Have you ever wondered how modern businesses keep their machinery and facilities running smoothly without unexpected breakdowns? The secret lies in effective maintenance scheduling, powered by a CMMS (Computerized Maintenance Management System). CMMS is like the conductor of an orchestra, ensuring all instruments play in harmony at the right time.
A CMMS enhances maintenance scheduling accuracy by streamlining processes and minimizing human error. Imagine it as a digital assistant for your maintenance team, keeping track of every task and alerting technicians when equipment needs attention. By storing historical data and maintenance records, a CMMS analyzes patterns to predict future maintenance needs. This predictive capability prevents sudden breakdowns, saving businesses from costly downtime.
One of the standout features of a CMMS is its ability to automate routine tasks. This automation reduces the burden on maintenance staff, allowing them to focus on more complex issues that require human expertise. By setting predefined schedules and automated alerts, a CMMS ensures that no maintenance task is overlooked or delayed, thereby improving operational efficiency.
Furthermore, a CMMS facilitates better resource allocation. It helps in assigning the right technician with the necessary skills to each job. This ensures that repairs are conducted swiftly and accurately, reducing the time equipment spends out of service. As a result, businesses can maintain optimal productivity levels without interruptions.
In essence, a CMMS is not just a tool but a strategic asset for any organization looking to optimize maintenance operations. It fosters a proactive maintenance approach rather than a reactive one, aligning with the modern ethos of efficiency and reliability in business management.
Streamlining Maintenance: How CMMS Software Enhances Scheduling Precision
CMMS software enables organizations to meticulously plan and schedule maintenance activities, ensuring that equipment and facilities remain in optimal condition. By centralizing data related to maintenance schedules, work orders, and asset management, CMMS software provides maintenance teams with real-time visibility and control over their operations.
One of the key advantages of CMMS software is its ability to automate routine maintenance tasks based on predefined schedules or triggers. This automation helps in preventing breakdowns and prolonging the lifespan of critical assets. For instance, predictive maintenance features in CMMS software analyze historical data and equipment performance to forecast potential issues, allowing maintenance teams to proactively address them before they escalate.
Moreover, CMMS software facilitates better resource allocation by efficiently managing inventory and labor resources. By optimizing resource utilization, organizations can reduce unnecessary costs associated with emergency repairs and downtime, thereby improving overall profitability.
Another significant benefit of CMMS software is its role in compliance management. Industries operating under stringent regulatory requirements benefit from CMMS systems that ensure all maintenance activities are documented and compliant with regulatory standards. This helps organizations avoid penalties and maintain operational continuity.
CMMS software transforms maintenance operations by streamlining scheduling, enhancing precision, and ensuring compliance. By leveraging advanced features such as predictive maintenance and resource optimization, businesses can achieve higher productivity levels and operational efficiency.
Unlocking Efficiency: The Role of CMMS in Optimizing Maintenance Timelines
In the dynamic world of maintenance management, achieving peak efficiency is paramount. Enter CMMS, or Computerized Maintenance Management Systems, a game-changer in optimizing maintenance timelines. But what exactly makes CMMS so pivotal?
Imagine CMMS as your digital ally, orchestrating maintenance tasks with precision akin to a maestro leading a symphony. By centralizing data on equipment, work orders, and schedules, CMMS streamlines operations seamlessly. It’s like having a virtual assistant dedicated to keeping your facility running smoothly.
One of CMMS’s standout features is its preventive maintenance capabilities. Instead of waiting for equipment to break down, CMMS schedules proactive upkeep based on usage data and predefined intervals. This foresight not only minimizes downtime but also extends the lifespan of critical assets, saving both time and money.
Moreover, CMMS enhances workflow transparency. Team members can access real-time updates on tasks and priorities, fostering collaboration and accountability across departments. It’s akin to equipping your team with high-powered binoculars in a dense fog, ensuring everyone sees the same clear path forward.
The beauty of CMMS lies in its adaptability. Whether you manage a bustling manufacturing floor or oversee a sprawling office complex, CMMS adjusts to your unique needs. It integrates seamlessly with existing software and hardware, offering a cohesive solution without disrupting established workflows.
In essence, CMMS isn’t just a tool—it’s a catalyst for operational excellence. By harnessing data-driven insights and fostering proactive maintenance practices, CMMS empowers organizations to unlock new levels of efficiency. It’s the difference between navigating through choppy waters blindly versus sailing with precision towards your goals.
Ready to elevate your maintenance strategy? Embrace CMMS and transform your maintenance timelines from reactive chaos to proactive harmony. Efficiency awaits—seize it with CMMS at your helm.
Data-Driven Decisions: Enhancing Maintenance Accuracy with CMMS Technology
In today’s fast-paced industrial landscape, precision and efficiency in maintenance operations can make all the difference. This is where CMMS (Computerized Maintenance Management System) technology steps in as a game-changer. By leveraging data-driven insights, CMMS empowers maintenance teams to enhance accuracy and streamline operations like never before.
Imagine a scenario where every maintenance decision is backed by real-time data analysis. CMMS systems collect and process vast amounts of data from equipment sensors, historical maintenance records, and operational metrics. This wealth of information allows maintenance managers to identify patterns, predict failures, and schedule preventive maintenance proactively.
One of the key benefits of CMMS technology is its ability to optimize asset management. By tracking the lifecycle of each asset, from installation to decommissioning, CMMS ensures that maintenance tasks are performed at optimal intervals. This not only prolongs the lifespan of equipment but also reduces downtime and operational costs.
Moreover, CMMS facilitates compliance with regulatory standards and industry best practices. By documenting maintenance activities and generating comprehensive reports, organizations can demonstrate adherence to safety and quality standards during audits.
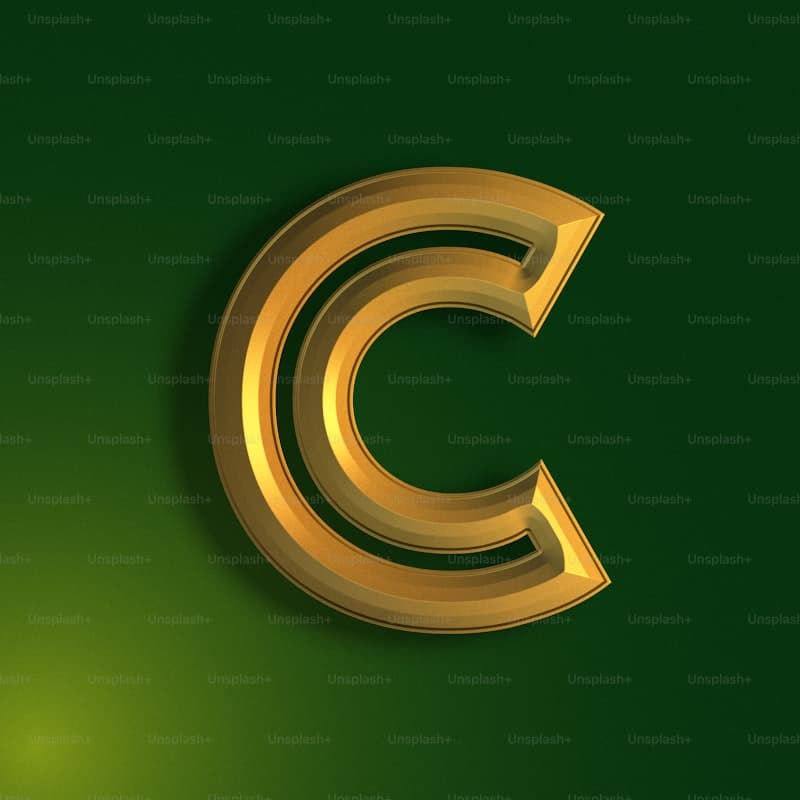
Another compelling aspect of CMMS is its role in fostering a culture of continuous improvement. By analyzing performance metrics and feedback loops, teams can iterate on maintenance strategies, refine processes, and achieve higher levels of operational efficiency over time.
In essence, CMMS technology transforms maintenance into a proactive, data-driven endeavor. It empowers organizations to make informed decisions, minimize risks, and maximize asset uptime. As industries evolve, embracing CMMS not only ensures operational excellence but also positions businesses to thrive in competitive markets.
Ready to elevate your maintenance operations with CMMS technology? Embrace the power of data-driven decisions and watch as your organization achieves new heights of efficiency and reliability.
From Chaos to Coordination: CMMS Tools and Reliable Maintenance Scheduling
CMMS tools are the superheroes of maintenance scheduling. Imagine having a digital assistant that not only keeps a detailed record of all your equipment but also reminds you when maintenance tasks are due. It’s like having a reliable sidekick that ensures everything runs smoothly behind the scenes.
One of the key features of CMMS tools is their ability to centralize information. Instead of hunting through paper records or different spreadsheets, everything you need is neatly organized in one place. This centralized approach not only saves time but also minimizes the risk of errors and oversights.
Another game-changing aspect is the predictive maintenance capabilities offered by advanced CMMS systems. By analyzing historical data and equipment performance, these tools can predict when a machine is likely to fail. This proactive approach allows maintenance teams to intervene before a breakdown occurs, thereby preventing costly repairs and unexpected downtime.
Moreover, CMMS tools promote better coordination among maintenance teams. Assigning tasks, tracking progress, and communicating updates become seamless processes. It’s like orchestrating a well-choreographed dance where every move is synchronized for maximum efficiency.
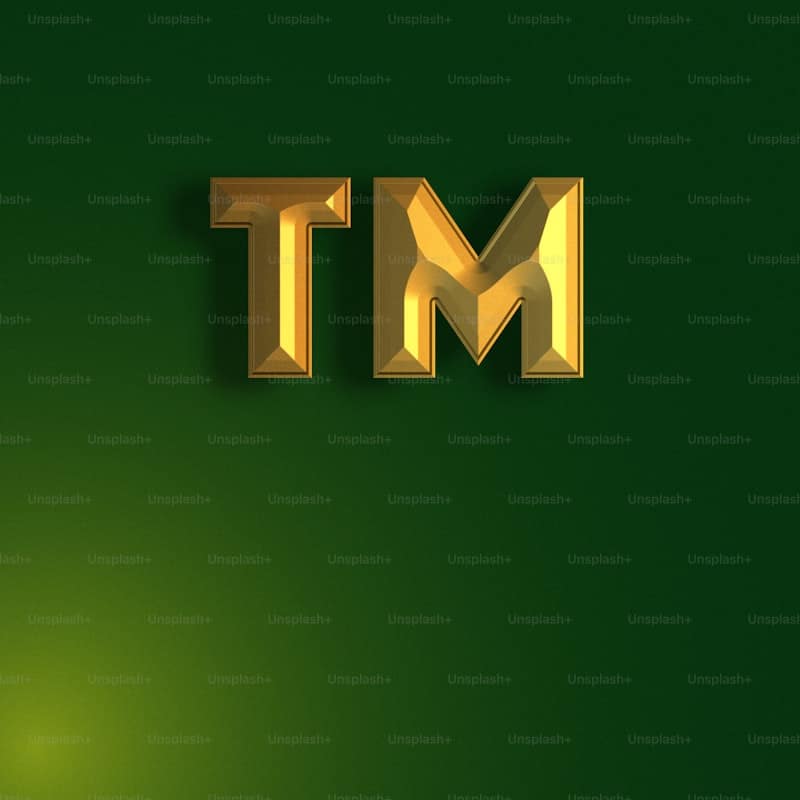
In essence, CMMS tools have revolutionized maintenance scheduling from being reactive to proactive. They empower businesses to streamline operations, reduce costs, and prolong the lifespan of their equipment. Whether you’re managing a small business or a large industrial facility, investing in a robust CMMS system can truly transform chaos into coordination.
Predictive Power: Using CMMS to Forecast Maintenance Needs
Have you ever wondered how some businesses seem to effortlessly maintain their equipment in prime condition, avoiding costly breakdowns and downtime? The secret lies in predictive maintenance powered by CMMS (Computerized Maintenance Management Systems). CMMS tools harness the predictive power of data to forecast maintenance needs accurately.
Imagine your equipment as a car traveling down a road. Without regular maintenance, it’s like driving without ever checking the engine oil or brakes. Eventually, something is bound to break down, causing delays and unexpected expenses. Now, picture having a skilled mechanic who can predict exactly when and what maintenance your car needs, ensuring smooth travels with minimal interruptions. That’s what CMMS does for industrial machinery and equipment.
Using historical data and advanced algorithms, CMMS analyzes past performance, detects patterns, and predicts when maintenance is likely needed. This proactive approach prevents equipment failures before they occur, saving businesses significant time and money. Instead of waiting for something to break, companies can schedule maintenance during planned downtimes, optimizing operational efficiency.
Moreover, CMMS integrates seamlessly with IoT (Internet of Things) devices, sensors, and other smart technologies, creating a network of real-time data streams. This connectivity enables continuous monitoring of equipment health, providing instant alerts when anomalies or potential issues arise. It’s like having a team of vigilant inspectors constantly on watch, ensuring everything runs smoothly.
In essence, predictive maintenance through CMMS transforms reactive, costly repairs into proactive, cost-effective strategies. By leveraging data insights, businesses can extend the lifespan of their assets, reduce maintenance costs, and enhance overall productivity. It’s not just about fixing problems—it’s about foreseeing and preventing them, empowering businesses to stay ahead in today’s competitive landscape.
This article aims to highlight the benefits and capabilities of CMMS in predictive maintenance, using a conversational tone and engaging language to captivate the reader’s interest.
Frequently Asked Questions
How does using a CMMS reduce downtime through improved maintenance scheduling?
Learn how utilizing a Computerized Maintenance Management System (CMMS) minimizes downtime by enhancing maintenance scheduling. Discover how streamlined workflows and proactive maintenance planning prevent equipment failures and optimize operational efficiency.
What role does data analytics play in enhancing maintenance scheduling with a CMMS?
Data analytics optimizes maintenance scheduling with a CMMS by leveraging historical data to predict equipment failures, schedule preventive maintenance efficiently, and minimize downtime. It enables proactive decision-making based on real-time insights, ensuring equipment reliability and operational efficiency.
How can a CMMS optimize preventive maintenance schedules to improve accuracy?
Learn how a CMMS (Computerized Maintenance Management System) optimizes preventive maintenance schedules to enhance accuracy by automating task scheduling based on equipment usage, condition monitoring data, and predefined maintenance intervals. This ensures timely maintenance, reduces downtime, extends equipment lifespan, and enhances operational efficiency.
What are the key features of a CMMS that contribute to better maintenance scheduling accuracy?
Discover how CMMS features enhance maintenance scheduling accuracy. Learn about key tools like preventive maintenance scheduling, asset tracking, and real-time updates.
What is a CMMS and how does it enhance maintenance scheduling accuracy?
Discover how CMMS software improves maintenance scheduling accuracy by centralizing data, automating tasks, and providing real-time insights, ensuring timely maintenance interventions and minimizing downtime.