Ever wondered how facilities stay ahead in maintaining top-notch conditions? It’s not just about fixing things when they break anymore. Today, facility maintenance teams rely on cutting-edge technology to predict and prevent issues before they even arise. One such powerful tool in their arsenal is CMMS, or Computerized Maintenance Management System.
CMMS goes beyond mere scheduling of maintenance tasks. It collects a treasure trove of data every day – from equipment performance to work order history. This data isn’t just numbers; it’s insights waiting to be uncovered. Imagine having the power to foresee when a critical piece of machinery might need attention, long before it causes a breakdown. That’s the kind of foresight CMMS data provides.
Forecasting maintenance needs becomes almost like predicting the weather, but with actionable intelligence. Just like how meteorologists use past weather patterns to forecast storms, CMMS analyzes historical maintenance data to predict equipment failures. It’s not magic; it’s smart algorithms at work, crunching numbers and identifying patterns that humans might miss.
Think about it this way: your car’s dashboard warns you when you’re low on fuel or when tire pressure is low. CMMS does the same but for complex industrial machinery and building systems. It alerts maintenance teams about potential issues based on real-time data, ensuring that operations run smoothly without unexpected downtime.
The beauty of using CMMS for facility maintenance forecasting lies in its ability to adapt and learn. As more data is fed into the system, it becomes smarter, refining its predictions and becoming more accurate over time. It’s like teaching a child to ride a bike – with each attempt, they get better and more confident.
In essence, CMMS transforms reactive maintenance into proactive maintenance. Instead of waiting for something to go wrong, facilities can take preemptive actions to keep everything running smoothly. It’s a game-changer for industries where downtime can be costly – from manufacturing plants to hospitals and beyond.
Next time you walk into a well-maintained facility, remember that behind the scenes, CMMS data insights are quietly working their magic to ensure everything stays in perfect harmony. It’s not just about fixing problems; it’s about foreseeing them and preventing them from happening in the first place.
Unlocking Efficiency: How CMMS Data Revolutionizes Facility Maintenance Predictions
Imagine a world where facility maintenance isn’t just reactive, but proactive—where issues are identified and resolved before they even become a problem. That’s the promise of CMMS (Computerized Maintenance Management System) data analytics in revolutionizing facility maintenance predictions.
CMMS systems have traditionally been used to schedule maintenance tasks and manage work orders. However, the real game-changer lies in their ability to analyze data. By collecting and processing information on equipment performance, maintenance history, and environmental conditions, CMMS can uncover patterns and trends that human analysis might miss. This predictive capability is akin to having a crystal ball for facility managers.
Think of it this way: just like how weather forecasts use historical data to predict future weather patterns, CMMS utilizes past maintenance records and equipment performance metrics to forecast potential breakdowns or inefficiencies. This proactive approach not only minimizes downtime but also extends the lifespan of equipment, saving costs in the long run.
Moreover, CMMS doesn’t stop at predicting when equipment might fail. It also helps optimize maintenance schedules. Instead of adhering to rigid calendar-based maintenance, which can lead to unnecessary servicing or overlooking critical issues, CMMS tailors maintenance intervals based on actual equipment usage and performance data. It’s like customizing your car’s service schedule based on how and where you drive it—efficient and cost-effective.
Another advantage of CMMS data analytics is its role in resource allocation. By accurately predicting maintenance needs, facilities can better allocate manpower and resources. This means no more scrambling for spare parts at the last minute or overstaffing maintenance teams during quiet periods. Efficiency at its finest!
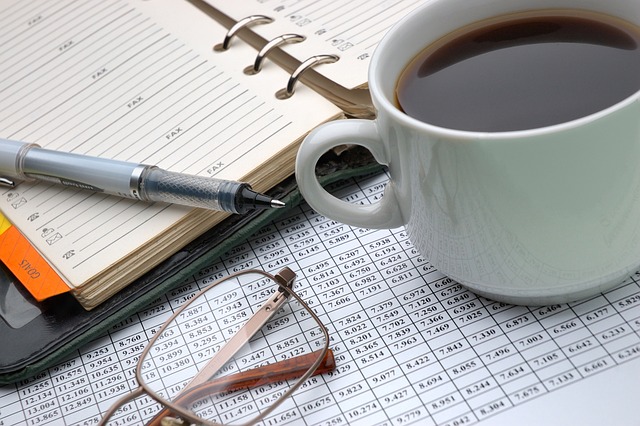
In essence, CMMS data isn’t just numbers on a screen—it’s the key to unlocking efficiency in facility management. It empowers decision-makers with actionable insights, transforms reactive maintenance into proactive strategies, and ultimately, keeps operations running smoothly. So, the next time you marvel at how smoothly your facility operates, remember: behind the scenes, CMMS data is working its magic to predict and prevent issues before they disrupt your day.
The Future of Facility Management: Harnessing CMMS Data for Predictive Maintenance
CMMS, or Computerized Maintenance Management System, is more than just a fancy acronym. It’s a game-changer in how facilities maintain their assets. Traditionally, maintenance was reactive—you waited until something broke down, then fixed it. But with CMMS, facilities can now be proactive. By analyzing historical data on equipment performance, usage patterns, and environmental factors, CMMS can predict potential failures. It’s like having a crystal ball that shows you what might go wrong, allowing you to fix issues before they disrupt operations.
Take a heating system in a large office building, for example. In the past, if it failed unexpectedly in the dead of winter, it could mean hours of discomfort for employees and costly emergency repairs. But with CMMS data analysis, facility managers can detect subtle changes in system efficiency, identify components showing signs of wear, and schedule maintenance during off-peak times. This not only prevents breakdowns but also optimizes energy use and extends the lifespan of equipment.
The benefits extend beyond just equipment reliability. Predictive maintenance saves money by reducing emergency repair costs and minimizing downtime. It also enhances safety by ensuring critical systems like fire alarms and elevators are always in peak condition. Imagine knowing months in advance that a crucial component needs replacing—CMMS makes this possible.
As technology advances, so does the potential of CMMS. Artificial intelligence and machine learning are being integrated into these systems, making predictions even more accurate. Facilities are moving from simply managing maintenance to mastering it—anticipating needs, maximizing efficiency, and ensuring smooth operations.
Data-Driven Decisions: Forecasting Facility Maintenance Needs with CMMS Insights
Imagine your facility as a well-oiled machine, each part needing timely attention to keep everything running smoothly. CMMS acts as the expert mechanic, analyzing historical maintenance data, current equipment status, and predictive analytics to forecast future maintenance needs with accuracy. It’s like having a crystal ball that not only predicts but also prepares you for what’s to come.
CMMS collects vast amounts of data—everything from equipment performance metrics to maintenance schedules and repair histories. This data is then processed to identify patterns and trends, revealing potential issues before they escalate into costly problems. It’s akin to a seasoned detective, piecing together clues to uncover the next potential maintenance challenge.
By harnessing these insights, facilities can proactively schedule maintenance tasks, allocate resources efficiently, and minimize downtime. It’s a proactive approach that saves time, cuts costs, and enhances overall operational efficiency. Picture it as navigating a ship through rough waters with a precise map, avoiding hidden reefs and steering clear of storms.
Moreover, CMMS doesn’t just stop at predicting maintenance needs; it also optimizes the entire maintenance workflow. From work order management to inventory control and compliance tracking, CMMS streamlines processes, ensuring every task is completed on schedule and within budget. Think of it as orchestrating a symphony where every instrument plays in harmony, creating a flawless performance.
Beyond Reactive: Proactive Strategies in Facility Maintenance Using CMMS Analytics
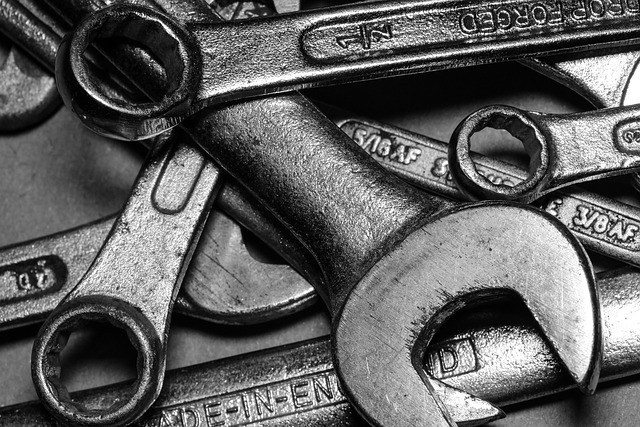
Imagine a facility where every machine, every system operates seamlessly, with minimal downtime and maximum efficiency. CMMS analytics make this vision a reality by analyzing historical data to predict maintenance needs before they escalate. By harnessing the power of data, facilities can identify trends, spot potential failures, and schedule preventive maintenance tasks accordingly.
One of the key advantages of using CMMS analytics is its ability to optimize resources. Instead of waiting for a breakdown to occur, maintenance teams can strategically plan inspections and repairs based on data-driven insights. This not only reduces unplanned downtime but also extends the lifespan of equipment, saving costs in the long run.
Moreover, CMMS analytics foster a culture of continuous improvement within facilities. By monitoring performance metrics in real-time, managers can make informed decisions to enhance operational efficiency. This proactive approach minimizes risks associated with equipment failures, ensuring smooth operations and uninterrupted productivity.
In essence, transitioning from reactive to proactive strategies in facility maintenance with CMMS analytics is akin to having a reliable crystal ball. It empowers facilities to anticipate needs, mitigate risks, and optimize resources effectively. By embracing data-driven insights, organizations can elevate their maintenance practices to new heights, ensuring they are always one step ahead of potential challenges.
Frequently Asked Questions
What is CMMS and how does it improve facility maintenance forecasting?
Learn what CMMS is and how it enhances facility maintenance forecasting. CMMS, or Computerized Maintenance Management System, is software that streamlines maintenance operations by automating tasks such as scheduling, inventory management, and work orders. It improves forecasting by providing real-time data on equipment performance, maintenance histories, and resource availability, enabling better planning and proactive maintenance strategies.
How to effectively integrate CMMS data into facility management strategies?
Learn how to optimize facility management by integrating CMMS data effectively. Discover strategies to leverage CMMS insights for streamlined maintenance, improved asset performance, and cost savings.
What are the key benefits of using CMMS for predictive maintenance in facilities?
Discover the advantages of using CMMS for predictive maintenance in facilities. Learn how it optimizes equipment reliability, reduces downtime, extends asset lifespan, and enhances maintenance scheduling efficiency.
How can CMMS data insights optimize preventive maintenance schedules?
Learn how CMMS data insights can enhance preventive maintenance schedules, optimizing efficiency and reducing downtime by predicting maintenance needs based on real-time equipment performance data.
What role does predictive analytics play in CMMS-driven facility maintenance forecasting?
Learn about the pivotal role predictive analytics plays in CMMS-driven facility maintenance forecasting. Understand how data-driven insights from predictive models anticipate equipment failures and optimize maintenance schedules, ensuring efficient operations and reduced downtime.