At its core, CMMS acts as a digital hub where maintenance tasks are orchestrated with precision. It’s not just about fixing things when they break; it’s about proactive management and optimization. From scheduling routine inspections to tracking inventory and managing work orders, CMMS streamlines operations with efficiency.
For a maintenance engineer, CMMS is like having a trusted assistant who never forgets a detail. It ensures that equipment inspections happen on time, reducing the risk of unexpected breakdowns that could disrupt production. By keeping a digital record of maintenance history, CMMS helps engineers track trends and make data-driven decisions to improve equipment reliability.
One of the standout features of CMMS is its ability to prioritize tasks intelligently. It categorizes maintenance activities based on urgency and importance, allowing engineers to focus on critical issues first. This not only saves time but also enhances workplace safety and prolongs equipment lifespan.
In the fast-paced world of maintenance, where every minute counts, CMMS provides clarity and control. It eliminates the chaos of paperwork and spreadsheets, replacing them with a user-friendly interface that anyone can navigate. This accessibility empowers engineers to collaborate seamlessly across teams, sharing insights and coordinating efforts effortlessly.
Ultimately, CMMS isn’t just a tool; it’s a transformational force in how maintenance is approached. By integrating technology into daily workflows, it frees up engineers to tackle more strategic challenges, driving productivity and innovation forward. As industries evolve, CMMS stands as a testament to the power of digital solutions in optimizing operational efficiency and ensuring that every task—from routine maintenance to emergency repairs—is handled with precision and care.
Revolutionizing Efficiency: CMMS Tools Transform Maintenance Engineer Workflows
Imagine a world where every task, no matter how complex, is streamlined and managed effortlessly. That’s the promise of CMMS (Computerized Maintenance Management System) tools, the unsung heroes of modern maintenance engineering. These systems aren’t just software; they’re the backbone of efficient operations, allowing maintenance teams to soar to new heights of productivity.
CMMS tools are designed to centralize and optimize every aspect of maintenance workflows. From scheduling routine inspections to tracking inventory and managing work orders, these systems do it all with finesse. They act as a digital command center, where maintenance engineers can monitor equipment health in real-time, foresee potential breakdowns, and preemptively tackle issues before they disrupt operations.
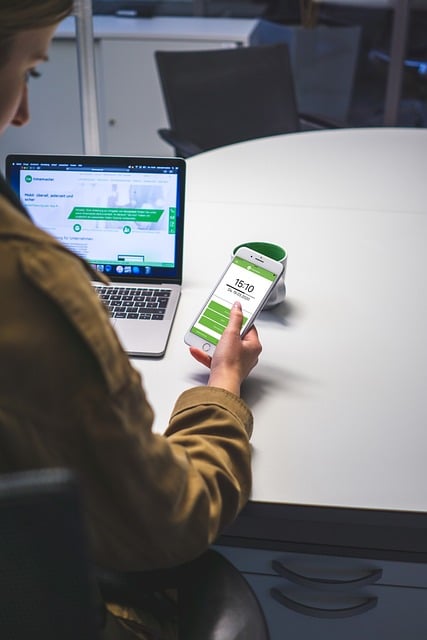
One of the most transformative features of CMMS tools is their ability to automate repetitive tasks. Imagine no longer having to manually update maintenance logs or schedule routine checks. With CMMS, these tasks are handled seamlessly, freeing up valuable time for engineers to focus on more critical aspects of their job. This automation doesn’t just save time; it reduces human error, ensuring that maintenance activities are performed with precision and consistency.
Moreover, CMMS tools are not just about efficiency; they’re about foresight. By analyzing historical data and maintenance trends, these systems can predict when equipment might require servicing or replacement. This predictive maintenance approach minimizes downtime and extends the lifespan of assets, ultimately saving organizations significant costs in repairs and replacements.
In a nutshell, CMMS tools are like having a supercharged assistant for every maintenance engineer. They simplify the complex, automate the mundane, and empower teams to operate at peak efficiency. Whether it’s a small manufacturing plant or a sprawling industrial complex, CMMS tools revolutionize how maintenance tasks are managed, ensuring smoother operations and happier engineers.
From Chaos to Control: CMMS Software’s Role in Streamlining Daily Tasks
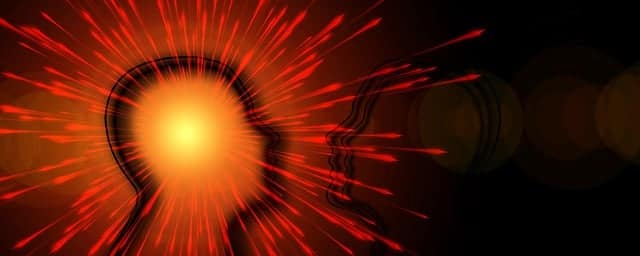
Imagine a busy factory floor buzzing with activity—machines humming, workers bustling, and maintenance schedules overlapping. In such an environment, keeping track of every piece of equipment’s maintenance needs manually would be akin to juggling flaming torches. Enter CMMS software, the ultimate juggler of tasks. It acts as a centralized hub where maintenance schedules, work orders, spare parts inventory, and equipment history converge seamlessly.
One of the standout features of CMMS software is its ability to schedule preventive maintenance automatically. It’s like having a crystal ball that predicts when a machine might throw a wrench in your operations—before it actually does. By preemptively scheduling maintenance tasks based on equipment usage or predefined time intervals, CMMS software helps businesses avoid costly downtime and sudden breakdowns.
But it doesn’t stop there. CMMS software also simplifies work order management. Instead of scribbling work requests on scraps of paper or sending emails into the void, employees can submit and track work orders directly through the software. This streamlined process ensures that maintenance tasks are assigned promptly, completed efficiently, and documented thoroughly—all without the hassle of misplaced requests or communication delays.
Moreover, CMMS software isn’t just about maintaining machines; it’s about optimizing efficiency across the board. By analyzing historical maintenance data, businesses can identify trends, pinpoint recurring issues, and make data-driven decisions to improve overall operational efficiency. It’s like having a skilled detective who uncovers clues hidden in maintenance logs to solve the mystery of inefficiency.
In today’s fast-paced business landscape, where every minute counts and downtime is the ultimate enemy, CMMS software stands as a beacon of efficiency. It empowers businesses to transform chaos into control, ensuring that operations run smoothly, machines hum harmoniously, and productivity soars to new heights. Ready to take control of your daily tasks? CMMS software is your trusted co-pilot on this journey from chaos to seamless operations.
Unlocking Productivity: How CMMS Enhances Maintenance Engineer Operations
Imagine a well-oiled machine humming along seamlessly day in and day out. That’s the goal of every maintenance engineer striving to keep operations running smoothly. But behind the scenes, it’s not just wrenches and grease; it’s about leveraging the right tools to maximize efficiency. One such tool gaining prominence is the Computerized Maintenance Management System (CMMS).
CMMS isn’t just another acronym in the sea of tech jargon. It’s a game-changer for maintenance engineers, revolutionizing how they oversee and execute maintenance tasks. Think of it as a digital brain that organizes, schedules, and tracks maintenance activities with precision. From preventive maintenance to reactive repairs, CMMS streamlines workflows, ensuring downtime is minimized and productivity soars.
How exactly does CMMS elevate the role of maintenance engineers? Picture this: instead of sifting through piles of paperwork or relying on memory, engineers can access a centralized database at their fingertips. They can instantly pull up equipment histories, maintenance schedules, and even troubleshoot issues on the go. It’s like having a supercharged toolbox that not only fixes problems but predicts and prevents them before they arise.
But CMMS isn’t just about data crunching; it’s about empowerment. By automating routine tasks and generating insightful reports, engineers can focus more on strategic initiatives. They become proactive problem solvers rather than reactive firefighters, driving operational efficiency and cost savings across the board.
In today’s fast-paced industrial landscape, downtime is not just a hiccup—it’s a costly setback. CMMS helps mitigate this risk by fostering a proactive maintenance culture. It’s the difference between waiting for equipment to break down and anticipating issues before they impact production. This predictive prowess isn’t just about saving time and money; it’s about safeguarding the reliability and longevity of critical assets.
Data-Driven Maintenance: The CMMS Advantage in Modern Workflow Management
Imagine your business operations as a well-oiled machine. Every part needs to function smoothly to maximize productivity and minimize downtime. CMMS acts as the central nervous system, providing real-time data insights that empower maintenance teams to make informed decisions promptly.
Unlike traditional maintenance approaches that rely on fixed schedules or reactive repairs, CMMS leverages data analytics to predict equipment failures before they occur. By monitoring key performance indicators (KPIs) such as equipment usage, downtime trends, and maintenance costs, CMMS enables proactive maintenance strategies. This predictive capability not only reduces unexpected breakdowns but also optimizes asset lifespan and operational efficiency.
Moreover, CMMS enhances workflow management by streamlining work orders and scheduling. Maintenance tasks are prioritized based on urgency and criticality, ensuring resources are allocated efficiently. Whether it’s scheduling routine inspections or coordinating complex repairs, CMMS ensures tasks are completed on time and within budget.
Furthermore, CMMS facilitates regulatory compliance by maintaining comprehensive records of maintenance activities and equipment history. This audit trail not only simplifies inspections but also mitigates risks associated with non-compliance.
In essence, adopting a data-driven approach through CMMS transforms maintenance from a cost center into a strategic asset. It empowers organizations to achieve higher equipment reliability, reduce operational costs, and ultimately, deliver superior service to customers.
In the dynamic landscape of modern industry, where every minute counts, CMMS isn’t just an advantage—it’s a necessity for businesses aiming to stay ahead of the curve. Ready to optimize your workflow with data-driven maintenance? Let CMMS pave the way to efficiency and excellence in your operations.
Optimizing Uptime: CMMS Solutions and Their Impact on Maintenance Engineers
Imagine a scenario where every machine and equipment in a factory operates at peak performance without interruptions. This is the promise of CMMS solutions. By centralizing maintenance data, scheduling preventive maintenance tasks, and facilitating real-time monitoring, CMMS empowers engineers to proactively manage maintenance activities. It shifts the paradigm from reactive to proactive maintenance, thereby preventing costly breakdowns and unplanned downtime.
One of the key impacts of CMMS is its ability to optimize resource allocation. Maintenance engineers can efficiently allocate manpower, materials, and equipment based on real-time data insights provided by the CMMS platform. This not only improves operational efficiency but also reduces operational costs associated with over-maintenance or emergency repairs.
Furthermore, CMMS solutions foster collaboration across different departments within an organization. By providing a centralized platform for communication and data sharing, these systems break down silos and enable seamless coordination between maintenance teams, production departments, and management. This collaborative approach ensures that everyone is aligned towards the common goal of maximizing uptime and productivity.
In essence, CMMS solutions are more than just tools for maintenance management; they are catalysts for operational excellence. They empower maintenance engineers with the tools and insights needed to keep critical assets running smoothly. As industries continue to digitize and prioritize efficiency, the role of CMMS in optimizing uptime and reducing maintenance costs becomes increasingly indispensable.
The Digital Shift: CMMS and Its Influence on Daily Maintenance Practices
Imagine having a virtual assistant dedicated solely to ensuring that every piece of equipment in your facility operates at peak efficiency. That’s precisely what CMMS systems do. They revolutionize maintenance by automating routine tasks, from scheduling preventive maintenance to managing work orders and tracking inventory. This automation not only saves time but also minimizes downtime by preemptively addressing potential issues before they escalate.
One of the standout features of CMMS is its ability to provide real-time data insights. By capturing and analyzing maintenance data, these systems empower decision-makers to make informed choices swiftly. It’s like having a crystal ball that predicts when equipment might need servicing, allowing maintenance teams to stay proactive rather than reactive.
Furthermore, CMMS solutions are versatile, catering to a wide range of industries, including manufacturing, healthcare, hospitality, and beyond. Whether you’re overseeing a factory floor or maintaining critical medical equipment, CMMS adapts to your specific needs, ensuring compliance, efficiency, and cost-effectiveness.
In essence, the digital shift enabled by CMMS isn’t just about embracing technology; it’s about optimizing operations and maximizing productivity. It transforms how maintenance practices are approached, offering a seamless blend of automation and human expertise. As industries continue to evolve, CMMS stands as a testament to innovation, shaping the future of maintenance management with its unparalleled efficiency and reliability.
Frequently Asked Questions
What role does CMMS play in preventive maintenance scheduling?
Learn about the crucial role CMMS plays in preventive maintenance scheduling, ensuring timely inspections, maintenance tasks, and equipment upkeep to prevent breakdowns and extend asset lifespan.
How does CMMS streamline work order management for maintenance engineers?
Learn how CMMS (Computerized Maintenance Management System) optimizes work order management for maintenance engineers, ensuring efficient task allocation, tracking, and reporting to enhance operational productivity.
How can CMMS improve asset tracking and management?
Discover how CMMS enhances asset tracking and management efficiency, optimizing maintenance schedules, reducing downtime, and ensuring asset reliability.
What are the advantages of real-time data access through CMMS for maintenance engineers?
Real-time data access through CMMS (Computerized Maintenance Management System) offers maintenance engineers advantages such as immediate visibility into equipment status, quicker response times to issues, proactive maintenance scheduling, and enhanced decision-making based on up-to-date information.
What are the key benefits of using CMMS for maintenance engineers?
Learn about the key benefits of using CMMS (Computerized Maintenance Management System) for maintenance engineers, including improved asset reliability, streamlined maintenance workflows, better inventory management, enhanced regulatory compliance, and optimized maintenance scheduling.