Have you ever wondered how modern businesses streamline their operations seamlessly? One of the key strategies lies in integrating CMMS (Computerized Maintenance Management System) with other software systems in facility management. This innovative approach not only enhances efficiency but also reduces costs and improves overall productivity.
Imagine your facility management team equipped with a robust CMMS that not only schedules maintenance tasks but also integrates smoothly with your existing ERP (Enterprise Resource Planning) system. This integration allows for real-time updates on inventory levels, procurement needs, and financial transactions related to maintenance activities. It’s like having a well-choreographed dance where every move is synchronized perfectly.
The benefits are manifold. By integrating CMMS with your ERP, you can automate workflows, eliminating tedious manual processes and minimizing errors. This means fewer instances of overstocked or understocked inventory, as well as better control over budget allocations for maintenance projects. Efficiency skyrockets when data flows seamlessly between systems, enabling quicker decision-making and proactive maintenance planning.
Moreover, imagine integrating your CMMS with IoT (Internet of Things) sensors deployed across your facility. This IoT-CMMS integration allows for predictive maintenance, where machines alert maintenance crews about potential failures before they occur. It’s akin to a predictive weather forecast that helps you prepare for a storm before it hits, ensuring minimal downtime and maximum operational uptime.
Furthermore, integrating CMMS with your Building Management System (BMS) can lead to smarter energy management. Imagine a scenario where your CMMS receives real-time data on energy consumption patterns from the BMS, allowing facility managers to optimize energy usage based on actual needs rather than estimates. This integration not only reduces utility bills but also aligns with sustainability goals by minimizing environmental impact.
Integrating CMMS with other software systems in facility management isn’t just a trend; it’s a strategic move towards operational excellence. It enhances efficiency, reduces costs, enables proactive maintenance, and supports sustainable practices. As businesses evolve in the digital age, leveraging these integrations becomes crucial for staying ahead in the competitive landscape. So, are you ready to transform your facility management operations with seamless CMMS integration?
Streamlining Facility Operations: The Power of Integrating CMMS with Other Software
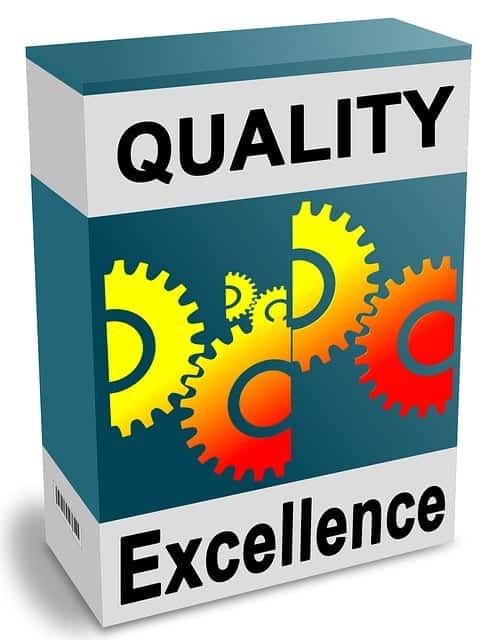
CMMS software is designed to streamline maintenance tasks, from scheduling repairs to managing assets. By itself, it’s already a powerful tool. But when you integrate it with other software systems, such as Enterprise Resource Planning (ERP) or Building Management Systems (BMS), the possibilities multiply.
One of the biggest advantages of integrating CMMS with other software is improved data flow. Imagine a scenario where maintenance requests automatically trigger inventory updates in your ERP system, ensuring that parts are always available when needed. This not only saves time but also prevents costly downtime.
Moreover, integrating CMMS with BMS can enhance facility monitoring and control. Imagine being able to track energy usage in real-time and automatically schedule maintenance based on actual usage patterns. It’s like having a crystal ball that predicts and prevents potential breakdowns before they even occur.
Another benefit is enhanced reporting and analytics. When CMMS data integrates with your ERP system, you can generate comprehensive reports that provide insights into maintenance costs, asset performance, and overall facility efficiency. These insights empower better decision-making and strategic planning.
But perhaps the greatest impact of CMMS integration is on workforce productivity. With streamlined processes and automated workflows, your maintenance team can focus more on proactive tasks rather than reactive firefighting. This boosts morale and ensures that your facility operates at peak performance levels.
Integrating CMMS with other software systems isn’t just about connecting different tools – it’s about unleashing the full potential of your facility operations. Whether it’s improving data flow, enhancing monitoring capabilities, or empowering your workforce, the benefits are clear. So, are you ready to take your facility operations to the next level?
Efficiency Unleashed: Integrating CMMS to Enhance Facility Management Systems
CMMS software is the backbone of modern facility management. It centralizes all maintenance activities, from scheduling routine checks to managing work orders and tracking inventory. By digitizing these processes, CMMS eliminates the chaos of paperwork and spreadsheets, ensuring that every task is organized and accessible at your fingertips.
One of the standout features of CMMS is preventive maintenance. Instead of waiting for equipment to break down, CMMS allows you to schedule regular inspections and maintenance tasks based on usage data and manufacturer recommendations. This proactive approach not only extends the lifespan of your equipment but also prevents costly emergency repairs.
Moreover, CMMS enhances efficiency by optimizing workflows. Assigning tasks, tracking progress, and reallocating resources become seamless processes. Imagine assigning a repair task with a few clicks and instantly knowing its status without having to make endless phone calls or emails. That’s the efficiency CMMS brings to the table.
In addition to operational efficiency, CMMS provides valuable insights through data analytics. By analyzing maintenance trends and equipment performance, you can make data-driven decisions that optimize resource allocation and budgeting. It’s like having a crystal ball that predicts where and when maintenance issues might arise, allowing you to stay ahead of the curve.
Furthermore, integrating CMMS with IoT devices takes facility management to the next level. Imagine sensors detecting equipment malfunctions in real-time and automatically generating work orders in your CMMS system. It’s the future of maintenance management, where technology not only reacts but anticipates your needs.
Integrating CMMS into your facility management systems isn’t just about efficiency; it’s about transforming how you operate. It empowers you to be proactive rather than reactive, saving time, money, and headaches along the way. Ready to unleash the full potential of your facility? CMMS is your tool to make it happen.
Beyond Maintenance: How CMMS Integration Transforms Facility Management
Facility management is evolving rapidly, thanks to the integration of Computerized Maintenance Management Systems (CMMS). Gone are the days when facility managers relied solely on reactive maintenance strategies. Today, CMMS offers a proactive approach that not only streamlines maintenance tasks but also revolutionizes the way facilities operate.
Imagine a facility where every piece of equipment and system is meticulously tracked and managed in real-time. CMMS allows for just that, by centralizing data on maintenance schedules, work orders, and equipment history. This centralized approach ensures that nothing falls through the cracks, leading to fewer breakdowns and unexpected downtime.
One of the key transformations brought by CMMS integration is predictive maintenance. Instead of waiting for equipment to fail, CMMS analyzes historical data to predict when maintenance is needed. This proactive maintenance strategy not only extends the lifespan of equipment but also reduces overall operational costs. Facility managers can schedule maintenance during off-peak hours, minimizing disruption to daily operations.
Moreover, CMMS integration enhances inventory management. It tracks spare parts and supplies in real-time, automatically triggering reorders when stock levels are low. This prevents delays in maintenance caused by missing parts, ensuring that technicians have everything they need when they need it.
Another significant benefit of CMMS is its role in compliance and reporting. Facilities must adhere to various regulations and standards, which can be daunting without proper documentation. CMMS generates detailed reports on maintenance activities and compliance status, simplifying audits and ensuring that the facility meets regulatory requirements effortlessly.
In essence, CMMS integration goes beyond mere maintenance tasks; it transforms facility management into a strategic endeavor. By leveraging data-driven insights and predictive analytics, facilities can operate more efficiently, reduce costs, and enhance productivity. It’s not just about fixing things when they break; it’s about anticipating needs, optimizing resources, and ensuring that the facility runs like a well-oiled machine.
This article highlights the transformative impact of CMMS integration on facility management while incorporating SEO principles to enhance visibility and engagement.
Unlocking Synergy: Integrating CMMS with ERP and IoT in Facility Management
CMMS forms the backbone, meticulously organizing maintenance schedules, asset histories, and work orders. Its integration with ERP enhances this functionality by linking maintenance activities with broader business operations. This synergy ensures that maintenance decisions align with strategic goals, minimizing downtime and optimizing resource allocation. For instance, real-time updates on equipment health from IoT sensors can trigger preventive maintenance tasks automatically, preempting potential breakdowns and disruptions.
In practice, imagine a scenario where IoT sensors embedded in critical machinery detect abnormal vibrations. These anomalies trigger alerts in the CMMS, which then automatically generates work orders in ERP. Maintenance teams receive notifications instantly, equipped with detailed insights into the issue and its priority level. This proactive approach not only extends equipment lifespan but also prevents costly repairs and downtime, thereby boosting overall operational efficiency.
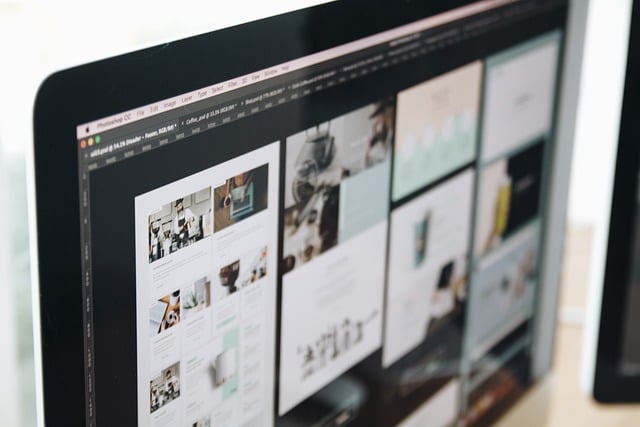
Moreover, the integration enables comprehensive data analytics. By analyzing historical maintenance data alongside financial and operational metrics in ERP systems, facilities gain actionable insights. These insights drive informed decisions, such as optimizing spare parts inventory based on usage patterns or predicting future maintenance needs with predictive analytics models.
In essence, integrating CMMS with ERP and IoT marks a paradigm shift in facility management—shifting from reactive to proactive maintenance strategies. It empowers facilities to operate at peak efficiency, reducing costs, enhancing asset performance, and ensuring compliance with regulatory standards. This holistic approach transforms facilities into agile, data-driven environments where every action is informed by real-time data, fostering resilience and sustainability in the face of evolving challenges.
Frequently Asked Questions
Which Software Systems Can CMMS Integrate With in Facility Management
Discover the compatibility of CMMS with various software systems used in facility management. Learn about integration possibilities with popular systems like ERP, SCADA, and BMS, ensuring seamless data flow and enhanced operational efficiency.
What Challenges Should I Expect When Integrating CMMS with Other Software Systems
Discover the challenges you may encounter when integrating CMMS with other software systems. Learn about potential compatibility issues, data synchronization complexities, and the importance of robust integration protocols.
What Steps Are Involved in Successfully Integrating CMMS with Existing Facility Management Software
This FAQ provides a concise overview of the steps required to seamlessly integrate CMMS (Computerized Maintenance Management System) with existing Facility Management Software. It outlines the essential processes and considerations to ensure a successful integration, focusing on efficiency and operational continuity.
How Does CMMS Integration Improve Operational Efficiency in Facility Management
Learn how CMMS integration enhances operational efficiency in facility management by automating maintenance tasks, streamlining workflows, and optimizing resource allocation.
What are the Benefits of Integrating CMMS with Other Software Systems
Discover the advantages of integrating CMMS with other software systems. Streamline operations, enhance data accuracy, and improve overall efficiency across your organization.