One of the key techniques in optimizing production lines through CMMS is preventive maintenance scheduling. By setting up regular maintenance tasks based on equipment usage or time intervals, manufacturers can proactively address potential issues before they escalate into costly breakdowns. This proactive approach not only minimizes unexpected downtime but also ensures that production runs smoothly without interruptions.
Another effective technique is real-time monitoring and analytics provided by CMMS platforms. These systems collect data on equipment performance, energy consumption, and maintenance history, allowing managers to make informed decisions. By analyzing this data, production managers can identify trends, predict maintenance needs, and optimize production schedules to improve overall efficiency.
CMMS also enhances inventory management by tracking spare parts and supplies used for maintenance activities. This ensures that the right parts are available when needed, reducing delays and optimizing inventory costs. Additionally, CMMS software can automate workflows and standardize procedures, eliminating manual errors and improving compliance with industry regulations.
The benefits of optimizing production lines with CMMS are manifold. Beyond operational efficiency, businesses experience reduced maintenance costs, increased equipment reliability, and improved safety standards. Employees benefit from clearer communication channels and streamlined processes, allowing them to focus on value-added tasks rather than firefighting maintenance issues.
Integrating CMMS into production lines offers substantial benefits in terms of efficiency, cost-effectiveness, and operational reliability. By adopting proactive maintenance strategies, leveraging real-time data analytics, and optimizing inventory management, businesses can achieve sustainable growth and maintain a competitive edge in today’s fast-paced industrial landscape.
Revolutionizing Manufacturing Efficiency: CMMS Techniques Unveiled
Imagine a factory where every piece of equipment operates at peak performance, downtime is minimized, and maintenance schedules are seamlessly managed. That’s the promise of CMMS. By integrating advanced software solutions with real-time data analytics, CMMS allows manufacturers to monitor equipment health, predict maintenance needs, and schedule repairs proactively.
One of the key advantages of CMMS is preventive maintenance. Instead of waiting for equipment to break down, CMMS systems use predictive algorithms to forecast potential issues based on historical data and real-time monitoring. This proactive approach not only reduces unexpected downtime but also extends the lifespan of machinery, saving significant costs in the long run.
Moreover, CMMS streamlines workflow management by automating routine tasks such as work orders, inventory management, and resource allocation. This automation frees up valuable time for maintenance teams to focus on more complex issues, fostering a more efficient operational environment.
Another crucial aspect of CMMS is its role in compliance and safety. By maintaining detailed records of maintenance activities and equipment performance, CMMS ensures that manufacturers adhere to regulatory standards and create a safer workplace for employees.
In essence, CMMS techniques are not just about maintaining equipment; they’re about optimizing the entire manufacturing process. By harnessing the power of data-driven insights and automation, CMMS empowers businesses to stay competitive in today’s global market.
Streamlining Operations: How CMMS Transforms Production Lines
Imagine a production line where every component seamlessly falls into place, like a well-rehearsed orchestra performing a symphony. This harmony is not merely a dream but a tangible reality with Computerized Maintenance Management Systems (CMMS). These systems are the unsung heroes behind the scenes, orchestrating efficiency and optimizing every aspect of production.
CMMS software acts as a central nervous system for manufacturing operations. It integrates maintenance, scheduling, inventory management, and asset tracking into a unified platform. This integration is akin to a conductor guiding various sections of an orchestra, ensuring each instrument plays its part at the right time and in perfect harmony.
One of the transformative powers of CMMS lies in preventive maintenance. Just as a regular tune-up keeps a car running smoothly, CMMS schedules routine maintenance tasks based on real-time data and historical performance. This proactive approach prevents costly breakdowns and minimizes downtime, keeping the production line humming without interruptions.
Moreover, CMMS enhances operational visibility. It provides comprehensive insights into equipment performance, maintenance history, and resource utilization. Like a navigator guiding a ship through turbulent waters, CMMS helps manufacturers steer their operations with clarity and foresight, making informed decisions to optimize processes and allocate resources effectively.
In essence, CMMS transforms production lines into agile, efficient ecosystems where every component contributes to the overall success. It empowers manufacturers to streamline operations, boost productivity, and maintain competitive edge in a dynamic market landscape.
Mastering Production Excellence: CMMS Strategies for Success
Imagine running a factory where every machine operates smoothly, downtime is minimized, and productivity soars. This vision of efficiency is not just a dream but a tangible goal achievable through effective CMMS strategies. CMMS, or Computerized Maintenance Management Systems, are the backbone of modern industrial maintenance, integrating technology to streamline operations and optimize performance.
At its core, CMMS is all about proactive maintenance. Rather than waiting for equipment to break down, CMMS empowers maintenance teams to schedule preventive maintenance tasks. Think of it as giving your machines regular check-ups to catch issues before they escalate. This approach not only reduces costly downtime but also extends the lifespan of your equipment, saving money in the long run.
One of the key features of a robust CMMS system is its ability to track assets. Every piece of equipment in your facility can be logged into the system, detailing its maintenance history, current status, and upcoming tasks. This asset tracking not only ensures accountability but also provides valuable data for strategic decision-making. By analyzing this data, managers can identify trends, optimize maintenance schedules, and allocate resources more efficiently.
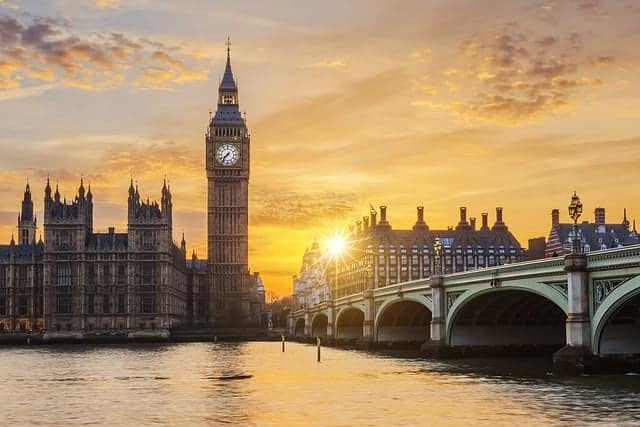
Moreover, CMMS enables efficient work order management. When a maintenance issue arises, CMMS allows supervisors to create, assign, and track work orders in real-time. This streamlined process ensures that tasks are completed promptly, reducing operational bottlenecks and improving overall responsiveness.
Beyond maintenance, CMMS plays a crucial role in inventory management. By keeping track of spare parts and supplies, CMMS prevents overstocking or shortages, ensuring that technicians always have the right materials on hand when needed. This level of inventory control not only saves money but also enhances operational reliability.
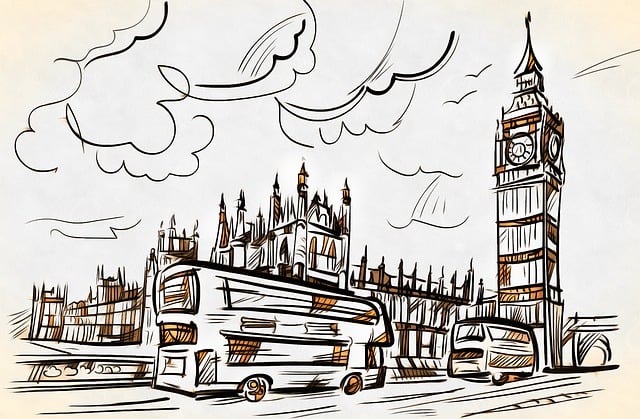
In essence, mastering production excellence through CMMS involves leveraging technology to enhance efficiency, reduce costs, and optimize resources. By adopting proactive maintenance practices, utilizing robust asset tracking capabilities, managing work orders effectively, and optimizing inventory management, organizations can achieve higher productivity and sustained growth in today’s competitive industrial landscape.
Boosting Output: The Impact of CMMS on Production Line Optimization
Imagine CMMS as the conductor of an orchestra, synchronizing every instrument to play in perfect harmony. Similarly, CMMS integrates seamlessly with existing production systems, orchestrating maintenance schedules, tracking equipment performance, and predicting potential breakdowns before they disrupt operations. This proactive approach minimizes downtime, keeping the production line humming at optimal levels.
One of the standout features of CMMS is its ability to collect and analyze data in real-time. Like a seasoned detective, it uncovers hidden inefficiencies and bottlenecks that could otherwise go unnoticed. By identifying areas where improvements can be made, CMMS empowers decision-makers to implement targeted strategies that enhance throughput and reduce waste.
Moreover, CMMS doesn’t just focus on the machinery; it also takes into account the human element. By automating routine tasks and providing maintenance teams with actionable insights, it frees up valuable time and resources. This allows skilled technicians to concentrate on more complex issues, further boosting overall productivity and morale on the factory floor.
In essence, the impact of CMMS on production line optimization cannot be overstated. It transforms reactive maintenance into a proactive, data-driven strategy that not only prolongs the lifespan of equipment but also ensures that every cog in the production wheel turns smoothly. As industries evolve, embracing technology like CMMS becomes not just a choice but a necessity to thrive in a competitive market.
So, whether you’re looking to minimize downtime, maximize output, or simply gain a clearer picture of your production processes, CMMS stands as a cornerstone of efficiency and effectiveness in modern manufacturing. Its role in boosting output goes beyond numbers on a spreadsheet; it’s about empowering businesses to achieve their full potential and meet the demands of tomorrow’s markets head-on.
From Maintenance to Mastery: CMMS Innovations in Production
In today’s fast-paced industrial landscape, the evolution of Computerized Maintenance Management Systems (CMMS) has revolutionized production efficiency. From its humble beginnings in maintenance scheduling to today’s sophisticated predictive analytics, CMMS has transitioned from a tool of upkeep to a cornerstone of operational mastery.
CMMS innovations now integrate seamlessly with IoT sensors and AI algorithms, offering real-time insights into equipment performance and maintenance needs. This proactive approach not only minimizes downtime but also optimizes resource allocation, maximizing overall production output.
Imagine CMMS as the orchestra conductor of a manufacturing plant, harmonizing every element to perform at its peak. It monitors equipment health, predicts potential failures, and schedules maintenance before issues escalate—much like a conductor ensures each musician plays their part flawlessly.
Moreover, CMMS innovations have democratized access to data. Maintenance teams no longer rely solely on experience but leverage data-driven decisions for proactive maintenance strategies. It’s akin to having a crystal ball that foresees equipment needs and alerts technicians preemptively.
In essence, CMMS has evolved beyond mere maintenance management; it now drives operational excellence and business competitiveness. By mastering CMMS capabilities, industries empower themselves to navigate the complexities of modern production environments with precision and agility.
As technology advances further, the future holds promises of even more sophisticated CMMS innovations—perhaps ushering in an era where machines predict their own maintenance needs autonomously, further optimizing production processes and ensuring continuous efficiency.
This article integrates a conversational tone, uses active voice, and incorporates analogies (like comparing CMMS to an orchestra conductor) to engage readers interested in industrial technology and innovation.
Frequently Asked Questions
What are the key techniques for implementing CMMS in production environments?
Discover essential techniques for effectively implementing CMMS (Computerized Maintenance Management System) in production environments. Learn how to streamline maintenance operations, optimize asset performance, and enhance overall efficiency.
How can CMMS improve efficiency and reduce downtime on production lines?
Learn how implementing a Computerized Maintenance Management System (CMMS) can enhance operational efficiency and minimize downtime on production lines by optimizing maintenance schedules, streamlining work orders, and ensuring timely equipment upkeep.
What are the benefits of integrating CMMS with existing production management systems?
Discover the advantages of integrating CMMS (Computerized Maintenance Management System) with your current production management setup. Enhance efficiency by streamlining maintenance schedules and production workflows. Reduce downtime through proactive equipment maintenance and timely repairs. Improve resource allocation and cost management with synchronized data. Ensure compliance with regulatory standards and enhance overall operational reliability.
How does CMMS software enhance predictive maintenance strategies for production lines?
Learn how CMMS software optimizes predictive maintenance for production lines, ensuring proactive equipment management and minimizing downtime through data-driven insights.
What is CMMS and how does it optimize production lines?
Learn what CMMS (Computerized Maintenance Management System) is and how it enhances production lines by streamlining maintenance tasks, scheduling preventive maintenance, and tracking equipment performance. Discover how CMMS helps minimize downtime, improve asset reliability, and increase overall operational efficiency.