Ever wondered how operations managers can take teamwork to the next level? Enter CMMS, the unsung hero of collaboration in modern workplaces. CMMS, or Computerized Maintenance Management System, isn’t just about fixing machinery; it’s a powerhouse tool that can revolutionize how teams work together.
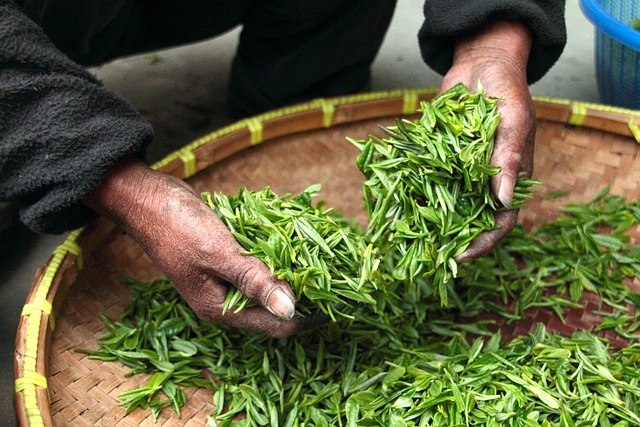
Imagine this: your maintenance crew, your scheduling team, and your inventory management all seamlessly synced up like a well-choreographed dance. That’s the magic of CMMS. By centralizing all maintenance-related activities into one digital platform, CMMS becomes the hub where every team member can access real-time data, track progress, and communicate effortlessly.
Think of it as your team’s command center, where every operation, from routine maintenance tasks to urgent repairs, is managed with precision and clarity. No more confusion over who’s doing what or when the next maintenance check is due. With CMMS, everything is laid out in a user-friendly interface, ensuring that everyone stays on the same page.
But how exactly does CMMS enhance collaboration? Well, picture this: you’re in charge of a manufacturing plant. Your engineers need to schedule equipment inspections, your procurement team needs to order spare parts, and your finance department needs cost reports. Without CMMS, coordinating all these tasks could be a logistical nightmare.
CMMS streamlines communication by providing a centralized platform where every team member can input data, update statuses, and leave notes for others to see. It’s like having a virtual whiteboard where everyone can contribute, ensuring that crucial information isn’t lost in a flurry of emails or post-it notes.
Moreover, CMMS doesn’t just improve internal communication; it also fosters a culture of accountability and efficiency. When every task is logged into the system, it’s easier to track progress, identify bottlenecks, and allocate resources where they’re needed most. This transparency not only speeds up decision-making but also empowers team members to take ownership of their roles.
In essence, CMMS isn’t just a tool for operations managers; it’s a game-changer for the entire team. By leveraging its capabilities, managers can ensure smoother workflows, fewer breakdowns in communication, and ultimately, happier and more productive teams.
Ready to take your team collaboration to new heights? Consider integrating CMMS into your operations and watch as efficiency and teamwork soar.
Streamlining Efficiency: Harnessing CMMS for Seamless Team Collaboration
In today’s fast-paced work environment, efficiency is not just a goal but a necessity. Companies are constantly seeking ways to streamline processes and improve collaboration among teams. One powerful tool that has emerged to address these needs is Computerized Maintenance Management Systems (CMMS). These systems are no longer just about managing maintenance tasks; they have evolved into comprehensive platforms that enhance overall operational efficiency.
CMMS platforms facilitate seamless team collaboration by centralizing communication, task management, and resource allocation. Imagine a digital hub where every team member can access real-time updates, assign tasks, and track progress effortlessly. This centralized approach eliminates the chaos of scattered emails and manual updates, ensuring everyone is on the same page.
Moreover, CMMS systems offer robust features like scheduling preventive maintenance, inventory management, and detailed analytics. These functionalities not only optimize equipment uptime but also empower teams to work proactively rather than reactively. By identifying maintenance patterns and resource utilization trends, teams can allocate resources more effectively, reducing downtime and operational costs.
The impact of CMMS on team collaboration extends beyond operational efficiency. It fosters a culture of accountability and transparency. When tasks are clearly defined and tracked within the system, team members feel more accountable for their contributions. This accountability breeds trust and cohesion among team members, leading to smoother workflows and higher productivity levels.
Boosting Productivity: CMMS Strategies for Operations Teams to Collaborate Effectively
Imagine CMMS as the conductor of a symphony orchestra, harmonizing the efforts of maintenance, production, and logistics teams. It centralizes maintenance activities, asset tracking, and work order management into a single digital platform. This integration allows operations teams to synchronize their tasks effortlessly, ensuring minimal downtime and optimal resource utilization.
By implementing CMMS, operations teams can bid farewell to the chaos of manual processes and spreadsheets. Instead, they gain access to real-time data and insights that empower proactive decision-making. For instance, maintenance technicians can promptly respond to equipment breakdowns with predefined workflows, while supervisors monitor progress in real-time.
Moreover, CMMS facilitates collaboration beyond physical boundaries. Remote teams can access the same database, update work statuses, and communicate seamlessly. This capability is akin to a well-coordinated relay race, where each team member passes the baton smoothly, ensuring the race – or project – moves forward without interruptions.
In essence, CMMS strategies transform operations teams into a cohesive unit, where each member understands their role in achieving overarching productivity goals. It’s like equipping a team of explorers with state-of-the-art navigation tools – they can navigate through challenges efficiently, knowing they have the support and data they need at their fingertips.
From Data to Action: Leveraging CMMS Tools for Improved Team Synergy
In today’s fast-paced business environment, achieving seamless teamwork is crucial for success. One powerful way companies are enhancing team synergy is through Computerized Maintenance Management Systems (CMMS). These tools aren’t just about managing maintenance schedules anymore—they’re transforming how teams collaborate and perform.
CMMS tools streamline data collection, allowing teams to capture and analyze maintenance data in real-time. This data isn’t just numbers; it’s actionable insights waiting to be harnessed. Imagine having a dashboard that highlights equipment performance trends or identifies recurring issues before they escalate. It’s like having a crystal ball for maintenance efficiency.
By leveraging CMMS tools, teams can break down silos and foster better communication. For instance, technicians can update work orders instantly from the field, while managers track progress in real-time. This seamless flow of information ensures everyone is on the same page, reducing downtime and boosting productivity.
Moreover, CMMS tools empower proactive decision-making. Instead of reacting to breakdowns, teams can preemptively schedule maintenance based on data-driven predictions. It’s akin to maintaining a car regularly to avoid unexpected breakdowns—a small investment in proactive maintenance saves substantial costs in the long run.
In essence, CMMS tools are not just about managing assets; they’re about transforming data into actionable insights that drive team synergy. They enable teams to collaborate more effectively, make informed decisions, and ultimately, achieve operational excellence. Embracing CMMS isn’t just a trend—it’s a strategic move towards efficiency, reliability, and team cohesion.
Mastering Collaboration: CMMS Best Practices for Operations Managers
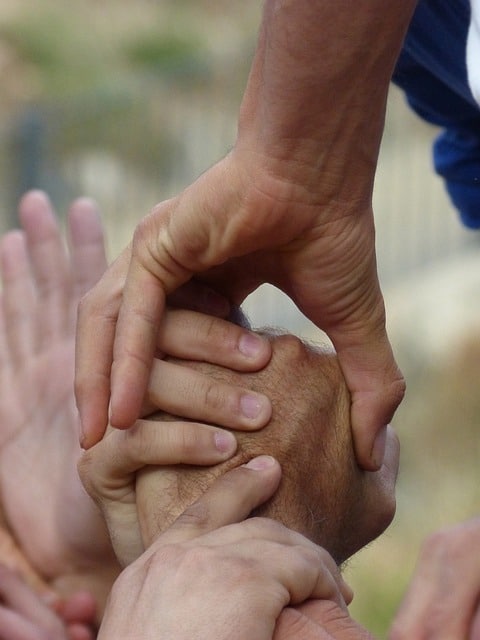
Effective collaboration is the cornerstone of successful operations management, especially when leveraging CMMS (Computerized Maintenance Management System) tools. These systems streamline workflows, enhance communication, and ensure optimal asset management. For operations managers, mastering collaboration through CMMS involves several best practices that maximize efficiency and minimize downtime.
Firstly, clear communication is key. CMMS platforms centralize data, allowing team members to access real-time information on maintenance schedules, equipment status, and work orders. This transparency fosters better communication among team members, enabling them to coordinate tasks effectively and resolve issues promptly.
Secondly, proactive maintenance planning plays a crucial role. By utilizing CMMS data analytics and predictive maintenance features, operations managers can anticipate equipment failures before they occur. This proactive approach not only reduces unexpected downtime but also extends the lifespan of critical assets, ultimately lowering maintenance costs.
Moreover, leveraging mobile accessibility enhances collaboration flexibility. Modern CMMS solutions offer mobile apps that empower field technicians and managers to access data, update work orders, and communicate seamlessly from anywhere. This mobility ensures that teams remain connected and informed, regardless of their location, promoting swift decision-making and problem-solving.
Furthermore, integrating CMMS with other business systems amplifies collaboration effectiveness. By syncing with ERP (Enterprise Resource Planning) and SCADA (Supervisory Control and Data Acquisition) systems, operations managers gain comprehensive insights into overall business operations. This integration streamlines data sharing across departments, aligns organizational goals, and improves cross-functional collaboration.
Additionally, continuous training and support are vital. Operations managers should invest in ongoing CMMS training for their teams to ensure proficiency in system usage and maximize its potential. Regular updates and technical support also guarantee that the CMMS functions optimally, addressing any issues promptly to maintain operational continuity.
Mastering collaboration through CMMS best practices empowers operations managers to orchestrate efficient maintenance workflows, enhance team synergy, and optimize asset performance. By embracing these strategies, organizations can achieve operational excellence, minimize costs, and deliver superior service to stakeholders.
Empowering Teams: Transforming Collaboration with CMMS Integration
Imagine a scenario where every team member, from maintenance technicians to project managers, is seamlessly connected through a centralized CMMS platform. Tasks are assigned and tracked in real-time, updates are instant, and everyone stays on the same page effortlessly. This level of integration isn’t just about convenience; it’s about revolutionizing the way teams collaborate.
By integrating CMMS into daily operations, organizations can streamline workflows and eliminate the bottlenecks that often hinder productivity. Maintenance teams can schedule tasks more effectively, anticipate equipment needs, and proactively address issues before they escalate. Project teams can coordinate resources, track progress, and ensure that deadlines are met with precision.
But it’s not just about efficiency; CMMS integration fosters a culture of accountability and transparency within teams. With clear visibility into tasks and responsibilities, team members are empowered to take ownership of their work and contribute meaningfully to the collective goals of the organization. This empowerment leads to higher morale, improved job satisfaction, and ultimately, better business outcomes.
In essence, CMMS integration isn’t just a technological upgrade—it’s a catalyst for organizational transformation. It breaks down silos, enhances communication, and enables teams to collaborate like never before. As businesses continue to evolve in an increasingly digital landscape, embracing CMMS integration isn’t just an option—it’s a strategic imperative for staying competitive and driving growth in the modern era.
Frequently Asked Questions
What features should operations managers look for in CMMS systems to boost team collaboration?
Discover essential features for operations managers to enhance team collaboration with CMMS systems. Learn how to streamline communication, facilitate task assignment, ensure real-time updates, and integrate easily with existing tools.
What are the benefits of integrating CMMS with other collaboration tools for operations teams?
Learn about the advantages of combining CMMS with collaboration tools for operational teams. Discover how this integration enhances efficiency, streamlines communication, and boosts productivity by synchronizing maintenance tasks with team workflows.
What is CMMS and how does it improve team collaboration for operations managers?
Learn how CMMS (Computerized Maintenance Management System) enhances team collaboration for operations managers by streamlining maintenance tasks, centralizing data, and facilitating real-time communication among team members. Discover how this tool boosts efficiency, reduces downtime, and ensures smoother operations management.
How can CMMS software streamline communication among team members?
Learn how CMMS software enhances team communication by centralizing data, enabling real-time updates, assigning tasks efficiently, and facilitating seamless collaboration.
How does CMMS help in tracking team tasks and improving productivity?
Learn how CMMS (Computerized Maintenance Management System) enhances productivity by efficiently tracking team tasks. Discover its role in streamlining workflows, scheduling maintenance, and ensuring timely task completion, ultimately optimizing team performance.