In the realm of facility management, staying ahead of challenges is key to ensuring smooth operations and optimal efficiency. One powerful tool that has revolutionized how facilities are managed is Computerized Maintenance Management Systems (CMMS). These systems are not just software; they’re game-changers.
CMMS helps facility managers tackle a myriad of common challenges with precision and effectiveness. One of the most significant benefits is preventive maintenance. By scheduling regular inspections and repairs before equipment fails, CMMS helps avoid costly downtime and repairs. Imagine having the ability to predict and prevent breakdowns before they occur, saving both time and money.
Moreover, CMMS enhances asset management by providing a centralized database of all equipment and assets. This means managers can easily track each asset’s lifecycle, from acquisition to retirement, ensuring optimal usage and minimal wastage. It’s like having a digital fingerprint for every piece of equipment, ensuring accountability and efficiency.
Another critical area where CMMS shines is in inventory management. No more overstocking or running out of essential supplies at crucial times. CMMS enables real-time tracking of inventory levels and automates reordering processes, ensuring that stock levels are always optimized without manual intervention.
Furthermore, CMMS facilitates streamlined work order management. Instead of relying on paper-based systems or emails, work orders can be created, assigned, and tracked digitally. This improves communication, reduces paperwork, and speeds up response times for maintenance requests.
In essence, CMMS transforms facility management by providing tools that empower managers to proactively handle challenges. Whether it’s preventing equipment failures, optimizing asset usage, managing inventory efficiently, or improving workflow processes, CMMS is the backbone that supports operational excellence.
Streamlining Operations: How CMMS Revolutionizes Facility Management
CMMS software acts as a centralized hub where all maintenance-related information can be stored and accessed. It integrates various functionalities such as asset management, work order management, preventive maintenance scheduling, and inventory control. By digitizing these processes, CMMS eliminates the need for cumbersome paperwork and manual tracking, thereby reducing errors and improving overall productivity.
Facility managers can now monitor equipment performance in real-time, enabling proactive maintenance rather than reactive fixes. This proactive approach minimizes downtime, extends asset lifespan, and reduces operational costs. Imagine a facility where equipment issues are anticipated and resolved before they escalate – that’s the power of CMMS.
Moreover, CMMS empowers decision-making by providing insightful data analytics and reports. Managers can analyze maintenance trends, identify areas for improvement, and allocate resources more effectively. It’s like having a crystal ball that forecasts maintenance needs and guides strategic planning.
Implementing CMMS isn’t just about adopting new software; it’s about embracing a culture of efficiency and continuous improvement. It fosters collaboration among maintenance teams, streamlines communication, and enhances transparency across all levels of the organization. Think of it as laying a solid foundation for operational excellence – where every task is streamlined, every resource is optimized, and every goal is within reach.
Maximizing Efficiency: CMMS Solutions for Modern Facility Challenges
CMMS solutions offer a centralized platform where facility managers can track and schedule maintenance tasks, monitor equipment performance, and manage work orders efficiently. By integrating preventive maintenance schedules, CMMS helps facilities avoid costly breakdowns and reduce downtime, thus improving overall operational efficiency.
Imagine CMMS as the conductor of an orchestra, harmonizing all the elements of facility management. Like a skilled conductor guides each musician to play their part at the right time, CMMS coordinates maintenance activities and asset management seamlessly. It ensures that every piece of equipment is maintained at optimal performance levels, just as a conductor ensures each musical instrument produces the right notes.
Moreover, CMMS solutions provide real-time insights and analytics, enabling managers to make data-driven decisions. This capability is akin to a GPS navigator that guides you through the best route, helping facility managers navigate challenges and allocate resources effectively.
In today’s fast-paced business environment, where every minute counts, CMMS solutions act as the backbone of efficient facility management. They empower organizations to stay proactive rather than reactive, fostering a culture of productivity and reliability.
By leveraging CMMS solutions, modern facilities not only enhance operational efficiency but also extend the lifespan of their assets and improve compliance with regulatory standards. This proactive approach ensures that facilities can meet customer demands consistently, just like a well-tuned engine powering ahead smoothly on a long journey.
In essence, CMMS solutions are more than just software; they are transformative tools that elevate facility management to new heights of efficiency and reliability.
From Downtime to Uptime: CMMS Tools Transform Facility Maintenance
CMMS tools are like the Swiss Army knives of maintenance management. They streamline workflows, track assets, schedule preventive maintenance, and manage work orders efficiently. Think of them as your proactive assistant, always on the lookout for potential issues before they escalate into costly downtime.
One of the standout features of CMMS tools is their ability to schedule preventive maintenance tasks. Instead of waiting for equipment to fail, which can lead to unplanned downtime, these systems allow maintenance teams to stay ahead of the curve. They automatically generate work orders based on predefined schedules or meter readings, ensuring that equipment is serviced at optimal intervals.
Moreover, CMMS tools provide comprehensive asset management capabilities. Every piece of equipment in a facility can be logged into the system, along with crucial details such as maintenance history, warranties, and spare part inventories. This not only improves maintenance planning but also enhances inventory management efficiency.
In addition to preventive maintenance and asset management, CMMS tools offer robust reporting and analytics. They capture data on maintenance activities, downtime incidents, and asset performance metrics. This data can then be analyzed to identify trends, optimize maintenance strategies, and make data-driven decisions for continuous improvement.
Furthermore, these tools are accessible via desktops, laptops, and even mobile devices, enabling maintenance teams to manage tasks on the go. Imagine a technician receiving a real-time alert on their smartphone about an urgent equipment issue, complete with instructions and historical data to diagnose and resolve the problem swiftly.
Cost Savings Unveiled: The Financial Impact of CMMS in Facility Management
Ever wondered how facility managers streamline operations while saving costs effortlessly? Enter CMMS, the unsung hero behind efficient facility management. Let’s unveil the financial impact of CMMS and how it revolutionizes cost savings in managing facilities.
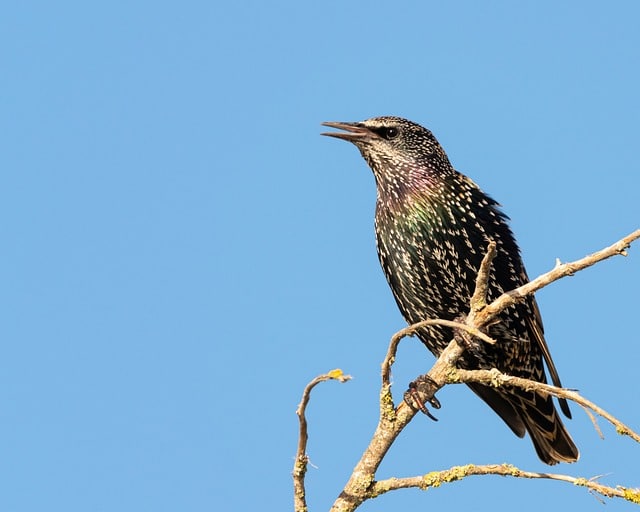
CMMS, short for Computerized Maintenance Management System, is a game-changer in the realm of facility management. Imagine having a tool that schedules maintenance tasks, tracks assets, manages work orders, and optimizes inventory—all from a centralized platform. It’s like having a super-organized toolkit that anticipates your facility’s needs before they even arise.
One of the most significant financial benefits of CMMS lies in preventive maintenance. Instead of waiting for equipment to fail and incurring hefty repair costs, CMMS schedules regular upkeep. This proactive approach not only prolongs the lifespan of assets but also prevents costly breakdowns. Think of it as regularly servicing your car to avoid a major engine failure down the road.
Furthermore, CMMS enhances labor productivity. By automating routine tasks and minimizing downtime, your facility operates like a well-oiled machine. Technicians spend less time reacting to emergencies and more time on value-adding activities. It’s akin to having a skilled orchestra conductor who ensures every player performs their best without missing a beat.
Moreover, CMMS provides invaluable insights through data analytics. Managers can analyze maintenance trends, identify inefficiencies, and make data-driven decisions to optimize resources. It’s like having a crystal ball that predicts where to invest resources wisely, ensuring every penny counts towards improving facility performance.
CMMS isn’t just a tool; it’s a financial wizard that transforms facility management. By embracing CMMS, facilities can achieve significant cost savings, boost operational efficiency, and prolong asset life—all while ensuring smooth sailing without unexpected financial storms.
Preventive Power: Harnessing CMMS for Proactive Facility Maintenance
Imagine your facility as a well-oiled machine, running smoothly day in and day out without a hitch. How is this possible? The secret lies in harnessing the power of CMMS (Computerized Maintenance Management System) for proactive facility maintenance.
CMMS isn’t just another acronym in the world of facility management; it’s a game-changer. Think of it as your facility’s digital brain, constantly monitoring, analyzing, and predicting maintenance needs before they become problems. By integrating CMMS into your operations, you shift from reactive firefighting to proactive planning.
One of the standout features of CMMS is its preventive maintenance capabilities. Instead of waiting for equipment to break down and disrupt operations, CMMS allows you to schedule regular maintenance tasks based on data-driven insights. This proactive approach not only extends the lifespan of your assets but also minimizes unexpected downtime, saving you both time and money in the long run.
Moreover, CMMS empowers your maintenance team by streamlining workflows and optimizing resource allocation. Tasks are prioritized based on urgency and criticality, ensuring that your team focuses on what matters most at any given time. This efficiency boost translates into improved productivity and happier tenants or employees who rely on your facility’s uninterrupted functionality.
In essence, CMMS is more than just a tool; it’s a strategic asset in your facility management arsenal. By embracing its preventive power, you transform your maintenance operations from reactive to proactive, paving the way for smoother operations and reduced costs over time.
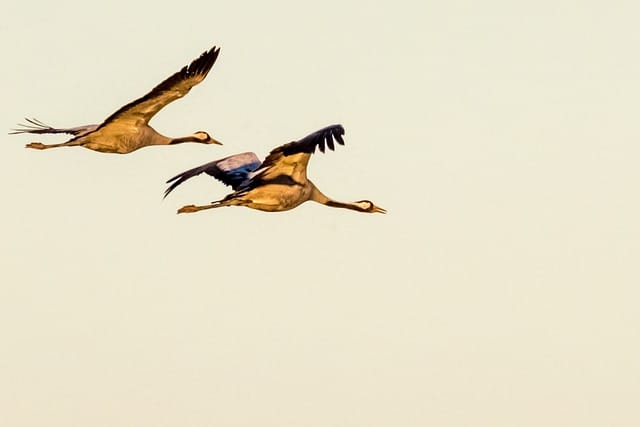
This article leverages a conversational tone to engage the reader, emphasizes the benefits of CMMS in facility management, and includes analogies (like ‘digital brain’) to simplify complex concepts. If you need any adjustments or further content, feel free to let me know!
Frequently Asked Questions
How does CMMS help in managing work orders and tracking maintenance history?
Discover how CMMS enhances efficiency by managing work orders and tracking maintenance history seamlessly, ensuring streamlined operations and informed decision-making.
What are the typical cost considerations when implementing a CMMS for facility management?
Understanding the typical cost considerations for implementing a CMMS (Computerized Maintenance Management System) in facility management is crucial. Costs typically include initial software purchase or subscription fees, implementation and customization expenses, training costs, ongoing support and maintenance fees, and potential costs associated with integrating with existing systems. It’s important to budget for these aspects to ensure a smooth implementation and effective utilization of the CMMS.
What is a CMMS and how does it benefit facility management?
Learn about CMMS (Computerized Maintenance Management System) and its benefits for facility management. Understand how CMMS streamlines maintenance tasks, improves asset reliability, and enhances operational efficiency. Discover how CMMS software enables proactive maintenance planning, reduces downtime, and extends asset lifespan.
What are the key features to look for when choosing a CMMS for facility management?
Learn about the essential features to consider when selecting a CMMS for facility management, ensuring effective maintenance tracking, asset management, work order management, integration capabilities, mobile access, reporting and analytics, and user-friendly interface.
How can CMMS software streamline preventive maintenance tasks?
Learn how CMMS software optimizes preventive maintenance tasks, enhancing efficiency and reducing downtime through automated scheduling, real-time monitoring, and comprehensive reporting.