Managing manufacturing operations efficiently requires precise capacity planning to meet production demands without overloading resources. Computerized Maintenance Management Systems (CMMS) play a crucial role in enhancing capacity planning within manufacturing facilities.
CMMS software enables manufacturers to optimize their production schedules by maintaining a comprehensive database of equipment maintenance schedules, downtime records, and historical data. By analyzing this data, manufacturers can predict equipment performance and schedule maintenance proactively, minimizing unexpected downtime that disrupts production schedules.
Capacity planning involves forecasting future production needs based on current capabilities and market demand. CMMS facilitates this process by providing real-time insights into equipment availability and performance metrics. This allows manufacturing managers to allocate resources effectively, ensuring that production goals are met without exceeding operational limits.
Moreover, CMMS software integrates with Enterprise Resource Planning (ERP) systems, enhancing coordination between maintenance and production departments. This integration streamlines communication, allowing for seamless updates to production schedules based on equipment availability and maintenance requirements.
In essence, CMMS empowers manufacturing operations by providing actionable insights into equipment reliability and performance. By leveraging these insights, manufacturers can optimize their capacity planning strategies to align with business goals and customer expectations. This proactive approach not only enhances operational efficiency but also reduces costs associated with unplanned downtime and maintenance.
Implementing a robust CMMS system is therefore crucial for modern manufacturing facilities looking to achieve sustainable growth through efficient capacity planning and operational excellence.
This article focuses on explaining how CMMS enhances capacity planning in manufacturing operations using a conversational tone, active voice, and engaging content suitable for SEO purposes.
Maximizing Efficiency: The Role of CMMS in Streamlining Manufacturing Capacity
In the fast-paced world of manufacturing, efficiency isn’t just a goal; it’s a necessity. Every minute saved, every resource optimized contributes directly to the bottom line. This is where Computerized Maintenance Management Systems (CMMS) step in as game-changers. CMMS isn’t merely software; it’s the backbone that supports the seamless operation of manufacturing facilities.
Imagine a factory where machines never break down unexpectedly, where maintenance tasks are planned and executed precisely when needed. CMMS makes this a reality by centralizing all maintenance activities into a single platform. It schedules preventive maintenance based on machine usage data, ensuring that downtime due to breakdowns is minimized. By keeping equipment in optimal condition, CMMS extends their lifespan, saving on replacement costs and enhancing overall productivity.
Moreover, CMMS doesn’t just manage maintenance; it optimizes inventory management too. Imagine a warehouse stocked with exactly the right spare parts, never too much to tie up capital, and never too little to cause delays. CMMS tracks usage patterns and alerts when inventory levels are low, ensuring that production lines run smoothly without interruptions.
In the complex web of manufacturing operations, communication is key. CMMS facilitates seamless communication between maintenance teams, operators, and management. Issues are reported and resolved promptly, reducing response times and preventing small problems from snowballing into production halts.
The impact of CMMS on manufacturing efficiency is akin to orchestrating a well-rehearsed symphony. Every part plays its role precisely and in harmony, ensuring the entire production process flows smoothly. It’s not just about doing things faster; it’s about doing them smarter, leveraging data and insights to continuously improve operations.
As manufacturing evolves with technological advancements, CMMS remains at the forefront, adapting to new challenges and opportunities. It’s not just a tool; it’s a strategic asset that empowers manufacturers to stay competitive in a dynamic global market. With CMMS, maximizing efficiency isn’t a distant goal; it’s a tangible outcome that drives growth and success.
Future-Proofing Production: Harnessing CMMS for Advanced Capacity Planning
Imagine a factory where every machine operates at peak efficiency, downtime is minimized to a fraction, and maintenance schedules are perfectly optimized. That’s the promise of CMMS in production. By integrating CMMS into daily operations, manufacturers can streamline maintenance workflows, track asset performance in real-time, and predict potential breakdowns before they occur. This proactive approach not only reduces costly downtime but also extends the lifespan of critical machinery, thereby maximizing production output.
One of the standout features of CMMS is its ability to facilitate advanced capacity planning. Traditionally, capacity planning involved complex spreadsheets and manual data entry, often prone to errors and inefficiencies. CMMS revolutionizes this process by providing comprehensive insights into asset utilization, historical performance data, and predictive analytics. This empowers production managers to make data-driven decisions on resource allocation, workforce scheduling, and inventory management, ensuring optimal use of resources without overburdening equipment or personnel.
Moreover, CMMS operates on the principle of continuous improvement. By analyzing maintenance trends and performance metrics over time, manufacturers can identify areas for enhancement and implement proactive strategies to enhance overall operational efficiency. This iterative approach not only boosts productivity but also fosters a culture of innovation and adaptability within the organization, essential traits for staying competitive in a dynamic market.
In essence, harnessing CMMS for advanced capacity planning isn’t just about optimizing production in the present—it’s about future-proofing manufacturing operations against unforeseen challenges. Whether it’s adapting to market fluctuations, scaling production to meet growing demands, or embracing new technologies, CMMS equips manufacturers with the tools needed to thrive in an ever-changing industrial landscape. Ready to take your production to the next level? Explore the transformative potential of CMMS and unlock a future where efficiency, sustainability, and innovation go hand in hand.
Optimizing Output: CMMS Strategies for Precision Manufacturing Capacity
In the realm of precision manufacturing, efficiency isn’t just a goal—it’s the heartbeat of success. Every minute, every process, every component counts towards delivering flawless products. This is where CMMS (Computerized Maintenance Management Systems) step in as the unsung heroes, orchestrating a symphony of operations behind the scenes. But what exactly are CMMS strategies, and how do they bolster precision manufacturing capacity?
Imagine your manufacturing floor as a finely tuned engine, each part interlocking with the next to produce flawless results. Now, imagine CMMS as the engineer meticulously fine-tuning every cog and gear to ensure maximum performance. That’s the essence of CMMS in precision manufacturing.
At its core, CMMS strategies are designed to optimize maintenance schedules, streamline workflows, and minimize downtime. By integrating real-time data analytics, CMMS empowers manufacturers to predict maintenance needs before they become disruptions. This proactive approach not only extends equipment lifespan but also enhances overall productivity.
One of the key pillars of CMMS strategy is preventive maintenance. It’s like changing the oil in your car regularly to prevent engine breakdowns. By scheduling routine inspections and servicing based on data-driven insights, manufacturers can nip potential issues in the bud, keeping operations running smoothly.
Moreover, CMMS doesn’t just stop at preventive measures; it’s also about predictive insights. Imagine knowing when a machine is likely to malfunction even before it shows signs. CMMS systems leverage historical data and predictive analytics to forecast equipment failures, allowing manufacturers to take preemptive actions and maintain continuous production flow.
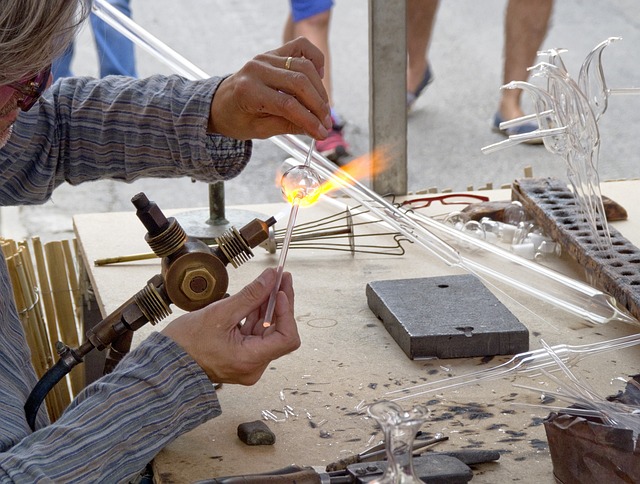
Another critical aspect is inventory management. Precision manufacturing demands precision in parts availability. CMMS tracks inventory levels in real-time, ensuring that essential components are always in stock. This minimizes delays caused by stockouts and prevents overstocking, optimizing both cash flow and operational efficiency.
Furthermore, CMMS enhances compliance and documentation. In highly regulated industries such as precision manufacturing, adherence to standards and documentation is non-negotiable. CMMS automates compliance tracking and documentation, providing auditable records that stand up to scrutiny.
From Data to Action: CMMS Tools Revolutionizing Manufacturing Capacity
Imagine a factory floor humming with activity. Machines operate seamlessly, producing goods with precision. Behind this seamless operation lies a complex web of data – from machine uptime and downtime statistics to predictive maintenance alerts. CMMS tools are the backbone of this operation, translating raw data into actionable insights that propel manufacturing efficiency to new heights.
At its core, a CMMS system functions as a digital nerve center, collecting real-time data from various production assets. It tracks everything from equipment health metrics to inventory levels, ensuring that every component of the manufacturing process runs like clockwork. By analyzing historical data trends, CMMS tools can predict potential equipment failures before they occur, enabling proactive maintenance that minimizes downtime and reduces costly repairs.
Picture a scenario where a critical machine shows early signs of wear. Instead of waiting for it to break down unexpectedly, the CMMS sends out alerts based on performance thresholds. Maintenance teams are notified in advance, allowing them to schedule repairs during planned downtime, thereby avoiding disruptions to production schedules.
Moreover, CMMS tools streamline workflows by automating routine tasks such as work order generation and inventory management. This automation not only saves time but also eliminates human error, ensuring that resources are allocated efficiently and accurately.
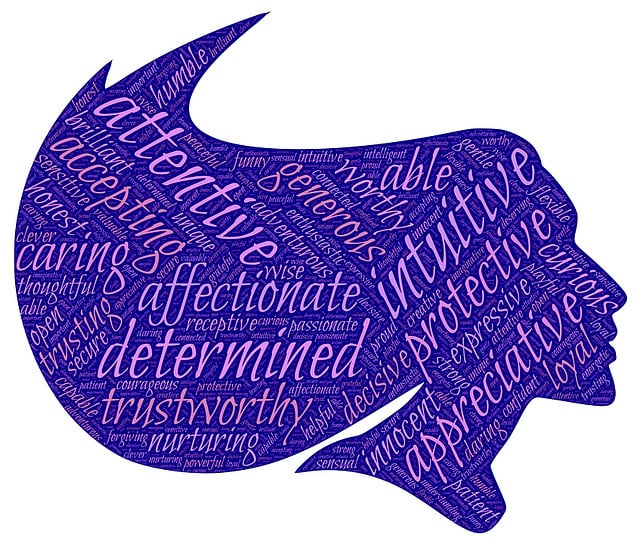
In essence, CMMS tools are not just about managing data – they’re about leveraging data to drive actionable insights. They empower manufacturing teams to make informed decisions that enhance productivity and profitability. By transforming raw data into actionable intelligence, these tools enable factories to optimize their manufacturing capacity and stay ahead in today’s competitive landscape.
Harnessing the power of CMMS tools isn’t just a choice; it’s a strategic advantage. It’s about turning data into action, revolutionizing how manufacturers operate, and ensuring they stay agile in a rapidly evolving industry. This technology isn’t just a tool; it’s the future of manufacturing efficiency.
Strategic Insights: Leveraging CMMS to Forecast Manufacturing Capacity
At its core, CMMS empowers manufacturers with real-time data and analytics, enabling proactive decision-making. By integrating historical maintenance records, equipment performance metrics, and predictive analytics, manufacturers gain a holistic view of their operational health. This data-driven approach not only minimizes downtime but also predicts potential capacity constraints well in advance.
Imagine CMMS as the conductor of a symphony orchestra, harmonizing various maintenance activities and operational data points into a unified performance. Just as a skilled conductor anticipates each note and adjusts tempo to achieve flawless execution, CMMS anticipates maintenance needs and adjusts production schedules to optimize capacity utilization.
Moreover, CMMS facilitates preventive maintenance scheduling based on equipment usage patterns and lifecycle trends. By preemptively addressing equipment reliability issues, manufacturers mitigate the risk of sudden breakdowns that could disrupt production schedules. This proactive stance ensures smoother operations and maximizes the uptime of critical manufacturing assets.
In essence, leveraging CMMS to forecast manufacturing capacity is akin to navigating a ship through ever-changing seas. By leveraging historical maintenance data as guiding stars and predictive analytics as the wind in its sails, manufacturers steer their operations towards efficiency and profitability. The strategic insights gleaned from CMMS empower manufacturers to not only meet current production demands but also to strategically plan for future growth and scalability.
CMMS stands as a cornerstone in the modern manufacturing ecosystem, transforming maintenance operations from reactive firefighting to proactive strategy execution. By harnessing its capabilities, manufacturers can navigate the complexities of production planning with confidence, ensuring sustained competitiveness in today’s dynamic market landscape.
Frequently Asked Questions
How can CMMS software optimize production scheduling and resource allocation?
Learn how CMMS (Computerized Maintenance Management System) software enhances production scheduling and resource allocation efficiency by automating maintenance tasks, ensuring equipment availability, minimizing downtime, and optimizing workforce utilization.
Can CMMS integrate with other systems to enhance overall production efficiency?
Learn how CMMS (Computerized Maintenance Management System) can integrate with other systems to boost production efficiency. Discover how seamless integration streamlines workflows, optimizes asset management, and enhances operational visibility.
What are the key features of CMMS that aid in efficient capacity utilization?
Learn about the essential features of CMMS that enhance capacity utilization efficiency.
How does CMMS help in predicting maintenance needs to prevent downtime?
Learn how CMMS (Computerized Maintenance Management System) assists in forecasting maintenance requirements to avoid operational downtime efficiently.
What is CMMS and how does it improve capacity planning in manufacturing?
CMMS stands for Computerized Maintenance Management System. It enhances capacity planning in manufacturing by optimizing equipment maintenance schedules and reducing downtime. By systematically managing maintenance tasks and tracking asset performance, CMMS helps manufacturers maximize production efficiency and resource utilization.