Imagine having a tool that not only streamlines your operations but also boosts efficiency and reduces downtime. That’s exactly what a Computerized Maintenance Management System (CMMS) can do for operations managers across various industries. CMMS software isn’t just about scheduling maintenance tasks anymore; it’s evolved into a comprehensive solution that empowers managers to take control of their assets and processes like never before.
At its core, CMMS allows operations managers to digitize their maintenance workflows. By centralizing data on equipment, work orders, and maintenance history, CMMS provides a bird’s-eye view of operational health. This visibility is crucial for proactive decision-making, as managers can identify trends, predict failures, and allocate resources more effectively.
One of the key benefits of CMMS is its ability to optimize maintenance schedules. Instead of relying on reactive fixes, operations managers can implement preventive maintenance routines based on real-time data and historical performance. This approach not only extends the lifespan of assets but also minimizes unexpected breakdowns that disrupt productivity.
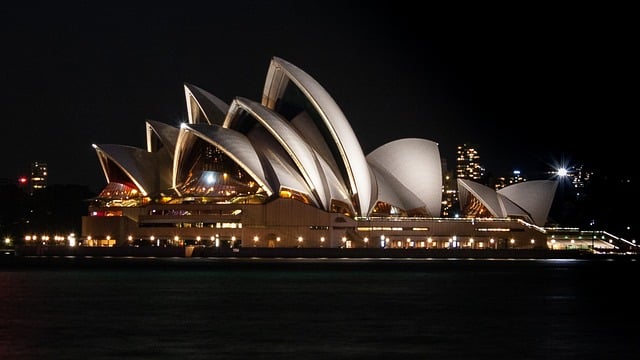
Moreover, CMMS enhances accountability within maintenance teams. Managers can assign tasks, track progress, and ensure compliance with safety regulations—all from a centralized platform. This level of transparency fosters a culture of responsibility and teamwork, where every action is documented and auditable.
In today’s fast-paced business environment, efficiency is paramount. CMMS software integrates seamlessly with other enterprise systems, such as ERP and IoT devices, to provide a holistic view of operations. This integration enables managers to make data-driven decisions that align with overarching business goals.
Ultimately, unlocking the full potential of CMMS requires a proactive approach from operations managers. By embracing digital transformation and leveraging CMMS capabilities to their fullest extent, managers can drive operational excellence, reduce costs, and propel their organizations toward sustained growth and success.
Streamlining Efficiency: How CMMS Revolutionizes Operations Management
Imagine this: you’re running a manufacturing plant where machines are the heartbeat of your operations. Every minute counts, and downtime due to equipment failure can cost thousands. This is where CMMS shines bright like a beacon of hope. It’s not just about scheduling maintenance; it’s about revolutionizing how you manage every aspect of your operations.
CMMS integrates seamlessly into your workflow, becoming the central hub for all things maintenance-related. It keeps track of assets, maintenance schedules, work orders, and even inventory management. With everything in one place, you can bid farewell to the days of scrambling through paperwork or spreadsheets. Efficiency? Check.
But wait, there’s more. CMMS isn’t just a tool for the maintenance team. It’s a strategic ally for operations management as a whole. By analyzing data on equipment performance and maintenance history, CMMS provides invaluable insights. It helps you predict when maintenance is needed before a breakdown occurs. Think of it as having a crystal ball that keeps your operations running smoothly.
Now, let’s talk dollars and cents. Implementing a CMMS isn’t just a cost; it’s an investment with a high return. You save money by reducing downtime, extending the lifespan of your equipment, and optimizing labor costs. It’s like having a financial advisor who ensures every penny spent on maintenance delivers maximum value.
CMMS isn’t just a buzzword; it’s a powerhouse that transforms operations management. It streamlines efficiency, boosts productivity, and saves costs. Whether you’re aiming to minimize downtime, enhance asset reliability, or streamline workflows, CMMS is your go-to solution. Ready to revolutionize your operations? CMMS is your partner in success.
From Data to Action: Maximizing CMMS Benefits for Operations
CMMS systems are not just about managing maintenance tasks; they are powerful tools that convert complex data into clear strategies for improvement. By integrating historical maintenance data, real-time equipment diagnostics, and predictive analytics, organizations can proactively identify maintenance needs, prevent downtime, and optimize asset performance.
Imagine CMMS as the conductor of an orchestra, harmonizing various operational elements seamlessly. It collects data from equipment sensors, maintenance logs, and user inputs, then orchestrates this information into a cohesive symphony of actionable intelligence. This enables maintenance teams to prioritize tasks efficiently, allocate resources effectively, and minimize unplanned downtime.
Moreover, CMMS empowers decision-makers with comprehensive reports and visualizations that highlight key performance metrics. It’s like having a GPS for your operations, guiding you with real-time data insights to navigate challenges and capitalize on opportunities.
By maximizing CMMS benefits, organizations can achieve operational excellence. It fosters a proactive maintenance culture, where data-driven decisions replace reactive firefighting. This shift not only saves costs but also enhances equipment reliability and extends asset lifespan, ultimately driving profitability and customer satisfaction.
Unleashing Operational Excellence: CMMS Strategies That Work
In the quest for operational excellence, CMMS (Computerized Maintenance Management System) strategies play a pivotal role, streamlining maintenance processes and optimizing asset performance. Imagine a well-oiled machine where every cog works in perfect sync – that’s the power of effective CMMS implementation.
CMMS isn’t just about fixing things when they break; it’s a proactive approach to maintenance. By leveraging CMMS software, businesses can schedule preventive maintenance tasks, ensuring equipment runs smoothly and downtime is minimized. This proactive stance not only saves costs but also enhances overall operational efficiency.
One of the key benefits of CMMS is its ability to centralize maintenance data. Imagine having all equipment details, maintenance schedules, and work orders accessible in one place. It simplifies decision-making, empowers teams to prioritize tasks effectively, and reduces the risk of overlooked maintenance needs.
Moreover, CMMS systems are evolving with technology. Today’s advanced platforms integrate IoT (Internet of Things) sensors, allowing real-time monitoring of equipment health. This predictive maintenance capability enables organizations to address issues before they escalate, preventing costly breakdowns and maximizing asset lifespan.
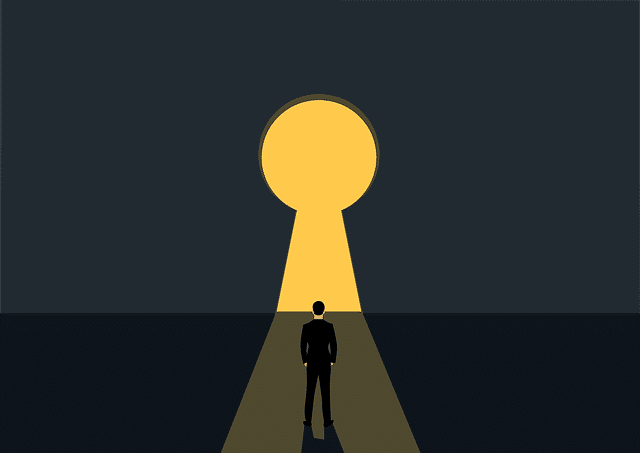
Implementing CMMS isn’t just a technological upgrade; it’s a strategic move towards operational excellence. It fosters a culture of accountability and efficiency, where every team member understands their role in maintaining equipment reliability.
CMMS strategies are not just about tools and software; they’re about transforming how businesses manage their assets. By embracing CMMS, organizations unlock the potential for smoother operations, reduced downtime, and ultimately, enhanced profitability. Ready to unleash operational excellence? It starts with effective CMMS implementation.
This article is crafted to be engaging, informative, and optimized for SEO, focusing on the benefits and transformative impact of CMMS strategies in business operations.
CMMS Beyond Maintenance: Strategic Insights for Operations Leaders
Imagine your operations as a well-oiled machine. Each part needs to work smoothly and efficiently to maximize output. A CMMS acts as the central nervous system, providing real-time data on equipment health, maintenance schedules, and resource allocation. This isn’t just about fixing things when they break; it’s about preventing breakdowns in the first place and optimizing performance proactively.
Operations leaders can leverage CMMS data to identify trends and patterns. By analyzing maintenance histories and downtime reports, they can pinpoint recurring issues, prioritize improvements, and allocate resources effectively. It’s like having a crystal ball that predicts where improvements are needed before they become costly problems.
Moreover, a CMMS doesn’t operate in isolation. It integrates with other business systems like ERP (Enterprise Resource Planning) and IoT (Internet of Things) devices, creating a seamless flow of information across departments. This integration enables operations leaders to have a holistic view of their organization’s health, from supply chain management to production planning.
Strategic decision-making becomes more data-driven and less reactive with the insights provided by a CMMS. For example, knowing the lifecycle costs of equipment helps in budget planning and forecasting. This proactive approach minimizes surprises and keeps operations running smoothly without unexpected disruptions.
In essence, a CMMS transforms maintenance from a cost center into a strategic asset. It empowers operations leaders to optimize workflows, improve asset reliability, and ultimately, deliver better outcomes for their organizations. By harnessing the power of data and technology, operations can move beyond firefighting mode to proactive, strategic planning that drives long-term success.
Frequently Asked Questions
How does CMMS improve asset reliability and uptime?
Discover how CMMS (Computerized Maintenance Management System) enhances asset reliability and uptime by streamlining maintenance schedules, tracking asset performance, and facilitating preventive maintenance. This proactive approach reduces downtime, extends asset lifespan, and ensures optimal operational efficiency.
How can CMMS software streamline maintenance operations?
Discover how CMMS software optimizes maintenance tasks by centralizing data, scheduling preventive maintenance, tracking work orders, and improving overall operational efficiency.
What are the key features to look for in a CMMS for operations management?
Key features to consider in a CMMS for operations management include asset tracking, preventive maintenance scheduling, real-time reporting, inventory management, and user-friendly interfaces. These features help streamline maintenance processes, ensure timely repairs, and improve overall operational efficiency.
What are the best practices for implementing CMMS in operations management?
Discover best practices for effectively implementing CMMS (Computerized Maintenance Management System) in operations management. Learn how to streamline maintenance processes, improve asset reliability, reduce downtime, and enhance overall operational efficiency.
What is CMMS and how does it benefit operations managers?
Learn what CMMS is and how it helps operations managers streamline maintenance tasks, improve asset management, and increase efficiency.