Imagine running a factory where machines hum tirelessly, each one crucial to your operations. Now, picture this: instead of waiting for those machines to break down unexpectedly, imagine being one step ahead—fixing issues before they even arise. That’s the power of CMMS, or Computerized Maintenance Management System. It’s not just a tool; it’s a game-changer for businesses aiming to stay ahead in the competitive landscape of today.
CMMS enables proactive maintenance strategies by acting as a digital guardian for your equipment. Unlike traditional reactive maintenance, where you fix things after they go wrong, proactive maintenance anticipates issues. It’s like having a crystal ball that predicts when a machine might need a tune-up, preventing costly downtime and repairs.
Here’s how it works: CMMS gathers data—lots of it. From machine performance metrics to historical maintenance records, it compiles everything into actionable insights. Think of it as your maintenance diary, but smarter. By analyzing this data, CMMS can identify patterns and trends, spotting potential problems before they escalate. It’s like having a savvy detective on your team, uncovering clues that could save you time and money.
Moreover, CMMS doesn’t just stop at predicting maintenance needs. It also helps streamline workflows. Tasks that used to be cumbersome—like scheduling maintenance, tracking spare parts, and managing work orders—are now a breeze. It’s as if your operations have suddenly found a shortcut, freeing up valuable time and resources for other critical tasks.
In essence, CMMS transforms maintenance from a reactive chore to a proactive strategy. It shifts the focus from firefighting to foresight, ensuring your machines run smoothly and your business stays ahead of the curve. With CMMS, you’re not just fixing problems; you’re preventing them altogether—a true game-changer in today’s fast-paced industrial landscape.

This article aims to engage readers by illustrating the transformative power of CMMS in a conversational and informative manner, focusing on its benefits and practical applications without delving into technical jargon.
Revolutionizing Maintenance: CMMS Unveils Proactive Strategies for Industry Leaders
In today’s fast-paced industrial landscape, staying ahead of maintenance issues is crucial for seamless operations. That’s where Computerized Maintenance Management Systems (CMMS) come into play, transforming how businesses manage their maintenance tasks. Unlike traditional reactive maintenance approaches that wait for equipment to break down, CMMS empowers industry leaders with proactive strategies.
Imagine having a tool that predicts when a machine might malfunction before it even shows signs of trouble. That’s the power of CMMS. By leveraging real-time data and analytics, CMMS software can detect patterns and anomalies in equipment performance. It allows maintenance teams to schedule preventive maintenance tasks precisely when they are needed, minimizing downtime and maximizing productivity.
For industry leaders, this proactive approach translates into significant cost savings and operational efficiency. Rather than dealing with sudden breakdowns that halt production and require costly emergency repairs, CMMS enables businesses to maintain their equipment in optimal condition. It’s like giving your machinery regular check-ups to catch potential issues early, ensuring they run smoothly without unexpected interruptions.
Moreover, CMMS doesn’t just stop at preventive maintenance. It also streamlines the entire maintenance workflow. From work order management to inventory tracking and reporting, CMMS centralizes all maintenance activities in one platform. This centralized approach improves communication between maintenance teams and other departments, fostering collaboration and transparency across the organization.
Implementing CMMS isn’t just a trend; it’s a strategic decision that sets industry leaders apart. By investing in proactive maintenance strategies, businesses not only enhance their operational resilience but also boost employee morale. When equipment functions reliably, employees can focus on their tasks without the stress of potential disruptions, fostering a more productive work environment.
CMMS is more than just a tool; it’s a game-changer for industry leaders looking to revolutionize maintenance practices. By embracing proactive strategies facilitated by CMMS, businesses can achieve sustainable growth, operational excellence, and a competitive edge in their respective markets.
Predictive Power: CMMS Technology Redefines Maintenance with Data-Driven Insights
Imagine having the ability to foresee equipment failures before they happen, like a crystal ball for maintenance professionals. That’s exactly what Predictive Maintenance, powered by CMMS (Computerized Maintenance Management System) technology, offers to industries today. By harnessing the power of data-driven insights, CMMS is revolutionizing how companies manage their assets and maintenance schedules.
Traditionally, maintenance has been a reactive process – waiting for equipment to break down before fixing it. This approach not only leads to costly downtime but also affects productivity and customer satisfaction. However, with CMMS systems integrating predictive analytics, maintenance teams can now predict when equipment might fail based on historical data, usage patterns, and real-time monitoring.
Picture this: Just like a doctor monitors your health through regular check-ups and diagnostic tests, CMMS monitors the health of machines. It continuously collects data on factors like temperature, vibration, and operating hours. Using sophisticated algorithms, it analyzes this data to detect patterns that indicate potential issues. This proactive approach allows maintenance teams to schedule repairs during planned downtimes, preventing unexpected breakdowns and optimizing asset performance.
Moreover, CMMS doesn’t stop at predicting failures. It also optimizes maintenance schedules by prioritizing tasks based on criticality and resource availability. This means technicians can focus their efforts where they are most needed, reducing downtime and improving operational efficiency.
In industries like manufacturing, where every minute of downtime translates into lost revenue, the predictive power of CMMS is a game-changer. It shifts maintenance from a cost center to a strategic asset, enabling companies to allocate resources more effectively and extend the lifespan of their equipment.
From Reactive to Proactive: CMMS Systems Leading the Charge in Maintenance Efficiency
Imagine your business as a well-oiled machine, where every part works harmoniously without interruptions. That’s the essence of what CMMS systems aim to achieve. By harnessing real-time data and predictive analytics, these systems empower maintenance teams to anticipate equipment failures before they occur. It’s like having a crystal ball that predicts when and where a breakdown might happen, allowing proactive measures to be taken well in advance.
One of the key strengths of CMMS is its ability to schedule maintenance tasks based on usage patterns and equipment condition. It’s akin to scheduling regular check-ups for your car before a breakdown happens on the highway. This approach not only reduces downtime but also extends the lifespan of critical assets, ultimately saving businesses significant costs in repairs and replacements.
Moreover, CMMS systems streamline workflows by automating routine tasks such as work orders, inventory management, and compliance tracking. This automation not only frees up valuable human resources but also ensures that maintenance activities are carried out efficiently and consistently. It’s like having a reliable assistant who manages all the nitty-gritty details, leaving your team to focus on more strategic initiatives.
In today’s fast-paced business environment, where every minute of downtime can translate into lost revenue, adopting CMMS systems isn’t just a choice but a necessity for staying competitive. Businesses that embrace proactive maintenance through CMMS are better equipped to respond to challenges swiftly and maintain high levels of operational uptime. It’s about moving from firefighting mode to a proactive stance, where maintenance becomes a strategic advantage rather than a reactive obligation.
As industries continue to evolve, CMMS systems will continue to evolve alongside them, incorporating advanced technologies like IoT (Internet of Things) and AI (Artificial Intelligence) to further enhance predictive capabilities. The future of maintenance lies in being proactive, and CMMS systems are at the forefront, leading the charge towards greater efficiency and reliability.
Harnessing Innovation: CMMS Tools Pave the Way for Predictive Maintenance Success
Imagine having the ability to predict equipment failures before they even occur. That’s the power of predictive maintenance fueled by CMMS tools. Unlike traditional reactive maintenance, where repairs are made after equipment breaks down, predictive maintenance uses data analytics to foresee issues. It’s like having a crystal ball for your machinery, allowing you to fix problems proactively, minimizing downtime and maximizing efficiency.
CMMS tools are the backbone of this predictive prowess. They gather real-time data from sensors embedded in equipment, analyzing it to detect patterns and anomalies. These insights enable maintenance teams to schedule repairs during planned downtimes, preventing costly unplanned shutdowns. It’s a game-changer for industries where every minute of operation counts towards profitability.
Moreover, CMMS tools streamline the entire maintenance process. From work orders to inventory management, everything is digitized and accessible in one centralized platform. This not only improves operational efficiency but also empowers teams to make data-driven decisions swiftly. Imagine having all maintenance records at your fingertips, accessible with just a few clicks. It’s efficiency redefined.
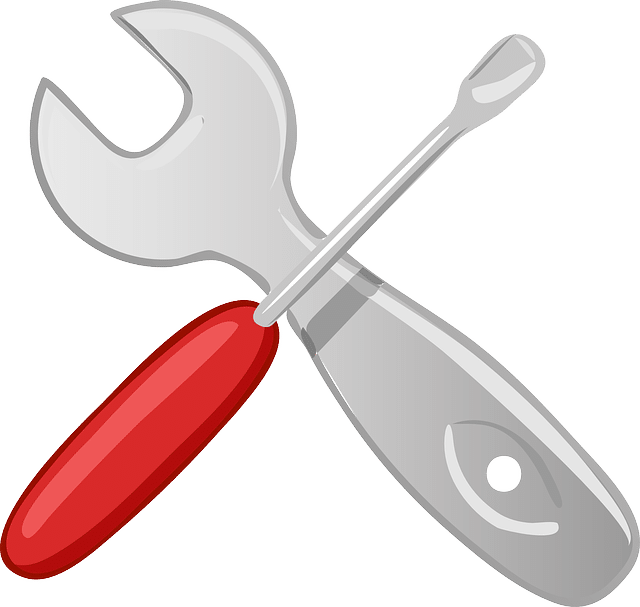
But the impact goes beyond just efficiency gains. Predictive maintenance reduces overall maintenance costs by preventing major breakdowns and extending equipment lifespan. It also enhances workplace safety, as well-maintained equipment is less likely to malfunction unexpectedly.
Breaking Down Barriers: CMMS Empowers Early Detection through Proactive Maintenance
Imagine a scenario where a manufacturing plant operates seamlessly without disruptions. Behind this efficiency lies CMMS, acting as a proactive sentinel. It streamlines maintenance workflows, ensuring equipment operates at peak performance. By leveraging data analytics and predictive algorithms, CMMS identifies potential faults in real-time, prompting technicians to intervene swiftly.
The true power of CMMS lies in its ability to transcend reactive approaches to maintenance. Instead of waiting for breakdowns to occur, facilities equipped with CMMS anticipate issues. It’s akin to having a weather radar that forecasts storms before they hit, allowing businesses to reinforce their defenses.
Furthermore, CMMS fosters a culture of accountability and efficiency. Maintenance teams are empowered with clear insights and actionable data, enabling them to prioritize tasks based on criticality and impact. This proactive stance not only minimizes downtime but also optimizes resources, driving overall operational excellence.
In essence, CMMS isn’t just a tool; it’s a catalyst for change. It shifts the paradigm from firefighting to foresight, from crisis management to controlled precision. Organizations embracing CMMS gain a competitive edge by preemptively addressing maintenance needs, thereby safeguarding assets and bolstering productivity.
Frequently Asked Questions
How does CMMS help in scheduling preventive maintenance tasks?
Learn how CMMS (Computerized Maintenance Management System) facilitates scheduling preventive maintenance tasks efficiently. Discover how it automates reminders, tracks maintenance history, and optimizes equipment uptime.
How can CMMS software improve asset reliability through proactive maintenance?
Learn how CMMS software enhances asset reliability by enabling proactive maintenance strategies. Discover how to leverage scheduled inspections, predictive analytics, and preventive maintenance tasks to minimize downtime and extend asset lifespan.
What are the key features of CMMS that facilitate predictive maintenance?
Learn about the essential features of CMMS (Computerized Maintenance Management System) that enable predictive maintenance, enhancing efficiency and reducing downtime. Discover how CMMS automates asset management, schedules maintenance tasks proactively based on real-time data, integrates with IoT sensors for condition monitoring, and analyzes historical maintenance data to predict equipment failures.
What role does data analytics play in enabling proactive maintenance with CMMS?
Data analytics in CMMS enables proactive maintenance by analyzing historical equipment data to predict and prevent potential failures. It helps in scheduling maintenance tasks based on actual performance metrics, optimizing equipment uptime, and reducing unplanned downtime.
What is CMMS and how does it support proactive maintenance?
Learn what CMMS is and how it enhances proactive maintenance strategies. Discover its role in scheduling tasks, tracking equipment health, and optimizing maintenance workflows for improved efficiency and reduced downtime.