In today’s interconnected world, maintaining equipment and facilities to global standards is crucial for businesses aiming to stay competitive. Computerized Maintenance Management Systems (CMMS) play a pivotal role in achieving and surpassing these standards. CMMS software empowers organizations by centralizing maintenance operations, streamlining workflows, and enhancing overall efficiency.
Imagine a scenario where a multinational corporation operates various manufacturing plants across different continents. Each facility requires meticulous upkeep to ensure optimal performance and safety compliance. Here, CMMS acts as the backbone of maintenance operations, enabling seamless coordination between teams regardless of geographical location.
One of the primary benefits of CMMS is its ability to standardize maintenance procedures. By digitizing work orders, scheduling preventive maintenance, and tracking asset histories, CMMS ensures consistency in maintenance practices across all sites. This standardization not only improves reliability but also reduces downtime and extends the lifespan of critical assets.
Moreover, CMMS facilitates real-time data management. Supervisors can monitor maintenance activities remotely, access live updates on work progress, and make data-driven decisions swiftly. This capability not only enhances operational transparency but also enables proactive maintenance strategies that prevent costly breakdowns.
In essence, CMMS transforms how global maintenance standards are achieved and maintained. It fosters collaboration, enhances accountability, and promotes a culture of continuous improvement. By integrating CMMS into their operations, organizations can achieve greater reliability, compliance with regulatory standards, and ultimately, higher profitability.
Revolutionizing Maintenance: How CMMS Is Setting Global Standards
CMMS isn’t just a fancy acronym; it’s the backbone of modern maintenance practices, setting global standards by streamlining workflows, enhancing efficiency, and cutting down on downtime. Whether you’re managing a fleet of vehicles, a manufacturing plant, or even a hospital, CMMS is the game-changer that keeps everything ticking.
At its core, CMMS is all about proactive maintenance rather than reactive fixes. Instead of waiting for something to break down, CMMS allows maintenance teams to schedule preventive tasks like inspections, lubrication, and part replacements well in advance. It’s like giving your car regular check-ups to avoid a breakdown on a deserted highway.
But CMMS goes beyond just preventive maintenance; it’s a data powerhouse. Imagine having all your maintenance records, equipment details, and repair histories neatly organized and accessible at the click of a button. No more digging through piles of paperwork or endless spreadsheets. With CMMS, everything is centralized and easily searchable, making audits and compliance a breeze.
One of the biggest advantages of CMMS is its ability to optimize resources. By analyzing maintenance data, CMMS can help identify trends, predict equipment failures, and allocate resources more effectively. It’s like having a crystal ball that tells you exactly when and where you’ll need to focus your efforts, ensuring maximum uptime and minimal disruptions.
In today’s fast-paced world, downtime is not just inconvenient; it’s costly. Every minute a machine is out of commission means potential loss of production and revenue. CMMS helps mitigate these risks by keeping equipment running smoothly and reducing unplanned downtime to a bare minimum.
So, whether you’re a small business looking to streamline operations or a multinational corporation managing a global supply chain, CMMS is the key to staying ahead of the curve. It’s not just about maintenance anymore; it’s about efficiency, productivity, and ultimately, staying competitive in a rapidly evolving market.
CMMS: The Key to Unifying Maintenance Practices Worldwide
Imagine a world where every piece of machinery, every critical asset in a factory or facility, operates at peak efficiency without unexpected breakdowns. That’s the promise CMMS holds. Essentially, CMMS is a digital hub where all maintenance-related information resides. It streamlines workflows, schedules preventive maintenance tasks, and tracks asset performance in real-time. This proactive approach not only minimizes downtime but also extends the lifespan of equipment, saving substantial costs in the long run.
One of the standout features of CMMS is its ability to centralize data. Instead of relying on scattered spreadsheets or manual logs, maintenance teams can access comprehensive information from a single platform. This accessibility ensures everyone is on the same page, from technicians on the floor to managers overseeing multiple sites. It fosters collaboration and transparency, essential for efficient maintenance operations across different locations or even globally.
Moreover, CMMS isn’t just about reacting to issues; it’s about predictive prowess. By analyzing historical data and performance metrics, CMMS can forecast potential failures before they occur. This foresight empowers maintenance teams to preemptively address issues, further reducing downtime and optimizing productivity.
Think of CMMS as the conductor of a symphony orchestra, harmonizing diverse instruments (or in this case, maintenance practices) into a cohesive performance. Whether it’s a manufacturing plant in Asia, a logistics hub in Europe, or a tech facility in Silicon Valley, CMMS ensures uniformity in how maintenance tasks are managed and executed. It standardizes processes, adheres to compliance requirements, and ultimately enhances operational reliability on a global scale.
CMMS isn’t just a tool; it’s a strategic asset for organizations aiming to streamline maintenance practices worldwide. By leveraging technology to unify processes and maximize efficiency, CMMS sets the stage for smoother operations, reduced costs, and increased uptime across industries and continents alike.
From Local to Global: CMMS and the Evolution of Maintenance Standards
Imagine this: in the past, maintenance schedules were managed manually with stacks of paperwork, leading to delays, missed inspections, and inefficient resource allocation. But with CMMS, everything changes. It’s like upgrading from a manual typewriter to a sleek, high-speed laptop. CMMS digitizes and centralizes maintenance data, allowing maintenance teams to schedule tasks, track work orders, and manage inventory effortlessly.
One of the most significant benefits of CMMS is its ability to provide real-time insights and analytics. This means maintenance managers can now make data-driven decisions on the fly, ensuring equipment uptime and optimizing resources. It’s akin to having a crystal ball that predicts when and where maintenance issues might arise, allowing proactive measures to be taken before they become costly problems.
Moreover, CMMS isn’t just about fixing things when they break. It’s about preventive maintenance – identifying potential issues before they impact operations. This proactive approach not only saves money but also extends the lifespan of assets, making every dollar invested in maintenance count.
From a local perspective, small businesses can now compete on a global scale with the efficiency and reliability that CMMS provides. Imagine a local bakery ensuring their ovens are always in top condition or a neighborhood garage managing their tools and equipment with precision – CMMS empowers them to deliver consistent quality and reliability.
On a global scale, multinational corporations utilize CMMS to standardize maintenance practices across multiple sites worldwide. This consistency not only ensures compliance with regulations but also boosts operational efficiency and reduces risks associated with equipment failures.
Breaking Boundaries: CMMS Propels Maintenance Standards Across Continents
Imagine a world where every maintenance task, from routine checks to complex repairs, is seamlessly managed through a single platform accessible anywhere in the world. CMMS makes this vision a reality by centralizing maintenance data, schedules, and resources in one place. Whether you’re overseeing a factory in North America or a facility in Asia, CMMS ensures that critical maintenance tasks are executed with precision and timeliness.
At its core, CMMS empowers maintenance teams to optimize their workflows. By digitizing work orders and maintenance logs, the system eliminates the chaos of paperwork and manual tracking. Technicians receive real-time updates on tasks, reducing downtime and increasing equipment uptime. This proactive approach not only saves costs but also boosts productivity by enabling predictive maintenance strategies.
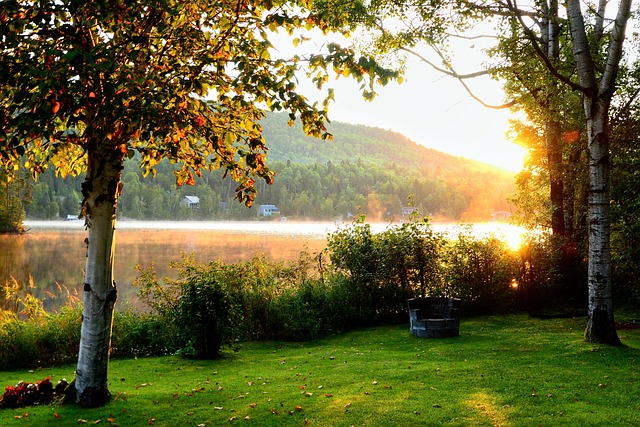
Moreover, CMMS isn’t just about operational efficiency; it’s about strategic decision-making. Through comprehensive reporting and analytics, stakeholders gain valuable insights into asset performance and maintenance trends. This data-driven approach allows businesses to allocate resources effectively, prioritize high-impact tasks, and ensure regulatory compliance across different geographical locations.
In essence, CMMS transcends geographical boundaries to standardize maintenance practices globally. It fosters collaboration among teams spread across continents, fostering a culture of continuous improvement and operational excellence. By harnessing the power of technology, businesses can uphold the highest maintenance standards, ensuring equipment reliability and customer satisfaction in a competitive marketplace.
CMMS Success Stories: Transforming Global Maintenance Practices
Imagine a large manufacturing plant struggling with downtime due to equipment failures. Every hour of halted production translates to significant losses. This was the challenge a leading automotive manufacturer faced until they implemented a robust CMMS solution. By digitizing their maintenance workflows and scheduling preventive tasks efficiently, they reduced unplanned downtime by 40% within the first year. The real-time analytics provided by CMMS helped them predict potential failures, allowing proactive maintenance that kept their production lines running smoothly.
In another compelling example, a multinational food processing company enhanced their maintenance operations using CMMS. Previously, managing maintenance across multiple facilities worldwide was a logistical nightmare. They adopted a cloud-based CMMS platform that unified their maintenance data and standardized processes globally. This centralized approach streamlined communication between teams, optimized spare parts inventory management, and improved compliance with safety regulations. As a result, they achieved a 30% reduction in maintenance costs while ensuring higher reliability of their equipment.
Small to medium-sized enterprises (SMEs) also benefit greatly from CMMS solutions. Take for instance a regional airline company struggling with maintaining its fleet of aircraft efficiently. By implementing a user-friendly CMMS tailored for aviation, they transformed their maintenance operations. The system enabled them to track the maintenance history of each aircraft, schedule inspections, and manage compliance with stringent aviation regulations seamlessly. This proactive approach not only enhanced flight safety but also reduced overall maintenance costs by 25% annually.
These success stories underscore the versatility and impact of CMMS across diverse industries. Whether it’s minimizing downtime, optimizing resources, or ensuring regulatory compliance, CMMS has proven to be a catalyst for operational excellence on a global scale. As technology continues to evolve, so too will the capabilities of CMMS, further empowering organizations to achieve new heights of efficiency and reliability in maintenance management.
Standardizing Excellence: CMMS’s Role in Global Maintenance Efficiency
CMMS acts as the backbone of maintenance operations across various industries, from manufacturing plants to healthcare facilities. At its core, CMMS software facilitates streamlined management of maintenance activities, ensuring equipment uptime, reliability, and longevity. By centralizing maintenance data and processes, CMMS empowers maintenance teams to operate proactively rather than reactively.
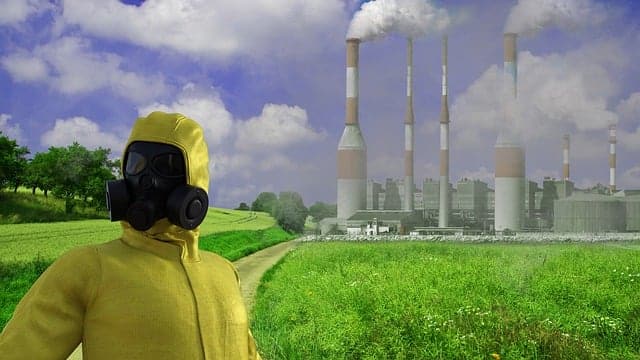
Imagine CMMS as the conductor of an orchestra, harmonizing maintenance schedules, work orders, and inventory management seamlessly. It allows maintenance managers to allocate resources effectively, prioritize tasks based on criticality, and minimize downtime. This orchestration not only boosts productivity but also reduces operational costs significantly over time.
Moreover, CMMS fosters a culture of accountability and transparency within maintenance teams. It provides real-time insights into asset performance, historical maintenance data, and predictive analytics, enabling informed decision-making. This data-driven approach empowers organizations to forecast maintenance needs accurately, optimize spare parts inventory, and adhere to regulatory compliance effortlessly.
In essence, CMMS transforms the complexities of maintenance management into a well-choreographed symphony of efficiency. It empowers organizations to standardize maintenance practices globally, ensuring consistent performance across all operational facets. By leveraging CMMS, businesses can achieve operational excellence, enhance equipment reliability, and ultimately, deliver exceptional value to their stakeholders.
Navigating Complexity: CMMS Solutions for International Maintenance Challenges
Managing maintenance across international operations can be as intricate as a carefully woven tapestry, requiring precision and foresight to ensure seamless operations. Enter CMMS (Computerized Maintenance Management System) solutions, the modern-day toolkit for businesses grappling with the complexities of global maintenance.
CMMS systems serve as the backbone of maintenance operations, offering a centralized platform to streamline tasks, track assets, and optimize workflows across diverse geographical locations. Imagine it as a digital command center, where maintenance managers can oversee everything from routine inspections to urgent repairs with ease and efficiency.
One of the standout features of CMMS solutions is their ability to standardize processes across borders. By centralizing data and procedures, these systems ensure consistency in maintenance practices, irrespective of whether your assets are in New York or Nairobi. This standardization not only enhances operational efficiency but also minimizes downtime, keeping your global workforce focused on productive tasks rather than firefighting unexpected issues.
Moreover, CMMS platforms are designed to be adaptable, accommodating varying regulatory requirements and cultural nuances without missing a beat. They offer multilingual interfaces and customizable workflows, making them versatile companions for multinational enterprises navigating diverse operational landscapes.
In the realm of international maintenance challenges, data-driven decision-making is key. CMMS systems empower stakeholders with actionable insights derived from real-time analytics. Whether it’s predicting equipment failures before they occur or optimizing spare parts inventory across continents, these insights enable proactive maintenance strategies that save both time and resources.
In essence, CMMS solutions aren’t just tools; they’re strategic assets that empower organizations to conquer the complexities of global maintenance. By harnessing the power of technology, businesses can transcend geographical boundaries and achieve operational excellence on a global scale.
Frequently Asked Questions
What are CMMS and how do they support global maintenance standards?
Learn about CMMS (Computerized Maintenance Management Systems) and how they uphold international maintenance norms efficiently.
How can CMMS software facilitate standardized maintenance practices across different locations?
Learn how CMMS software streamlines maintenance practices across multiple locations by providing centralized management of work orders, scheduling, and inventory. It ensures consistent procedures, enhances communication between teams, and improves overall operational efficiency.
How does CMMS help in tracking compliance with international maintenance regulations?
Learn how CMMS (Computerized Maintenance Management System) aids in ensuring adherence to international maintenance regulations by providing centralized oversight of maintenance activities, facilitating documentation of compliance tasks, and enabling real-time monitoring and reporting.
What are the key features to look for in a CMMS to ensure it meets global maintenance standards?
Learn about the essential features that ensure a CMMS meets global maintenance standards, focusing on criteria like scalability, mobile accessibility, integration capabilities with IoT and ERP systems, comprehensive reporting tools, and compliance with international standards such as ISO 55000.
What challenges do organizations face in implementing global maintenance standards using CMMS?
Discover the common challenges organizations encounter when implementing global maintenance standards through CMMS. Learn about the complexities of standardization across diverse locations, the integration issues with existing systems, and the training requirements for global workforce alignment.