In the dynamic world of operations management, swift problem resolution is often the key to maintaining efficiency and meeting targets. CMMS, or Computerized Maintenance Management System, plays a pivotal role in achieving this goal by streamlining maintenance processes and enhancing overall operational efficiency.
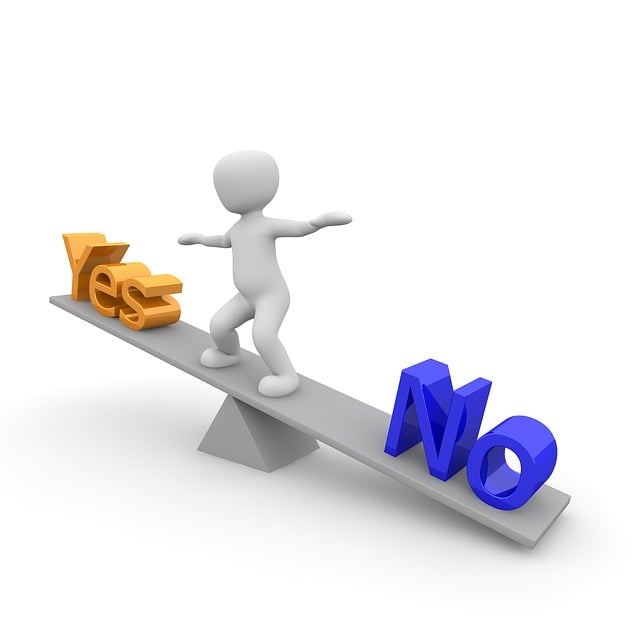
Imagine your facility running smoothly without interruptions due to equipment breakdowns or maintenance delays. CMMS makes this a reality by centralizing maintenance data and automating workflows. It acts as a digital hub where maintenance schedules, work orders, equipment history, and technician assignments converge, ensuring everyone is on the same page and tasks are executed promptly.
One of the standout features of CMMS is its ability to prioritize and categorize maintenance tasks based on urgency and impact. By leveraging real-time data and historical performance metrics, CMMS helps operations teams identify critical issues before they escalate into costly downtime. This proactive approach not only saves time but also minimizes disruptions to production schedules.
Furthermore, CMMS empowers maintenance teams with mobile accessibility, allowing technicians to receive work orders instantly on their devices. This capability eliminates the need for paperwork and phone calls, enabling technicians to focus on resolving issues swiftly on the ground. Picture a technician receiving a notification about a malfunctioning machine, accessing its maintenance history via CMMS, and promptly diagnosing the problem—this seamless process accelerates problem resolution significantly.
Analogously, CMMS can be likened to the conductor of an orchestra, harmonizing the efforts of maintenance personnel and equipment to ensure optimal performance. Just as a conductor guides musicians through a piece of music, CMMS directs maintenance activities with precision and efficiency, ensuring that operations run smoothly without missing a beat.
In essence, CMMS isn’t just a tool; it’s a catalyst for operational excellence. By facilitating faster problem resolution through streamlined processes and real-time insights, CMMS empowers organizations to stay agile, productive, and ahead of the curve in today’s competitive landscape.
Optimizing Efficiency: How CMMS Systems Revolutionize Problem Resolution in Operations
One of the key benefits of CMMS systems lies in their ability to streamline problem resolution processes. By integrating all maintenance-related data into a single platform, CMMS systems enable quick identification and resolution of issues. Maintenance teams can access historical data, equipment manuals, and maintenance logs instantly, allowing them to diagnose problems promptly and accurately.
Moreover, CMMS systems facilitate proactive maintenance strategies. Through predictive maintenance functionalities, these systems use data analytics and machine learning to forecast equipment failures before they occur. This proactive approach minimizes downtime, reduces repair costs, and extends the lifespan of critical assets.
Another significant advantage is the automation capabilities of CMMS systems. Routine tasks such as work order generation, scheduling, and inventory management can be automated, freeing up maintenance teams to focus on more complex issues. Automation also ensures consistency and compliance with maintenance protocols, enhancing overall operational efficiency.
Furthermore, CMMS systems promote accountability and transparency within organizations. Managers can track performance metrics, monitor work order statuses in real-time, and generate comprehensive reports. This transparency fosters a culture of accountability among team members and facilitates continuous improvement initiatives.
CMMS systems are indispensable tools for modern businesses looking to optimize efficiency in operations. By revolutionizing problem resolution processes through centralized data management, proactive maintenance strategies, automation, and enhanced transparency, CMMS systems empower organizations to achieve higher productivity, reduce costs, and maintain competitive advantage in today’s dynamic business environment.
Streamlining Maintenance: The Impact of CMMS on Swift Problem Solving
Imagine a well-oiled machine that never breaks down unexpectedly. That’s the dream for any business relying on machinery or equipment. But in the real world, breakdowns happen. That’s where CMMS, or Computerized Maintenance Management Systems, step in to save the day.
CMMS isn’t just another piece of software; it’s the superhero of maintenance departments. It’s like having a team of vigilant experts constantly monitoring your equipment’s health, ready to tackle any issue before it snowballs into a disaster.
So, what exactly does CMMS do? It’s all about proactive maintenance. Instead of waiting for something to go wrong, CMMS keeps track of equipment performance and schedules maintenance tasks automatically. It’s like having a personal assistant that reminds you when your car needs an oil change, except it’s for all your business machinery.
One of the biggest impacts of CMMS is on problem-solving speed. Imagine a scenario: a critical piece of equipment suddenly stops working. Without CMMS, you’re scrambling to figure out what went wrong, wasting precious time and money. With CMMS, you already have a maintenance history at your fingertips. You know when the equipment was last serviced, what parts were replaced, and any recurring issues. This means technicians can jump straight into fixing the problem, armed with all the information they need.
Another game-changer is data-driven decision-making. CMMS collects a wealth of data on equipment performance and maintenance activities. Over time, this data becomes invaluable for predicting breakdowns, optimizing maintenance schedules, and even planning for equipment upgrades. It’s like having a crystal ball that shows you the future of your machinery’s health.
Moreover, CMMS doesn’t just benefit maintenance teams. It improves overall efficiency across the board. When equipment downtime decreases, production can ramp up. Happy customers, happier bottom line – it’s a win-win situation.
In essence, CMMS isn’t just a tool; it’s a strategic asset. It empowers businesses to be proactive, efficient, and ultimately, more profitable. Whether you’re in manufacturing, healthcare, hospitality, or any other industry reliant on equipment, CMMS could be the secret weapon your business needs to stay ahead of the curve.
From Downtime to Uptime: CMMS Tools Accelerate Operational Issue Fixes
In today’s fast-paced industrial landscape, minimizing downtime is crucial for maintaining operational efficiency and profitability. Enter CMMS (Computerized Maintenance Management System) tools, the unsung heroes behind streamlined maintenance operations. These robust software solutions are designed to track, manage, and optimize maintenance activities, ensuring that equipment downtime is minimized and productivity remains at peak levels.
CMMS tools act as a digital nerve center for maintenance teams, allowing them to schedule preventive maintenance tasks proactively. By staying ahead of potential issues, organizations can avoid unexpected breakdowns that can halt production and incur costly repairs. Imagine these tools as virtual detectives, constantly monitoring equipment health indicators and alerting maintenance crews at the earliest signs of trouble.
What makes CMMS tools truly transformative is their ability to centralize data and insights. Instead of relying on disparate spreadsheets or manual logs, maintenance teams can access a unified platform where all maintenance activities are logged in real-time. This centralized approach not only improves communication and collaboration but also provides actionable insights into equipment performance trends.
Furthermore, CMMS tools enable organizations to optimize inventory management by tracking spare parts and supplies more efficiently. This ensures that maintenance crews have the right resources on hand when needed, reducing downtime associated with waiting for critical parts to arrive.
In essence, CMMS tools are like the conductor of an orchestra, ensuring that each instrument (or piece of equipment) plays harmoniously without missing a beat. They empower maintenance teams to transition from reactive firefighting to proactive maintenance strategies, ultimately driving operational uptime and enhancing overall organizational efficiency.
Breaking Down Barriers: CMMS Software’s Role in Rapid Problem Resolution
At its core, CMMS is designed to break down barriers that often hinder operational smoothness. It acts as a centralized hub where maintenance teams can track, manage, and resolve issues promptly. By digitizing maintenance workflows, CMMS eliminates the traditional pen-and-paper approach, offering real-time insights into equipment performance and maintenance history. This real-time capability allows maintenance staff to pinpoint potential problems before they escalate, thereby preventing costly breakdowns and interruptions.
Moreover, CMMS software doesn’t just stop at maintenance. It integrates seamlessly with other enterprise systems, such as ERP (Enterprise Resource Planning) and IoT (Internet of Things) platforms, to provide a comprehensive view of asset health and performance. This integration empowers decision-makers with data-driven insights, enabling proactive maintenance strategies that enhance overall equipment effectiveness (OEE) and operational uptime.
In essence, CMMS software acts as a proactive guardian, anticipating maintenance needs and swiftly resolving issues to keep operations running smoothly. Its ability to automate routine tasks, schedule preventive maintenance, and manage work orders efficiently makes it indispensable in industries ranging from manufacturing to healthcare. By breaking down barriers to efficient maintenance, CMMS software not only improves operational efficiency but also boosts organizational productivity and customer satisfaction.
In today’s fast-paced industrial landscape, where every minute of downtime counts, CMMS software stands as the ultimate tool for maintaining operational continuity and driving business success.
Speeding Up Solutions: CMMS Enhances Operational Troubleshooting
CMMS is like a superhero for businesses, offering a streamlined approach to maintenance operations. It’s not just about fixing things when they break; it’s about preventing breakdowns in the first place. By centralizing maintenance data and automating processes, CMMS ensures that your equipment stays in top shape, reducing downtime and increasing productivity.
One of the standout features of CMMS is its ability to enhance operational troubleshooting. Picture a scenario where a machine malfunctions unexpectedly. With CMMS, technicians can quickly access its maintenance history, pinpoint the issue, and take action immediately. This proactive approach minimizes downtime and keeps operations flowing smoothly.
Moreover, CMMS empowers your team with real-time insights. It provides detailed analytics and reports on equipment performance, maintenance costs, and inventory levels. This data-driven approach allows businesses to make informed decisions, optimize resources, and allocate budgets more effectively.
Implementing a CMMS system is like having a personal assistant dedicated to your maintenance needs. It schedules preventive maintenance tasks, sends alerts for upcoming inspections, and tracks work orders from start to finish. This level of organization not only boosts efficiency but also extends the lifespan of your equipment, saving you money in the long run.
In today’s fast-paced business environment, every minute counts. CMMS ensures that you’re always one step ahead by streamlining workflows and eliminating bottlenecks. Whether you’re in manufacturing, healthcare, or hospitality, integrating CMMS into your operations is a game-changer that enhances operational troubleshooting and accelerates your path to success.
Efficiency Unleashed: CMMS Solutions Transforming Problem Resolution
CMMS solutions are like the orchestra conductor of maintenance operations, orchestrating a symphony of tasks to ensure equipment runs smoothly and downtime is minimized. By integrating advanced software capabilities with real-time data analytics, CMMS empowers maintenance teams to proactively tackle issues before they escalate into costly disruptions.
Think of CMMS as your digital detective, constantly monitoring equipment health, tracking historical data, and predicting potential failures. This proactive approach not only saves time but also prevents unexpected breakdowns that could halt production.
One of the most significant benefits of CMMS solutions is their ability to centralize information. No more digging through stacks of paperwork or endless spreadsheets to find that one maintenance log. With CMMS, everything is at your fingertips, organized and accessible. This centralized approach not only improves decision-making but also enhances collaboration across teams.
Moreover, CMMS solutions are designed with user-friendliness in mind. They’re intuitive, easy to navigate, and don’t require a PhD in computer science to operate. Maintenance technicians can focus on what they do best—fixing problems—rather than wrestling with complex software.
Imagine CMMS as your Swiss Army knife for maintenance—versatile, reliable, and always ready to tackle any challenge that comes your way. Whether it’s scheduling preventive maintenance, managing work orders, or analyzing performance metrics, CMMS solutions are the backbone of operational efficiency.
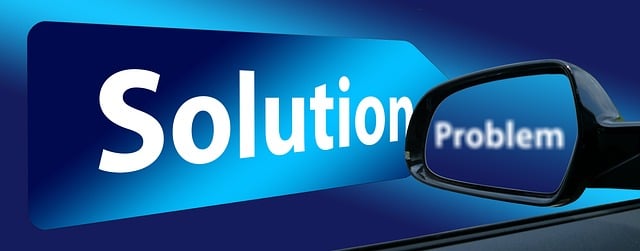
CMMS solutions aren’t just tools; they’re transformers of how businesses approach maintenance and problem resolution. By leveraging technology to its fullest potential, organizations can achieve unparalleled efficiency, minimize downtime, and stay ahead in today’s competitive landscape. So, if you’re looking to unleash the full potential of your maintenance operations, CMMS solutions are your ticket to streamlined success.
Frequently Asked Questions
How does CMMS enhance operational efficiency by resolving problems faster?
Learn how CMMS (Computerized Maintenance Management System) boosts operational efficiency by enabling faster resolution of problems. By streamlining maintenance workflows and facilitating quicker identification and repair of issues, CMMS minimizes downtime, increases equipment reliability, and enhances overall productivity.
What is CMMS and how does it expedite problem resolution?
CMMS (Computerized Maintenance Management System) is a software solution used to streamline maintenance operations. It expedites problem resolution by centralizing maintenance data, scheduling tasks efficiently, and providing quick access to historical maintenance records. This organized approach reduces downtime, enhances asset reliability, and improves overall operational efficiency.
How can CMMS software streamline troubleshooting processes?
Learn how CMMS software enhances troubleshooting efficiency by centralizing maintenance data, automating work orders, and enabling quick access to equipment histories.
What are the key features of CMMS that accelerate problem-solving in operations?
Learn about the essential features of CMMS that enhance operational efficiency and problem-solving. Understand how CMMS streamlines maintenance scheduling, asset tracking, and data analytics to proactively manage issues and minimize downtime.
What role does CMMS play in reducing downtime through faster issue resolution?
Learn how CMMS (Computerized Maintenance Management System) helps minimize downtime by speeding up issue resolution through efficient tracking, scheduling, and prioritization of maintenance tasks.