Imagine a world where machines could predict their own maintenance needs before they broke down. Sounds like something straight out of a sci-fi movie, right? Well, thanks to advancements in technology, this futuristic scenario is becoming a reality in the realm of maintenance management.
AI (Artificial Intelligence) and IoT (Internet of Things) are revolutionizing the way we approach maintenance, particularly when integrated with CMMS (Computerized Maintenance Management Systems). Let’s break down what this means and why it’s generating so much buzz.
Firstly, AI brings the power of predictive analytics to CMMS. Traditionally, maintenance tasks were scheduled based on predetermined intervals or when something went wrong. Now, with AI algorithms analyzing vast amounts of data from IoT sensors embedded in machinery, systems can predict failures before they happen. This proactive approach minimizes downtime and reduces costs significantly.
Picture this: a factory floor equipped with IoT sensors continuously monitoring equipment performance. These sensors collect real-time data on metrics like temperature, vibration, and usage patterns. AI processes this data, identifying patterns that indicate potential issues. Maintenance teams receive alerts suggesting preemptive actions, preventing costly breakdowns and optimizing asset lifespan.
Moreover, AI doesn’t just stop at predictive maintenance. It also enhances decision-making processes. By analyzing historical data, AI can recommend optimal maintenance schedules based on usage patterns and environmental conditions. This data-driven approach ensures resources are allocated efficiently, maximizing productivity and minimizing operational disruptions.
Now, let’s talk about the synergy between AI, IoT, and CMMS. While AI analyzes data and predicts maintenance needs, CMMS acts as the central hub where all this information is managed. Think of CMMS as the conductor in an orchestra, coordinating maintenance activities based on insights provided by AI and IoT.
Revolutionizing Maintenance: How AI and IoT Are Transforming CMMS Systems
Imagine a facility where machines preemptively signal their need for maintenance before a breakdown occurs—a scenario made possible by AI and IoT integration. These technologies allow CMMS to collect real-time data from equipment sensors, analyzing performance metrics and identifying anomalies. This proactive approach not only prevents costly downtime but also optimizes maintenance schedules, reducing overall operational expenses.
AI’s role in this transformation is pivotal. Machine learning algorithms sift through vast amounts of historical and real-time data, learning patterns and predicting future maintenance needs with unprecedented accuracy. It’s like having a predictive maintenance expert on staff 24/7, continuously improving its insights as it gathers more data—a capability that traditional CMMS could only dream of.
Moreover, IoT devices act as the eyes and ears of the operation, monitoring equipment health metrics such as temperature, vibration, and energy consumption in real-time. They provide a constant stream of data that AI algorithms analyze, enabling maintenance teams to intervene precisely when needed, ensuring equipment operates at peak efficiency.
This symbiotic relationship between AI and IoT not only enhances operational efficiency but also transforms how maintenance is perceived—from a reactive chore to a proactive strategy that drives business competitiveness. Companies embracing these technologies gain a significant edge, not just in terms of cost savings but also in reliability and customer satisfaction.
Future-Proofing Facilities: Integrating AI and IoT for Enhanced Maintenance Efficiency
Imagine a facility where every component, from HVAC systems to production machinery, operates not just reactively but proactively. AI algorithms analyze vast amounts of real-time data collected by IoT sensors embedded throughout the facility. These sensors monitor equipment performance, environmental conditions, and energy consumption, providing a continuous stream of actionable insights.
By harnessing AI, facilities can predict maintenance needs before issues arise. Machine learning algorithms detect patterns indicative of potential failures, allowing maintenance teams to intervene preemptively. This predictive maintenance approach not only minimizes downtime but also extends the lifespan of critical assets, ultimately reducing operational costs.
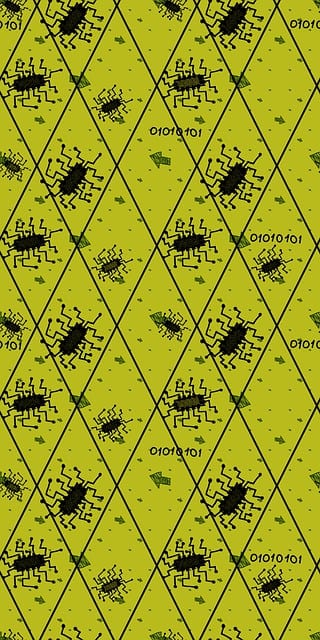
Moreover, AI-driven analytics enhance decision-making processes. Facility managers gain deep visibility into performance metrics and operational trends. They can optimize resource allocation, streamline workflows, and identify areas for improvement with unprecedented precision.
The synergy of AIoT doesn’t just stop at maintenance. It transforms facilities into adaptive ecosystems. Smart buildings adjust lighting, heating, and ventilation based on occupancy patterns and environmental conditions, enhancing energy efficiency and occupant comfort.
In essence, AIoT isn’t just about integrating technology; it’s about transforming facilities into intelligent entities capable of self-monitoring, self-diagnosing, and self-optimizing. It’s the marriage of data-driven insights and automation, empowering facilities to thrive in a future where adaptability and efficiency are paramount.
As industries continue to evolve, those embracing AIoT are poised to lead the charge towards smarter, more sustainable operations. The journey towards future-proofing facilities begins with embracing the transformative power of AI and IoT, ensuring readiness for whatever challenges the future may hold.
Smart Maintenance Solutions: Harnessing AI and IoT in CMMS Implementation
Imagine a facility where machines predict their own maintenance needs, reducing downtime to a bare minimum. This is the promise of AI-powered CMMS systems. By analyzing historical data and real-time sensor inputs from IoT devices, these systems can forecast equipment failures before they happen. They not only detect anomalies but also prescribe proactive maintenance schedules, optimizing operational efficiency.
AI algorithms, akin to vigilant digital overseers, continuously learn from data patterns, enhancing their predictive accuracy over time. This adaptive learning capability allows CMMS to evolve from reactive to proactive maintenance strategies, saving costs and boosting productivity.
Moreover, IoT sensors play a crucial role by providing a steady stream of operational data. They monitor equipment conditions such as temperature, vibration, and performance metrics in real time. This constant monitoring enables early detection of potential issues, preventing catastrophic failures and extending asset lifespans.
Implementing AI and IoT in CMMS isn’t just about predicting breakdowns; it’s about transforming maintenance into a strategic advantage. Organizations can shift from costly scheduled maintenance to more efficient, need-based repairs, thereby optimizing resource allocation and minimizing downtime disruptions.
From Theory to Practice: Implementing AI and IoT in CMMS for Improved Asset Management
AI, or Artificial Intelligence, in CMMS refers to the ability of software to analyze data from various sources and make intelligent predictions. It’s like having a smart assistant that can sift through mountains of maintenance data, detect patterns, and suggest optimized maintenance schedules. For example, AI can analyze historical maintenance records and equipment performance data to predict when a machine might fail, allowing proactive maintenance rather than reactive fixes.
On the other hand, IoT, or the Internet of Things, involves connecting devices and machines to collect real-time data. In CMMS, IoT sensors installed on equipment continuously gather information such as temperature, vibration, or operating hours. This data is then fed into the AI algorithms within the CMMS, providing a real-time view of equipment health and performance.
Together, AI and IoT transform CMMS into a predictive and prescriptive maintenance powerhouse. Instead of relying on scheduled maintenance or waiting for equipment to break down, organizations can anticipate issues and intervene proactively. This not only reduces downtime but also extends the lifespan of assets and lowers maintenance costs significantly.
Moreover, the implementation of AI and IoT in CMMS isn’t limited to large enterprises. Small and medium-sized businesses are also embracing this technology to gain a competitive edge. Imagine a factory where every machine is interconnected, communicating its status and health in real-time, while AI algorithms analyze this data to optimize operations seamlessly.
Integrating AI and IoT into CMMS is more than a technological upgrade—it’s a strategic decision to enhance asset management practices. By leveraging these technologies, businesses can achieve higher operational efficiency, reduced downtime, and ultimately, improved profitability. The future of maintenance management is here, and it’s intelligent, interconnected, and incredibly promising.
Predictive Maintenance Redefined: The Role of AI and IoT in Modern CMMS Strategies
In today’s tech-driven era, AI and IoT have revolutionized Computerized Maintenance Management Systems (CMMS). These smart systems go beyond traditional scheduled maintenance by analyzing real-time data from sensors embedded in machinery. They become the eyes and ears of the operation, detecting anomalies, predicting failures, and prescribing maintenance tasks proactively.
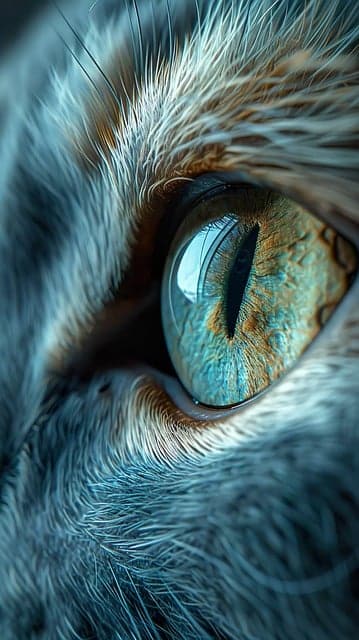
Think of it as having a personal health monitor for your machinery. Just like how a fitness tracker alerts you to irregular heartbeats, AI-powered CMMS monitors machine vibrations, temperatures, and performance metrics. It collects this data, crunches numbers using machine learning algorithms, and identifies patterns that indicate potential issues. This preemptive approach not only prevents unexpected downtime but also extends the lifespan of equipment, saving businesses significant time and money.
Furthermore, AI enhances CMMS by continuously learning from data streams. It adapts to changing operational conditions and refines its predictive accuracy over time. This adaptive capability is akin to how a seasoned chef adjusts seasoning to perfect a dish—always improving, always optimizing.
IoT plays a crucial role by connecting disparate components into a cohesive network. Sensors placed strategically throughout the production line or facility gather data in real-time. This interconnectedness allows for swift decision-making based on actual performance metrics rather than assumptions.
In essence, AI and IoT redefine Predictive Maintenance by making it smarter, faster, and more efficient. They transform reactive maintenance practices into proactive strategies, where potential issues are addressed before they disrupt operations. It’s like having a crystal ball that not only foresees problems but also suggests precise actions to mitigate them.
As industries embrace this technological evolution, the future of maintenance shifts from guesswork to data-driven certainty. The synergy of AI and IoT in CMMS isn’t just about innovation—it’s about staying ahead in a competitive landscape where every minute of uptime counts.
Unlocking the Power of Data: AI, IoT, and CMMS Synergy in Maintenance Operations
In today’s digital age, the convergence of Artificial Intelligence (AI), Internet of Things (IoT), and Computerized Maintenance Management Systems (CMMS) is revolutionizing maintenance operations across industries. These technologies, when combined synergistically, empower organizations to enhance operational efficiency, reduce downtime, and optimize resource allocation.
AI plays a pivotal role by leveraging machine learning algorithms to analyze vast amounts of data generated by IoT devices. These devices, embedded with sensors, collect real-time operational data from machinery and equipment. AI algorithms process this data to identify patterns, predict potential failures, and recommend proactive maintenance schedules. By anticipating issues before they occur, AI helps organizations shift from reactive to predictive maintenance strategies, thereby minimizing unplanned downtime and extending asset lifespan.
IoT devices act as the frontline data collectors in this ecosystem. They monitor equipment performance metrics such as temperature, vibration, and operational cycles. This continuous stream of data enables maintenance teams to monitor asset health in real-time and detect anomalies promptly. For instance, IoT sensors installed on manufacturing equipment can alert technicians to deviations from normal operating parameters, allowing for timely intervention to prevent breakdowns.
CMMS platforms serve as the centralized hub where all maintenance data converges. They facilitate the organization, scheduling, and execution of maintenance tasks based on AI insights and IoT data inputs. CMMS software also tracks historical maintenance records, equipment manuals, and warranty information, providing technicians with comprehensive asset visibility. This unified approach streamlines maintenance workflows, improves response times, and ensures compliance with regulatory requirements.
The synergy between AI, IoT, and CMMS transforms maintenance operations into a proactive and data-driven discipline. Organizations harness the power of predictive analytics to optimize spare parts inventory, allocate resources efficiently, and prioritize critical maintenance tasks. By embracing these technologies, businesses not only enhance operational reliability but also achieve significant cost savings and competitive advantage in today’s dynamic marketplace.
This integration of AI, IoT, and CMMS marks a paradigm shift in how maintenance is managed, moving beyond traditional reactive methods to a predictive and preventative approach. As industries continue to digitize and adopt smart technologies, the role of data-driven maintenance becomes increasingly indispensable in ensuring sustainable business success.
The Digital Maintenance Frontier: AI and IoT Integration in CMMS Technologies
AI, with its ability to analyze vast amounts of data and learn from patterns, transforms CMMS by enabling predictive maintenance. Instead of reacting to equipment failures, AI algorithms proactively identify potential issues based on real-time data from IoT sensors. These sensors, embedded in machinery, collect and transmit data on performance metrics like temperature, pressure, and usage patterns. They act as the eyes and ears of the system, feeding continuous streams of information to AI algorithms.
Picture an AI-powered CMMS predicting a conveyor belt’s maintenance needs before it breaks down, thus preventing costly downtime and ensuring smooth operations. This proactive approach not only saves money but also enhances safety and reliability in industrial settings.
Moreover, AI in CMMS streamlines decision-making processes by analyzing historical data to optimize maintenance schedules. It can prioritize tasks based on criticality and resource availability, maximizing operational efficiency. This efficiency extends to inventory management, as AI can forecast spare parts requirements with precision, reducing inventory costs while ensuring availability.
Incorporating IoT into CMMS further enhances its capabilities by enabling remote monitoring and control. Imagine technicians receiving real-time alerts on their smartphones about equipment malfunctions, even before these issues affect production. IoT sensors facilitate condition-based monitoring, allowing for timely interventions that prolong equipment lifespan and improve overall asset performance.
Frequently Asked Questions
What IoT devices can be integrated with CMMS for better asset management?
Discover how integrating IoT devices with CMMS enhances asset management efficiency. Learn about the IoT devices compatible with CMMS systems, optimizing maintenance schedules and asset performance.
What are the challenges of implementing AI and IoT with CMMS, and how can they be overcome?
Challenges of integrating AI and IoT with CMMS include data interoperability, cybersecurity risks, and system complexity. Overcoming these challenges involves standardizing data formats, implementing robust security measures, and ensuring seamless integration through careful planning and testing.
How can AI-driven analytics improve efficiency in maintenance tasks with CMMS?
Learn how AI-driven analytics enhance efficiency in maintenance tasks with CMMS by predicting equipment failures, optimizing schedules, and automating data analysis for proactive maintenance.
How does AI enhance predictive maintenance when combined with CMMS?
Learn how AI enhances predictive maintenance when integrated with CMMS (Computerized Maintenance Management Systems). Discover how AI algorithms analyze historical data from CMMS to predict equipment failures, optimize maintenance schedules, and reduce downtime, thereby improving overall operational efficiency.
What are the benefits of integrating AI and IoT with CMMS for maintenance operations?
Learn about the advantages of combining AI and IoT with CMMS for streamlined maintenance operations, enhancing predictive maintenance capabilities, optimizing asset performance, reducing downtime, and improving overall operational efficiency.