Imagine running a bustling facility without a clear system in place to manage maintenance tasks, track asset performance, and optimize operations. It would be like navigating a maze blindfolded. This is where CMMS (Computerized Maintenance Management System) steps in as a game-changer for modern facility management.
CMMS isn’t just a tool; it’s the backbone that supports seamless operations. By centralizing data on equipment, maintenance schedules, and work orders, CMMS empowers facility managers to stay proactive rather than reactive. It’s like having a virtual assistant that never sleeps, constantly monitoring the health of your assets and alerting you before problems arise.
One of the most significant benefits of CMMS is its ability to extend the lifespan of equipment. By scheduling regular maintenance based on actual usage data rather than guesswork, facilities can reduce downtime and unexpected breakdowns. This proactive approach not only saves money but also enhances operational efficiency.
Moreover, CMMS fosters a culture of accountability and transparency. Every maintenance activity is logged, from inspections to repairs, creating a comprehensive audit trail. This not only ensures compliance with regulatory standards but also provides valuable insights for future planning and budgeting.
In today’s fast-paced world, where downtime can mean significant revenue loss, CMMS acts as a safeguard against operational disruptions. It helps facilities prioritize tasks, allocate resources effectively, and ultimately, deliver superior service to clients and customers.
In essence, CMMS isn’t just a tool for facility managers; it’s a strategic investment in the longevity and efficiency of your operations. By harnessing the power of data-driven maintenance, modern facilities can navigate challenges with confidence, ensuring smooth sailing even in the stormiest of conditions.
Streamlining Efficiency: How CMMS Revolutionizes Facility Management
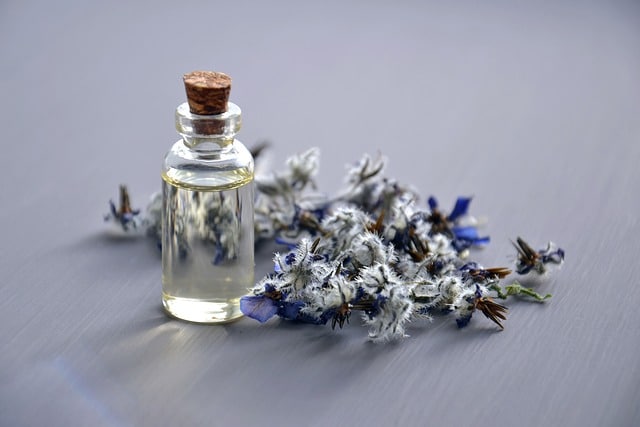
In the fast-paced world of facility management, efficiency is key to maintaining optimal operations and ensuring smooth functionality. One of the game-changers in this arena is CMMS, or Computerized Maintenance Management System. This innovative software solution has revolutionized how facilities streamline their operations, enhancing productivity and minimizing downtime.
CMMS is designed to centralize and automate maintenance tasks, from scheduling regular inspections to managing work orders and tracking inventory. By digitizing these processes, facilities can achieve greater efficiency in their maintenance operations. Imagine a tool that not only schedules routine checks for HVAC systems and equipment but also alerts maintenance teams to upcoming tasks, ensuring proactive maintenance rather than reactive fixes.
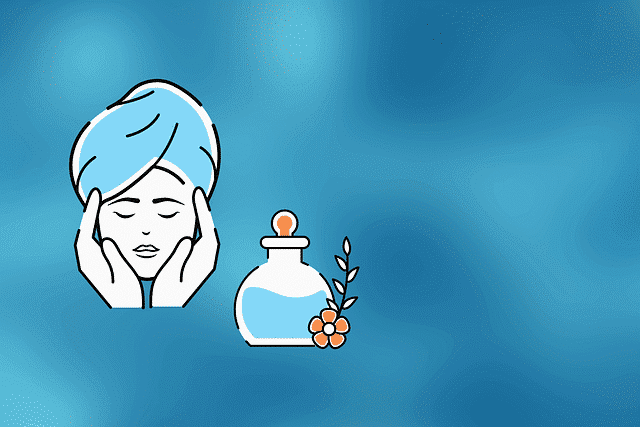
Moreover, CMMS enables real-time monitoring and reporting, providing facility managers with valuable insights into asset performance and operational trends. This data-driven approach empowers decision-making, allowing managers to allocate resources effectively and prioritize critical repairs based on actual usage and maintenance history.
The impact of CMMS goes beyond just operational efficiency; it translates into cost savings and improved asset longevity. By reducing unexpected breakdowns and prolonging equipment life through regular maintenance, facilities can minimize downtime and avoid costly emergency repairs.
In essence, CMMS is the backbone of modern facility management, offering a systematic approach to maintenance that enhances productivity and prolongs asset life. Its intuitive interface and user-friendly features make it accessible to both large-scale facilities and smaller operations looking to optimize their maintenance strategies.
CMMS stands as a testament to how technology can transform traditional practices, offering a streamlined solution that not only simplifies maintenance tasks but also elevates overall operational efficiency in facility management.
Cost Savings Unveiled: The Financial Impact of CMMS in Facilities
Curious about how CMMS (Computerized Maintenance Management Systems) could transform your facility’s financial landscape? Let’s dive into the details of how implementing CMMS can lead to significant cost savings and operational efficiencies.
Imagine a tool that not only streamlines maintenance processes but also pinpoints areas where costs can be trimmed, all while ensuring your facility runs smoothly like a well-oiled machine. That’s the power of CMMS. By centralizing maintenance data and automating workflows, CMMS allows facilities to proactively manage assets, schedule preventive maintenance, and swiftly address issues before they escalate. This proactive approach not only extends the lifespan of equipment but also prevents costly breakdowns that can disrupt operations and inflate expenses.
One of the key financial benefits of CMMS lies in its ability to optimize inventory management. By maintaining accurate inventory records and automating replenishment processes, facilities can reduce excess inventory holding costs and minimize emergency purchases. This strategic inventory control not only frees up capital but also ensures that resources are utilized efficiently, contributing to overall cost savings.
Moreover, CMMS enables facilities to track maintenance expenses accurately. From labor costs to materials used, every expenditure is recorded and analyzed, providing valuable insights into spending patterns. Armed with this data, facilities can make informed decisions to allocate resources more effectively and identify areas where further cost reductions are possible.
Another compelling advantage of CMMS is its role in enhancing regulatory compliance. By documenting maintenance activities and ensuring adherence to industry standards, facilities can avoid costly fines and penalties associated with non-compliance. This proactive compliance management not only protects the bottom line but also enhances the facility’s reputation for reliability and safety.
In essence, the financial impact of CMMS in facilities is profound. By fostering operational efficiency, optimizing resource allocation, and ensuring regulatory compliance, CMMS not only reduces costs but also enhances overall productivity and profitability. Ready to unveil the cost-saving potential of CMMS in your facility?
From Maintenance to Mastery: CMMS and Enhanced Facility Operations
CMMS isn’t just about fixing things when they break; it’s about proactive maintenance that prevents breakdowns in the first place. Picture this: instead of waiting for a critical piece of equipment to fail, CMMS notifies you ahead of time when maintenance is due. It’s like having a personal assistant for your facility that keeps everything running smoothly without you having to lift a finger.
One of the standout features of CMMS is its ability to schedule maintenance tasks automatically based on equipment usage or time intervals. This proactive approach minimizes downtime, boosts productivity, and extends the lifespan of costly equipment. For businesses, this means more uptime, fewer emergency repairs, and ultimately, happier customers.
But CMMS goes beyond just maintenance scheduling. It’s also a powerhouse for data analytics. By collecting and analyzing data on equipment performance and maintenance history, CMMS helps businesses make informed decisions. Think of it as having a crystal ball that predicts when and where issues might arise, allowing you to take preventive action before they impact operations.
Another game-changing aspect of CMMS is its role in compliance and documentation. Whether it’s regulatory standards or internal audits, CMMS keeps meticulous records of maintenance activities, inspections, and repairs. This not only ensures adherence to standards but also simplifies the audit process, saving time and reducing compliance risks.
In essence, CMMS is the secret sauce behind enhanced facility operations. It’s the tool that shifts businesses from reactive maintenance to proactive management, from firefighting to strategic planning. With CMMS in place, facilities can achieve mastery over their operations, ensuring efficiency, reliability, and ultimately, success in a competitive landscape.
Predictive Power: How CMMS Prevents Equipment Failures Before They Happen
At its core, CMMS harnesses the power of data and analytics to predict when maintenance is needed, rather than waiting for equipment to malfunction. By integrating historical performance data, real-time monitoring, and predictive algorithms, CMMS systems can identify patterns indicative of impending issues. This predictive capability not only extends the lifespan of machinery but also enhances overall operational reliability.
One of the key features of CMMS is its ability to schedule maintenance tasks based on predictive insights. Instead of adhering to rigid maintenance schedules that may not align with actual equipment conditions, CMMS uses predictive analytics to optimize maintenance intervals. This means maintenance teams can address issues precisely when they are most likely to occur, thereby reducing downtime and avoiding costly emergency repairs.
Furthermore, CMMS facilitates better resource allocation by ensuring that maintenance personnel and spare parts are available precisely when needed. Imagine a factory where maintenance teams are empowered with data-driven insights, allowing them to preemptively replace worn-out components or adjust settings before critical failures arise.
In essence, CMMS transforms reactive maintenance practices into a proactive, data-driven strategy. It empowers businesses to stay ahead of equipment failures, enhance productivity, and ultimately, deliver better service to customers. As industries increasingly embrace digital transformation, CMMS stands out as a cornerstone technology that not only prevents disruptions but also fosters a culture of continuous improvement and operational excellence.
The predictive power of CMMS represents a paradigm shift in maintenance management. By leveraging advanced analytics and real-time data, businesses can preempt equipment failures, optimize operational efficiency, and maintain a competitive edge in today’s dynamic market landscape.
Frequently Asked Questions
Why should facilities invest in a CMMS system?
Learn why facilities should invest in a CMMS system, which helps streamline maintenance operations, prolong asset lifespan, reduce downtime, and optimize resource utilization.
What is CMMS and how does it benefit facility management?
Learn about CMMS (Computerized Maintenance Management System), a software solution that enhances facility management by streamlining maintenance operations. Discover how CMMS optimizes asset management, reduces downtime, improves productivity, and ensures regulatory compliance through efficient maintenance scheduling and tracking.
How does CMMS contribute to cost savings and asset longevity in facilities?
Learn how CMMS (Computerized Maintenance Management System) enhances cost savings and prolongs asset lifespan by optimizing maintenance schedules, reducing downtime, and improving operational efficiency.
How does CMMS improve maintenance efficiency in facilities?
Learn how CMMS (Computerized Maintenance Management System) enhances maintenance efficiency in facilities by centralizing asset management, scheduling preventive maintenance, tracking work orders, and optimizing inventory. Discover how CMMS streamlines operations, reduces downtime, and extends equipment lifespan.
What features should I look for in a CMMS for facility management?
Learn about the essential features to consider when choosing a CMMS (Computerized Maintenance Management System) for effective facility management. Discover key functionalities that enhance maintenance scheduling, asset tracking, work order management, and reporting capabilities.