Imagine this: your facility is buzzing with activity, from equipment running at full tilt to technicians scurrying to perform maintenance. Amidst this whirlwind, CMMS stands tall as your trusty assistant. It’s like having a personal organizer that keeps track of every asset, ensuring they’re in peak condition and ready to perform.
Asset tracking is where CMMS truly shines. Picture it as a virtual map that pinpoints every piece of equipment in your facility. Need to know when a particular machine was last serviced? CMMS has you covered. Want to schedule preventive maintenance to avoid costly breakdowns? CMMS does that too, sending timely reminders like a friendly nudge from a conscientious colleague.
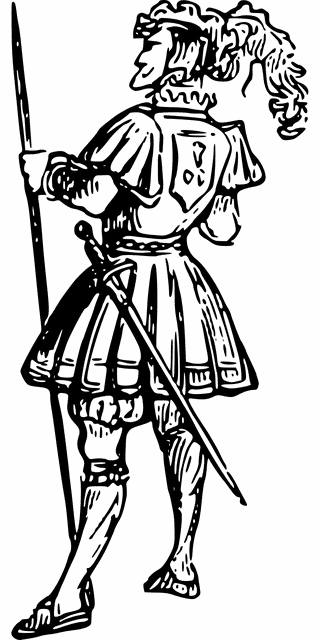
But it doesn’t stop there. CMMS goes beyond basic tracking; it’s your proactive partner in asset management. Think of it as a superhero cape draped over your facility operations. It predicts maintenance needs, analyzes performance trends, and optimizes workflows, all while you focus on steering your facility towards peak efficiency.
Now, imagine running your facility without CMMS. It’s like navigating through a storm without a compass. You’d be left in the dark, reacting to problems rather than preventing them. With CMMS, you’re equipped with real-time data and insights, making informed decisions that keep your facility humming like a well-oiled machine.
Streamlining Efficiency: How CMMS Transforms Asset Tracking for Facility Managers
Managing a facility comes with its challenges, from equipment maintenance to inventory tracking. Facility managers are constantly seeking ways to streamline operations and optimize efficiency. Enter CMMS, or Computerized Maintenance Management Systems, which revolutionize asset tracking in facilities of all sizes.
CMMS software is designed to centralize and automate the management of assets, maintenance schedules, and work orders. Imagine it as a digital assistant for facility managers, keeping a watchful eye on every piece of equipment and ensuring everything runs smoothly. This technology allows managers to monitor the health of assets in real-time, schedule preventive maintenance tasks, and track historical data effortlessly.
One of the key benefits of CMMS is its ability to extend the lifespan of assets. By implementing regular maintenance schedules based on actual usage data, facilities can reduce unexpected breakdowns and prolong the operational life of costly equipment. This proactive approach not only saves money on repairs but also enhances overall productivity by minimizing downtime.
Moreover, CMMS enhances accountability within the maintenance team. Each task and maintenance activity can be logged into the system, providing a transparent record of who did what and when. This transparency promotes a culture of responsibility and ensures that nothing falls through the cracks.
For facility managers, time is of the essence. CMMS simplifies the process of generating reports and analyzing data, offering actionable insights at the click of a button. Whether it’s tracking maintenance costs, evaluating equipment performance, or forecasting future needs, CMMS empowers managers with the information they need to make informed decisions swiftly.
CMMS isn’t just a tool; it’s a game-changer for facility management. By streamlining asset tracking and maintenance operations, CMMS enables managers to optimize efficiency, reduce costs, and improve overall facility performance. Embracing this technology isn’t just about keeping up with trends; it’s about staying ahead in an increasingly competitive landscape.
Mastering Maintenance: The Role of CMMS in Facility Asset Management
Imagine running a facility smoothly, with equipment humming along perfectly, and operations flowing like a well-conducted orchestra. This seamless operation doesn’t just happen by chance; it’s orchestrated by the careful management of assets using a powerful tool known as CMMS, or Computerized Maintenance Management System.
CMMS is the backbone of efficient facility asset management. It’s like having a digital assistant dedicated to ensuring that every piece of equipment in your facility is performing at its best, minimizing downtime and maximizing productivity. Think of it as your personal trainer for equipment health!
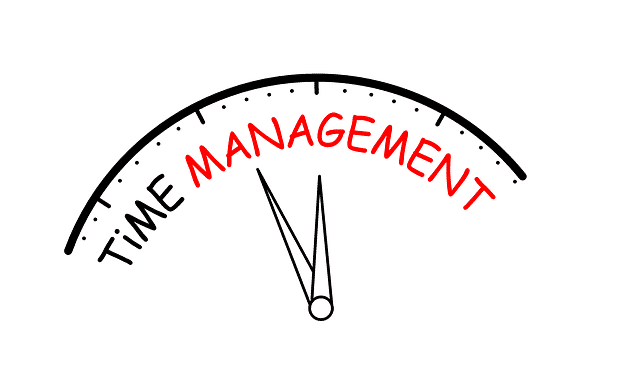
So, what exactly does CMMS do? Simply put, it helps you plan, track, and optimize maintenance activities. From scheduling routine inspections to logging repair histories, CMMS keeps a detailed record of each asset’s lifecycle. This proactive approach not only extends the lifespan of equipment but also prevents costly breakdowns that can disrupt operations.
One of the standout features of CMMS is its ability to generate insightful reports. These reports provide managers with valuable data on maintenance costs, asset performance trends, and compliance metrics. Armed with this information, decision-makers can make informed choices that drive efficiency and cut unnecessary expenses.
In the fast-paced world of facility management, time is money. CMMS saves both. By automating routine tasks like work order generation and inventory management, it frees up valuable time for maintenance teams to focus on more strategic initiatives. It’s like having a superhero sidekick that handles the mundane, leaving you to tackle the extraordinary.
Moreover, CMMS isn’t just for large corporations with sprawling facilities. Businesses of all sizes can benefit from its streamlined approach to asset management. Whether you’re overseeing a bustling factory floor or a small office space, CMMS adapts to your needs, scaling with your business as it grows.
In essence, mastering maintenance with CMMS isn’t just about keeping things running; it’s about optimizing every facet of your facility’s operations. By harnessing the power of technology to monitor, manage, and maintain assets, businesses can achieve peak performance and stay ahead of the curve in an ever-evolving landscape.
This article aims to provide a clear and engaging overview of CMMS and its role in facility asset management, using a conversational tone and relatable analogies to keep the reader interested and informed.
From Data to Action: Leveraging CMMS for Effective Facility Asset Tracking
CMMS platforms serve as a centralized hub where all asset-related data converges, offering real-time visibility into asset performance, maintenance history, and lifecycle management. By capturing detailed information on each asset, such as maintenance schedules, repair logs, and operational costs, facilities gain a comprehensive understanding of their asset landscape. This data empowers decision-makers to prioritize maintenance tasks based on criticality and asset condition, minimizing downtime and extending asset lifespan.
Imagine a facility manager who can instantly access a dashboard displaying the health status of every piece of equipment, from HVAC systems to production machinery, at a glance. CMMS not only provides this level of visibility but also forecasts potential issues before they escalate, allowing proactive interventions that prevent costly breakdowns. This proactive approach transforms reactive maintenance practices into predictive strategies, optimizing resource allocation and reducing operational risks.
Moreover, CMMS facilitates compliance with regulatory standards and industry best practices by ensuring all maintenance activities are logged and documented. This capability not only enhances safety and reliability but also fosters a culture of accountability and transparency within the organization. By maintaining accurate records and automating routine tasks, CMMS frees up valuable time for maintenance teams to focus on strategic initiatives that drive business growth.
In essence, leveraging CMMS for effective facility asset tracking goes beyond mere data management; it empowers organizations to convert insights into actionable strategies. By harnessing the power of data, facilities can achieve operational excellence, enhance productivity, and ultimately, deliver superior service to their customers. As technology continues to evolve, CMMS remains a cornerstone of modern facility management, ensuring facilities stay agile, efficient, and ready to meet the challenges of tomorrow.
Optimizing Operations: CMMS Tools for Seamless Facility Management
Imagine CMMS tools as the conductor of a well-orchestrated symphony, where every instrument represents a different aspect of facility management. From ensuring equipment reliability to optimizing maintenance schedules, these tools keep everything in harmony. They provide real-time data on equipment health, allowing maintenance teams to preemptively address issues before they escalate, thus minimizing downtime and maximizing operational uptime.
Moreover, CMMS tools facilitate compliance with regulatory standards and industry best practices by automating record-keeping and audit trails. This capability not only simplifies the management of compliance requirements but also reduces the risk of penalties and operational disruptions.
In essence, adopting CMMS tools is akin to installing a GPS system in your car – it guides you with precise information, helping you navigate efficiently and reach your destination smoothly. Similarly, these tools equip facility managers with actionable insights, empowering them to make informed decisions that optimize resources and improve overall performance.
By leveraging CMMS tools, facilities can transition from reactive to proactive maintenance strategies, thereby extending the lifespan of assets and reducing maintenance costs over time. This proactive approach transforms maintenance from a cost center into a strategic asset that drives operational excellence and business success.
Frequently Asked Questions
What features should facility managers look for in a CMMS system for effective asset tracking?
Learn about the essential features facility managers should consider when selecting a CMMS system to optimize asset tracking efficiently.
How does CMMS improve equipment reliability and reduce downtime?
Learn how CMMS enhances equipment reliability and minimizes downtime with streamlined maintenance schedules, proactive fault detection, and efficient resource allocation.
What is CMMS and how does it help in asset tracking for facility management?
CMMS, or Computerized Maintenance Management System, is a software solution designed to streamline maintenance operations and asset tracking in facility management. It helps organizations efficiently manage assets, track maintenance schedules, and optimize resource allocation. CMMS enhances operational efficiency by ensuring timely maintenance, reducing downtime, and prolonging asset lifespan through systematic tracking and management.
How can CMMS software streamline maintenance tasks for facility managers?
Learn how CMMS software optimizes maintenance tasks for facility managers, enhancing efficiency through streamlined scheduling, inventory management, and maintenance history tracking.
What are the key benefits of using CMMS for asset management in facilities?
Learn about the essential benefits of using CMMS (Computerized Maintenance Management System) for managing assets in facilities, including improved maintenance efficiency, enhanced asset lifespan, streamlined operations, and better regulatory compliance.