Imagine a well-oiled machine, running smoothly without unexpected breakdowns or costly delays. That’s the promise of a robust CMMS system in action. By centralizing maintenance schedules, equipment data, and work orders, CMMS allows businesses to proactively identify and address potential risks before they escalate into major issues. This proactive approach not only minimizes downtime but also extends the lifespan of critical assets, ultimately saving companies significant costs in repairs and replacements.
One of the key features of CMMS that contributes to risk mitigation is its ability to track historical maintenance data. By analyzing past maintenance records, businesses can identify patterns of equipment failures or performance issues. This foresight enables preemptive maintenance interventions, ensuring that equipment operates at peak efficiency and reducing the likelihood of unexpected failures that could disrupt operations.
Moreover, CMMS facilitates regulatory compliance by ensuring that equipment meets required standards through regular inspections and maintenance checks. This adherence to regulations not only mitigates legal risks but also enhances the reputation of the business as a reliable and responsible entity in its industry.
In essence, deploying an effective CMMS is akin to having a skilled navigator guiding a ship through turbulent waters. It provides clarity, foresight, and control over operational processes, allowing businesses to navigate risks with confidence. Whether it’s maintaining critical machinery, managing inventory levels, or ensuring workplace safety protocols are followed, CMMS empowers businesses to stay ahead of potential risks and focus on growth and innovation.
Effective CMMS deployment isn’t just about implementing software—it’s about transforming operational strategies to foster resilience and sustainability in an ever-evolving business landscape. By embracing CMMS technology, businesses can turn operational risks into opportunities for efficiency and growth, securing a competitive edge in their respective industries.
Streamline Efficiency: How CMMS Revolutionizes Operational Risk Management
Imagine a tool that not only keeps your operations running smoothly but also predicts and prevents potential risks before they occur. That’s the power of Computerized Maintenance Management Systems (CMMS) in revolutionizing Operational Risk Management (ORM). In today’s fast-paced business environment, minimizing downtime and maximizing efficiency are crucial for staying competitive. This is where CMMS steps in as a game-changer.
CMMS software serves as a centralized hub for managing maintenance activities, from scheduling equipment inspections to tracking work orders and managing inventory. By digitizing these processes, CMMS eliminates the inefficiencies of paper-based systems and spreadsheets, ensuring that tasks are completed on time and resources are used optimally. This proactive approach not only saves time but also reduces costs associated with unexpected equipment failures or regulatory compliance issues.
One of the standout features of CMMS is its ability to identify and assess potential risks in real-time. By analyzing historical data and maintenance records, CMMS can pinpoint areas prone to breakdowns or safety hazards. This foresight allows maintenance teams to prioritize tasks based on criticality and allocate resources accordingly, thus mitigating risks before they escalate into costly problems.
Moreover, CMMS enhances collaboration and communication across departments. With instant access to maintenance histories and equipment documentation, teams can make informed decisions swiftly. Whether it’s ensuring compliance with safety regulations or optimizing asset performance, CMMS empowers organizations to operate at peak efficiency while minimizing operational risks.
In essence, CMMS isn’t just about fixing things when they break; it’s about preventing breakdowns altogether. By integrating predictive maintenance algorithms and IoT sensors, modern CMMS platforms go beyond reactive maintenance to predictive and even prescriptive maintenance strategies. This proactive approach not only extends asset lifespan but also enhances overall operational reliability.
CMMS represents a paradigm shift in how businesses manage operational risks. By streamlining maintenance processes, enhancing data-driven decision-making, and fostering a culture of proactive maintenance, CMMS empowers organizations to stay resilient in the face of challenges. Embracing CMMS isn’t just an upgrade—it’s a strategic investment in operational excellence and long-term sustainability.
Mastering Reliability: The Impact of CMMS on Operational Risk Mitigation
In the realm of modern industrial operations, reliability stands as a cornerstone of success. Ensuring equipment functions optimally, minimizing downtime, and preemptively addressing maintenance needs are crucial for operational continuity and efficiency. Here’s where Computerized Maintenance Management Systems (CMMS) step in, revolutionizing how businesses manage their assets and mitigate operational risks.
CMMS software acts as a digital nerve center, orchestrating maintenance activities with precision and foresight. By centralizing data on equipment health, historical performance, and maintenance schedules, CMMS empowers maintenance teams to proactively identify potential issues before they escalate into costly breakdowns. This proactive approach not only extends the lifespan of critical assets but also enhances overall operational reliability.
Imagine CMMS as a vigilant guardian, constantly monitoring the pulse of machinery and systems. It tracks maintenance tasks, schedules inspections, and alerts teams to emerging faults or inefficiencies. This real-time monitoring capability allows businesses to implement predictive maintenance strategies, where repairs are conducted based on data-driven insights rather than reactionary responses. The result? Reduced downtime, improved productivity, and significant cost savings over time.
Furthermore, CMMS fosters accountability and transparency within maintenance operations. Detailed records of maintenance activities, including work orders and technician notes, provide a comprehensive audit trail. This transparency not only ensures compliance with regulatory standards but also aids in continuous improvement initiatives. By analyzing maintenance data trends, businesses can fine-tune their operational strategies, optimize resource allocation, and enhance overall reliability.
In essence, CMMS is more than just a tool; it’s a strategic asset for businesses aiming to master reliability in their operations. By harnessing the power of data and automation, CMMS empowers organizations to mitigate operational risks proactively, streamline maintenance processes, and uphold the integrity of their critical assets. As industries evolve and demand for operational efficiency grows, CMMS remains indispensable in shaping a reliable, resilient future for businesses worldwide.
Future-Proofing Operations: CMMS Strategies to Safeguard Against Risks
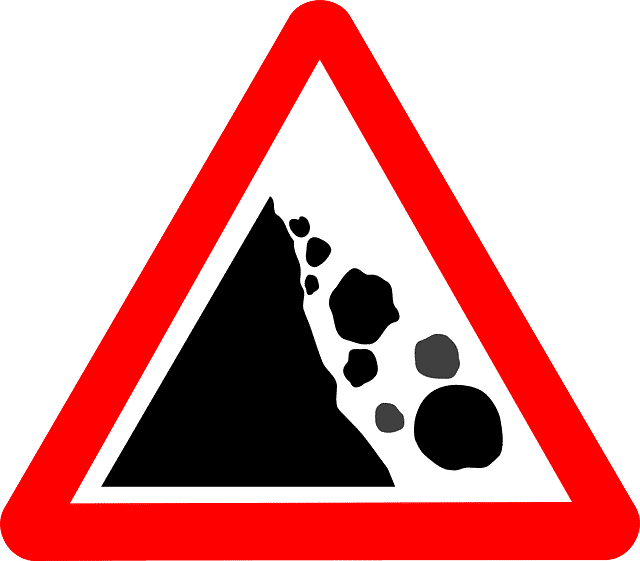
In today’s fast-paced industrial landscape, staying ahead means more than just keeping up with the competition; it’s about future-proofing your operations against unforeseen challenges. CMMS (Computerized Maintenance Management System) emerges as a critical tool in this endeavor, offering robust strategies to safeguard against risks and ensure continuity.
Imagine your business as a well-oiled machine, running smoothly day in and day out. Just like any machine, it requires regular maintenance and monitoring to operate at peak efficiency. This is where CMMS comes into play, acting as the central nervous system that oversees all maintenance activities. From scheduling routine inspections to tracking equipment performance and managing work orders, CMMS streamlines operations and minimizes downtime.
But what sets apart a truly future-proof CMMS strategy? It’s all about proactive rather than reactive maintenance. Instead of waiting for equipment to break down, predictive maintenance tools integrated into CMMS can anticipate issues before they occur. This predictive capability not only saves time and money but also prevents costly disruptions to your production schedule.
Moreover, CMMS doesn’t just stop at maintenance; it also enhances asset reliability. By keeping a detailed record of each asset’s maintenance history and performance metrics, CMMS empowers businesses to make data-driven decisions. Imagine having real-time insights into which machines are due for maintenance or which areas of your facility are prone to frequent breakdowns. This information allows you to allocate resources more effectively and optimize workflows.
In the face of evolving regulatory requirements and technological advancements, flexibility is key. A robust CMMS system adapts to these changes seamlessly, integrating new updates and functionalities without disrupting ongoing operations. This adaptability ensures that your operations remain compliant and efficient, regardless of external changes.
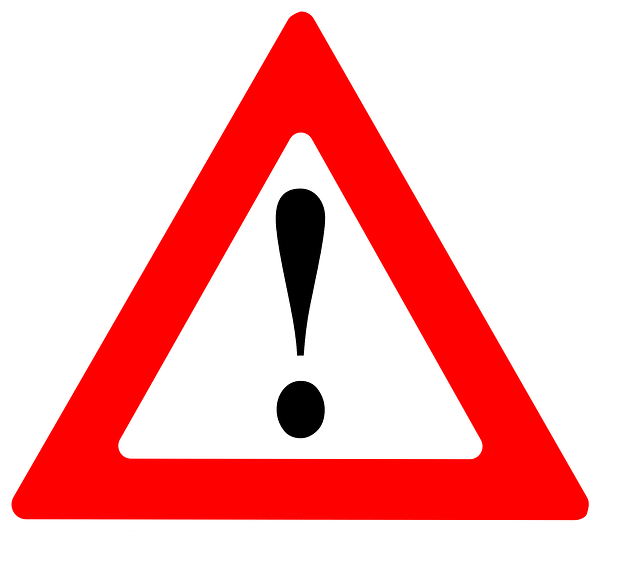
Ultimately, future-proofing with CMMS isn’t just about mitigating risks; it’s about fostering a culture of continuous improvement and innovation. By leveraging CMMS to its full potential, businesses can stay agile, responsive, and ready to tackle whatever challenges the future may bring.
Unlocking Potential: Why CMMS is Vital for Operational Risk Reduction
In today’s fast-paced industrial landscape, minimizing operational risks is crucial for maintaining efficiency and safety. That’s where Computerized Maintenance Management Systems (CMMS) step in as indispensable tools. CMMS software plays a pivotal role in proactively managing maintenance activities, thereby reducing the likelihood of equipment failures and operational disruptions.
Imagine a factory floor humming with activity, machines synchronized like a well-oiled orchestra. CMMS acts as the conductor, ensuring every component performs harmoniously. By centralizing maintenance data and schedules, CMMS empowers maintenance teams to stay ahead of potential issues. It’s not just about reacting to breakdowns; it’s about predicting and preventing them altogether.
With CMMS, businesses can schedule routine inspections and preventive maintenance tasks with precision. This proactive approach not only extends the lifespan of critical assets but also enhances overall operational reliability. Imagine your production line running smoothly without unexpected downtime, saving both time and money.
Moreover, CMMS facilitates compliance with regulatory standards and industry best practices. By maintaining comprehensive records of maintenance activities and equipment history, businesses can demonstrate adherence to safety protocols during audits. This transparency not only builds trust with regulatory bodies but also ensures a safer working environment for employees.
In essence, CMMS transforms reactive maintenance into proactive asset management. It empowers businesses to unlock their operational potential by reducing downtime, optimizing resource allocation, and mitigating risks. From manufacturing plants to healthcare facilities, the benefits of CMMS resonate across industries, enhancing operational efficiency and fostering sustainable growth.
From Challenges to Solutions: CMMS Best Practices for Risk Management
At its core, CMMS enables organizations to digitize their maintenance workflows, centralizing data on equipment, assets, and maintenance history. This centralized approach allows maintenance teams to monitor equipment health in real-time, identify trends, and predict potential failures. By staying ahead of maintenance needs, businesses can reduce the risk of unexpected breakdowns that could disrupt operations and incur unplanned expenses.
Moreover, CMMS facilitates comprehensive asset management by tracking maintenance schedules, equipment warranties, and service histories. This proactive management ensures that assets are serviced regularly and according to manufacturer recommendations, extending their lifespan and optimizing their performance. By adhering to these best practices, businesses not only enhance operational efficiency but also minimize the risk of equipment failures that could lead to production delays or safety hazards.
Furthermore, CMMS systems promote regulatory compliance by maintaining detailed records of maintenance activities and inspections. This documentation is invaluable during audits, demonstrating that equipment is properly maintained and meets regulatory standards. Ensuring compliance not only mitigates legal risks but also enhances organizational reputation and trust among stakeholders.
In essence, implementing CMMS best practices for risk management involves leveraging technology to enhance maintenance operations, optimize asset performance, and ensure regulatory compliance. By adopting a proactive approach to maintenance and asset management, businesses can mitigate risks associated with equipment downtime, operational disruptions, and regulatory non-compliance, thereby fostering a sustainable and efficient workplace environment.
Safety First: Implementing CMMS for Enhanced Operational Resilience
What exactly does it do? Well, think of it as a digital brain for all your maintenance activities. It keeps track of equipment, schedules preventive maintenance, and alerts you when something needs attention. It’s like having a proactive maintenance team working around the clock, ensuring everything runs at peak efficiency.
One of the biggest advantages of using a CMMS is safety. By keeping equipment in top shape through regular check-ups and maintenance, you significantly reduce the risk of accidents and unexpected failures. For industries where safety is paramount—like manufacturing, healthcare, or transportation—implementing a CMMS is not just beneficial; it’s crucial.
Take a hospital, for instance. With a CMMS in place, they can ensure that all medical equipment is regularly serviced and calibrated, minimizing the chances of equipment failures during critical procedures. This directly translates to better patient care and safety.
Moreover, a CMMS helps in compliance with safety regulations and standards. It maintains a detailed record of all maintenance activities, inspections, and repairs, which can be invaluable during audits or inspections. It’s like having your paperwork always organized and ready, ensuring you’re always prepared.
In today’s fast-paced world, operational downtime can be costly, both financially and in terms of reputation. A CMMS helps prevent unplanned downtime by addressing maintenance issues before they become disruptive. This proactive approach not only saves money but also boosts operational efficiency and customer satisfaction.
So, whether you’re running a factory, managing a fleet of vehicles, or overseeing a healthcare facility, implementing a CMMS is a strategic move towards enhancing operational resilience and safety. It’s about staying ahead of the curve, ensuring your business operates smoothly while keeping safety at the forefront. After all, in business as in life, safety should always come first.
Beyond Maintenance: How CMMS Enhances Overall Operational Safety
Imagine running a facility where every piece of equipment hums with efficiency, and safety is more than just a checklist—it’s a culture. This is the promise of a well-implemented CMMS, or Computerized Maintenance Management System. Beyond the routine tasks of maintenance, CMMS plays a pivotal role in enhancing overall operational safety.
At its core, CMMS is a digital powerhouse that keeps your operations in sync. It schedules maintenance tasks, tracks equipment downtime, and optimizes inventory—all while ensuring compliance with safety regulations. By streamlining these processes, CMMS minimizes human error, a crucial factor in preventing workplace accidents.
But CMMS goes beyond mere compliance. It acts as a proactive guardian of safety, foreseeing potential risks before they escalate. Imagine it as a vigilant sentinel, constantly analyzing data to predict maintenance needs and identify safety hazards. This foresight not only prevents equipment failures but also safeguards your most valuable asset—your workforce.
In essence, CMMS transforms safety protocols from reactive to proactive. It empowers teams to address issues swiftly, reducing downtime and enhancing productivity. Picture a scenario where every maintenance check isn’t just a task but a step towards fortifying your operational fortress.
Moreover, CMMS doesn’t operate in isolation. It integrates with other enterprise systems, fostering a holistic approach to safety management. This interconnectedness ensures that safety data flows seamlessly across departments, empowering decision-makers with real-time insights.
The true essence of CMMS lies in its ability to weave safety into the fabric of daily operations. It’s not just about maintaining equipment; it’s about nurturing a culture where safety isn’t an obligation but a shared commitment. Embrace CMMS, and witness how it transforms your operational landscape, making safety not just a goal but a way of life.
Frequently Asked Questions
What are the key benefits of deploying CMMS for risk management?
Discover the key benefits of using CMMS for effective risk management. Learn how CMMS enhances preventive maintenance, reduces downtime, improves regulatory compliance, and increases equipment reliability, ensuring operational resilience.
What are the essential features to look for in a CMMS for risk mitigation?
Learn about the key features to consider when choosing a CMMS (Computerized Maintenance Management System) to effectively mitigate risks. Discover how functionalities like preventive maintenance scheduling, asset tracking, real-time data analytics, and compliance management can enhance risk management strategies.
What is CMMS and how does it help mitigate operational risks?
Learn how CMMS (Computerized Maintenance Management System) helps mitigate operational risks by efficiently managing maintenance schedules, tracking assets, and ensuring compliance with safety regulations. Discover its role in minimizing equipment downtime and optimizing maintenance workflows.
How can CMMS enhance operational reliability and reduce downtime?
Learn how a Computerized Maintenance Management System (CMMS) can improve operational reliability and minimize downtime by streamlining maintenance tasks, scheduling preventive maintenance, and enabling better asset management and tracking.
How do you successfully implement CMMS to minimize operational risks?
Learn how to effectively implement CMMS to reduce operational risks with our concise guide. Discover key strategies and best practices to optimize maintenance management.