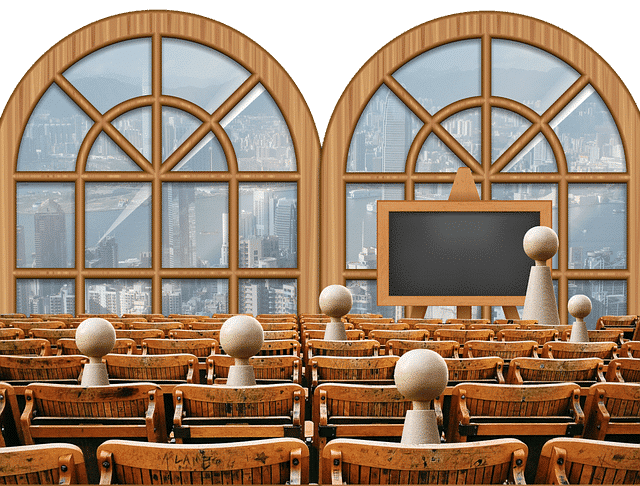
In today’s fast-paced industrial landscape, meeting production deadlines is crucial for maintaining competitiveness and customer satisfaction. One powerful tool that many manufacturing companies are turning to is CMMS (Computerized Maintenance Management System) integration. But can CMMS integration really help meet tighter production deadlines?
CMMS integration streamlines maintenance operations by centralizing data, scheduling tasks, and optimizing resources. By automating preventive maintenance schedules and reducing unplanned downtime, CMMS ensures that machinery and equipment are in optimal working condition, minimizing production interruptions.
Moreover, CMMS systems provide real-time insights into equipment performance and maintenance needs. This proactive approach allows manufacturing teams to identify potential issues before they escalate, thereby preventing costly breakdowns that could derail production schedules.
Beyond maintenance, CMMS integration enhances overall operational efficiency. It facilitates better coordination between maintenance and production teams, ensuring that maintenance tasks are aligned with production schedules. This synchronization helps in prioritizing critical maintenance activities without disrupting ongoing production processes.
Furthermore, CMMS enables data-driven decision-making by providing analytics on equipment reliability, maintenance costs, and downtime trends. These insights empower manufacturers to fine-tune production workflows, allocate resources more effectively, and optimize asset utilization—all contributing to meeting tighter production deadlines.
In essence, CMMS integration acts as a strategic ally in the quest for meeting tighter production deadlines. By improving equipment reliability, minimizing downtime, and enhancing operational efficiency, CMMS empowers manufacturing businesses to operate more competitively in today’s demanding market environment.
This article aims to highlight the benefits of CMMS integration in helping manufacturing businesses cope with the challenges of meeting stringent production deadlines, focusing on efficiency, reliability, and strategic decision-making.
Boosting Efficiency: How CMMS Integration Revolutionizes Production Timelines
CMMS, or Computerized Maintenance Management System, is a powerful tool designed to organize, track, and streamline maintenance operations within an organization. By integrating CMMS into production workflows, businesses can achieve significant improvements in efficiency and operational effectiveness.
One of the key benefits of CMMS integration lies in its ability to enhance asset management. With real-time data on equipment performance and maintenance schedules readily accessible, production managers can proactively address potential breakdowns and schedule preventive maintenance tasks without disrupting ongoing operations. This proactive approach not only minimizes downtime but also extends the lifespan of critical assets, ultimately boosting overall productivity.
Moreover, CMMS integration facilitates better resource allocation. By centralizing maintenance data and automating workflows, production teams can optimize labor resources and ensure that skilled technicians are deployed where they are most needed. This efficient allocation of resources translates into faster turnaround times for maintenance tasks and smoother production schedules.
Another significant advantage of CMMS integration is its role in data-driven decision-making. By collecting and analyzing comprehensive maintenance data, businesses can identify trends, predict equipment failures, and make informed decisions to optimize production processes. This proactive maintenance strategy not only reduces unexpected downtime but also enhances the reliability of production timelines.
Furthermore, CMMS integration fosters accountability and transparency across the organization. With clear visibility into maintenance activities and performance metrics, stakeholders can monitor progress in real-time and hold teams accountable for meeting production targets. This transparency promotes a culture of continuous improvement, where feedback loops and lessons learned from past maintenance events drive ongoing operational efficiencies.
In essence, CMMS integration represents more than just a technological upgrade—it’s a catalyst for transforming production timelines. By leveraging real-time data insights, optimizing resource allocation, and fostering a culture of proactive maintenance, businesses can streamline operations, minimize disruptions, and ultimately enhance their competitive edge in the market.
Strategic Advantage: Achieving Tight Production Deadlines with CMMS Integration
CMMS, or Computerized Maintenance Management System, is more than just a tool for scheduling maintenance tasks. When integrated strategically into your production processes, CMMS can optimize workflows, enhance resource allocation, and ultimately, boost your efficiency in meeting production deadlines.
One of the key advantages of CMMS integration is its ability to centralize data and communication. Think of it as a conductor orchestrating a symphony. By keeping all maintenance schedules, equipment records, and work orders in one accessible place, CMMS ensures that everyone involved in the production process is on the same page. This centralized approach minimizes delays caused by miscommunication or outdated information, allowing your team to focus squarely on achieving those critical deadlines.
Moreover, CMMS provides real-time insights and analytics that empower decision-making. It’s like having a crystal ball that predicts equipment failures before they occur, thus preventing unexpected downtime that could derail your production timeline. By proactively addressing maintenance issues and optimizing equipment uptime, CMMS helps maintain a smooth and uninterrupted workflow.
Integration with CMMS also supports predictive maintenance strategies. Instead of waiting for something to break down, predictive maintenance uses data analytics to identify potential issues early on. This proactive approach not only extends the lifespan of your equipment but also minimizes unplanned downtime, ensuring that your production line keeps humming along as planned.
Maximizing Output: The Impact of CMMS Integration on Meeting Production Targets
In today’s fast-paced industrial landscape, meeting production targets efficiently is crucial for businesses aiming to stay competitive. One of the game-changing tools in achieving this efficiency is Computerized Maintenance Management Systems (CMMS). These systems not only streamline maintenance operations but also play a pivotal role in maximizing overall output.
CMMS integration brings a myriad of benefits to production environments. By centralizing maintenance data and workflows, it allows for better tracking of equipment performance and downtime. This proactive approach enables maintenance teams to identify potential issues before they escalate, minimizing unplanned downtime that can hinder production schedules.
Moreover, CMMS systems facilitate preventive maintenance scheduling based on equipment usage and performance data. This means machines are serviced at optimal intervals, reducing the likelihood of breakdowns during critical production periods. Imagine a factory floor where machines are always operating at peak efficiency, thanks to timely maintenance driven by CMMS insights.
Another significant impact of CMMS integration is improved resource allocation. With real-time visibility into asset availability and condition, production managers can allocate resources more effectively. This includes manpower, spare parts, and equipment, ensuring that production lines run smoothly without delays caused by resource shortages.
Furthermore, CMMS enhances data-driven decision-making. Detailed analytics provided by these systems offer valuable insights into equipment lifecycle costs, maintenance trends, and overall operational efficiency. Armed with this information, businesses can make informed decisions to optimize production processes and investments.
On Time, Every Time: Enhancing Production Schedules with CMMS Integration
In today’s fast-paced manufacturing landscape, keeping production schedules on track is crucial for efficiency and profitability. One powerful tool that industry leaders are increasingly turning to is Computerized Maintenance Management Systems (CMMS). These systems not only streamline maintenance tasks but also play a pivotal role in enhancing production schedules.
CMMS integration offers a systematic approach to scheduling maintenance activities, ensuring that machines and equipment remain operational without unexpected downtime. By scheduling preventive maintenance tasks proactively, manufacturers can avoid costly breakdowns that disrupt production flow. This proactive approach not only saves time but also reduces overall maintenance costs, contributing to improved profitability.
Moreover, CMMS systems provide real-time insights into equipment performance and maintenance history. This data-driven approach allows production managers to make informed decisions regarding scheduling and resource allocation. For instance, predictive maintenance capabilities within CMMS predict potential equipment failures based on historical data, enabling preemptive action to be taken before issues arise.
Beyond maintenance, CMMS integration facilitates better coordination between maintenance teams and production schedules. It ensures that maintenance activities are aligned with production downtime windows, minimizing disruption to the workflow. This synchronization optimizes the use of resources and manpower, leading to smoother operations and enhanced productivity.
In essence, CMMS integration transforms production scheduling by leveraging technology to maintain equipment reliability and optimize efficiency. By integrating CMMS into their operations, manufacturers can achieve the dual goals of maximizing uptime and meeting production deadlines consistently. This strategic use of technology not only enhances operational efficiency but also strengthens the overall competitiveness of manufacturing enterprises in today’s dynamic market environment.
This article aims to capture the essence of using CMMS to enhance production schedules, focusing on its benefits and practical applications in a conversational and engaging manner.
From Concept to Completion: How CMMS Integration Streamlines Production Deadlines
Imagine a factory floor buzzing with activity, where every machine plays a crucial role in the production line. Ensuring these machines operate smoothly is not just about fixing them when they break down but preventing breakdowns altogether. This proactive approach is at the heart of CMMS integration. By digitizing maintenance processes and schedules, CMMS allows maintenance teams to schedule preventive maintenance tasks based on real-time data and predictive analytics. This means fewer unexpected breakdowns and downtime, keeping production lines running smoothly and deadlines on track.
Moreover, CMMS doesn’t just stop at maintenance scheduling. It also integrates seamlessly with other operational systems like inventory management and procurement. This integration ensures that the right parts and supplies are always available when needed, further minimizing delays caused by shortages or logistical issues.
One of the most significant advantages of CMMS integration is its ability to provide detailed insights into equipment performance and maintenance history. This data-driven approach allows facilities to identify recurring issues, optimize maintenance strategies, and even predict when equipment might need replacement or major repairs. By addressing these issues proactively, facilities can extend the lifespan of their equipment and avoid costly disruptions to production schedules.
In essence, CMMS integration is more than just a tool; it’s a strategic asset that empowers facilities to maximize productivity, minimize downtime, and ultimately, deliver products to market faster. As industries continue to evolve, the role of CMMS in streamlining production deadlines will only grow, making it a cornerstone of modern manufacturing and facility management practices.
Breaking Barriers: CMMS Integration as the Key to Meeting Aggressive Production Goals
In today’s fast-paced industrial landscape, meeting aggressive production goals is no longer just a challenge but a necessity for staying competitive. To achieve this, companies are turning to advanced solutions like Computerized Maintenance Management Systems (CMMS) integrated with their production processes.
CMMS integration breaks down traditional barriers by streamlining maintenance operations and enhancing overall efficiency. By seamlessly integrating maintenance tasks with production schedules, CMMS ensures that equipment downtime is minimized and productivity is maximized. This integration allows for real-time monitoring of equipment health, predictive maintenance scheduling, and swift resolution of issues before they escalate.
Imagine a factory floor where every machine communicates its operational status in real-time, allowing maintenance teams to proactively address potential problems. This proactive approach not only reduces unplanned downtime but also extends the lifespan of critical equipment, saving substantial costs in the long run.
Moreover, CMMS integration empowers decision-makers with valuable data insights. By analyzing historical maintenance data and production metrics, managers can identify trends, optimize workflows, and make data-driven decisions to further boost efficiency and meet aggressive production targets.
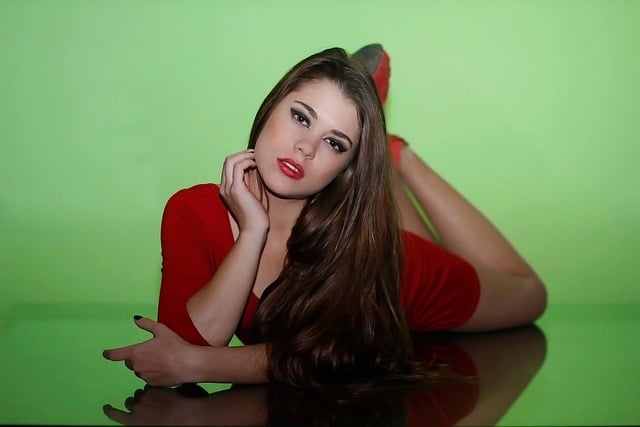
In essence, CMMS integration is more than just a tool—it’s a strategic asset that transforms how modern industries operate. It fosters collaboration between maintenance and production teams, aligning their efforts towards a common goal of maximizing uptime and output. By breaking down silos and enhancing communication, CMMS integration creates a synergistic environment where efficiency thrives and barriers to productivity are dismantled.
Beyond Limits: How CMMS Integration Redefines Speed and Accuracy in Production
CMMS systems are designed to streamline maintenance operations by centralizing data, automating workflows, and providing real-time insights. By integrating CMMS into production processes, companies can significantly enhance both speed and accuracy. Here’s how:
Firstly, CMMS integration eliminates the inefficiencies of manual maintenance tracking. Instead of relying on cumbersome paperwork or outdated spreadsheets, workers can access comprehensive maintenance schedules and historical data instantly. This accessibility not only speeds up decision-making but also reduces downtime by preemptively addressing potential issues.
Secondly, the accuracy of maintenance tasks is greatly improved through CMMS integration. Automated alerts and notifications ensure that preventive maintenance tasks are completed on time, reducing the risk of equipment failure and costly repairs. With predictive maintenance capabilities, CMMS systems can even anticipate maintenance needs based on historical data and performance trends.
Moreover, CMMS integration facilitates better resource allocation. By optimizing maintenance schedules and resource usage, companies can minimize idle time and maximize productivity. This efficiency translates into tangible cost savings and improved overall performance metrics.
In essence, CMMS integration goes beyond traditional maintenance approaches by offering a holistic solution that enhances operational speed and accuracy. It empowers production teams to operate at peak efficiency, meeting demands with minimal disruptions. As industries evolve, embracing CMMS integration becomes not just a choice but a strategic advantage in staying competitive and adaptable to changing market dynamics.
This seamless integration of technology into everyday operations illustrates how forward-thinking businesses are redefining production standards. By leveraging CMMS capabilities, companies can achieve unprecedented levels of efficiency and reliability, setting new benchmarks for success in the modern industrial landscape.
Frequently Asked Questions
How can CMMS integration optimize production scheduling and workflow
Learn how integrating CMMS (Computerized Maintenance Management System) can streamline production scheduling and workflow, improving efficiency by automating maintenance tasks, minimizing downtime, and optimizing resource allocation.
Which industries benefit the most from CMMS integration in deadline-driven environments
Discover which industries benefit the most from CMMS integration in deadline-driven environments. Learn how CMMS enhances efficiency and reduces downtime in manufacturing, healthcare, facilities management, and more.
What are the key benefits of using CMMS integration for meeting tight production deadlines
Discover the key benefits of utilizing CMMS integration to meet stringent production deadlines efficiently. Enhance scheduling, reduce downtime, optimize resource allocation, and ensure timely maintenance for seamless workflow.
What is CMMS integration and how does it relate to production deadlines
CMMS integration refers to the process of connecting Computerized Maintenance Management Systems with other production systems to streamline maintenance operations and enhance efficiency. It helps ensure that maintenance tasks are scheduled and executed promptly, reducing downtime and aligning with production deadlines.
What are some practical tips for implementing CMMS integration to improve deadline management
Discover practical tips for integrating CMMS to enhance deadline management. Learn how to streamline workflows, sync schedules, and optimize task allocation. Improve efficiency and meet project milestones effectively.