and Its Impact on Tomorrow’s Engineering Operations
CMMS is the backbone of modern engineering operations, streamlining maintenance tasks, and optimizing asset management like never before. It’s like having a digital assistant that keeps all equipment in peak condition, ensuring smooth operations round the clock. From manufacturing plants to healthcare facilities, CMMS integrates seamlessly, enhancing efficiency and reliability.
Think of CMMS as your proactive partner in maintenance. It schedules routine tasks, tracks work orders, and even predicts equipment failures before they occur. By doing so, it prevents costly breakdowns and extends the lifespan of critical assets. Engineers can focus more on strategic projects rather than firefighting daily issues, thanks to CMMS’s predictive maintenance capabilities.
Moreover, CMMS doesn’t just stop at maintenance. It’s a data powerhouse, gathering insights that drive informed decision-making. Imagine having real-time analytics at your fingertips, guiding you on resource allocation, budgeting, and overall operational strategy. It’s like having a crystal ball that foresees challenges and suggests optimal solutions.
In essence, CMMS isn’t just a tool; it’s a catalyst for change in engineering operations. It empowers teams to work smarter, not harder, fostering a culture of efficiency and innovation. As industries evolve, CMMS remains at the forefront, adapting to new technologies and challenges, ensuring that tomorrow’s operations are not just efficient but also sustainable and resilient.
Frequently Asked Questions
How can CMMS improve efficiency and reduce downtime in engineering?
Learn how CMMS (Computerized Maintenance Management Systems) enhance efficiency and minimize downtime in engineering operations.
What are the key benefits of implementing CMMS in engineering operations?
Discover the essential advantages of integrating CMMS (Computerized Maintenance Management System) into engineering operations. Learn how CMMS enhances equipment reliability, reduces downtime, optimizes maintenance scheduling, and improves overall operational efficiency.
How does CMMS integrate with IoT and predictive maintenance technologies?
Learn how CMMS systems integrate seamlessly with IoT and predictive maintenance technologies, optimizing equipment management by leveraging real-time data for proactive maintenance, reducing downtime, and enhancing operational efficiency.
What is CMMS and how does it revolutionize maintenance practices?
Learn about CMMS (Computerized Maintenance Management System), a powerful tool that revolutionizes maintenance practices by centralizing asset management, scheduling maintenance tasks, tracking work orders, and optimizing equipment performance. Discover how CMMS enhances efficiency, reduces downtime, and improves asset lifespan through streamlined maintenance operations.
What are the essential features to look for when choosing a CMMS for engineering applications?
Discover the crucial features to consider when selecting a CMMS for engineering applications. Learn about essential functionalities that optimize maintenance scheduling, asset management, and reporting, ensuring streamlined operations and cost-efficiency.