A CMMS is essentially a digital toolkit that empowers maintenance teams to streamline their operations, manage assets efficiently, and respond promptly to urgent maintenance needs. It acts as a centralized hub where all maintenance-related information converges, from scheduled tasks to real-time alerts and historical data. Picture it as a control center where every detail of your facility’s maintenance activities is meticulously tracked and readily accessible.
In emergency maintenance scenarios, the immediacy with which a CMMS can dispatch work orders and prioritize tasks becomes invaluable. Maintenance technicians receive instant notifications on their mobile devices, detailing the issue at hand and its criticality. This ensures they can swiftly mobilize with the right tools and expertise to address the problem head-on, minimizing downtime and preventing further escalation.
Moreover, a well-implemented CMMS doesn’t just react to emergencies; it proactively mitigates risks. By scheduling preventive maintenance tasks and conducting regular inspections, potential issues can be identified and resolved before they manifest into full-blown crises. Think of it as regularly servicing your car to avoid a breakdown on a long road trip—you invest a little time and effort upfront to ensure smooth sailing ahead.
Furthermore, the data analytics capabilities of modern CMMS platforms offer insights that drive continuous improvement in maintenance strategies. By analyzing trends and performance metrics, facilities can optimize their asset lifecycle management and make informed decisions about resource allocation and future investments. It’s like having a crystal ball that helps you foresee maintenance needs and plan accordingly, ensuring operational resilience and efficiency.
Saving Time and Resources: How CMMS Software Streamlines Emergency Maintenance
Imagine a scenario where a critical piece of machinery breaks down unexpectedly. In traditional setups, this would trigger a flurry of reactive responses, leading to potential delays, extended downtimes, and increased costs. However, with CMMS software in place, the approach shifts from reactive to proactive. By centralizing all maintenance activities into a single digital platform, CMMS enables maintenance teams to swiftly identify, prioritize, and resolve emergency issues.
The core strength of CMMS lies in its ability to automate workflows. Upon receiving an emergency maintenance request, the software initiates predefined protocols, such as alerting the right personnel, assigning tasks based on skill sets and availability, and even ordering necessary parts or equipment automatically. This automation not only accelerates response times but also minimizes human error, ensuring that every step of the process is carried out efficiently.
Moreover, CMMS software acts as a comprehensive repository of historical data and maintenance records. This means that maintenance managers can quickly access past maintenance logs, equipment histories, and performance metrics, aiding in diagnosing recurring issues and making informed decisions for future preventive measures.
In essence, CMMS software transforms emergency maintenance into a structured, streamlined process. It empowers maintenance teams to act decisively, reduce unplanned downtime, optimize resource allocation, and ultimately, uphold operational continuity. By harnessing the power of technology, facilities can navigate emergencies with agility and precision, safeguarding their assets and enhancing overall productivity.
Ensuring Operational Continuity: CMMS Systems in Emergency Repair Management
When disaster strikes, whether it’s a sudden equipment breakdown or a critical facility issue, operational continuity becomes paramount. This is where Computerized Maintenance Management Systems (CMMS) step in as invaluable tools for emergency repair management. CMMS systems are the backbone of modern maintenance strategies, combining technology with efficient workflows to minimize downtime and swiftly address emergencies.
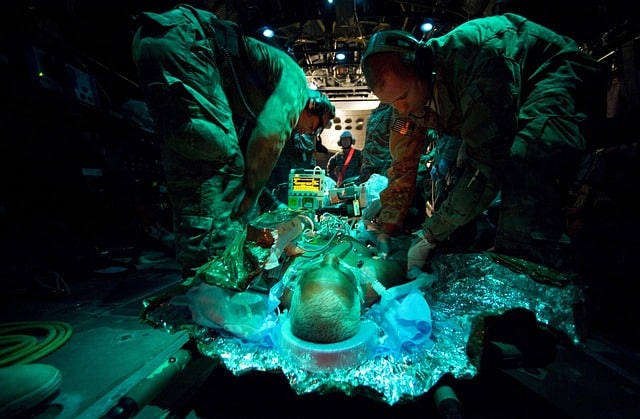
Imagine a scenario where a manufacturing plant experiences a crucial machinery failure during peak production hours. Without a proactive system in place, every minute of downtime translates to significant losses in productivity and revenue. Here, CMMS systems shine by centralizing maintenance operations, enabling real-time tracking of equipment status, and automating repair workflows.
These systems operate on a simple yet powerful premise: prevention is better than cure. By scheduling routine maintenance tasks and conducting predictive analyses, CMMS not only reduces the likelihood of sudden breakdowns but also ensures that maintenance teams are well-prepared for any emergency. This proactive approach transforms reactive emergency management into a controlled response system.
Moreover, CMMS systems facilitate seamless communication between maintenance teams, managers, and stakeholders. Through mobile access and cloud-based platforms, critical information flows effortlessly, enabling quick decision-making even in high-pressure situations. This transparency and accessibility are crucial for maintaining operational continuity and mitigating the impact of emergencies.
In essence, the integration of CMMS systems into emergency repair management represents a paradigm shift towards efficiency and resilience. By leveraging technology to predict, prepare, and respond, organizations can safeguard their operations against disruptions, uphold service levels, and uphold the trust of their customers.
From Crisis to Control: CMMS Solutions for Rapid Maintenance Responses
CMMS solutions are designed to streamline maintenance workflows, from identifying issues to scheduling repairs and tracking maintenance history. They act as a digital hub where facility managers, technicians, and stakeholders can converge to ensure prompt resolution of maintenance needs.
One of the standout features of CMMS solutions is their ability to facilitate rapid responses to crises. When an unexpected breakdown occurs, time is of the essence. With CMMS, maintenance teams can receive instant alerts, detailing the nature and location of the issue. This proactive notification system ensures that technicians can swiftly mobilize, armed with all the information they need to diagnose and fix the problem promptly.
Moreover, CMMS software isn’t just reactive; it empowers proactive maintenance strategies. By analyzing historical data and trends, CMMS can predict potential equipment failures before they occur. This predictive capability allows maintenance teams to preemptively schedule inspections and preventive maintenance tasks, reducing the likelihood of sudden breakdowns.
Furthermore, CMMS solutions enhance overall operational efficiency. By automating routine tasks such as work orders, inventory management, and asset tracking, they free up valuable time for maintenance teams to focus on more strategic initiatives. This efficiency not only cuts down on downtime but also optimizes resource allocation and improves the longevity of critical assets.
In essence, transitioning from crisis to control with CMMS solutions means more than just managing maintenance; it’s about empowering organizations to operate smoothly and resiliently. With real-time insights, predictive analytics, and streamlined workflows, CMMS solutions are pivotal in transforming how businesses respond to and manage maintenance challenges, ensuring smoother operations and sustained productivity.
Emergency Preparedness Redefined: The Power of CMMS in Maintenance
CMMS platforms empower maintenance teams by centralizing critical data on equipment, assets, and workflows. Imagine having a robust tool at your fingertips that not only schedules routine maintenance but also alerts you to potential issues before they escalate into emergencies. It’s like having a proactive guardian that prevents downtime and ensures operational continuity.
In the face of crises, whether it’s a sudden breakdown or a natural disaster, CMMS enables rapid response. With real-time data and predictive analytics, maintenance personnel can swiftly assess the situation, prioritize tasks, and deploy resources efficiently. It’s akin to having a well-drilled emergency response team that springs into action at a moment’s notice, minimizing downtime and reducing costs.
Furthermore, CMMS transforms reactive maintenance into proactive strategies. By continuously monitoring equipment performance and conducting preventive maintenance based on data-driven insights, organizations can preemptively address potential failures. This proactive approach not only enhances equipment reliability but also strengthens overall emergency preparedness.
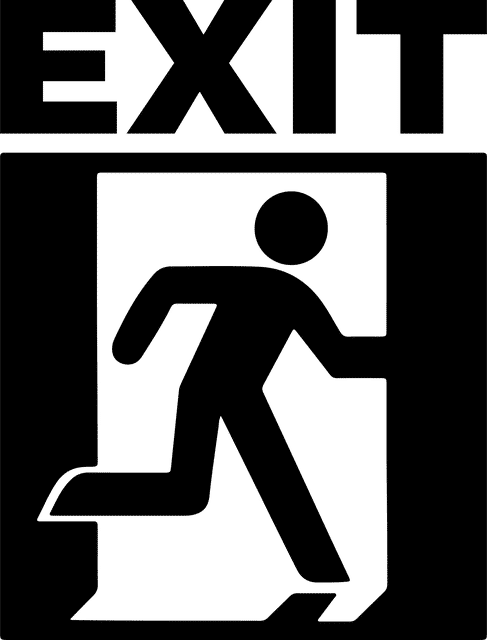
In essence, CMMS redefines emergency preparedness by embedding resilience into everyday operations. It equips organizations with the foresight and agility needed to navigate challenges seamlessly. Just as a ship relies on its navigational systems to steer clear of storms, businesses equipped with CMMS navigate uncertainties with confidence, ensuring they stay afloat and operational when faced with unexpected disruptions.
Frequently Asked Questions
What is CMMS and how does it support emergency maintenance?
Learn what CMMS (Computerized Maintenance Management System) is and how it facilitates emergency maintenance tasks efficiently. Discover its role in enabling quick response times, ensuring equipment reliability, and minimizing downtime during urgent maintenance needs.
Why is CMMS essential for managing unexpected maintenance tasks?
Discover why CMMS (Computerized Maintenance Management System) is crucial for handling unexpected maintenance tasks efficiently. Learn how it streamlines scheduling, tracks equipment health, and reduces downtime, ensuring optimal operations.
How can CMMS software improve response times during emergencies?
Learn how CMMS software enhances emergency response times through streamlined communication, prioritized task management, and real-time access to critical data.
How does CMMS help prioritize emergency repairs?
Learn how CMMS systems streamline emergency repair prioritization, ensuring critical issues are promptly addressed to minimize downtime and maintain operational efficiency.
What features should a CMMS have to handle emergency maintenance effectively?
A CMMS (Computerized Maintenance Management System) should include features like real-time alerts, prioritization of urgent tasks, mobile accessibility for field staff, detailed asset history tracking, and seamless integration with emergency response protocols to effectively manage emergency maintenance.