In today’s competitive manufacturing landscape, ensuring top-notch quality control is not just a goal but a necessity. This is where Computerized Maintenance Management Systems (CMMS) step in as game-changers. Imagine having a tool that not only streamlines maintenance schedules but also optimizes your entire production process to ensure every product meets stringent quality standards. That’s the power of CMMS in enhancing quality control in manufacturing.
One of the standout features of CMMS is its ability to centralize maintenance operations. By integrating all maintenance tasks into a single platform, CMMS allows manufacturers to track and manage equipment performance in real-time. This proactive approach not only minimizes downtime but also identifies potential quality issues before they escalate, thus saving both time and resources.
Moreover, CMMS provides detailed insights through comprehensive reporting and analytics. Manufacturers can delve into performance metrics, identify recurring problems, and implement corrective measures swiftly. This data-driven approach not only improves overall equipment effectiveness (OEE) but also enhances product quality by addressing root causes systematically.
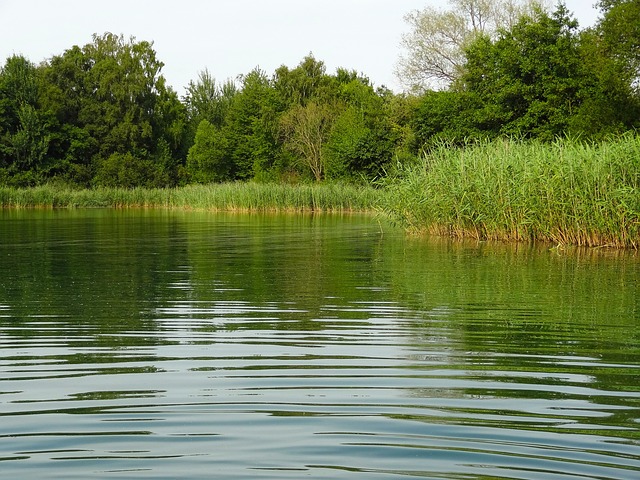
Another critical aspect where CMMS shines is in regulatory compliance. Manufacturing industries are bound by strict quality regulations and standards. CMMS helps in maintaining meticulous records, scheduling audits, and ensuring adherence to compliance requirements effortlessly. This proactive compliance management reduces risks of non-conformance and ensures that products meet regulatory expectations consistently.
Furthermore, CMMS facilitates better communication and collaboration across departments. From maintenance teams to production managers, everyone stays on the same page regarding equipment status and quality goals. This seamless coordination fosters a culture of accountability and continuous improvement, where every stakeholder plays a vital role in maintaining and enhancing product quality.
In essence, integrating CMMS into manufacturing operations isn’t just about managing maintenance tasks; it’s about transforming the entire quality control paradigm. By leveraging technology to its fullest potential, manufacturers can uphold high standards, achieve operational excellence, and ultimately deliver products that exceed customer expectations consistently. Ready to take your quality control to the next level? CMMS is the tool you’ve been looking for.
Revolutionizing Manufacturing: How CMMS is Transforming Quality Control
Imagine a scenario where every nut, bolt, and circuit board in a production line seamlessly communicates its health status in real-time. CMMS makes this vision a reality by integrating maintenance schedules, equipment data, and quality metrics into a unified digital platform. This not only streamlines workflows but also enhances predictive maintenance capabilities, preemptively addressing potential defects before they disrupt production.
At its core, CMMS empowers manufacturing facilities to uphold stringent quality standards without compromise. By centralizing maintenance data and performance analytics, manufacturers gain unparalleled insights into equipment reliability and operational efficiency. This proactive approach minimizes downtime, optimizes resource allocation, and ensures consistent product quality batch after batch.
The impact of CMMS extends beyond the factory floor. It fosters a culture of continuous improvement where every operational hiccup becomes a learning opportunity. Imagine a well-oiled machine, where maintenance teams are not just reactive but proactive detectives, uncovering inefficiencies and fine-tuning processes to perfection.
In essence, CMMS isn’t just a tool; it’s a game-changer. It transforms quality control from a reactive process to a proactive strategy, driving productivity and profitability. As manufacturing complexities evolve, CMMS stands as the cornerstone of modern quality management, ensuring that products leaving the assembly line meet and exceed customer expectations.
Streamlining Excellence: The Role of CMMS in Manufacturing Quality Assurance
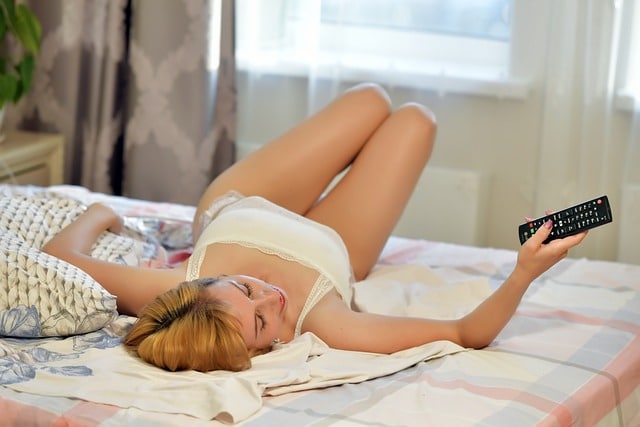
CMMS acts as the central nervous system of manufacturing operations, seamlessly integrating maintenance activities with overall business objectives. Its role in quality assurance is pivotal, offering real-time insights into equipment performance, maintenance schedules, and downtime analysis. By streamlining maintenance processes, CMMS ensures that machinery operates at peak efficiency, minimizing defects and optimizing production output.
Imagine CMMS as a vigilant conductor orchestrating a symphony of manufacturing processes. It tracks equipment health, detects potential issues before they escalate, and schedules proactive maintenance. This proactive approach prevents unexpected breakdowns, reducing costly downtime and ensuring consistent product quality.
Moreover, CMMS enhances compliance with industry regulations and standards by maintaining meticulous records of maintenance activities and inspections. It provides a comprehensive audit trail, essential for demonstrating adherence to quality protocols during regulatory inspections.
In essence, CMMS empowers manufacturers to uphold their commitment to excellence. By fostering a proactive maintenance culture and leveraging data-driven insights, companies can elevate their quality assurance practices to new heights. This not only enhances operational efficiency but also cultivates a reputation for reliability and product integrity in the marketplace.
As manufacturing evolves, CMMS remains a cornerstone of modern quality assurance strategies, continually adapting to meet the demands of an ever-changing industry landscape. Its ability to synchronize maintenance efforts with business goals underscores its indispensable role in achieving and sustaining manufacturing excellence.
From Good to Great: Boosting Manufacturing QC Through CMMS Integration
Imagine a manufacturing process where every component seamlessly fits into place like a well-orchestrated symphony. This seamless operation isn’t just a dream but a reality achievable through effective Quality Control (QC) measures powered by Computerized Maintenance Management System (CMMS) integration.
In today’s competitive landscape, ensuring top-notch quality is non-negotiable. Manufacturers are constantly seeking ways to enhance their QC processes, and CMMS integration emerges as a game-changer. CMMS not only streamlines maintenance schedules and asset management but also plays a pivotal role in bolstering QC standards.
By integrating CMMS into manufacturing QC, companies can achieve meticulous tracking and analysis of production data. This means identifying potential issues before they escalate, thus preventing costly downtime. Imagine having real-time insights into equipment performance and maintenance needs at your fingertips. CMMS empowers manufacturers with predictive maintenance capabilities, ensuring machines are always in optimal condition.
Moreover, CMMS integration fosters a proactive approach to quality management. It allows for the creation of standardized QC procedures that are consistently applied across all production lines. This uniformity not only improves product quality but also enhances customer satisfaction by delivering reliable and defect-free products.
Furthermore, CMMS facilitates compliance with regulatory standards and certifications. It ensures that every manufacturing process adheres to stringent quality guidelines, thereby mitigating risks and liabilities. This level of meticulousness not only protects the brand reputation but also instills trust among stakeholders.
Ensuring Perfection: How CMMS Software Enhances Manufacturing Quality
When it comes to manufacturing, precision and quality are paramount. Every step in the production process must be executed flawlessly to maintain high standards. This is where CMMS (Computerized Maintenance Management System) software steps in to revolutionize manufacturing quality.
Imagine CMMS software as the vigilant overseer of every aspect of your manufacturing operations. It doesn’t just keep track of equipment maintenance schedules; it ensures that every machine operates at optimal efficiency. By monitoring equipment performance in real-time, CMMS software detects potential issues before they escalate, preventing costly downtime and defects in products.
One of the most significant advantages of CMMS software is its ability to streamline workflows. It assigns tasks, schedules maintenance checks, and alerts technicians automatically. This proactive approach minimizes human error and ensures that all machinery operates within safe parameters, contributing to a smoother manufacturing process.
Moreover, CMMS software doesn’t stop at maintenance. It collects and analyzes data on equipment performance over time. This data-driven insight allows manufacturers to make informed decisions about when to replace parts, upgrade machinery, or adjust production schedules for maximum efficiency.
In essence, CMMS software acts as the backbone of manufacturing quality assurance. It integrates seamlessly with existing systems, providing a comprehensive overview of operations. Manufacturers can rest assured knowing that each product leaving their facility meets rigorous quality standards.
In a competitive market where precision and reliability are non-negotiable, CMMS software isn’t just a tool—it’s a strategic asset. By enhancing operational efficiency, reducing downtime, and ensuring consistent quality, CMMS software empowers manufacturers to deliver excellence with every product.
This article highlights the role of CMMS software in enhancing manufacturing quality, emphasizing its proactive maintenance capabilities and data-driven insights without including a concluding sentence.
Frequently Asked Questions
What is CMMS and how does it improve quality control in manufacturing?
Learn what CMMS is and how it enhances quality control in manufacturing. CMMS, or Computerized Maintenance Management System, streamlines maintenance activities, schedules inspections, and tracks equipment performance. By ensuring timely maintenance and reducing downtime, CMMS significantly improves production efficiency and product quality.
How can CMMS software streamline inspection processes in manufacturing?
Learn how CMMS software optimizes manufacturing inspection processes efficiently. Discover streamlined workflows, enhanced scheduling capabilities, and real-time data insights.
How does CMMS help in maintaining compliance and regulatory standards?
Learn how CMMS (Computerized Maintenance Management System) supports compliance and regulatory standards by automating maintenance schedules, ensuring timely inspections and audits, tracking asset data for reporting, and maintaining documentation integrity.
What are the best practices for implementing CMMS for effective quality control in manufacturing?
Learn how to implement a Computerized Maintenance Management System (CMMS) effectively for quality control in manufacturing with best practices. Discover methods to streamline maintenance schedules, integrate with quality assurance processes, and leverage data analytics for proactive maintenance and improved product quality.
What are the key benefits of integrating CMMS with quality control systems?
Discover the advantages of combining CMMS (Computerized Maintenance Management System) with quality control systems. Learn how this integration enhances maintenance efficiency, ensures compliance with quality standards, reduces downtime, and optimizes asset performance.