Have you ever wondered how technology could transform teamwork? Enter CMMS, a game-changer in team collaboration and communication. CMMS, or Computerized Maintenance Management System, isn’t just about managing maintenance tasks anymore. It’s a dynamic tool that enhances how teams work together, communicate, and achieve common goals.
Imagine a digital hub where every team member, from maintenance technicians to managers, is seamlessly connected. CMMS platforms streamline communication by centralizing information on maintenance schedules, equipment status, and work orders. This accessibility means fewer missed messages and more efficient responses, fostering a smoother workflow.
But CMMS goes beyond mere coordination—it revolutionizes collaboration. Picture a relay race where each baton pass is flawless; that’s how CMMS optimizes task delegation. Assignments are clear, responsibilities defined, and progress tracked in real-time. This clarity minimizes confusion and empowers team members to take ownership of their tasks, knowing exactly where they stand in the grand scheme of operations.
Moreover, CMMS acts as a catalyst for proactive problem-solving. By providing predictive maintenance insights and data analytics, teams can preempt issues before they escalate. It’s like having a crystal ball that anticipates maintenance needs, ensuring equipment downtime is minimized and operations remain smooth sailing.
In essence, CMMS isn’t just a tool; it’s a conductor orchestrating harmony among team members. It breaks down silos, fosters open communication, and boosts productivity. Imagine a symphony where every instrument plays in sync, creating a masterpiece—CMMS achieves this for teams by harmonizing efforts and maximizing efficiency.
Ready to elevate your team’s collaboration and communication? Embrace CMMS and witness firsthand how technology can amplify teamwork and drive success.
Streamlining Operations: How CMMS Transforms Team Collaboration
Imagine a scenario where a manufacturing plant faces frequent breakdowns due to outdated maintenance schedules and poor asset tracking. This not only halts production but also increases costs and frustrates employees. Enter CMMS—a robust solution that centralizes all maintenance processes into one streamlined platform.
With CMMS, team collaboration reaches new heights. Maintenance technicians can easily access real-time data on equipment status, upcoming tasks, and historical maintenance records. This transparency fosters better communication among team members, ensuring everyone is on the same page regarding maintenance priorities and schedules.
Moreover, CMMS automates routine tasks such as scheduling preventive maintenance and generating work orders. This automation not only saves time but also reduces human error, allowing teams to focus on more strategic initiatives that drive business growth.
In essence, CMMS transforms team collaboration by breaking down silos and enabling seamless communication and data sharing across departments. It empowers employees to work more efficiently, make informed decisions, and ultimately, contribute to the overall success of the organization.
From Silos to Synergy: CMMS’s Role in Enhancing Team Communication
Imagine a bustling factory floor where machinery hums in harmony, each unit performing its part seamlessly. CMMS acts as the conductor in this symphony, ensuring every maintenance task is scheduled, tracked, and executed without a hitch. It’s not just about fixing things when they break; it’s about predictive maintenance—anticipating issues before they occur, saving time and costs.
In practical terms, CMMS enhances team communication by centralizing information. Imagine a scenario where a technician identifies a potential issue with a critical machine. With CMMS, they can log the problem immediately, triggering alerts to relevant team members. This proactive approach prevents downtime, keeping operations smooth.
Moreover, CMMS fosters synergy by breaking down silos. Traditionally, maintenance, operations, and management might work in isolated bubbles, each with its own set of data and priorities. CMMS integrates these functions, creating a unified platform where data flows freely. It empowers teams to collaborate effortlessly, share insights, and make data-driven decisions collectively.
Think of CMMS as the glue that binds different teams together—a shared platform where everyone speaks the same language of efficiency and reliability. It’s not just a tool; it’s a catalyst for change, transforming how businesses manage their assets and communicate across departments.
CMMS revolutionizes team communication by bridging gaps, enhancing efficiency, and fostering a culture of collaboration. In a world where every minute counts, CMMS ensures that teams work together harmoniously towards common goals—maximizing uptime, minimizing disruptions, and ultimately, driving business success.
Efficiency Unleashed: Exploring CMMS’s Impact on Team Dynamics
Imagine a workplace where every task flows seamlessly, where downtime is minimized, and productivity soars. This is the promise of CMMS (Computerized Maintenance Management Systems), a game-changer in modern team dynamics. CMMS isn’t just about tracking maintenance schedules; it’s about transforming how teams collaborate and perform.
At its core, CMMS streamlines maintenance operations. It schedules preventive maintenance, tracks work orders, manages inventory, and even provides real-time data insights. But its impact goes beyond these functionalities. It reshapes team dynamics by fostering collaboration and enhancing communication.
By automating routine tasks, CMMS frees up valuable time for teams to focus on strategic initiatives. It eliminates the chaos of manual processes, reducing human error and ensuring consistency in operations. This not only boosts efficiency but also builds trust within the team.
Picture this: a maintenance technician receives a work order instantly on their mobile device, complete with all necessary details and history. They can update the status in real-time, keeping everyone in the loop. This seamless flow of information ensures faster response times and quicker resolutions, improving overall service delivery.
Moreover, CMMS provides data-driven insights that empower teams to make informed decisions. From identifying equipment trends to predicting maintenance needs, these insights optimize resource allocation and minimize downtime. It’s like having a crystal ball that helps teams stay one step ahead.
In essence, CMMS isn’t just a tool; it’s a catalyst for change in team dynamics. It promotes efficiency, collaboration, and innovation, driving towards operational excellence. As businesses strive to do more with less, CMMS emerges as a pivotal force in achieving those goals.
Embrace the future of maintenance management with CMMS and witness how it unleashes efficiency while transforming team dynamics. Because when technology aligns with teamwork, the possibilities are limitless.
Breaking Down Barriers: CMMS Tools and Improved Team Collaboration
CMMS, or Computerized Maintenance Management Systems, are more than just tools for managing maintenance tasks. They’re powerful platforms that break down barriers within teams, fostering improved collaboration across all levels of an organization. Whether you’re in manufacturing, healthcare, hospitality, or any other industry, effective teamwork is essential for productivity and innovation.
So, how exactly do CMMS tools facilitate improved team collaboration? Let’s delve into it. Imagine a maintenance team in a large facility. Traditionally, communication might involve phone calls, emails, or even sticky notes – a disjointed process prone to errors and delays. With CMMS, however, everything changes. Tasks can be assigned, updated, and tracked in real-time on a centralized platform accessible to everyone involved. This transparency not only streamlines workflow but also enhances accountability and efficiency.
Moreover, CMMS tools go beyond task management. They provide valuable insights through data analytics and reporting features. For instance, maintenance schedules can be optimized based on historical data, preventing unexpected breakdowns and downtime. When teams have access to such information, decision-making becomes more informed and proactive.
Another significant advantage of CMMS tools is their ability to integrate with other software systems used within an organization. Whether it’s ERP systems, IoT devices, or mobile apps, seamless integration ensures that data flows effortlessly across various departments. This interconnectedness eliminates silos and encourages cross-functional collaboration, where different teams can work together towards common objectives.
Beyond Maintenance: How CMMS Boosts Cross-Functional Communication
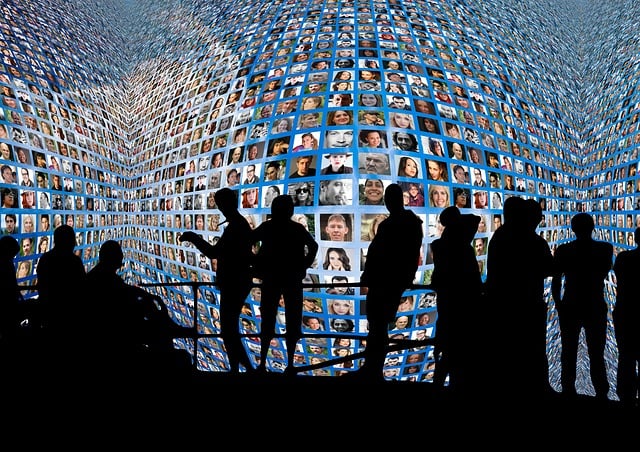
Imagine this: You’re overseeing a bustling manufacturing plant where every minute counts. Equipment breakdowns can halt production lines, costing thousands in downtime. Now, with a robust Computerized Maintenance Management System (CMMS) in place, your maintenance team isn’t just reactive; they’re proactive. They can anticipate issues before they escalate, thanks to real-time data and predictive analytics.
But CMMS isn’t just about keeping machines humming; it’s about fostering collaboration across departments. By centralizing maintenance data and workflows, CMMS bridges the gap between maintenance, operations, and management teams. No more silos—everyone’s on the same page, accessing information instantly and communicating seamlessly.
Picture a scenario: A technician flags a potential issue with a critical piece of equipment. Instead of relying on scattered emails or phone calls, CMMS triggers automated alerts to relevant stakeholders. Production managers are notified instantly, enabling them to adjust schedules or allocate resources swiftly. The result? Minimal disruption and maximum efficiency.
Moreover, CMMS acts as a universal language within your organization. Whether you’re in maintenance, procurement, or upper management, the intuitive interface and customizable dashboards provide insights tailored to your role. It’s like having a translator that converts complex technical jargon into actionable insights, fostering clearer communication and informed decision-making.
In essence, CMMS isn’t just a tool; it’s a catalyst for organizational synergy. By streamlining workflows and enhancing transparency, it empowers teams to collaborate effectively towards shared goals. So, the next time you think about maintenance management, think beyond the wrenches and oil changes. Think about how CMMS can elevate your team’s communication and propel your organization towards operational excellence. Ready to unlock the power of seamless collaboration? CMMS is your answer.
The Digital Shift: CMMS as a Catalyst for Seamless Team Collaboration
Imagine a seamless workflow where every team member is synced in real-time, like a well-orchestrated symphony. That’s exactly what CMMS aims to achieve for businesses across various industries. By integrating CMMS into daily operations, teams can bid farewell to the chaos of outdated spreadsheets and disjointed communication. Instead, they embrace a unified platform that centralizes all maintenance activities, from scheduling tasks to tracking inventory and managing work orders.
But how does CMMS truly foster seamless team collaboration? Picture this: a facility manager assigns a maintenance task through the CMMS interface. Instantly, notifications are sent to technicians equipped with mobile devices. They receive detailed instructions, including the equipment involved and the urgency level. Meanwhile, managers can oversee progress in real-time, ensuring accountability and swift resolution of issues.
The beauty lies in its simplicity. CMMS doesn’t just automate processes; it enhances communication. Team members can leave comments, update statuses, and even attach photos of completed tasks, all within the same system. This transparency eliminates guesswork and promotes a proactive approach to maintenance.
Moreover, CMMS acts as a knowledge hub. It stores historical data and performance metrics, enabling teams to make data-driven decisions. Imagine having access to a wealth of information right at your fingertips, empowering teams to anticipate issues before they escalate and optimize resources efficiently.
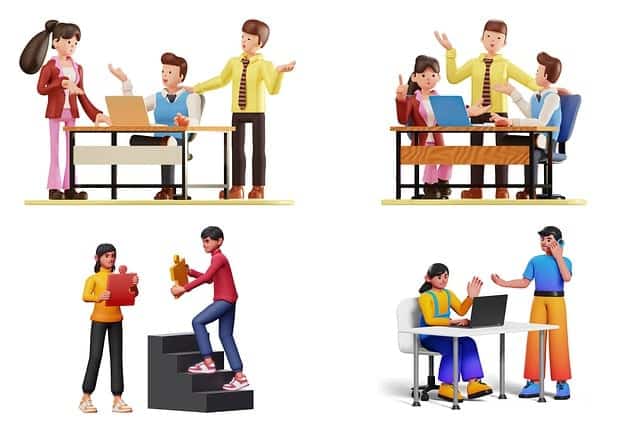
CMMS isn’t merely a tool; it’s a game-changer for team collaboration. By embracing this digital shift, businesses can foster a culture of efficiency and innovation. It’s time to elevate your team’s potential and embrace the future of maintenance management with CMMS.
Frequently Asked Questions
What features should I look for in a CMMS system to boost team productivity?
Discover the essential features to enhance team productivity with a CMMS system. Learn how functionalities like preventive maintenance scheduling, mobile accessibility, asset tracking, and reporting capabilities can streamline operations and optimize efficiency.
What are the key benefits of using CMMS for team collaboration?
Learn about the key benefits of using CMMS for team collaboration, including improved communication, streamlined task management, enhanced productivity through better resource allocation, and comprehensive data tracking for informed decision-making.
What is CMMS and how does it enhance team collaboration?
Learn about CMMS software and its role in enhancing team collaboration. Discover how CMMS streamlines maintenance operations, improves communication among team members, and increases productivity through efficient task management and asset tracking.
How can CMMS improve communication within teams?
Discover how CMMS (Computerized Maintenance Management System) enhances team communication by centralizing information, streamlining workflows, and facilitating real-time updates, fostering efficiency and collaboration.
How does CMMS streamline workflow and communication processes?
Discover how CMMS (Computerized Maintenance Management System) optimizes workflow and communication processes by centralizing maintenance activities, scheduling tasks efficiently, tracking equipment status in real-time, and facilitating seamless communication among teams. Learn how CMMS enhances productivity and reduces downtime through streamlined operations.