These systems serve as a centralized hub for managing maintenance activities, equipment inspections, and safety procedures. By integrating CMMS into daily operations, hazardous industries can proactively monitor equipment health, schedule regular inspections, and promptly address potential safety hazards. This proactive approach minimizes downtime due to unexpected equipment failures and reduces the likelihood of accidents caused by faulty machinery.
Moreover, CMMS software provides real-time data on equipment performance and maintenance histories. This data empowers safety managers to make informed decisions regarding equipment repairs and replacements, ensuring that all machinery meets stringent safety standards. By leveraging historical maintenance data, industries can identify recurring issues, implement preventive measures, and continuously improve safety protocols.
In essence, CMMS enhances safety in hazardous industries by promoting proactive maintenance practices, reducing equipment downtime, and optimizing safety inspections. It acts as a digital guardian, constantly monitoring equipment health and alerting maintenance teams to potential risks before they escalate. By integrating CMMS into their operations, industries not only prioritize safety but also enhance operational efficiency and regulatory compliance.
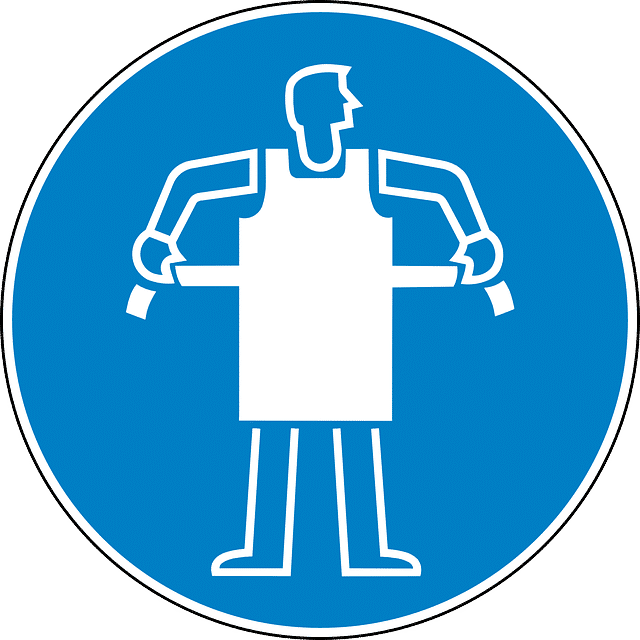
For hazardous industries, embracing CMMS technology isn’t just about compliance—it’s about fostering a culture of safety where every worker can operate confidently, knowing that their environment is diligently monitored and maintained. As these industries navigate complex operational challenges, CMMS stands as a reliable ally in safeguarding both personnel and productivity, ensuring a safer workplace for all.
Revolutionizing Safety: CMMS Integration Redefines Hazardous Industry Protocols
Picture this: a bustling factory floor, where machines hum with precision, and workers navigate with confidence. CMMS acts as the conductor in this symphony of operations, orchestrating maintenance schedules, tracking equipment health, and alerting teams to potential hazards before they escalate. It’s like having a vigilant sentinel that never sleeps, always vigilant for signs of trouble and proactively addressing them.
But how does CMMS achieve this feat? By centralizing data and streamlining communication, it ensures that critical information flows effortlessly between departments. Maintenance crews receive instant notifications of faulty equipment, while supervisors access comprehensive analytics to make informed decisions swiftly. It’s akin to having a crystal ball that predicts maintenance needs before breakdowns occur, thus averting potential disasters.
Moreover, CMMS integration democratizes safety knowledge across the organization. No longer is safety confined to manuals and sporadic training sessions; it becomes ingrained in everyday operations. Technicians become empowered with real-time insights, enabling them to perform preventive maintenance with surgical precision. It’s like arming every worker with a shield against unforeseen dangers, fostering a culture where safety isn’t just a priority but a way of life.
In essence, CMMS integration redefines hazardous industry protocols by bridging the gap between reactive and proactive safety measures. It transforms workplaces into safer environments where risks are minimized, productivity soars, and peace of mind prevails. As industries evolve, embracing CMMS isn’t just an option; it’s a necessity to stay ahead of the curve and ensure that safety remains the cornerstone of operational excellence.
Harnessing Technology: CMMS as the Cornerstone of Safety in Hazardous Environments
CMMS operates like a digital guardian, keeping an eagle eye on equipment maintenance schedules, alerting teams well in advance of any potential issues. It’s like having a proactive assistant who never sleeps, always ready to prevent malfunctions before they even think of occurring. This preemptive approach not only saves time but can be a literal lifesaver in hazardous conditions where a breakdown could mean disaster.
But how does CMMS enhance safety beyond maintenance reminders? Picture this: in a bustling factory with heavy machinery, there’s always a risk of wear and tear going unnoticed. CMMS steps in with its ability to analyze data trends, predicting when a part might need replacement before it gives out unexpectedly. It’s akin to predicting the weather—anticipating storms before they hit rather than dealing with the aftermath.
Moreover, CMMS doesn’t just stop at equipment upkeep. It plays a pivotal role in compliance too, ensuring that all safety regulations are met without fail. In hazardous environments where regulatory adherence can make or break operations, having a robust system that automatically documents every maintenance action and inspection is invaluable. It’s like having a meticulous secretary who keeps flawless records, ready to present at a moment’s notice.
In essence, CMMS isn’t just a tool; it’s a cornerstone of safety in hazardous environments. It integrates seamlessly into daily operations, empowering teams to focus on their tasks with confidence, knowing that behind the scenes, technology is tirelessly working to keep everyone safe. As industries evolve and hazards persist, embracing CMMS isn’t just a choice—it’s a necessity to safeguard both people and productivity in an increasingly complex world.
Smart Solutions: How CMMS Innovations Are Bolstering Safety Standards
Imagine a workplace where every piece of equipment, from complex machinery to HVAC systems, is meticulously monitored and maintained with precision. CMMS platforms are the backbone of such efficiency. They allow maintenance teams to schedule preventive maintenance tasks proactively, ensuring that equipment operates at optimal levels, thereby reducing the risk of unexpected failures that could compromise safety.
One of the key features of CMMS innovations lies in their ability to centralize data. By digitizing maintenance records and integrating them into a single platform, these systems enable easy access to historical data and performance metrics. This data-driven approach empowers decision-makers with insights into equipment health trends and maintenance patterns, facilitating informed decisions that prioritize safety.
Moreover, CMMS solutions are increasingly incorporating predictive maintenance capabilities. Through the use of sensors and IoT (Internet of Things) technology, these systems can now forecast equipment failures before they occur. This proactive approach not only minimizes downtime but also mitigates safety hazards associated with malfunctioning equipment.
In industries where compliance with stringent safety regulations is paramount, CMMS innovations provide a structured framework for ensuring regulatory adherence. By automating compliance checks and audit trails, these systems help organizations maintain safety protocols consistently, reducing the risk of non-compliance penalties and workplace incidents.
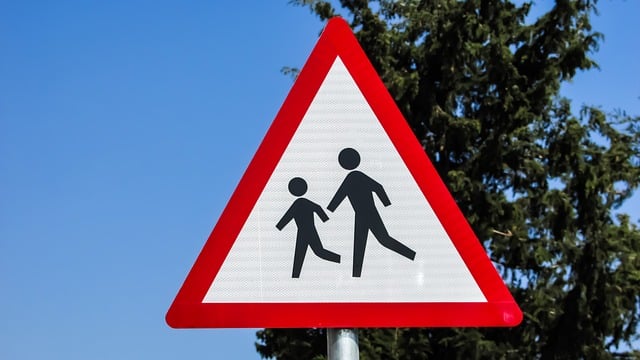
Overall, CMMS innovations represent a paradigm shift towards smarter, safer workplaces. They empower maintenance teams to work proactively, anticipate challenges, and uphold the highest safety standards. As industries continue to embrace digital transformation, the role of CMMS in bolstering safety will only become more pronounced, safeguarding both workers and operational continuity alike.
From Risk to Resilience: CMMS Strategies for Hazard Mitigation
Imagine your facility as a ship sailing through unpredictable waters. Just as a skilled captain relies on navigation tools to steer clear of reefs and storms, a robust CMMS acts as your compass in risk management. It empowers organizations to proactively identify potential hazards, whether it’s equipment failures, regulatory compliance issues, or environmental risks. By maintaining a comprehensive database of assets, work orders, and maintenance histories, CMMS enables quick responses and informed decision-making.
The heart of CMMS lies in preventive maintenance. Like regular check-ups for your car to prevent breakdowns, scheduled inspections and maintenance tasks prescribed by CMMS preemptively address vulnerabilities before they escalate into crises. This proactive approach not only minimizes downtime but also safeguards personnel and assets from avoidable risks.
Moreover, CMMS transforms data into actionable insights. It tracks key performance indicators (KPIs) and generates real-time reports, allowing managers to detect trends, streamline workflows, and allocate resources efficiently. By harnessing predictive analytics, CMMS goes beyond reactive measures, predicting potential hazards based on historical data and enabling preemptive interventions.
In essence, adopting CMMS strategies shifts the focus from mere hazard management to holistic resilience-building. It cultivates a culture where safety is ingrained into daily operations, empowering teams to anticipate, adapt, and thrive in the face of challenges. As industries evolve and risks evolve with them, CMMS remains a steadfast ally, navigating organizations from risk mitigation to resilience with precision and foresight.
Next-Gen Safety: CMMS Applications Transforming Hazardous Industry Operations
Imagine a world where safety is not just a goal but a reality woven into the fabric of everyday operations. CMMS applications are leading this charge by seamlessly integrating maintenance, safety protocols, and operational efficiency into a unified platform. This isn’t just about mitigating risks; it’s about proactive management that anticipates and prevents potential hazards before they arise.
But what exactly makes CMMS a game-changer in hazardous industries? Let’s break it down. Picture a meticulous conductor orchestrating a symphony – except here, the orchestra is a complex industrial environment, and the conductor is CMMS, harmonizing safety measures with operational excellence.
CMMS empowers industries to schedule and track maintenance tasks with precision, ensuring that critical equipment operates at peak performance levels. This proactive maintenance approach minimizes the likelihood of equipment failures that could lead to hazardous situations. Think of it as conducting regular health check-ups for machinery – detecting and addressing issues before they escalate into something more severe.
Furthermore, CMMS doesn’t just stop at maintenance. It acts as a digital sentinel, constantly monitoring safety protocols and regulatory compliance. It provides real-time insights and analytics, allowing decision-makers to identify trends, analyze risks, and implement proactive measures swiftly. It’s akin to having a vigilant guardian that never sleeps, always alert to potential dangers and ready to intervene.
In hazardous industries where every second counts, having this level of foresight and control is not just beneficial; it’s essential. CMMS applications are not merely tools; they are transformative agents shaping the future of industrial safety. They empower organizations to foster a culture where safety isn’t just a priority but an ingrained value, ensuring that workers return home safely every day.
Frequently Asked Questions
What Features Should I Look for When Choosing a CMMS for Enhancing Safety in Hazardous Industries
Choosing a CMMS (Computerized Maintenance Management System) for enhancing safety in hazardous industries requires prioritizing features like robust risk assessment tools, real-time monitoring capabilities, integration with safety protocols, audit trail functionalities, and comprehensive reporting. These features ensure proactive maintenance planning, timely hazard identification, and compliance with safety standards, ultimately reducing risks and enhancing workplace safety.
What Role Does Preventive Maintenance Play in CMMS for Hazardous Industry Safety
Learn about the crucial role of preventive maintenance in CMMS for ensuring safety in hazardous industries. Discover how proactive maintenance schedules and inspections help mitigate risks, ensure equipment reliability, and maintain regulatory compliance.
What are the Key Benefits of Using CMMS for Safety in Hazardous Industries
Discover the key benefits of using CMMS (Computerized Maintenance Management System) for enhancing safety in hazardous industries. Learn how CMMS helps streamline maintenance tasks, ensures regulatory compliance, minimizes downtime, and improves overall safety protocols.
How Does CMMS Improve Compliance with Safety Regulations in Hazardous Environments
Learn how CMMS enhances safety compliance in hazardous environments by streamlining maintenance schedules, tracking equipment inspections, and ensuring timely repairs to meet regulatory standards.
How Can CMMS Help in Incident Management and Emergency Response
Learn how CMMS (Computerized Maintenance Management System) aids in incident management and emergency response by facilitating quick access to asset information, tracking maintenance history for rapid troubleshooting, and ensuring timely repairs to minimize downtime and enhance safety.