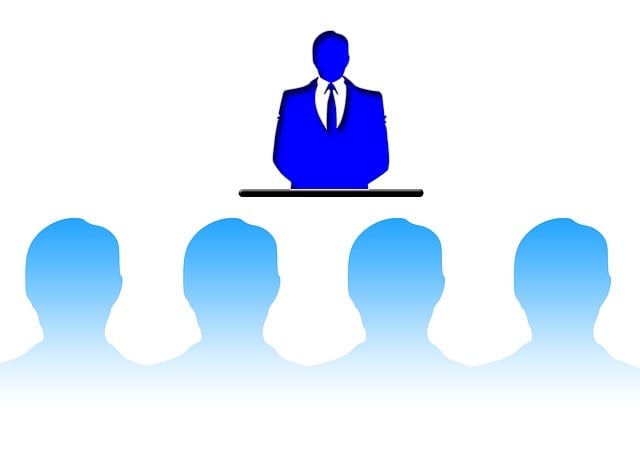
Imagine this: your maintenance team starts their day equipped not just with tools, but with a streamlined plan of action. CMMS does just that by organizing schedules, automating routine tasks, and ensuring everyone knows their role without confusion. This clarity alone can uplift team spirits, eliminating the guesswork and allowing them to focus on what they do best – maintaining equipment and facilities.
Ever felt bogged down by paperwork and endless spreadsheets? CMMS swoops in to save the day. It centralizes all maintenance data in one accessible place, making information retrieval a breeze. No more rifling through files or searching for that elusive work order – everything is neatly categorized and instantly retrievable. This efficiency not only saves time but also reduces frustration, keeping your team motivated and engaged.
Now, let’s talk about productivity. With CMMS handling the nitty-gritty details, your team can devote more energy to proactive maintenance rather than reactive firefighting. Preventive maintenance schedules are automated, ensuring equipment is serviced at optimal intervals. This proactive approach minimizes downtime and costly repairs, boosting overall productivity and keeping operations running smoothly.
Picture this: your maintenance team, empowered by CMMS, feels valued and integral to the organization’s success. When employees feel their work is appreciated and supported by effective tools, morale naturally skyrockets. They become more invested in their tasks, striving for excellence because they see the direct impact of their efforts on operational efficiency.
In essence, CMMS isn’t just a tool – it’s a morale and productivity booster wrapped in digital innovation. By simplifying processes, reducing downtime, and empowering your team, CMMS transforms maintenance from a chore into a strategic advantage. Ready to elevate your maintenance game? Explore how CMMS can revolutionize your team’s morale and productivity today!
Boosting Team Spirit: CMMS Tools That Transform Maintenance Morale
Imagine a workplace where every team member feels empowered and motivated, much like a well-oiled machine humming smoothly. CMMS tools act as the backbone of efficient maintenance operations, streamlining processes and ensuring that equipment downtime is minimized. This not only saves time and resources but also prevents frustration among team members who rely on smooth-running machinery to perform their jobs effectively.
By implementing CMMS tools, teams can better coordinate maintenance schedules, track equipment performance, and proactively address issues before they escalate. This proactive approach not only reduces stress but also instills a sense of accomplishment and pride in maintaining high operational standards.
Furthermore, these tools provide real-time data and analytics, allowing teams to make informed decisions quickly. Imagine having the ability to predict maintenance needs accurately and prevent breakdowns before they occur. It’s like having a crystal ball that guides you through challenges effortlessly, boosting confidence and morale within the team.
In essence, CMMS tools are more than just software; they are catalysts for teamwork and morale. They enable smoother communication between departments, foster a culture of accountability, and empower team members to take ownership of their roles in maintaining a well-functioning workplace.
From Efficiency to Enthusiasm: CMMS Impact on Maintenance Team Productivity
In the realm of maintenance management, CMMS (Computerized Maintenance Management System) stands as a pivotal tool transforming the landscape from mere efficiency to enthusiastic productivity. Imagine a scenario where every maintenance task flows seamlessly, schedules are adhered to without a hitch, and equipment downtime is minimized to negligible levels. That’s the power CMMS brings to the table.
CMMS systems streamline maintenance operations by centralizing data, automating workflows, and enhancing communication between team members. This centralized approach means that everyone involved in maintenance—from technicians to managers—has real-time access to critical information. Tasks are assigned promptly, and progress updates are logged instantly, ensuring that no detail gets lost in the shuffle.
What sets CMMS apart is its ability to turn routine tasks into opportunities for efficiency gains. By automating repetitive processes and providing predictive maintenance insights, CMMS empowers maintenance teams to preemptively address issues before they escalate. This proactive approach not only prolongs equipment lifespan but also boosts team morale as they witness tangible results of their efforts.
Picture a maintenance team where every member is not just meeting targets but surpassing them with a renewed sense of purpose. CMMS fosters this enthusiasm by freeing up time for technicians to focus on value-added activities rather than mundane paperwork or reactive maintenance. It’s akin to equipping them with tools that not only get the job done but also inspire them to excel.
The impact of CMMS on maintenance team productivity transcends efficiency metrics. It cultivates a culture where proactive maintenance becomes the norm, downtime becomes a rarity, and each team member contributes passionately to organizational success. Embracing CMMS isn’t just about adopting a software solution; it’s about igniting a spirit of enthusiasm that propels maintenance operations to new heights.
Unveiling the Secret Sauce: CMMS Systems and Elevated Team Morale
Imagine a tool that not only streamlines your maintenance operations but also boosts your team’s spirits. That’s precisely what a Computerized Maintenance Management System (CMMS) does. It’s like having a virtual assistant dedicated to keeping your equipment running smoothly while lifting the burden off your team’s shoulders.
Firstly, CMMS systems centralize all maintenance activities into one platform. Whether it’s scheduling preventive maintenance or managing work orders, everything is seamlessly organized. This means fewer missed tasks and breakdowns, translating to less stress for your maintenance team and fewer disruptions for the entire operation.
Moreover, these systems are proactive. By predicting when equipment might need servicing before issues arise, CMMS prevents unexpected downtime. Imagine your team no longer scrambling to fix a breakdown but instead working proactively to prevent it in the first place. It’s a shift from reactive chaos to proactive peace of mind.
Furthermore, CMMS software enhances communication and collaboration among team members. Everyone involved—technicians, managers, and even suppliers—can access real-time data and updates. This transparency not only fosters a sense of teamwork but also empowers employees to take ownership of their tasks and contribute to overall efficiency.
In addition to operational benefits, there’s a morale boost that comes with using modern tools effectively. When employees see their efforts leading to smoother operations and happier customers, job satisfaction naturally rises. It’s like giving your team the right tools and watching them flourish.
Ultimately, CMMS systems aren’t just about managing maintenance tasks; they’re about elevating team morale by reducing stress, fostering collaboration, and empowering proactive workflows. Ready to see how CMMS can transform your workplace? Discover the secret sauce that’s revolutionizing modern maintenance management.
Empowerment Through Technology: CMMS and Maintenance Team Motivation
In the realm of modern maintenance management, empowering your team is not just a catchphrase—it’s a game-changer. Imagine a scenario where every member of your maintenance team feels equipped, motivated, and valued. That’s where CMMS (Computerized Maintenance Management Systems) step in, revolutionizing how teams operate and perceive their roles.
CMMS isn’t merely a tool; it’s the cornerstone of empowerment. By streamlining workflows, automating routine tasks, and providing real-time data insights, CMMS empowers maintenance teams to work smarter, not harder. Picture this: instead of sifting through piles of paperwork or relying on outdated spreadsheets, technicians have instant access to work orders, asset histories, and maintenance schedules right at their fingertips. It’s like upgrading from a road map to GPS navigation—a seamless experience that enhances efficiency and boosts morale.
But how does this technological empowerment translate into motivation? Let’s break it down. Motivation stems from feeling competent and seeing the impact of one’s work. With CMMS, technicians can tackle tasks more efficiently, reducing downtime and preventing costly breakdowns. This newfound efficiency isn’t just about fixing things faster; it’s about taking pride in delivering top-notch service and being proactive rather than reactive.
Think of CMMS as the conductor of a well-oiled orchestra. It synchronizes efforts, ensures everyone is playing their part harmoniously, and allows for adjustments on the fly—all while keeping morale high and stress low. When maintenance teams are empowered with the right tools, they become proactive problem-solvers rather than firefighting responders.
Moreover, CMMS provides a platform for continuous improvement. By analyzing maintenance data trends, identifying areas for optimization, and implementing preventive strategies, teams can evolve from reactive to predictive maintenance. It’s akin to seeing patterns in the stars and using them to navigate future challenges with confidence.
Beyond Numbers: CMMS Solutions Elevating Maintenance Team Morale
Imagine a scenario where every task, from routine inspections to complex repairs, is seamlessly organized and prioritized. CMMS solutions excel in this aspect by centralizing all maintenance activities into a single platform. This means technicians spend less time searching for information or updating records manually, and more time focusing on hands-on maintenance work.
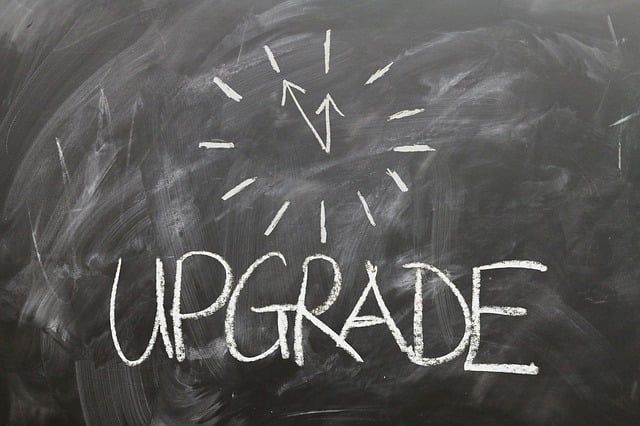
Moreover, these systems empower maintenance teams with real-time data and analytics. By providing insights into equipment performance, maintenance history, and upcoming tasks, CMMS solutions enable proactive maintenance strategies. Technicians can foresee potential issues, plan preventive measures, and prevent costly downtime effectively.
Beyond operational efficiency, CMMS solutions contribute significantly to team morale. When technicians have access to tools that simplify their daily tasks and enhance their productivity, they feel more valued and motivated. It’s akin to equipping them with the right gear to conquer their work challenges efficiently, thereby fostering a sense of accomplishment and pride in their contributions.
Furthermore, the collaborative features of CMMS platforms promote teamwork and communication among team members. Whether it’s assigning tasks, sharing updates, or collaborating on projects, these systems facilitate seamless interaction within the team, fostering a supportive work environment.
Navigating Challenges: CMMS Strategies for Boosting Team Productivity
Managing maintenance operations can be a complex puzzle, but with the right strategies, your team can achieve greater efficiency and productivity. CMMS (Computerized Maintenance Management System) plays a pivotal role in this journey, acting as the backbone of streamlined processes and proactive maintenance practices.
Imagine your maintenance team as a well-oiled machine, where every part works harmoniously to keep operations running smoothly. CMMS serves as the conductor, orchestrating tasks, schedules, and resources in a synchronized manner. By digitizing workflows and centralizing data, CMMS eliminates the chaos of paper trails and spreadsheets, ensuring that everyone is on the same page with real-time updates and notifications.
One of the key benefits of CMMS is preventive maintenance. Instead of waiting for equipment breakdowns to occur, which can lead to costly downtime, CMMS allows teams to schedule regular inspections and maintenance tasks based on usage data and manufacturer recommendations. This proactive approach not only extends the lifespan of equipment but also minimizes unexpected disruptions, keeping operations running like clockwork.
Furthermore, CMMS enhances accountability and transparency within your team. Each member can access task assignments, priorities, and deadlines through the system, fostering a sense of ownership and teamwork. Imagine a sports team where every player knows their position and plays their role seamlessly—CMMS ensures everyone is aligned towards the common goal of operational excellence.
In the fast-paced world of maintenance management, efficiency is the name of the game. CMMS provides actionable insights through robust reporting and analytics, allowing managers to identify bottlenecks, optimize workflows, and allocate resources more effectively. It’s like having a GPS for your maintenance operations, guiding you towards the most efficient route to success.
To sum it up, implementing effective CMMS strategies is not just about managing maintenance—it’s about empowering your team to work smarter, not harder. By leveraging technology to tackle challenges head-on, you pave the way for increased productivity, minimized downtime, and ultimately, happier stakeholders. So, buckle up and embrace the journey towards operational excellence with CMMS as your trusted navigator.
Frequently Asked Questions
How can CMMS software contribute to a safer work environment for maintenance teams
Learn how CMMS software enhances workplace safety for maintenance teams by streamlining maintenance processes, ensuring timely equipment inspections, and facilitating proactive maintenance scheduling.
What are the key ways CMMS boosts maintenance team morale
Discover how CMMS boosts maintenance team morale through streamlined workflow management, efficient task allocation, and proactive equipment maintenance scheduling.
Can CMMS help reduce downtime and enhance workflow efficiency
Learn how CMMS (Computerized Maintenance Management System) can effectively minimize downtime and optimize workflow efficiency.
Does implementing CMMS lead to better resource allocation and time management
Learn how implementing a Computerized Maintenance Management System (CMMS) can enhance resource allocation and time management efficiency.
How does CMMS software improve productivity for maintenance teams
Learn how CMMS software enhances productivity for maintenance teams by streamlining work orders, scheduling preventive maintenance, managing inventory efficiently, and providing real-time insights into equipment status and performance.