At its core, CMMS integrates data from various sources within an organization, such as equipment sensors, historical maintenance records, and real-time operational data. By analyzing this wealth of information, CMMS can identify patterns and trends that signal potential issues with machinery. This proactive approach allows maintenance teams to schedule repairs during planned downtimes, minimizing unplanned disruptions and costly downtime.
Moreover, CMMS enhances the accuracy of predictive maintenance models by providing real-time updates and alerts. Maintenance technicians receive notifications when equipment performance deviates from normal parameters, enabling them to take preemptive actions before failures escalate. This proactive stance not only saves on repair costs but also extends the lifespan of critical assets, optimizing overall operational efficiency.
Implementing CMMS also fosters a culture of continuous improvement within organizations. By systematically tracking maintenance activities and their outcomes, CMMS enables managers to refine predictive models based on empirical data. This iterative process enhances the reliability and effectiveness of predictive maintenance strategies over time, aligning maintenance efforts closely with business objectives.
CMMS empowers organizations to shift from reactive maintenance practices to proactive strategies that prioritize cost savings and operational efficiency. By harnessing the power of data analytics and real-time insights, CMMS transforms predictive maintenance into a dynamic process that anticipates and mitigates equipment failures before they impact production. As industries embrace digital transformation, CMMS stands as a cornerstone technology driving sustainable growth and competitiveness through optimized asset management and maintenance practices.
Unlocking Efficiency: CMMS and the Future of Predictive Maintenance
In today’s rapidly evolving industrial landscape, efficiency is not just a goal but a necessity. As businesses strive to optimize their operations and reduce downtime, the role of Computerized Maintenance Management Systems (CMMS) has become increasingly crucial. These systems, designed to streamline maintenance processes and asset management, are now paving the way for a new era in predictive maintenance.
CMMS platforms integrate various functionalities that empower maintenance teams to work smarter and more proactively. By centralizing data on equipment health, work orders, and historical maintenance records, CMMS enables organizations to make data-driven decisions swiftly. This shift from reactive to proactive maintenance strategies is where the true potential of CMMS lies.
Predictive maintenance, enabled by advanced analytics and machine learning algorithms within CMMS, allows businesses to anticipate equipment failures before they occur. Imagine a scenario where sensors embedded in machinery continuously gather data on performance metrics. These data points are then analyzed in real-time by CMMS, which detects anomalies or patterns indicative of potential issues. By preemptively scheduling maintenance based on these insights, businesses can prevent costly breakdowns and minimize unplanned downtime.
Furthermore, CMMS facilitates a more efficient allocation of resources. Maintenance tasks can be prioritized based on criticality and urgency, ensuring that the right resources are deployed at the right time. This optimization not only enhances equipment reliability but also improves overall operational efficiency.
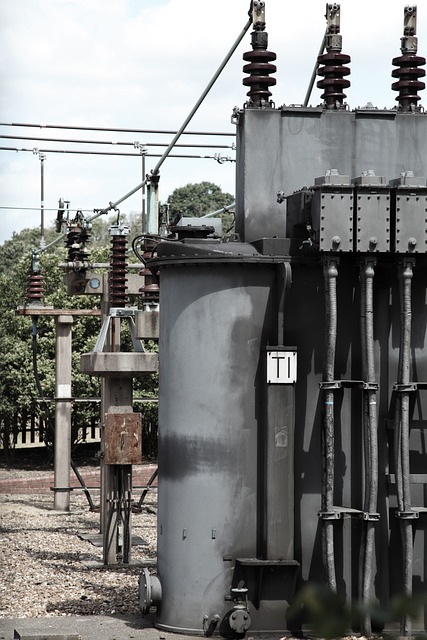
In essence, CMMS is not just a tool but a strategic asset that empowers organizations to unlock new levels of efficiency and productivity. By harnessing the power of predictive maintenance, businesses can stay ahead in a competitive market environment where uptime and reliability are paramount. As industries continue to embrace digital transformation, CMMS will undoubtedly play a pivotal role in shaping the future of maintenance practices.
Cost-Saving Secrets: The Impact of CMMS on Predictive Maintenance
Curious about how businesses can slash costs effectively while enhancing equipment reliability? Enter CMMS, or Computerized Maintenance Management Systems, the unsung heroes behind predictive maintenance strategies.
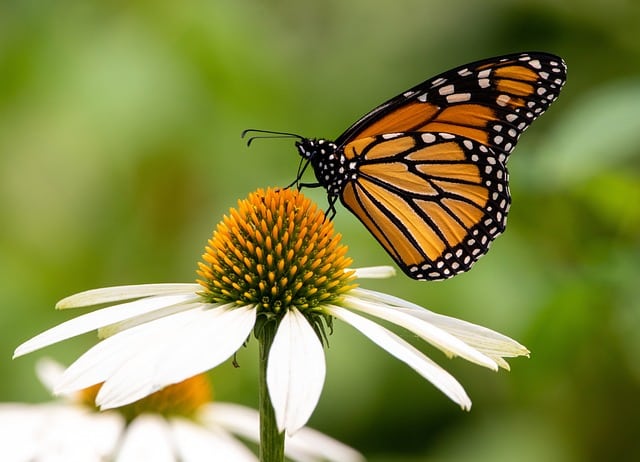
Imagine this: your company relies on a fleet of machines humming along, pivotal to daily operations. Suddenly, a critical machine falters, causing costly downtime and urgent repair bills. That’s where CMMS swoops in, transforming reactive maintenance woes into proactive solutions.
CMMS isn’t just another tech acronym. It’s your maintenance wizard, leveraging data analytics to predict potential breakdowns before they happen. By analyzing historical maintenance data and equipment performance metrics, CMMS identifies patterns that could signal future issues. This foresight allows maintenance teams to schedule repairs during planned downtime, minimizing disruptions and maximizing productivity.
But wait, there’s more. Beyond predicting maintenance needs, CMMS optimizes spare parts inventory management. No more stockpiling or scrambling for parts last minute. With CMMS, you can maintain just-in-time inventory levels, reducing excess stock and slashing inventory holding costs.
Picture this: your operations running smoother than ever, with fewer unexpected shutdowns and reduced emergency repairs. CMMS empowers your team to prioritize preventive tasks, keeping your equipment in peak condition and extending its lifespan.
In today’s competitive landscape, every dollar saved counts. CMMS doesn’t just save costs; it enhances operational efficiency and boosts your bottom line. It’s not just about fixing things when they break; it’s about anticipating needs and staying steps ahead.
Ready to revolutionize your maintenance strategy? Embrace CMMS, the game-changer in predictive maintenance. Harness its power to cut costs, streamline operations, and elevate your business to new heights. It’s not magic—it’s CMMS, making predictive maintenance a reality.
This article aims to inform readers about the benefits of CMMS in predictive maintenance while maintaining an engaging and conversational tone, suitable for both informative purposes and SEO optimization.
Smart Investments: Leveraging CMMS for Efficient Predictive Maintenance
When it comes to managing assets and equipment in industries like manufacturing or logistics, efficiency is the name of the game. Smart investments can make all the difference, and one such investment that stands out is leveraging CMMS (Computerized Maintenance Management System) for efficient predictive maintenance.
Imagine this: your factory operates like a well-oiled machine, humming along smoothly day in and day out. But behind the scenes, there’s a sophisticated system at work ensuring that every piece of equipment is running at its optimal best. That’s where CMMS comes into play. It’s not just about fixing things when they break anymore; it’s about predicting when something might go wrong and preventing it from happening in the first place.
CMMS software works by collecting real-time data from equipment sensors and historical maintenance records. It crunches numbers, identifies patterns, and spots potential issues before they escalate into costly downtime. Think of it as a crystal ball that helps maintenance teams stay one step ahead of problems, ensuring that operations run smoothly without unexpected interruptions.
The beauty of CMMS lies in its ability to streamline workflows. Maintenance tasks are scheduled automatically based on usage patterns and predictive analytics. This means less time spent putting out fires and more time focusing on strategic initiatives that drive the business forward.
But efficiency isn’t just about saving time and money. It’s also about improving safety and reliability. By catching problems early, CMMS helps reduce the risk of accidents and extends the lifespan of critical equipment. It’s like having a guardian angel watching over your machinery, ensuring that everything operates within safe parameters.
In today’s fast-paced world, where every minute of downtime can translate into lost revenue, leveraging CMMS for predictive maintenance isn’t just a smart move—it’s essential for staying competitive. It’s about embracing technology to work smarter, not harder, and reaping the benefits of a proactive approach to equipment management.
Ready to take your maintenance strategy to the next level? Explore how CMMS can transform your operations and pave the way for a more efficient and reliable future.
From Predictive to Profit: CMMS Tools Driving Cost-Saving Strategies
In today’s fast-paced industrial landscape, efficiency isn’t just a goal—it’s a necessity. That’s where CMMS (Computerized Maintenance Management Systems) tools step in, revolutionizing how businesses manage their maintenance operations from predictive models to profit-saving strategies.
Imagine having the power to foresee equipment failures before they even happen. CMMS tools do just that, leveraging predictive analytics to preemptively identify potential issues based on historical data and real-time insights. This proactive approach not only minimizes downtime but also slashes repair costs, keeping operations running smoothly without unexpected interruptions.
But the benefits of CMMS tools go beyond predictive maintenance. These systems streamline the entire maintenance workflow, optimizing schedules and resource allocation. By automating routine tasks and reminders, they ensure that every piece of equipment is serviced at the optimal time, extending their lifespan and preventing costly breakdowns.
Moreover, CMMS tools are not just about reacting to problems—they empower businesses to make data-driven decisions that drive profitability. By analyzing maintenance trends and performance metrics, companies can identify inefficiencies and fine-tune their processes for maximum output at minimal cost.
Picture CMMS tools as the orchestra conductor of maintenance operations, harmonizing every instrument (or machine) to play at its peak performance. They provide clarity amidst complexity, turning raw data into actionable insights that propel businesses forward in the competitive market.
CMMS tools are not merely tools—they are transformative assets that convert predictive insights into tangible profits. By embracing these technologies, businesses not only save costs but also gain a competitive edge through enhanced operational efficiency and strategic decision-making.
Harnessing Data: CMMS Integration and Predictive Maintenance Benefits
Integrating CMMS with predictive maintenance technologies enhances operational efficiency by leveraging data analytics to forecast equipment failures based on historical performance and real-time data inputs. This proactive approach minimizes downtime, reduces repair costs, and extends the lifespan of critical assets.
Predictive maintenance algorithms analyze data patterns, such as equipment runtime, vibration levels, and temperature fluctuations, to detect anomalies that indicate potential issues. By identifying these patterns early, maintenance teams can schedule repairs during planned downtime, avoiding unexpected breakdowns that disrupt production.
Moreover, CMMS integration streamlines workflow management by automating maintenance schedules and prioritizing tasks based on asset criticality and historical performance data. This ensures that maintenance resources are allocated efficiently, maximizing productivity and minimizing operational disruptions.
In essence, the benefits of harnessing data through CMMS integration for predictive maintenance are manifold. It empowers businesses to shift from reactive to proactive maintenance strategies, saving costs, improving reliability, and enhancing overall asset management. By embracing predictive analytics, organizations gain a competitive edge in today’s fast-paced industrial landscape, where operational efficiency and asset reliability are paramount for sustainable growth.
Frequently Asked Questions
What are the key benefits of using CMMS for predictive maintenance?
Discover the advantages of CMMS for predictive maintenance, ensuring equipment reliability, reducing downtime, optimizing maintenance schedules, and prolonging asset lifespan.
What is CMMS and how does it enhance predictive maintenance?
Learn what CMMS is and how it boosts predictive maintenance efficiency. Discover how CMMS software streamlines equipment monitoring, schedules preventive tasks, and analyzes data to predict breakdowns, minimizing downtime and maximizing operational uptime.
How does CMMS facilitate data-driven decision-making in maintenance?
Learn how CMMS (Computerized Maintenance Management System) enhances data-driven decision-making in maintenance by centralizing asset information, streamlining work orders, and providing analytics on equipment performance and maintenance history.
What features should I look for in a CMMS system to maximize cost savings?
Discover the essential features to optimize cost savings with a CMMS system. Learn how to leverage preventive maintenance scheduling, asset tracking, inventory management, and reporting capabilities to streamline operations and reduce downtime.
How can CMMS software optimize maintenance schedules to save costs?
Learn how CMMS software optimizes maintenance schedules to save costs by automating preventive maintenance tasks, scheduling inspections efficiently, minimizing downtime with predictive maintenance alerts, and tracking asset performance for timely repairs.