During times of crisis, the efficiency and resilience of operational management become paramount. CMMS (Computerized Maintenance Management System) plays a pivotal role in ensuring businesses can navigate through challenges effectively. By integrating maintenance, scheduling, and resource management into a centralized platform, CMMS enables proactive crisis management strategies.
CMMS serves as a vital tool by providing real-time insights into asset performance and maintenance needs. This proactive approach helps preemptively identify potential issues before they escalate, thus minimizing downtime during critical situations. Imagine it as the vigilant guardian of operational continuity, constantly monitoring and optimizing workflows to keep systems running smoothly.
In the midst of a crisis, every minute counts. CMMS streamlines communication and coordination between teams, ensuring everyone is on the same page regarding asset availability, maintenance schedules, and resource allocation. This clarity enables swift decision-making and effective deployment of resources where they are most needed.
Moreover, CMMS enhances data-driven decision-making by providing comprehensive historical data and predictive analytics. By analyzing past performance trends and anticipating future needs, businesses can proactively adjust their strategies to mitigate risks and optimize operational efficiency even under challenging circumstances.
In essence, CMMS transforms crisis management from reactive firefighting to proactive resilience-building. It empowers organizations to maintain operational continuity, uphold service levels, and safeguard against disruptions. Like a conductor orchestrating a symphony, CMMS harmonizes maintenance efforts, resource allocation, and data insights to ensure businesses not only survive but thrive amidst adversity.
This article highlights the proactive role of CMMS in crisis management, emphasizing its ability to enhance operational resilience and maintain efficiency during challenging times.
Navigating Turbulent Waters: How CMMS Systems Ensure Operational Stability During Crises
In times of crisis, maintaining operational stability is crucial for businesses to weather the storm and emerge resilient. CMMS (Computerized Maintenance Management System) systems play a pivotal role in achieving this goal by providing robust tools to streamline maintenance operations and enhance overall efficiency.
During turbulent times such as economic downturns or global pandemics, businesses face unprecedented challenges that can disrupt normal operations. Here’s where CMMS systems shine: they enable organizations to proactively manage their assets, resources, and maintenance activities with precision and foresight.
One of the key benefits of CMMS systems during crises is their ability to centralize maintenance management. By digitizing workflows and storing critical data in a unified platform, CMMS systems eliminate the inefficiencies of manual processes and paperwork. This centralized approach not only improves communication and collaboration but also ensures that maintenance tasks are prioritized based on urgency and impact on operations.
Moreover, CMMS systems provide real-time insights into asset performance and maintenance needs. Through predictive analytics and condition monitoring capabilities, businesses can anticipate potential equipment failures before they occur. This proactive maintenance strategy not only minimizes downtime but also extends the lifespan of assets, optimizing operational costs during turbulent periods.
Another significant advantage of CMMS systems is their role in regulatory compliance and risk management. By maintaining comprehensive maintenance records and audit trails, businesses can demonstrate compliance with industry standards and regulations even amidst crises. This capability not only reduces the risk of fines and penalties but also enhances organizational credibility and trust among stakeholders.
Furthermore, CMMS systems empower decision-makers with data-driven insights. By analyzing historical maintenance data and performance metrics, businesses can make informed decisions regarding resource allocation, budget planning, and strategic initiatives. This analytical approach fosters agility and adaptability, enabling businesses to navigate uncertainties and emerge stronger.
Critical Tools: Leveraging CMMS for Effective Crisis Response in Operations
Imagine a scenario where a manufacturing plant suddenly faces equipment failure amidst a crucial production deadline. In such moments, every minute counts. A well-integrated CMMS allows maintenance teams to instantly access detailed equipment records, maintenance histories, and operational data. This quick access empowers them to diagnose issues promptly and initiate necessary repairs without delay.
Moreover, CMMS platforms are designed to streamline communication and collaboration across departments. During crises, clear communication is essential for coordinating efforts and making informed decisions. CMMS provides a centralized platform where stakeholders can communicate in real-time, share updates, and track progress. This collaborative approach ensures that everyone involved is on the same page, minimizing confusion and maximizing efficiency.
Another significant advantage of CMMS in crisis response is its capability to generate actionable insights through data analytics. By analyzing historical maintenance data and real-time performance metrics, CMMS can predict potential failures before they occur. This proactive approach not only prevents crises but also optimizes resource allocation and reduces operational downtime.
Furthermore, CMMS enhances transparency and accountability within organizations. It tracks every maintenance activity, from work orders to inventory management, ensuring compliance with regulatory standards and operational best practices. This transparency fosters a culture of accountability where each team member understands their role in crisis management and strives towards collective goals.
In essence, leveraging CMMS for effective crisis response in operations is more than just a technological upgrade—it’s a strategic investment in resilience and agility. By integrating CMMS into daily operations, businesses can navigate crises with confidence, minimize disruptions, and maintain their competitive edge in an unpredictable market landscape.
CMMS: The Silent Hero in Crisis Management for Industrial Operations
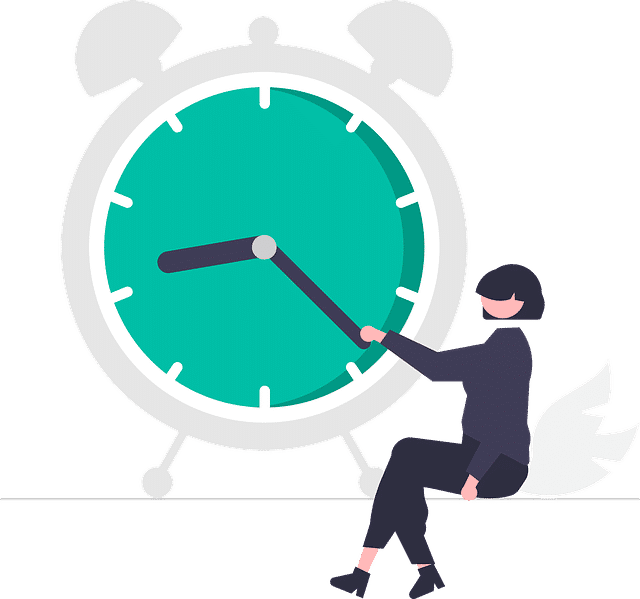
Imagine a factory floor suddenly experiencing equipment failure. In such moments, time is of the essence. CMMS steps in, swiftly pinpointing the issue, analyzing historical data, and streamlining the repair process. It acts as a virtual guardian, preemptively flagging potential failures before they escalate, saving not just time but crucial resources.
In the throes of a crisis, clarity is paramount. CMMS provides a centralized platform where every detail, from maintenance logs to inventory levels, is readily accessible. This accessibility ensures that decisions are informed and swift, minimizing downtime and maximizing productivity.
Moreover, CMMS doesn’t just react—it anticipates. Like a seasoned detective, it tracks trends over time, identifying patterns that could signal impending issues. This proactive approach transforms crisis management from reactive firefighting to a strategic, preemptive endeavor.
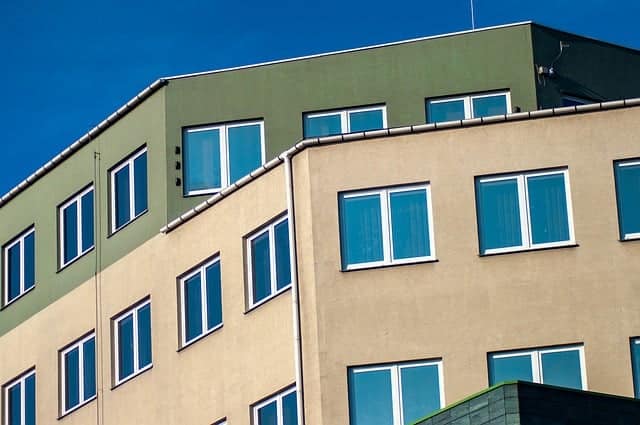
But CMMS isn’t solely about efficiency; it’s about resilience. In today’s volatile market landscape, industries must be agile and adaptive. CMMS empowers organizations to weather storms, ensuring that operations continue seamlessly even amidst adversity.
In essence, CMMS is the silent hero in crisis management for industrial operations, silently orchestrating behind the scenes to ensure that disruptions are minimized, efficiency is optimized, and resilience becomes the norm. As industries evolve, CMMS stands as a testament to the power of technology in safeguarding the backbone of our economy.
From Chaos to Control: Harnessing CMMS to Safeguard Operational Continuity
CMMS software acts as the nerve center of maintenance operations, streamlining workflows, and ensuring that every component of your facility functions at peak performance. It’s like having a digital assistant dedicated to keeping your operations smooth and uninterrupted.
One of the standout features of CMMS is its ability to schedule preventive maintenance tasks. Instead of waiting for equipment to break down, CMMS allows you to proactively schedule inspections, lubrications, and part replacements based on usage data and manufacturer recommendations. This proactive approach not only extends the lifespan of your equipment but also minimizes unexpected breakdowns that can disrupt production.
Moreover, CMMS provides real-time insights into maintenance activities. Managers and technicians can track work orders, monitor inventory levels, and analyze historical data to identify trends or recurring issues. This data-driven approach empowers decision-making, allowing teams to allocate resources effectively and optimize maintenance strategies.
Imagine the impact of having all this information at your fingertips: reduced downtime, increased productivity, and enhanced safety across your facility. CMMS ensures that every aspect of your maintenance operations is synchronized and well-coordinated, paving the way for operational excellence.
In essence, CMMS transforms the chaos of reactive maintenance into the control of proactive management. It’s like having a skilled conductor orchestrating a symphony, where each instrument plays harmoniously to achieve a flawless performance. By harnessing CMMS, businesses can safeguard their operational continuity, adapt to challenges swiftly, and stay ahead in today’s competitive market.
Harness the power of CMMS today and witness firsthand how it turns operational chaos into streamlined control, ensuring your facility operates like a well-oiled machine.
Ensuring Business Resilience: The Strategic Importance of CMMS in Crisis Scenarios
CMMS software acts as a comprehensive solution for managing maintenance activities, from scheduling tasks to tracking equipment performance. During crises, such as natural disasters or economic downturns, businesses face heightened pressure to optimize resources and minimize downtime. Here, CMMS shines by providing real-time insights into asset health and maintenance needs.
Imagine a ship navigating through a stormy sea. CMMS serves as the compass, guiding businesses through turbulent times by facilitating proactive maintenance planning and asset management. By centralizing data on equipment conditions and maintenance histories, CMMS enables timely interventions that prevent costly breakdowns and ensure uninterrupted operations.
Moreover, CMMS enhances decision-making by offering predictive analytics and reporting functionalities. Like a weather forecast predicting storm patterns, CMMS forecasts potential equipment failures and resource requirements, empowering businesses to strategize effectively. This foresight allows organizations to allocate resources wisely, optimize inventory levels, and maintain service levels even under duress.
In essence, CMMS isn’t merely a tool; it’s a strategic asset that bolsters business resilience. By streamlining maintenance workflows and fostering a proactive approach, CMMS enables businesses to weather uncertainties with confidence. It transforms crisis scenarios into opportunities for growth and operational excellence, ensuring that businesses not only survive but thrive in challenging environments.
For businesses navigating today’s unpredictable terrain, embracing CMMS isn’t just prudent; it’s essential. It’s the difference between being swept away by the storm and emerging stronger, more resilient, and ready for whatever comes next.
Emergency Preparedness Redefined: The Vital Role of CMMS in Operational Crisis Management
Imagine your company as a ship navigating stormy seas. Without warning, a critical machine fails, threatening to derail your entire production line. In such moments, every second counts. CMMS acts as your reliable compass, guiding you through the turbulence with its proactive maintenance scheduling and real-time monitoring capabilities.
CMMS is not just about fixing things when they break; it’s about preventing breakdowns before they happen. By meticulously tracking equipment performance and maintenance histories, CMMS empowers organizations to detect potential issues early on. It’s like having a skilled lookout who spots trouble on the horizon and alerts the crew well in advance.
Moreover, CMMS transforms crisis response into a well-oiled machine. Imagine firefighters equipped not only with hoses but also with precise blueprints of the building they’re entering. Similarly, CMMS equips maintenance teams with detailed asset information and predefined workflows, ensuring they respond swiftly and effectively to any emergency.
In the realm of operational crisis management, preparation is paramount. CMMS allows businesses to create tailored maintenance plans and contingency protocols tailored to their unique needs and challenges. It’s like having a personalized emergency kit stocked with exactly what you need, precisely when you need it.
Integrating CMMS into your crisis management strategy isn’t just about being prepared—it’s about redefining what preparedness looks like in the 21st century. It’s about leveraging technology to turn potential disasters into manageable challenges. Whether you’re in manufacturing, healthcare, or hospitality, CMMS stands as a testament to the power of foresight and proactive maintenance.
Real-Time Insights: How CMMS Enhances Decision-Making During Operational Disruptions
Imagine your facility facing unexpected downtime due to equipment failure. In such critical moments, having real-time data at your fingertips can make all the difference. CMMS provides a comprehensive view of equipment health, maintenance histories, and ongoing work orders. This wealth of information allows managers to swiftly assess the situation, prioritize tasks, and allocate resources efficiently.
Unlike traditional methods reliant on manual records or sporadic updates, CMMS offers a dynamic dashboard that updates in real-time. It’s like having a control tower overseeing every aspect of your facility’s operational health. Managers can track performance metrics, monitor inventory levels, and instantly spot emerging issues before they escalate into full-blown disruptions.
Moreover, CMMS doesn’t just react to disruptions; it helps prevent them altogether through predictive maintenance. By analyzing historical data and performance trends, these systems can forecast potential failures, prompting proactive interventions. It’s akin to having a weather forecast that predicts storms before they hit, allowing you to reinforce your defenses well in advance.
The beauty of CMMS lies in its ability to integrate with other business systems seamlessly. Whether it’s syncing with Enterprise Resource Planning (ERP) software or linking up with Internet of Things (IoT) devices, CMMS ensures that decision-makers have a holistic view of operations. This interconnectedness fosters a proactive rather than reactive approach to managing disruptions, turning challenges into opportunities for optimization.
Frequently Asked Questions
What are the best practices for integrating CMMS into crisis response strategies?
Learn about the optimal methods for incorporating CMMS into crisis response strategies, ensuring efficient maintenance operations and swift resolution during emergencies.
How does CMMS enhance decision-making during emergencies?
Learn how CMMS (Computerized Maintenance Management System) improves decision-making in emergencies by providing real-time data on equipment status, maintenance history, and resource availability. This proactive approach minimizes downtime, optimizes resource allocation, and ensures rapid response to critical situations.
How can CMMS systems help maintain operational continuity during crises?
Discover how CMMS systems contribute to maintaining operational continuity during crises. Learn how these systems streamline maintenance tasks, prioritize critical repairs, and ensure equipment reliability, reducing downtime and operational disruptions.
What are the key features to look for in a CMMS for crisis management?
Discover essential features to prioritize when selecting a CMMS for crisis management. Learn how to optimize maintenance operations efficiently.
What is CMMS and how does it aid in crisis management for operations?
Learn how CMMS (Computerized Maintenance Management System) supports crisis management by enhancing operational efficiency, ensuring timely maintenance of critical assets, and facilitating quick response to emergencies through automated workflows and real-time data insights.