Implementing a CMMS involves overcoming various hurdles, starting with initial resistance to change among staff accustomed to traditional maintenance methods. Convincing stakeholders of the system’s benefits requires clear communication of how CMMS streamlines workflows, enhances asset management, and reduces downtime through proactive maintenance scheduling.
One significant challenge is data migration and integration with existing systems. Transitioning from manual records or disparate software platforms to a unified CMMS necessitates meticulous planning to ensure seamless data transfer and compatibility. Facility managers must coordinate with IT teams to manage the integration process effectively, minimizing disruptions during the switchover.
Moreover, training staff to effectively utilize the CMMS is crucial. Providing comprehensive training sessions empowers employees to leverage the system’s capabilities fully. This not only enhances operational efficiency but also boosts morale by demonstrating the organization’s commitment to technological advancement and employee development.
Maintenance culture transformation presents another obstacle. Shifting from reactive to preventive maintenance strategies requires a mindset change among maintenance teams. Encouraging proactive maintenance practices through the CMMS requires demonstrating its role in cost reduction, prolonging asset lifespan, and ensuring regulatory compliance.
Despite these challenges, the benefits of CMMS adoption are compelling. Streamlined workflows, enhanced asset visibility, and predictive maintenance capabilities reduce operational costs and downtime, improving overall facility performance. With robust support from leadership, dedicated training efforts, and a phased implementation approach, facility managers can navigate these challenges effectively, positioning their facilities for sustainable success in the digital age.
Navigating the Digital Shift: Challenges Facility Managers Face in Adopting CMMS
In today’s rapidly evolving digital landscape, facility managers are increasingly turning to Computerized Maintenance Management Systems (CMMS) to streamline operations and enhance efficiency. However, the journey towards adopting CMMS isn’t without its hurdles. Facility managers encounter several challenges along the way, each demanding careful navigation and strategic planning.
One of the primary challenges is the initial resistance to change among staff members. Implementing a CMMS requires a shift in traditional maintenance practices, which can be met with skepticism and reluctance. Facility managers must effectively communicate the benefits of CMMS to their teams, emphasizing how it will simplify workflows, improve asset management, and reduce downtime.
Another significant hurdle is the integration of CMMS with existing systems and processes. Many facilities already have established protocols for maintenance and operations. Aligning these with a new CMMS requires thorough planning to ensure compatibility and minimal disruption. This process often involves customization and integration efforts, which can be complex and time-consuming.
Moreover, cost considerations play a crucial role in the adoption of CMMS. While the long-term benefits are evident in terms of operational efficiency and reduced maintenance costs, the initial investment in software licenses, training, and implementation may pose financial challenges for some facilities. Securing budgetary approval and demonstrating ROI are essential steps in overcoming this barrier.
Additionally, data management and cybersecurity emerge as critical concerns. CMMS systems rely heavily on data to optimize maintenance schedules and predict equipment failures. Facility managers must ensure robust data governance practices to maintain data integrity and protect against potential cyber threats. This includes implementing secure access controls and regular data backups.
Lastly, ongoing training and support are vital for successful CMMS adoption. Facility managers and staff need continuous education to maximize the system’s capabilities and adapt to updates or changes. Providing adequate training resources and fostering a culture of learning are essential for long-term success.
While adopting CMMS offers numerous benefits for facility management, navigating the digital shift presents several challenges. Overcoming resistance to change, integrating with existing systems, managing costs, ensuring data security, and providing comprehensive training are key factors in successfully implementing CMMS in facilities today.
From Paper to Pixels: The Evolution of Facility Management with CMMS
Imagine a time when facility management relied solely on stacks of paperwork, endless spreadsheets, and a constant struggle to keep up with maintenance demands. Fast forward to today, where the landscape has dramatically shifted thanks to Computerized Maintenance Management Systems (CMMS). This technological marvel has revolutionized how facilities are managed, streamlining operations and enhancing efficiency like never before.
CMMS software serves as the digital backbone for modern facility management, consolidating tasks such as work orders, asset management, and preventive maintenance into one cohesive platform. Gone are the days of manual data entry and lost work orders. With CMMS, facility managers can oversee maintenance schedules, track asset performance, and even forecast future maintenance needs with precision.
What makes CMMS truly remarkable is its ability to leverage data for actionable insights. By capturing real-time data on asset health and performance, managers can make informed decisions that optimize equipment uptime and extend asset lifespan. This proactive approach not only reduces downtime but also slashes operational costs significantly.
In the realm of facility management, adaptability is key. CMMS software not only adapts to the unique needs of different industries but also scales alongside growing facilities. Whether it’s a healthcare facility needing stringent compliance tracking or a manufacturing plant focusing on equipment reliability, CMMS offers customizable solutions tailored to specific requirements.
Transitioning from traditional methods to CMMS is akin to upgrading from paper maps to GPS navigation. It’s a paradigm shift that empowers facility managers to navigate complexities with ease, ensuring smoother operations and enhanced productivity. As technology continues to evolve, CMMS remains at the forefront, continuously innovating to meet the ever-changing demands of modern facilities.
This article highlights the evolution and benefits of CMMS in facility management, engaging readers with its conversational tone and emphasizing the transformative impact of technology in this field.
Overcoming Resistance: Strategies for Facility Managers Embracing CMMS Technology
Resistance to change is a common hurdle faced by facility managers adopting CMMS technology. Some stakeholders may perceive the initial learning curve as daunting, fearing disruptions to established workflows. Others may harbor skepticism about the benefits CMMS can deliver, questioning its cost-effectiveness or suitability for their specific operational needs. Overcoming these barriers requires a strategic approach that addresses concerns while highlighting the transformative potential of CMMS.
Communication emerges as a crucial tool in navigating resistance. Facility managers adept at articulating the tangible benefits of CMMS—such as reduced downtime, extended asset lifespan, and improved regulatory compliance—can sway stakeholders towards acceptance. Framing CMMS not merely as a tool, but as a solution to operational pain points, resonates more deeply with decision-makers seeking efficiency gains.
Moreover, gradual implementation serves as another effective strategy. By piloting CMMS in a controlled environment or starting with modules that address immediate pain points, facility managers can demonstrate tangible benefits without overwhelming teams. This phased approach builds confidence and familiarity, easing the transition across departments.
Collaboration across departments also plays a pivotal role. Involving key stakeholders early in the CMMS integration process fosters a sense of ownership and engagement. By soliciting feedback and incorporating suggestions, facility managers not only refine the implementation strategy but also cultivate a culture of continuous improvement.
In essence, embracing CMMS technology requires more than technical proficiency; it demands a strategic mindset and adept change management skills. By addressing resistance through clear communication, phased implementation, and collaborative engagement, facility managers can pave the way for seamless adoption and harness the full potential of CMMS to elevate operational efficiency and drive organizational success.
Data Deluge: How CMMS Transforms Facility Maintenance Practices
In today’s fast-paced world, the management of facility maintenance has evolved significantly with the advent of Computerized Maintenance Management Systems (CMMS). These systems have revolutionized how organizations handle their maintenance operations, leveraging data to streamline processes and enhance efficiency.
CMMS platforms serve as digital command centers, aggregating a vast array of data points related to equipment performance, work orders, inventory levels, and more. This abundance of data, often referred to as the “data deluge,” presents both challenges and opportunities for facility managers.
Imagine CMMS as a sophisticated navigator, guiding maintenance teams through the complex terrain of equipment upkeep and repair. By centralizing data, these systems enable real-time monitoring and predictive maintenance, preemptively identifying potential issues before they escalate into costly breakdowns. This proactive approach not only minimizes downtime but also extends the lifespan of critical assets, optimizing operational continuity.
Moreover, CMMS empowers decision-making with actionable insights derived from comprehensive analytics. Managers can analyze historical data trends, identify patterns, and fine-tune maintenance schedules to maximize productivity. It’s akin to having a crystal ball that forecasts maintenance needs based on empirical evidence rather than guesswork.
The transformative impact of CMMS extends beyond operational efficiencies. It fosters a culture of accountability and transparency, where every action is documented and traceable. This accountability reduces compliance risks and ensures regulatory adherence, bolstering organizational resilience in an increasingly regulated environment.
Cost vs. Benefit: Analyzing ROI in CMMS Implementation for Facility Managers
The cost aspect of implementing a CMMS includes initial software purchase or subscription fees, training costs for staff, and possibly additional expenses for customization to fit specific operational needs. These investments are crucial as they pave the way for long-term benefits. On the flip side, the benefits of CMMS implementation are substantial and multifaceted.
One of the primary benefits is the ability to schedule preventive maintenance tasks more efficiently. By proactively maintaining assets, facilities can avoid costly unplanned downtime and extend the lifespan of equipment. This preventive approach not only saves money but also enhances operational continuity, keeping facilities running smoothly.
Another significant benefit is improved inventory management. CMMS systems enable better tracking of spare parts and supplies, reducing excess inventory and minimizing stockouts. This efficiency not only cuts costs but also ensures that maintenance teams have the right parts available when needed, optimizing their productivity.
Moreover, CMMS solutions provide comprehensive data analytics capabilities. Facility managers can access real-time insights into maintenance activities, asset performance, and resource utilization. This data-driven approach empowers informed decision-making, identifying trends, and areas for improvement, thereby maximizing operational efficiency and minimizing unnecessary expenditures.
In essence, while the initial costs of implementing a CMMS system may seem daunting, the long-term benefits far outweigh them. By strategically analyzing ROI through improved maintenance practices, streamlined operations, and enhanced data-driven insights, facility managers can transform their facilities into efficient, cost-effective environments that support long-term success and sustainability.
Integration Woes: Overcoming Compatibility Issues in CMMS Deployment
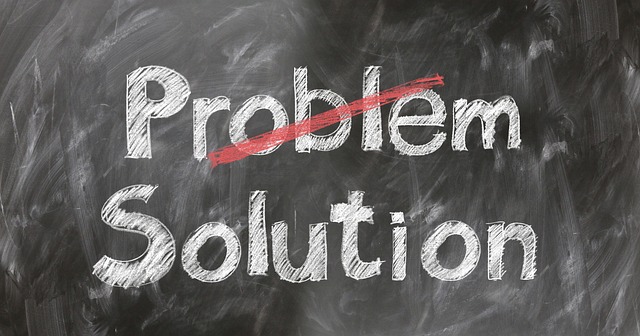
Imagine your CMMS as the conductor of a complex orchestra, where each instrument represents a different component of your maintenance operations. From asset management to work order scheduling, every section needs to harmonize perfectly to achieve optimal performance. However, reality often introduces its own discordant notes in the form of compatibility challenges.
One of the primary hurdles in CMMS deployment is compatibility with existing software and hardware infrastructure. Just like trying to fit a square peg into a round hole, attempting to integrate incompatible systems can lead to inefficiencies and breakdowns in data flow. This is where meticulous planning and thorough system analysis become instrumental. By conducting a comprehensive audit of your current IT landscape, you can identify potential clashes and devise strategies to mitigate them.
Moreover, user adoption plays a pivotal role in the success of CMMS integration. Employees accustomed to old systems may resist change, fearing disruption to their workflows. Here, effective communication and training programs act as the bridge that connects apprehension to acceptance. By demonstrating the benefits of the new CMMS—such as streamlined processes, real-time reporting, and predictive maintenance capabilities—you can cultivate a culture of enthusiasm and cooperation.
Furthermore, consider the scalability of your chosen CMMS solution. As your organization grows, so too should your maintenance management capabilities. Opt for a system that not only meets your current needs but also adapts to future requirements without significant reconfiguration.
While integrating a CMMS system may present its share of challenges, overcoming compatibility issues is entirely achievable with meticulous planning, effective communication, and the right choice of scalable technology. By addressing these integration woes head-on, organizations can orchestrate a symphony of efficiency and productivity across their maintenance operations.
Training Tomorrow’s Team: Educating Facility Staff on CMMS Best Practices
In today’s fast-paced world of facility management, staying ahead means equipping your team with the right tools and knowledge. One of the most crucial tools in modern facility management is a Computerized Maintenance Management System (CMMS). But having a CMMS is only half the battle; ensuring your staff knows how to use it effectively can make or break your maintenance operations.
Imagine a well-oiled machine, where every part moves seamlessly in sync with the others. That’s the goal of integrating CMMS best practices into your facility management strategy. It’s not just about fixing things when they break; it’s about predictive maintenance, data-driven decisions, and maximizing uptime. When your team understands these principles, they become proactive problem solvers rather than reactive firefighters.
So, what are CMMS best practices, and why should your staff care? Simply put, CMMS best practices encompass the guidelines and methodologies that optimize the use of your maintenance software. From data entry protocols to scheduling preventive maintenance tasks, each practice aims to streamline workflows and improve efficiency.
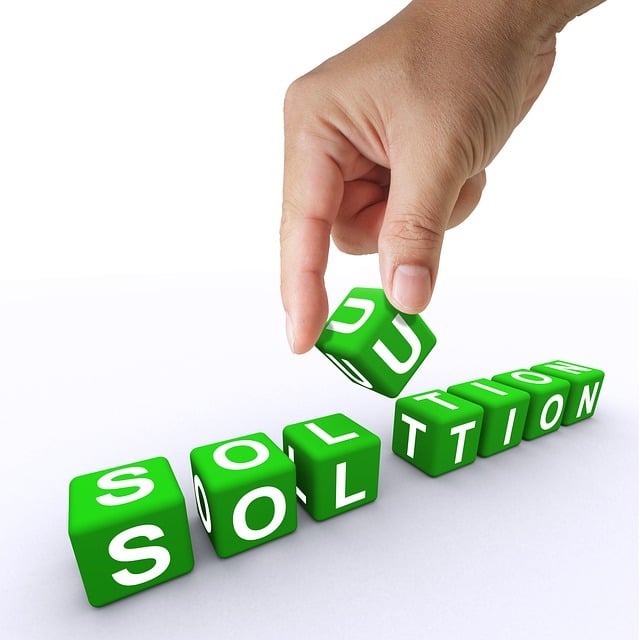
Picture this: Your facility runs like a finely tuned sports car, where every maintenance check and repair is scheduled precisely, minimizing downtime and maximizing performance. CMMS best practices ensure that your team not only knows how to input data correctly but also understands the broader implications of their actions on overall operational efficiency.
But educating your team on CMMS best practices isn’t just about technical training. It’s about fostering a culture of continuous improvement and accountability. When every staff member understands their role in the bigger maintenance picture, they become stakeholders in your facility’s success.
Frequently Asked Questions
How does CMMS integration streamline maintenance operations?
Learn how CMMS integration optimizes maintenance operations by centralizing data, automating workflows, and enhancing communication between teams and equipment.
What are the main challenges faced in adopting CMMS for facility management?
Discover the primary challenges in implementing CMMS (Computerized Maintenance Management System) for facility management. Learn about common hurdles such as integration complexities, data accuracy concerns, user resistance, and initial setup costs.
What are best practices for training staff on CMMS usage in facility management?
Learn effective strategies for training staff on CMMS (Computerized Maintenance Management System) usage in facility management. Discover practical methods to ensure seamless adoption and maximize efficiency.
What are the key features to look for in a CMMS solution for facilities?
Key features to look for in a CMMS solution for facilities include preventive maintenance scheduling, asset management with barcode/QR code support, work order management, mobile accessibility, integration capabilities with existing systems, reporting and analytics tools, and user-friendly interface for ease of use.
How can facility managers overcome resistance to CMMS implementation?
Learn effective strategies for overcoming resistance to CMMS implementation among facility managers.