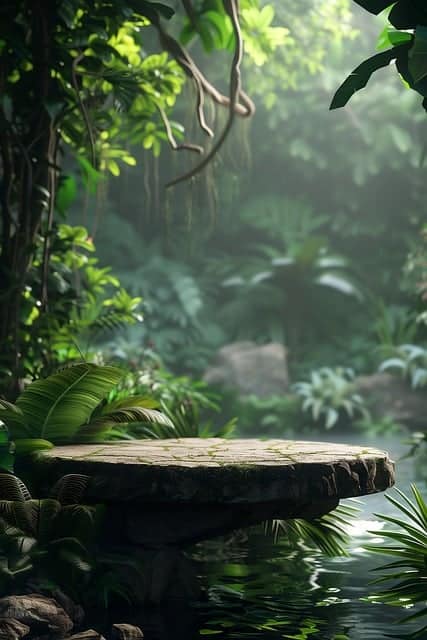
Imagine a smooth-running factory where every machine hums with efficiency, and downtime is as rare as a comet sighting. That’s the dream scenario for any manufacturing operation, and CMMS (Computerized Maintenance Management System) is the wizard behind the curtain making it all happen.
CMMS isn’t just another acronym in the tech jargon jungle; it’s the secret sauce that transforms reactive maintenance into proactive wizardry. By keeping a digital eye on every bolt and cog, CMMS predicts when maintenance is due before a breakdown even considers crashing the party. It’s like having a crystal ball that shows when and where issues might arise, allowing maintenance crews to swoop in like superheroes before things go haywire.
One of the most awe-inspiring feats of CMMS is its knack for slashing downtime. You know downtime, right? It’s that dreaded period where machines decide to take an impromptu nap, leaving workers twiddling thumbs and production goals hanging like ripe fruit just out of reach. CMMS turns those downtime nightmares into fairy tales of uninterrupted productivity. By scheduling maintenance during off-peak hours or when machines are least active, CMMS ensures that production keeps chugging along without a hitch.
But wait, there’s more! CMMS isn’t just about preventing breakdowns; it’s also a productivity powerhouse. Imagine if your factory floor were a well-choreographed dance, with machines pirouetting through tasks without missing a beat. CMMS keeps that rhythm going by optimizing workflows and ensuring that every minute of machine uptime counts towards your bottom line. It’s like having a maestro conducting a symphony of productivity, where every note (or in this case, every production cycle) hits its mark flawlessly.
In today’s hyper-competitive market, where downtime is the arch-nemesis of profit margins, CMMS isn’t just a luxury; it’s a lifeline. It’s the difference between watching your competitors zoom ahead while you struggle to catch up and leading the pack with a confident stride. So, if you’re still on the fence about embracing CMMS, ask yourself this: do you prefer to react to problems as they arise or stay ahead of the curve with a tool that anticipates and mitigates issues before they even knock on your door?
Maximizing Efficiency: How CMMS Systems Are Revolutionizing Productivity
Imagine this: your factory floor buzzing with activity, machines operating at peak efficiency, and maintenance tasks seamlessly scheduled and executed. This scenario is increasingly becoming a reality for businesses integrating CMMS systems into their operations. But what exactly is a CMMS?
At its core, a CMMS is a digital tool designed to simplify maintenance management by centralizing data, automating workflows, and optimizing maintenance schedules. Think of it as your digital assistant for all things maintenance-related, from scheduling routine inspections to tracking equipment downtime and managing work orders.
One of the key ways CMMS systems boost efficiency is by ensuring proactive maintenance rather than reactive firefighting. Instead of waiting for equipment to break down, which can lead to costly downtime and repairs, CMMS allows maintenance teams to schedule preventive maintenance tasks based on actual usage data and manufacturer recommendations.
Moreover, CMMS systems enhance communication and collaboration among maintenance teams. Through real-time updates and mobile accessibility, technicians can promptly report issues, access manuals or schematics, and receive instant notifications about critical maintenance tasks.
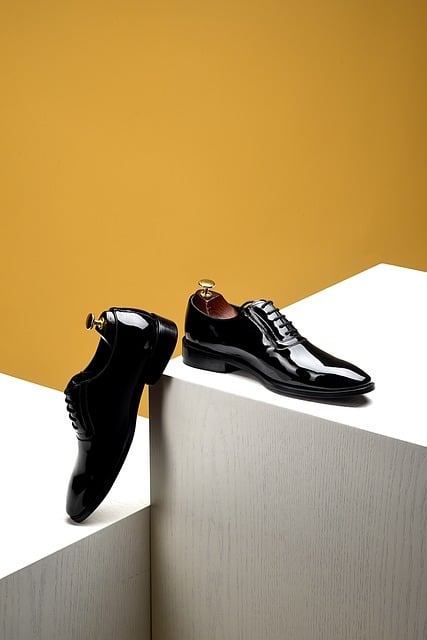
In terms of productivity, CMMS systems provide invaluable insights through detailed analytics and reporting functionalities. Managers can analyze maintenance trends, identify recurring issues, and make data-driven decisions to optimize equipment performance and overall operational efficiency.
Cutting Costs and Boosting Output: The Role of CMMS in Industrial Success
Imagine this: your factory floor humming with productivity, machines working at peak performance, and downtime reduced to a minimum. That’s the promise of CMMS. But what exactly is CMMS? It’s like having a digital assistant for maintenance, streamlining everything from equipment monitoring to scheduling repairs.
One of the biggest headaches in any industry is unexpected breakdowns. They not only halt production but also come with hefty repair costs. CMMS acts as a proactive shield against these issues. By scheduling regular maintenance checks and alerting you to potential problems early, it prevents breakdowns before they even occur. This predictive maintenance approach not only saves money but also ensures that your production lines keep rolling smoothly.
Moreover, CMMS isn’t just about reacting to problems—it’s about optimizing every aspect of your operations. It tracks asset performance over time, identifying trends and patterns that can help you fine-tune your processes. This data-driven approach empowers decision-making, allowing you to allocate resources more efficiently and optimize your maintenance budgets.
Think of CMMS as the conductor of an orchestra, harmonizing different parts of your operation to create a symphony of efficiency. From managing inventory to tracking work orders, it handles the nitty-gritty details so that you can focus on the big picture—driving your business forward.
Streamlining Operations: CMMS Tools That Minimize Downtime
CMMS tools are like the behind-the-scenes heroes of many industries, quietly ensuring that equipment and machinery are in top-notch condition, thereby reducing downtime. But how exactly do they do this? Let’s break it down.
Firstly, CMMS tools centralize maintenance operations. They provide a single platform where you can schedule and track maintenance tasks across all your equipment. This means no more juggling between different spreadsheets or missing out on crucial inspections. Everything is neatly organized and accessible with just a few clicks.
Secondly, preventive maintenance is where CMMS tools truly shine. Instead of waiting for something to break down (and causing unexpected downtime), these tools allow you to set up regular maintenance schedules based on equipment usage or manufacturer recommendations. It’s like giving your machinery a regular check-up to catch any potential issues before they escalate into costly problems.
Moreover, CMMS tools streamline communication within your maintenance team. Assigning tasks, updating progress, and sharing important information become effortless. This not only improves efficiency but also ensures that everyone is on the same page, working towards minimizing downtime collectively.
Imagine if your business were a professional athlete. You wouldn’t wait for an injury to occur before taking care of your body, right? You’d have a rigorous training schedule and regular check-ups to stay in top form. CMMS tools work similarly for your equipment—they keep everything in peak condition so that your operations can perform at their best without interruptions.
Integrating CMMS tools into your operations isn’t just about reducing downtime; it’s about optimizing efficiency and ensuring that your business runs like a well-oiled machine. So, why wait for downtime to disrupt your operations when you can proactively manage maintenance and keep everything running smoothly?
From Maintenance to Mastery: CMMS Software’s Impact on Workplace Efficiency
By streamlining maintenance processes, CMMS software helps organizations operate like well-oiled machines. It eliminates the chaos of manual systems, where maintenance schedules could be overlooked or assets mismanaged. Instead, CMMS automates these tasks, ensuring that every piece of equipment receives timely maintenance, reducing downtime and prolonging asset lifespan.
Moreover, CMMS software empowers teams with data-driven insights. It collects valuable information on asset history, maintenance costs, and performance trends. This data isn’t just numbers; it’s actionable intelligence that guides decision-making. For instance, predictive maintenance capabilities allow teams to anticipate issues before they occur, preventing costly breakdowns and unplanned downtime.
In the realm of inventory management, CMMS software brings order to chaos. It tracks spare parts and supplies in real-time, ensuring that technicians have the right resources at the right time. This efficiency not only saves costs but also boosts productivity by minimizing wait times for repairs.
Furthermore, CMMS fosters accountability and transparency within teams. With clear workflows and automated notifications, everyone knows their roles and responsibilities. Tasks are prioritized, deadlines are met, and communication flows smoothly—like a symphony orchestrated for maximum efficiency.
In essence, CMMS software isn’t just a tool; it’s a catalyst for workplace mastery. It transforms how organizations manage maintenance, turning what was once a reactive, labor-intensive process into a proactive, streamlined operation. With CMMS, businesses can focus on what matters most—delivering quality products and services while maximizing operational efficiency.
Frequently Asked Questions
What industries benefit most from implementing CMMS solutions?
Industries that benefit most from implementing CMMS (Computerized Maintenance Management Systems) solutions include manufacturing, healthcare, facilities management, transportation, and energy. These systems optimize maintenance processes, reduce downtime, extend asset lifespan, and enhance operational efficiency.
How can CMMS software enhance productivity in industrial settings?
Learn how CMMS software boosts productivity in industrial settings by streamlining maintenance tasks, reducing downtime, optimizing asset management, and improving overall operational efficiency.
How does preventive maintenance through CMMS prevent unexpected downtime?
Learn how preventive maintenance using CMMS helps prevent unexpected downtime by scheduling regular inspections and repairs, ensuring equipment reliability and minimizing costly disruptions.
What are the key features of CMMS systems that improve operational efficiency?
Discover how CMMS systems enhance operational efficiency with features like preventive maintenance scheduling, asset management, real-time reporting, and workflow automation. These tools streamline maintenance processes, reduce downtime, optimize resource allocation, and ensure regulatory compliance.
What is CMMS and how does it reduce downtime?
Learn about CMMS (Computerized Maintenance Management System), a software solution used to streamline maintenance operations. Discover how CMMS helps reduce downtime by enabling proactive maintenance scheduling, efficient resource allocation, and timely equipment inspections. By automating workflows and providing real-time insights, CMMS minimizes unplanned downtime, enhances equipment reliability, and improves overall operational efficiency.