One of the primary benefits of CMMS automation lies in its ability to optimize maintenance schedules. By analyzing historical data and usage patterns, CMMS can predict when equipment will require servicing, preemptively scheduling maintenance to prevent costly breakdowns. This proactive approach not only extends the lifespan of assets but also reduces downtime, keeping operations running smoothly.
Moreover, CMMS automation improves resource allocation. With real-time visibility into work order status and technician availability, managers can assign tasks more effectively, balancing workload and maximizing productivity. This ensures that skilled labor is utilized efficiently, reducing idle time and improving overall operational output.
Another compelling advantage is the enhanced compliance and documentation that CMMS automation provides. By standardizing maintenance procedures and documentation processes, businesses can ensure regulatory compliance more effectively. Detailed records of maintenance activities are automatically generated and stored, facilitating audits and demonstrating adherence to industry standards.
Furthermore, the analytical capabilities of CMMS enable continuous improvement. By analyzing performance metrics and identifying bottlenecks, businesses can refine their maintenance strategies over time. This data-driven approach empowers decision-makers to make informed choices that optimize efficiency and reduce operational costs.
In essence, automating work orders with CMMS isn’t just about embracing technology—it’s about unlocking potential. It empowers businesses to operate smarter, leaner, and more competitively in today’s fast-paced markets. By leveraging automation, organizations can elevate their maintenance practices, achieve higher levels of reliability, and ultimately deliver superior service to their customers.
Streamlining Efficiency: How CMMS Automation Revolutionizes Work Orders
Streamlining efficiency in workplace operations has become increasingly crucial in today’s fast-paced business environment. One of the key advancements driving this transformation is CMMS automation, particularly in managing work orders. CMMS, or Computerized Maintenance Management Systems, has revolutionized how organizations handle maintenance tasks, offering a systematic approach to maintenance planning and execution.
Automation through CMMS simplifies the entire work order process, from initiation to completion. Instead of relying on manual entry and communication, CMMS automates the scheduling of tasks, assigns work orders to the appropriate personnel, and tracks progress in real-time. This not only saves time but also minimizes errors that can occur through manual data entry.
Imagine a scenario where a facility manager needs to address a critical equipment breakdown. With CMMS automation, the manager can swiftly create a work order detailing the issue, set priorities, and automatically assign it to the maintenance team. Through real-time updates and notifications, stakeholders are informed of progress without delay, ensuring that downtime is minimized and operations remain efficient.
Moreover, CMMS automation enhances accountability and transparency across the maintenance workflow. Managers can easily monitor the status of work orders, track resource allocation, and analyze historical data to optimize future maintenance strategies. This proactive approach not only extends the lifespan of equipment but also reduces operational costs over time.
In essence, CMMS automation isn’t just about improving efficiency; it’s about transforming how organizations manage maintenance activities. By leveraging technology to streamline work orders, businesses can achieve higher productivity levels, improve asset reliability, and ultimately deliver better service to their customers.
This article focuses on how CMMS automation optimizes work orders, highlighting its benefits in enhancing efficiency and operational transparency within organizations.
Maximizing Productivity: The Strategic Advantages of CMMS Work Order Automation
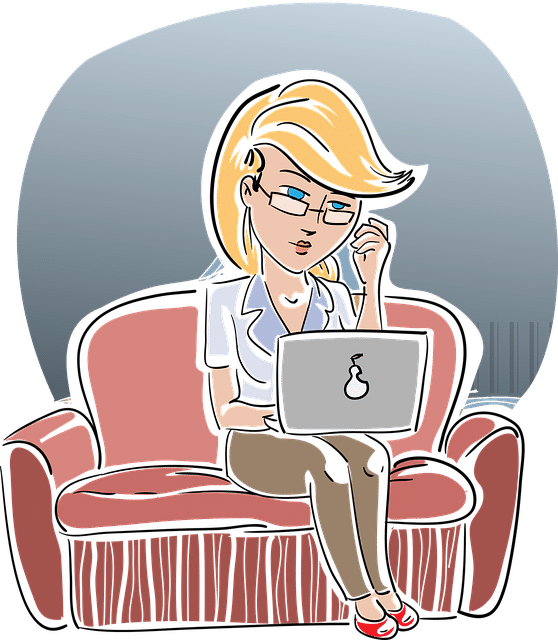
Imagine your maintenance team seamlessly handling work orders without the hassle of manual paperwork. CMMS work order automation makes this a reality. By automating the process of generating, assigning, and tracking work orders, businesses can significantly reduce downtime. This means fewer delays in repairs or maintenance tasks, leading to smoother operations overall.
But the benefits go beyond just efficiency. With CMMS, managers gain real-time insights into the status of work orders. They can easily prioritize tasks based on urgency and allocate resources accordingly. This proactive approach helps in preventing potential breakdowns before they occur, saving both time and costs.
Moreover, CMMS work order automation enhances accountability within teams. Each step of the maintenance process is recorded and tracked, leaving little room for errors or oversights. Team members are more accountable for their tasks, knowing that their performance is being monitored and evaluated.
For businesses aiming to scale, CMMS provides invaluable data for decision-making. By analyzing historical maintenance data, managers can identify trends, optimize workflows, and plan for future needs more effectively. This data-driven approach not only boosts productivity but also ensures that resources are used optimally.
In essence, adopting CMMS work order automation is more than just a technological upgrade; it’s a strategic advantage. It empowers businesses to operate efficiently, reduce costs, and deliver consistent results. By embracing automation in maintenance processes, businesses can stay ahead in a competitive landscape where every minute saved contributes to long-term success.
From Manual to Automated: Unveiling the Benefits of CMMS for Work Orders
Gone are the days of sorting through piles of paperwork or relying on memory to keep track of pending work orders. With CMMS, everything is streamlined and organized. It acts as a centralized hub where technicians can access real-time data about ongoing tasks, equipment status, and upcoming maintenance schedules. This not only improves efficiency but also reduces downtime significantly.
One of the standout features of CMMS is its ability to automate repetitive tasks. By setting up predefined workflows and triggers, routine processes like work order generation and assignment can be executed automatically. This frees up valuable time for maintenance teams to focus on more critical issues or proactive maintenance strategies.
Moreover, CMMS enhances communication across departments. Through its intuitive interface, stakeholders can collaborate effortlessly, sharing updates, instructions, and reports in real-time. This fosters a more connected work environment where everyone is on the same page, ultimately leading to faster resolutions and better decision-making.
In terms of cost-effectiveness, CMMS proves to be a game-changer. By reducing manual errors and optimizing resource allocation, businesses can save on operational costs in the long run. It also helps in extending the lifespan of equipment by ensuring timely inspections and preventive maintenance, thus minimizing the need for costly repairs or replacements.
Saving Time, Enhancing Accuracy: Why CMMS Automation Matters
Imagine a manufacturing plant buzzing with activity. Machines are running, production is in full swing, and suddenly, there’s a breakdown. In the past, this could lead to hours of downtime as technicians scrambled to diagnose and fix the issue manually. However, with CMMS automation, such scenarios are minimized. These systems monitor equipment in real-time, detecting anomalies before they escalate into problems. This proactive approach not only prevents costly breakdowns but also ensures smoother operations.
Accuracy is another pivotal benefit of CMMS automation. Manual record-keeping is prone to errors, whether it’s logging maintenance tasks or tracking inventory levels. With automation, every data point is recorded instantly and accurately. This means technicians have access to up-to-date information at their fingertips, enabling them to make informed decisions swiftly.
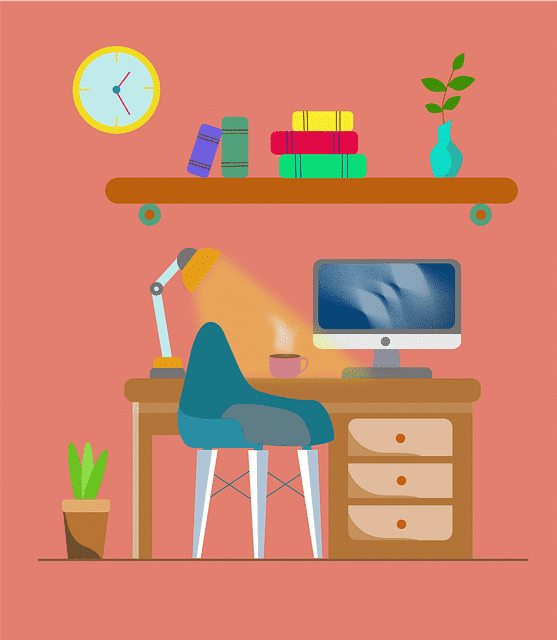
Moreover, CMMS automation optimizes scheduling. Instead of relying on guesswork or reactive maintenance, tasks are scheduled based on actual equipment conditions and usage patterns. This predictive capability extends the lifespan of assets, reduces maintenance costs, and enhances overall productivity.
For industries like healthcare, hospitality, and transportation, where downtime can have critical consequences, CMMS automation ensures operational continuity. Hospitals can’t afford equipment failures during surgeries, hotels need HVAC systems running flawlessly for guest comfort, and airlines must maintain aircraft to strict safety standards. In these sectors, CMMS automation isn’t just a convenience—it’s a necessity.
CMMS automation isn’t just about embracing technology; it’s about staying competitive in a global marketplace that demands efficiency and reliability. By saving time, enhancing accuracy, and enabling proactive maintenance, these systems empower organizations to focus on what truly matters: delivering exceptional service and maximizing uptime.
Transforming Operations: The Power of CMMS in Work Order Management
Imagine your business as a well-oiled machine, where every part works seamlessly in harmony. CMMS acts as the conductor, orchestrating maintenance activities with precision and foresight. It centralizes work orders, ensuring that every task, from routine inspections to urgent repairs, is logged, prioritized, and executed promptly.
With CMMS, supervisors gain a bird’s-eye view of operations in real-time. They can track the status of work orders, allocate resources effectively, and adjust schedules on the fly. This proactive approach minimizes downtime, enhances productivity, and prolongs the lifespan of critical assets.
Moreover, CMMS empowers maintenance teams with historical data and predictive analytics. By analyzing past maintenance patterns and equipment performance, businesses can anticipate potential issues before they escalate. This foresight not only prevents costly breakdowns but also allows for strategic planning and budgeting.
In today’s fast-paced business environment, agility is key. CMMS provides the flexibility to adapt to changing demands effortlessly. Whether it’s scaling operations, complying with regulatory standards, or integrating new technologies, CMMS ensures that businesses stay ahead of the curve.
Furthermore, CMMS isn’t just about maintenance; it’s about maximizing operational efficiency and driving profitability. By reducing downtime, optimizing resource utilization, and improving asset reliability, businesses can focus more on growth and less on operational hiccups.
In essence, CMMS isn’t just a software tool; it’s a game-changer. It transforms operations by streamlining work order management, boosting productivity, and fostering a proactive maintenance culture. With CMMS, businesses can navigate the complexities of modern industry with confidence and clarity, setting a new standard for operational excellence.
Cost Efficiency Unleashed: Exploring CMMS Automation for Work Orders
In today’s fast-paced business environment, efficiency and cost-effectiveness are paramount. This is where Computerized Maintenance Management Systems (CMMS) step in, particularly in automating work orders. Imagine a scenario where every maintenance task flows seamlessly, from initiation to completion, without manual intervention. CMMS automation makes this a reality by streamlining the entire process.
Automation in CMMS transforms how work orders are managed. Traditionally, initiating a work order involved multiple steps: logging the issue, assigning tasks manually, and tracking progress. With automation, these tasks are handled swiftly and accurately. The system automatically generates work orders based on predefined triggers such as equipment failure or scheduled maintenance intervals. This proactive approach minimizes downtime and reduces reactive maintenance costs.
Moreover, CMMS automation enhances workflow efficiency. By routing work orders directly to technicians equipped with mobile devices, response times are shortened. Technicians receive real-time updates and can update the status of tasks instantly, ensuring everyone stays informed and on track. This not only improves operational efficiency but also boosts overall productivity.
Cost efficiency is another significant benefit of CMMS automation. By reducing manual errors and optimizing resource allocation, organizations save both time and money. Predictive maintenance capabilities of CMMS systems help prevent costly equipment breakdowns, extending asset lifespan and reducing replacement costs. Additionally, streamlined inventory management ensures that only necessary parts are stocked, minimizing excess inventory expenses.
CMMS automation revolutionizes how organizations manage work orders, offering unparalleled efficiency and cost savings. By automating routine tasks, improving workflow processes, and enhancing predictive maintenance capabilities, CMMS systems unlock new levels of operational excellence. Embracing CMMS automation isn’t just about efficiency—it’s about future-proofing maintenance strategies and driving sustainable growth.
Empowering Maintenance Teams: The Impact of CMMS on Work Order Processes
In today’s fast-paced industrial landscape, the efficiency of maintenance teams plays a pivotal role in ensuring operational continuity and minimizing downtime. Enter CMMS, or Computerized Maintenance Management Systems — the technological backbone revolutionizing work order processes across industries.
CMMS software serves as a centralized hub, seamlessly integrating maintenance activities from scheduling to execution. Imagine it as a digital command center where maintenance managers, technicians, and stakeholders converge to streamline workflows. By digitizing work order management, CMMS eliminates the chaos of paperwork, empowering teams to focus on what matters most: proactive maintenance.
The impact of CMMS on work order processes is profound. Firstly, it enhances task prioritization by providing real-time visibility into asset health and maintenance history. This foresight allows teams to preemptively address potential issues, preventing costly breakdowns and downtime spikes. Secondly, CMMS automates routine tasks such as scheduling inspections and assigning work orders, freeing up valuable time for technicians to engage in more strategic activities.
Moreover, CMMS fosters accountability and transparency within maintenance operations. Through detailed analytics and reporting functionalities, managers gain actionable insights into performance metrics like mean time to repair (MTTR) and asset lifecycle costs. This data-driven approach not only optimizes resource allocation but also facilitates evidence-based decision-making for long-term maintenance strategies.
In essence, CMMS isn’t just a tool; it’s a catalyst for operational excellence. By digitizing and optimizing work order processes, it empowers maintenance teams to operate with agility, responsiveness, and efficiency. As industries evolve towards Industry 4.0 standards, CMMS stands as a testament to the transformative power of technology in enhancing productivity and sustaining competitive advantage.
Frequently Asked Questions
How does CMMS automation improve maintenance scheduling and asset uptime?
Learn how CMMS automation enhances maintenance scheduling and boosts asset uptime by streamlining tasks, ensuring timely inspections, and reducing downtime through predictive maintenance alerts.
What cost savings can be expected from using CMMS for work order automation?
Learn about the potential cost savings that can be achieved through CMMS (Computerized Maintenance Management System) for automating work orders.
How does CMMS automation enhance operational efficiency?
Discover how CMMS automation optimizes operational efficiency by streamlining maintenance tasks, reducing downtime, and enhancing asset management. Learn how automation improves workflow coordination and boosts productivity.
What are the key features to look for in a CMMS for automating work orders?
Discover the essential features to consider when choosing a CMMS for automating work orders. Learn how to streamline maintenance tasks efficiently and improve operational productivity.
What are the primary benefits of automating work orders with CMMS?
Discover the primary benefits of automating work orders with CMMS (Computerized Maintenance Management System), including streamlined workflows, improved asset reliability, enhanced maintenance scheduling, and increased operational efficiency.