CMMS isn’t just another acronym in the tech world; it’s the game-changer that propels businesses from reactive to proactive maintenance strategies. Picture this: instead of waiting for a machine to break down and disrupt production, CMMS allows you to monitor its health in real-time, much like how a doctor keeps an eye on a patient’s vital signs. It gathers data constantly, analyzing trends and anomalies to predict maintenance needs accurately.
What makes CMMS truly remarkable is its ability to deliver precise insights on demand. It’s like having a crystal ball that reveals the future of your equipment’s performance. Need to know when to schedule that critical maintenance task? CMMS has got you covered with its predictive analytics, ensuring downtime becomes a thing of the past.
Moreover, CMMS doesn’t just stop at predictive insights; it also streamlines workflows with its user-friendly interface. Think of it as your personal assistant, organizing maintenance schedules, tracking inventory, and even managing work orders effortlessly. It empowers maintenance teams to work smarter, not harder, maximizing efficiency and minimizing costs.
In essence, CMMS transforms maintenance into a proactive, data-driven endeavor. It’s not just about fixing what’s broken but preventing breakdowns altogether. With real-time maintenance data at your fingertips, courtesy of CMMS, you’re always steps ahead, ensuring smooth operations and happy stakeholders.
Unlocking Efficiency: CMMS and the Power of Real-Time Maintenance Data
In today’s fast-paced industrial landscape, maximizing efficiency isn’t just a goal—it’s a necessity. That’s where Computerized Maintenance Management Systems (CMMS) step in, revolutionizing how businesses manage their maintenance operations. At the heart of this transformation lies the power of real-time maintenance data.
Imagine a scenario where every piece of equipment in your facility communicates its operational status directly to your maintenance team. This isn’t science fiction; it’s the reality facilitated by CMMS. These systems integrate seamlessly with your existing infrastructure, capturing data on equipment performance, maintenance schedules, and repair histories.
One of the most significant advantages of CMMS is its ability to provide actionable insights instantly. By leveraging real-time data, maintenance teams can proactively identify and address potential issues before they escalate into costly downtime. This proactive approach not only minimizes disruptions but also extends the lifespan of critical assets.
Moreover, CMMS transforms reactive maintenance into a strategic asset management tool. Instead of waiting for equipment failures to occur, businesses can schedule preventive maintenance based on actual usage data. This predictive maintenance strategy reduces unplanned downtime, enhances operational continuity, and ultimately boosts productivity.
Furthermore, CMMS facilitates compliance with regulatory standards by maintaining comprehensive records of maintenance activities. Whether it’s documenting inspections, tracking repairs, or ensuring equipment calibration, these systems streamline audit processes and mitigate compliance risks.
Insider’s Guide: How CMMS Transforms Operations with Real-Time Data
Have you ever wondered how modern businesses streamline their operations seamlessly? The answer lies in CMMS (Computerized Maintenance Management Systems), a revolutionary tool transforming industries through real-time data insights. Imagine a scenario where every piece of equipment in a factory or facility communicates its operational status instantaneously, enabling proactive maintenance and reducing downtime to a minimum. That’s the power of CMMS.
CMMS isn’t just about managing maintenance schedules; it’s about harnessing the potential of data. By integrating real-time data analytics, CMMS platforms provide invaluable insights into equipment performance, energy consumption patterns, and predictive maintenance needs. This proactive approach not only extends the lifespan of machinery but also enhances overall operational efficiency.
In industries like manufacturing, healthcare, and hospitality, where downtime can cost thousands per hour, CMMS offers a competitive edge. It empowers decision-makers with actionable data, enabling them to make informed choices swiftly. Whether it’s scheduling preventive maintenance tasks or predicting inventory needs based on production forecasts, CMMS systems optimize resource allocation and workflow management.
The impact of CMMS goes beyond operational efficiency; it fosters a culture of continuous improvement. By monitoring key performance indicators (KPIs) in real-time, teams can identify trends, address inefficiencies promptly, and innovate proactively. This data-driven approach not only enhances productivity but also boosts employee morale by minimizing frustrations associated with unexpected breakdowns.
In essence, CMMS isn’t just a tool; it’s a strategic asset that transforms how businesses operate in today’s fast-paced world. By leveraging real-time data insights, organizations can stay ahead of the curve, ensuring smoother operations, reduced costs, and ultimately, happier customers.
This article aims to capture the essence of how CMMS systems enhance operations using real-time data while maintaining an engaging and informative tone suitable for a broad audience interested in industrial management and technology.
Breaking Down Barriers: CMMS and the Evolution of Maintenance Tracking
CMMS software serves as the backbone of modern maintenance strategies, streamlining the process from reactive to proactive maintenance. By digitizing workflows and centralizing data, CMMS enables maintenance teams to schedule tasks, track work orders, and manage inventory seamlessly. This shift not only enhances productivity but also minimizes downtime by preemptively identifying potential equipment issues.
One of the most significant advantages of CMMS is its ability to break down communication barriers within maintenance operations. Through real-time updates and notifications, stakeholders across the organization can stay informed about equipment status and maintenance progress. This transparency fosters collaboration and ensures that everyone is on the same page, from technicians on the floor to managers in the boardroom.
Moreover, CMMS systems empower decision-making by providing actionable insights derived from historical data and performance metrics. By analyzing trends and patterns, organizations can optimize maintenance schedules, allocate resources more effectively, and ultimately extend the lifespan of their assets.
In essence, CMMS represents a paradigm shift in maintenance management, where data-driven decisions replace guesswork and intuition. As industries embrace digital transformation, the integration of CMMS not only enhances operational efficiency but also sets the stage for future innovations in predictive maintenance and IoT (Internet of Things) integration.
From Data to Decision: CMMS Revolutionizes Real-Time Maintenance Insights
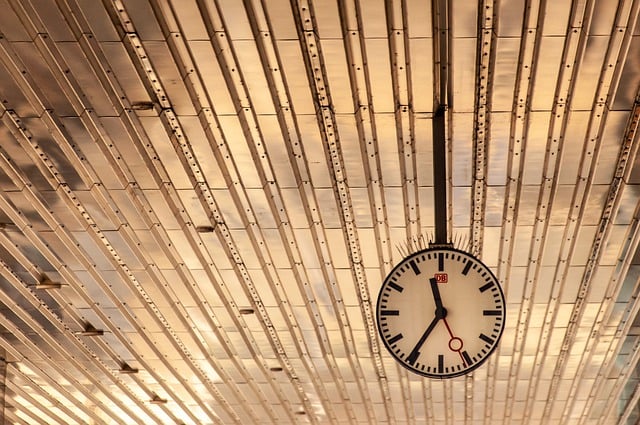
Imagine a scenario where every machine, every asset in your factory, communicates its health status directly to you, almost like having a doctor’s report on demand. That’s the power of CMMS. These systems collect and analyze data from various sensors and equipment, providing maintenance teams with critical information about asset performance, downtime patterns, and even predictive maintenance alerts.
One of the most significant impacts of CMMS is its ability to streamline maintenance workflows. By automating routine tasks such as work orders and scheduling, CMMS frees up valuable time for maintenance technicians to focus on more strategic activities. This not only boosts operational efficiency but also reduces costly downtime by ensuring that equipment is properly maintained and serviced at optimal intervals.
Moreover, CMMS enables proactive decision-making. With real-time insights into asset conditions and performance trends, maintenance managers can preemptively address potential issues before they escalate into costly breakdowns. This proactive approach not only extends the lifespan of equipment but also enhances overall productivity and profitability.
In essence, CMMS represents a paradigm shift in maintenance management, moving away from reactive, ad-hoc approaches to a data-driven, proactive methodology. By harnessing the power of data analytics, businesses can achieve higher operational reliability, lower maintenance costs, and ultimately, stay ahead in a competitive market landscape.
The Future is Now: CMMS Redefining Maintenance Management Through Data
CMMS isn’t just a software; it’s the brain behind efficient maintenance strategies. By amalgamating data analytics, IoT sensors, and predictive algorithms, CMMS doesn’t just react to maintenance needs; it predicts them. It’s akin to having a clairvoyant mechanic who can foresee a breakdown before it strands your operations.
One of the marvels of CMMS lies in its ability to collect and analyze vast amounts of data in real-time. Every vibration, every temperature fluctuation, and every anomaly is logged and processed, enabling maintenance teams to intervene precisely when needed. It’s like having a team of vigilant sentinels monitoring your equipment 24/7, ready to spring into action at the first sign of trouble.
Moreover, CMMS transforms historical maintenance data into actionable insights. It’s not just about fixing what’s broken; it’s about optimizing performance proactively. Imagine a symphony where every instrument plays harmoniously because each note is anticipated and corrected before it becomes discordant.
In industries ranging from manufacturing to healthcare, CMMS is the linchpin that ensures operational continuity. Downtime becomes a relic of the past as preventive maintenance becomes the norm. Costs are slashed, efficiency soars, and customer satisfaction reaches new heights—all thanks to CMMS.
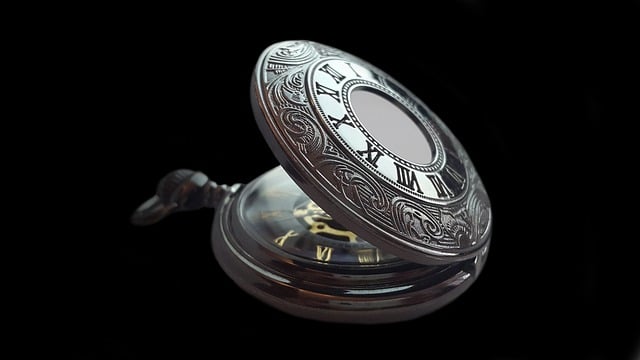
As we march into the future, CMMS will continue to evolve. Machine learning will refine its predictive capabilities, and AI will enhance its decision-making prowess. The future of maintenance management isn’t just promising; it’s transformative. With CMMS at the helm, the future is now—where data isn’t just power; it’s the lifeline of operational excellence.
Frequently Asked Questions
What are the key benefits of using CMMS for accessing on-demand maintenance data?
Discover the key advantages of utilizing CMMS for accessing maintenance data instantly. CMMS streamlines data retrieval, enhances equipment uptime by enabling proactive maintenance scheduling, improves cost-efficiency through optimized resource allocation, and boosts overall operational productivity.
What is real-time maintenance data, and why is it important for businesses?
Real-time maintenance data refers to continuously updated information about the condition, performance, and operational status of equipment or assets. It is crucial for businesses as it enables proactive maintenance scheduling, reduces downtime, enhances operational efficiency, and prolongs equipment lifespan by identifying issues promptly.
How does a CMMS system enable real-time data acquisition in maintenance operations?
Learn how a CMMS system facilitates real-time data acquisition during maintenance tasks, enhancing efficiency and accuracy by enabling technicians to input and access data instantly. This enables immediate tracking of work progress, equipment status updates, and timely decision-making based on up-to-date information.
How can real-time maintenance data from CMMS improve operational efficiency?
Learn how real-time maintenance data from CMMS (Computerized Maintenance Management System) enhances operational efficiency by enabling timely insights into equipment status, proactive maintenance scheduling, and optimizing resource allocation.
What are the challenges associated with implementing a real-time maintenance data strategy using CMMS?
This FAQ description outlines the challenges involved in implementing a real-time maintenance data strategy using CMMS (Computerized Maintenance Management System). It focuses on identifying and addressing obstacles that organizations may face when integrating live data into their maintenance operations efficiently.